MDM Welding with Single-Mode Lasers
Single-mode lasers delivered through a smart “wobble” head enable precise control of weld dimensions and heat input for welding medical devices.
July 11, 2023 by Coherent
While many existing production lines for medical devices use pulsed Nd:YAG lasers, most new lines use multi-mode QCW fiber lasers that have similar beam characteristics and pulsed parameter landscape to the Nd:YAG laser while offering the cost of ownership benefits of fiber technology.
As designs for next-generation devices are explored there is typically one constant – the new design is smaller than the last. As a result, the joining requirements become more demanding, particularly reducing the weld size and controlling heat input. The problem is pulsed lasers can sometimes be limiting from a material-selection perspective, as high cooling rates can create small process windows or a propensity for weld cracking. Is there another option?
Why single-mode fiber lasers are a solution
The continuous wave or CW single-mode fiber laser when paired with a scan head offers a unique and compelling weld capability: weld miniaturization - precise control of weld dimensions and heat input.
For those not so familiar with single-mode lasers, they have the absolute best beam quality, and, as a result, generate the smallest spot size for a given focal length of optic. Indeed, single-mode lasers are routinely focused to spot diameters in the 25 µm range (0.001”) using 150 mm (6”) focal lengths. The interesting part is when we pair the single-mode laser with a scan head, now there is the capability to move the 25 µm spot rapidly enough over the workpiece to scale the heat source as needed. If a 100 µm wide seam is required, the spot is moved rapidly perpendicularly to the seam direction creating the weld width. The spot motion is fast enough that the material from a heat input perspective reacts the same as if a larger spot diameter was used.
The rapid on-part movement created by the scan head is possible due to two very small low-inertia mirrors called galvanometers or “galvos” that are mounted orthogonally to each other and, therefore, able to create x and y motion. An F Theta lens creates a flat area focal plane so over 100x100 mm or 200x200 mm (according to the focal length of the optics), the laser remains in focus over the entire area.
The key aspect of the scan head is the distance “lever” from the mirrors to the part. Effectively very small high-speed motion in the galvos creates larger motion and extremely high speeds on the part. This provides the flexibility of using a 25 µm laser spot that can be moved to create any shape or size of weld that fits in the motion window of the scan head. In micro welding, this capability is a significant process enabler.
Here are some use cases single-mode fiber lasers solve:
1. Any shape or size of spot weld – this can be a circle, an annulus circle, a spiral, a square, a smiley face, or whatever that can be optimized for the thermal constraints of the parts and the mechanical needs of the weld.
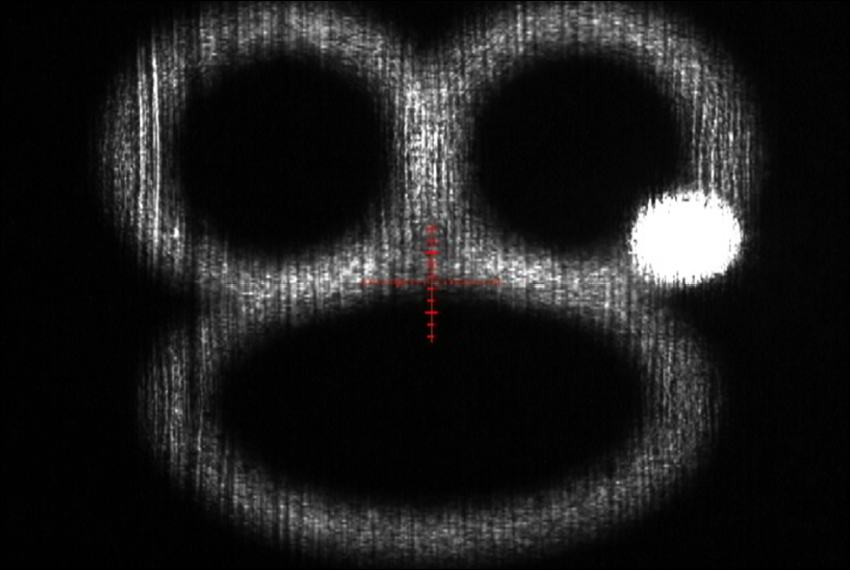
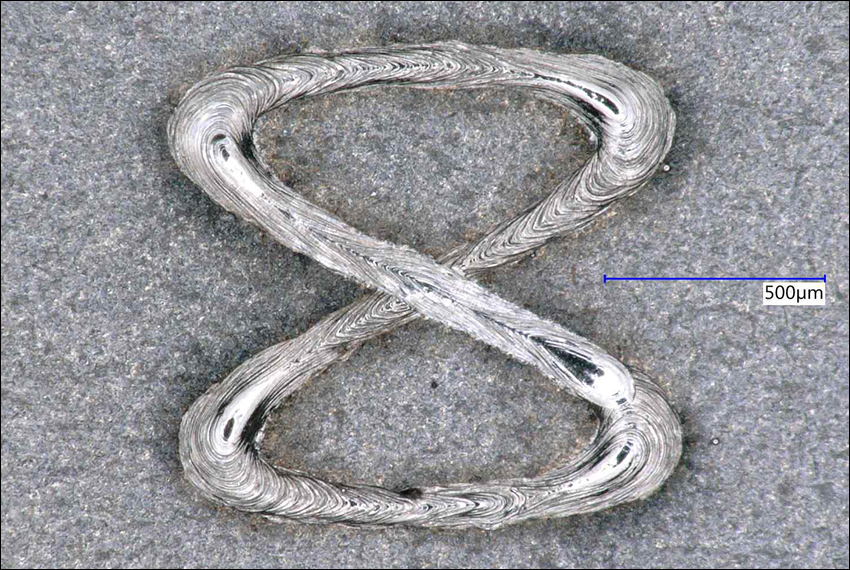
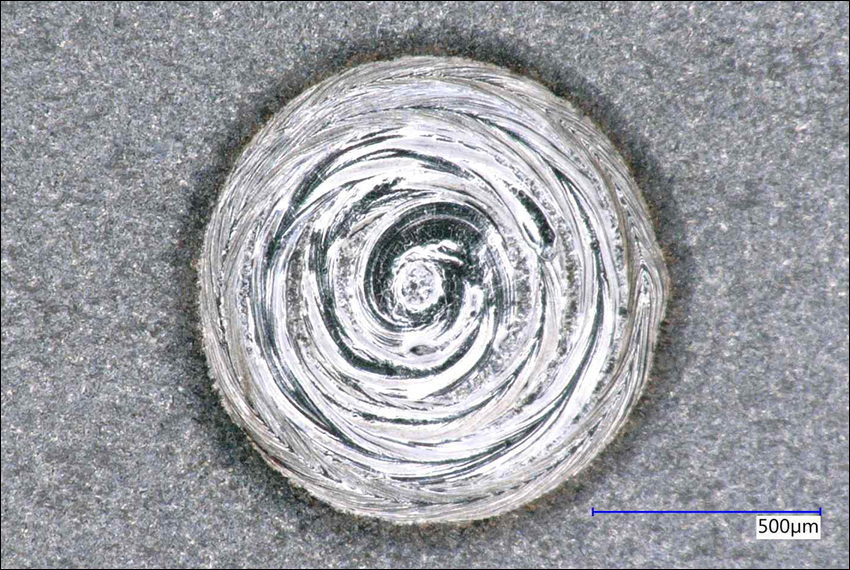
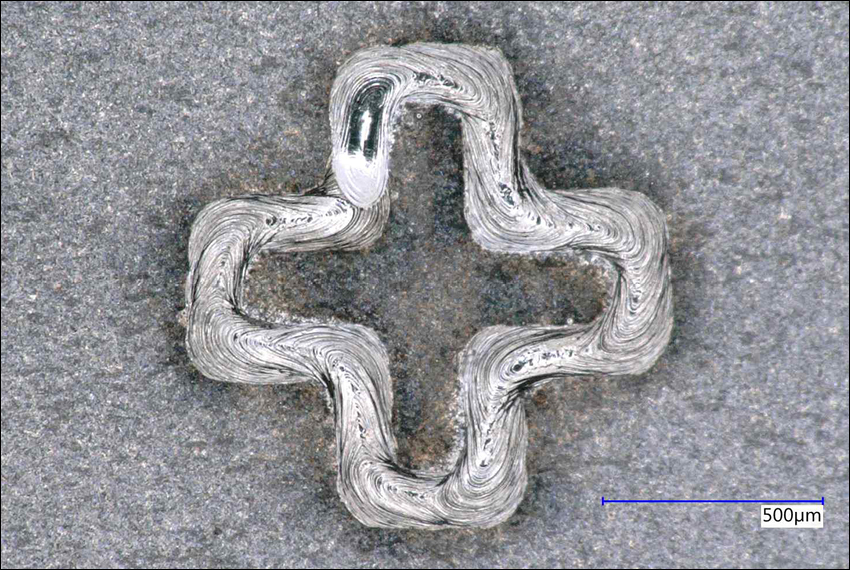
2. Dynamically scale welds – different welds on the same part can be sized and shaped individually by tooling path only rather than parameter changes or welds on different parts can be scaled or shaped as needed.
3. Reduce cycle time on multi-spot welds – moving between spot welds even using linear stages is relatively slow compared to a scan head that can move point to point in fractions of a second per second. A classic example of the use of scan heads for spot welding is for flexure arms that once were used for all disc drives, typically 25 spot welds are made in under 1s.
4. Tailored seam dimensions – lateral motion can be superimposed along the seam to precisely control the width and depth of the seam weld. For example, pulsed QCW or Nd:YAG seam weld cross-section depth decreases from the centerline to the edge. With a single-mode laser and scan head we can create a square cross-section profile, such that the penetration in the center and the edge of the weld are the same. Therefore, for butt or fillet welds any seam joint misalignment can be accommodated with no decrease in weld strength.
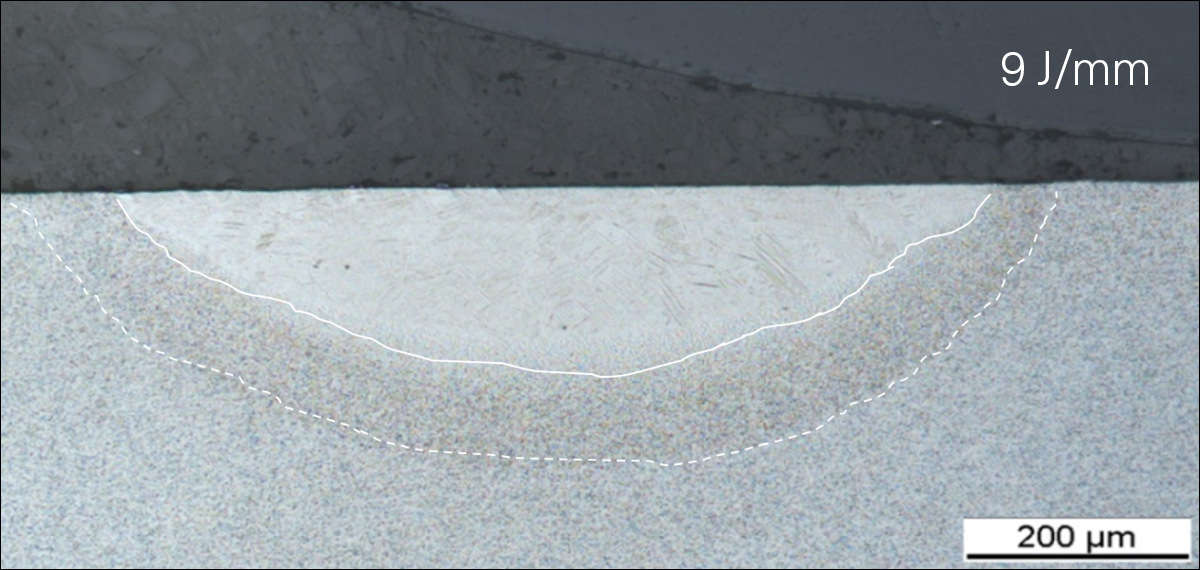
Regular penetration and cross-section of a spot applied by a pulsed laser, spot size ~ 800 µm.
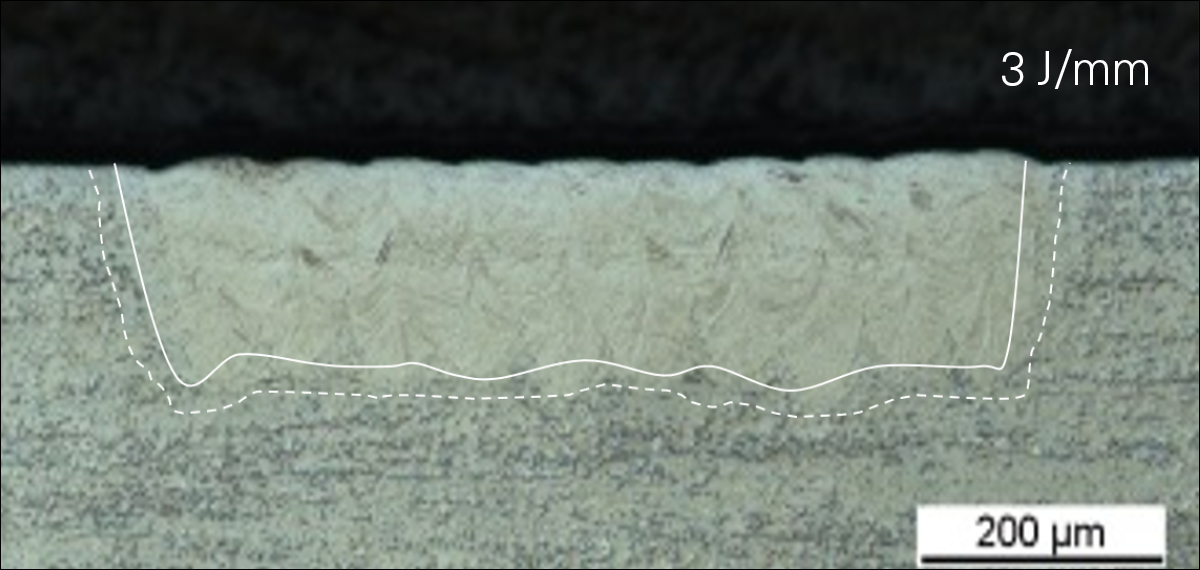
Penetration and cross-section of a spot applied by a single mode laser, spot size ~ 30 µm, moved rapidly through the material.
5. Minimize Heat Input – heat input is directly proportional to the strength of the heat source and time on part. The lateral effect of the heat source is a function of its size. By using a 25 µm spot that is moved rapidly over the part in whatever shape is needed we now have precise control over the heat input, and all the control levers to optimize.
Market: Electronics/Medical
Material: Stainless steel foil, 40 µm, to gold-plated copper, 140 µm
Application: Welding of electronic components to a PCB
Sub-system: PowerLine FL 150 P, SmartWeld+
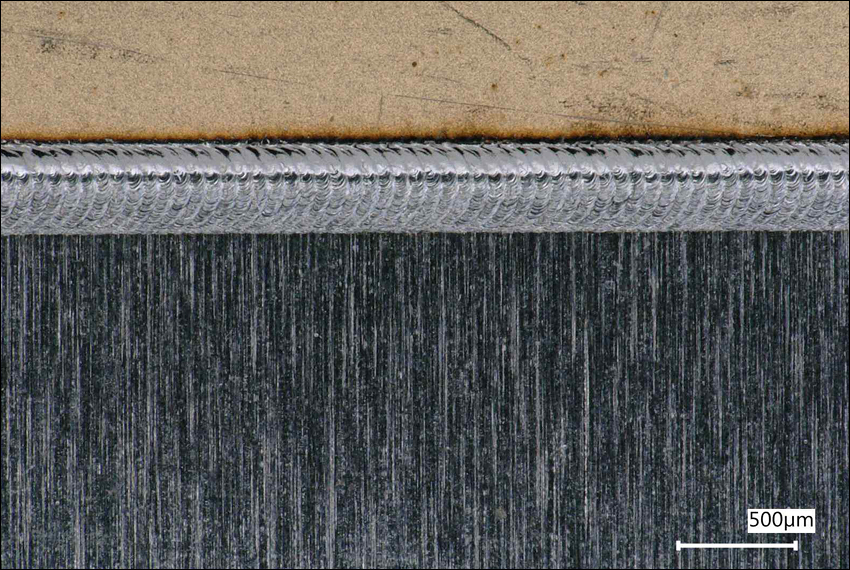
Linear speed: 800 mm/min
Welding depth: ~ 45 µm
Shear strength: 130 N per 10 mm
Homogenous seam, no cracks
No impact visible on PCB
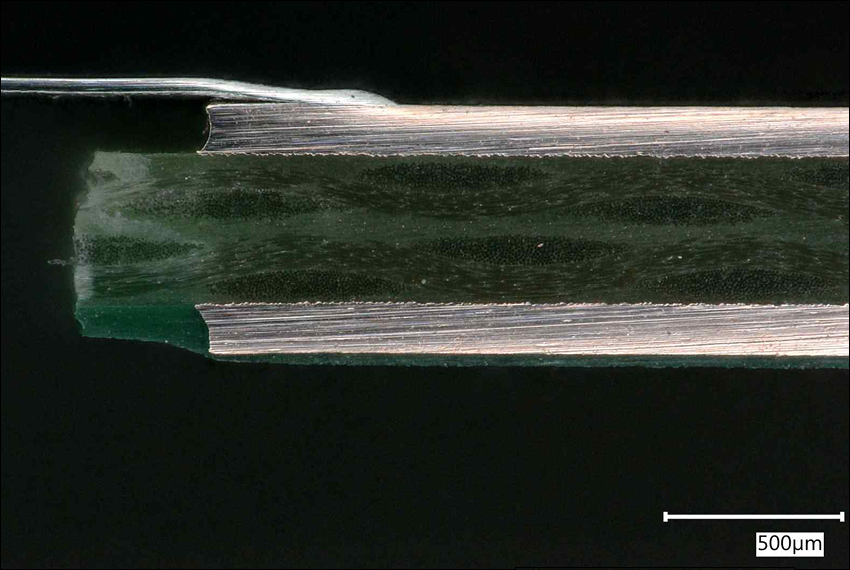
6. Large process windows, more weldable materials – with minimal heat input and a laser that is running in continuously on (wave) mode reduces the cooling rates the part experiences, increasing the range of weldable materials while reducing any likelihood for weld cracking.
Market: Medical Device
Material: Stainless steel
Application: Welding of wire mesh
Sub-system: PowerLine FL 150 P, SmartWeld+
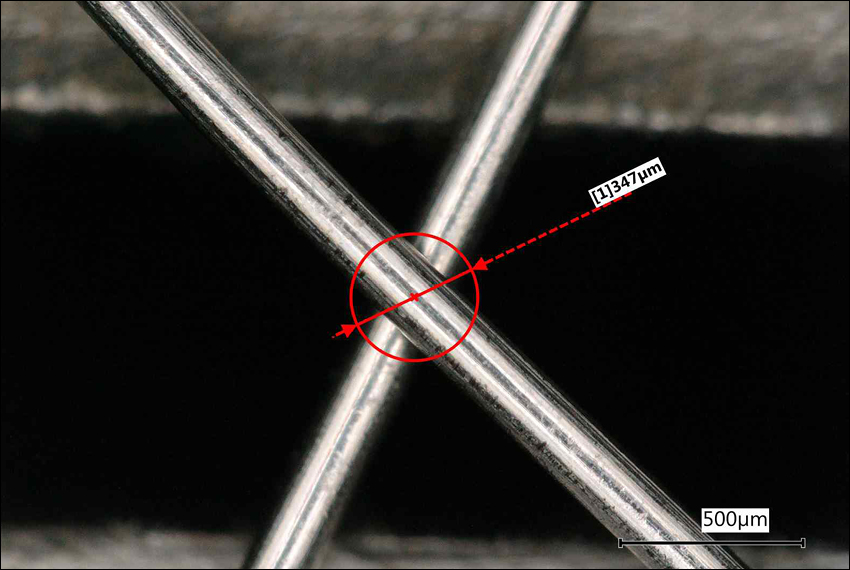
Wire Diameter: 200 µm
Spot Size: 30 µm
Number of pulses: Single pulse
Peaks: 85 W
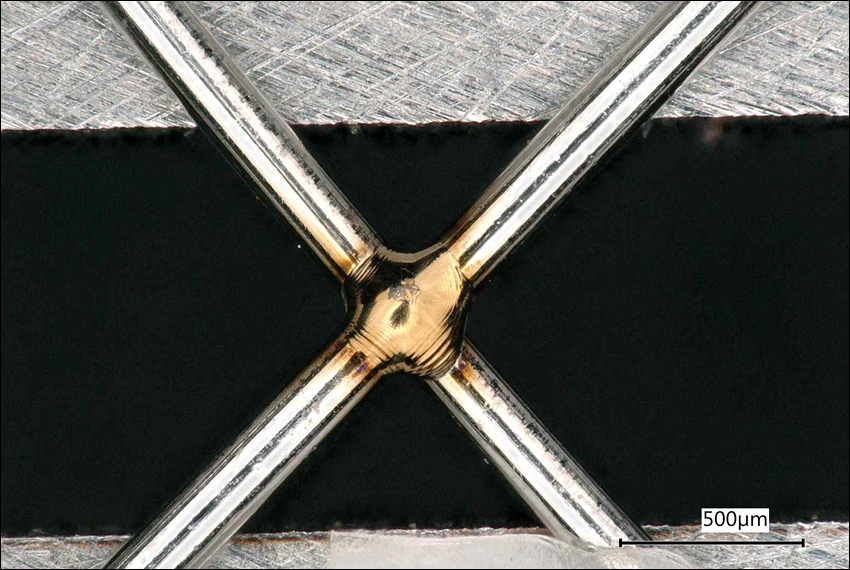
7. 3D motion capability – the scan head can be fitted with an additional axes of motion to move the focal plane in the z axes, offering even more functionality.
Benefits from single-mode fiber lasers:
- Lower laser power – using a focus spot size around 25 µm increases power density that means lower average power is needed, reducing the size of the laser needed and reducing cost.
- Lower cost motion – scan heads are a commodity item due to the volumes in laser marking, therefore a high-technology scan head is relatively inexpensive when compared to stages.
- Easy programming – motion programming of scan heads requires no knowledge of G or M code, as welding paths are created using circle and line functions as they would in a drawing package, the same as a laser marker. The software guides the user through the processing of building a production run list that might also include pre-weld vision, in-process monitoring, or post-weld inspection.
- Minimized system footprint – typically a scan head will have a motion of 200x200 mm (8x8”) and is no larger than a small shoebox, with laser delivered via fiber that is typically rack mounted the overall system footprint is very small.
Beyond the Scan Head
Even though the scan head accelerations and decelerations are very high, they are still present, which means certain welding paths may have sections with higher or lower heat input.
Our smart “wobble” head, the Coherent SmartWeld+ solves this and adjusts power and, therefore, heat input on the fly. This fully flexible and programmable wobble/power pattern allows you to precisely control the weld heating and cooling — delivering a more deterministic control of weld parameters, including seam width and penetration depth.
Learn all about Coherent SmartWeld+.
Related Resources