シングルモードレーザを使用したMDM溶接
スマートな「ウォブル」ヘッドを介して照射されるシングルモードレーザにより、医療機器を溶接する際の溶接寸法と入熱を正確に制御できます。
2023年7月11日 Coherent
医療機器の既存の生産ラインの多くでパルスNd:YAGレーザを使用していますが、ほとんどの新しいラインでは、Nd:YAGレーザと同様のビーム特性とパルス発振パラメータのランドスケープを備えたマルチモードQCWファイバーレーザを使用し、ファイバー技術が持つ所有コストのメリットを活用しています。
次世代デバイスの設計を検討する際に、通常不変の要素が1つあります。それは、新しい設計は前回の設計よりも小型になるということです。 そのために接合要件はより厳しくなり、特に溶接サイズの縮小と入熱の制御が求められます。問題は、パルスレーザでは、冷却速度が速いとプロセスウィンドウが小さくなったり、溶接割れが発生しやすくなったりするため、材料選択の点で制限される場合があることです。ほかの選択肢はありますか?
シングルモードファイバーレーザがソリューションとなる理由
連続波またはCWシングルモードファイバーレーザをスキャンヘッドと組み合わせると、ユニークで魅力的な溶接機能を得られます。たとえば溶接部の小型化により、溶接部の寸法と入熱を正確に制御します。
シングルモードレーザにあまり詳しくない方のために説明すると、シングルモードレーザは最高のビーム品質を備えており、その結果、光学素子の特定の焦点距離に対して最小のスポットサイズを生成します。実際にシングルモードレーザは、150 mm(6インチ)の焦点距離を使用して、25 μm範囲(0.001インチ)のスポット直径に定期的に集束されます。魅力的なのは、シングルモードレーザとスキャンヘッドを組み合わせると、必要に応じて熱源を拡大できるように、ワークピース上で25 µmのスポットを十分に高速に移動できる機能があることです。 幅100 µmのシームが必要な場合は、スポットをシーム方向に対して垂直に急速に移動させて溶接幅を作成します。スポットの動きは十分に速いので、入熱の観点から見ると、材料はより大きなスポット直径が使用された場合と同じように反応します。
スキャンヘッドによって生成される部品上の素早い動きは、ガルバノメーターまたは「ガルバノ」と呼ばれる2つの非常に小さな低慣性ミラーが実現しています。これらのミラーは互いに直角に取り付けられているため、X方向とY方向の動きを生み出すことができます。 Fシータレンズによって、100 x 100 mmまたは200 x 200 mm(光学系の焦点距離に応じて)を超える平らな領域の焦点面が作成され、レーザはその領域のどこでも焦点が合うようになります。
スキャンヘッドにおいて重要なのは、ミラーから部品までの「レバー」の距離です。ガルバノ内の非常に小さな高速動作が、部品上でのより大きな動作と非常に高速な動作を効果的に生み出します。これにより、25 µmのレーザスポットを移動して、スキャンヘッドのモーションウィンドウに収まる任意の形状やサイズの溶接を作成できる柔軟性が得られます。マイクロ溶接では、加工を実現するためにこの機能が重要です。
シングルモードファイバーレーザは、次のようなユースケースを解決します。
1. あらゆる形状やサイズのスポット溶接 – 円、環状の円、螺旋、正方形、スマイリーフェイスなど、部品の熱的制約や溶接の機械的ニーズに合わせて最適化できるものであればどのような形状でも可能です。
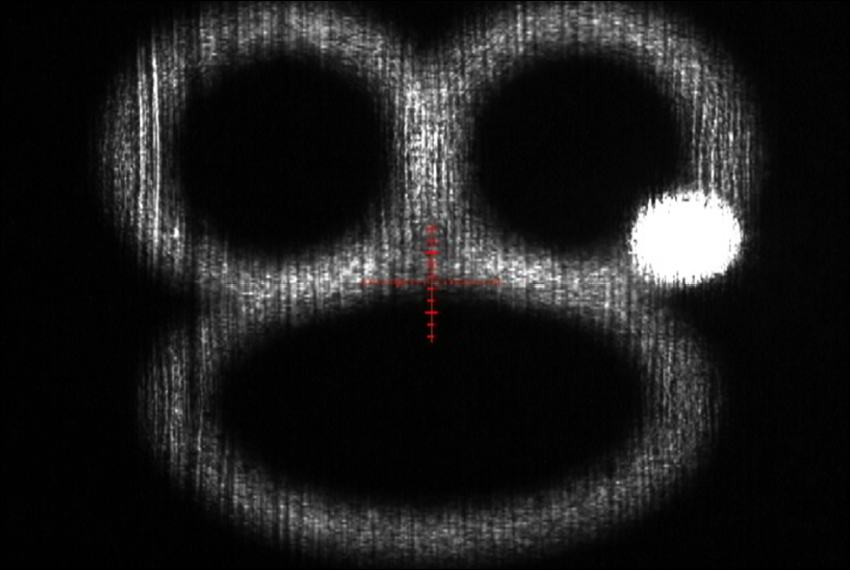
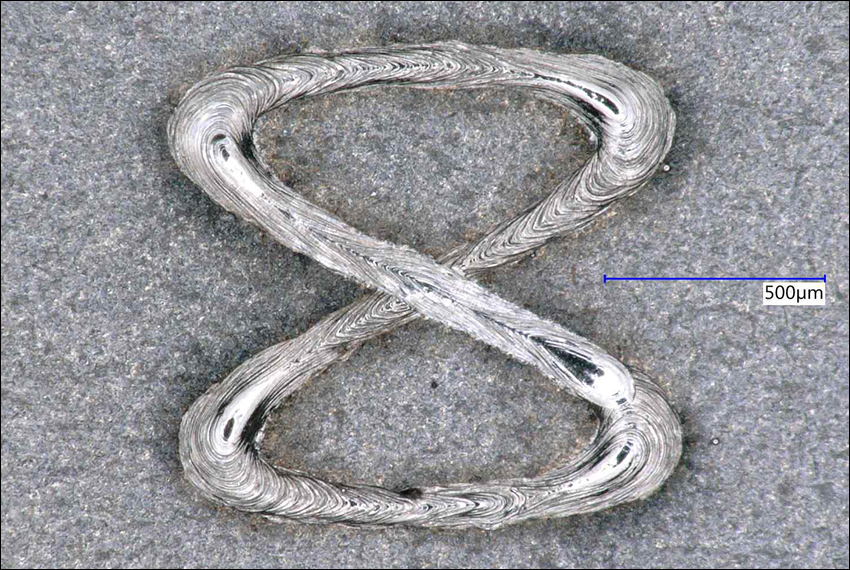
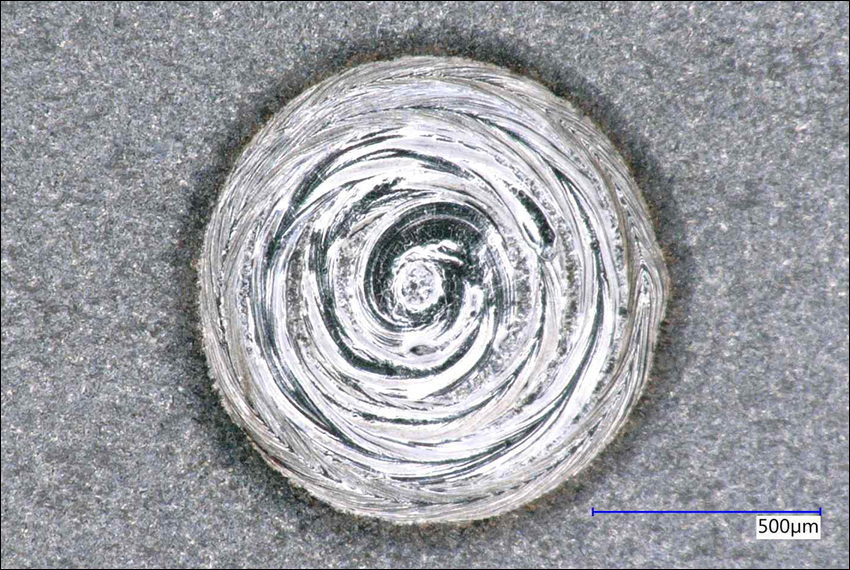
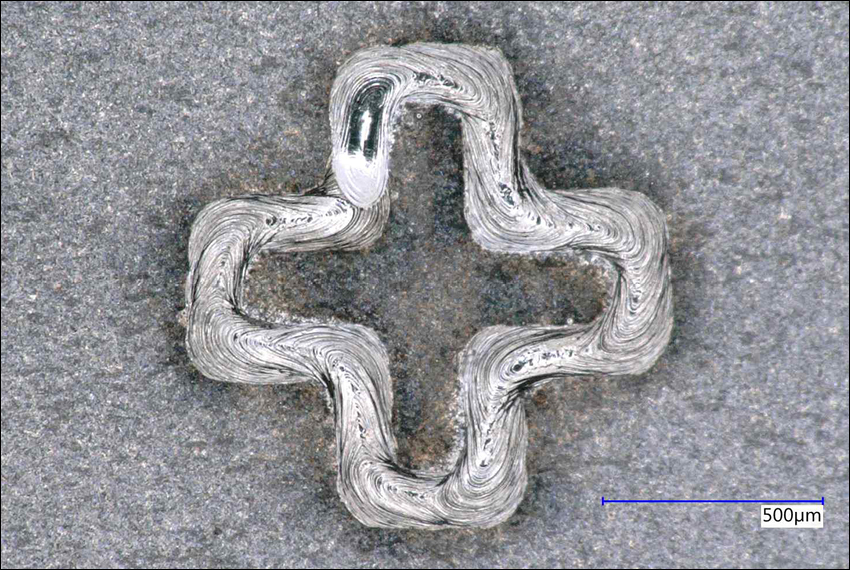
2. 溶接の動的なスケール – 同じ部品上の異なる溶接のサイズや形状を、パラメータを変更するのではなくツーリングパスのみで個別に変更できるほか、必要に応じて異なる部品上の溶接のサイズや形状を変更することができます。
3. マルチスポット溶接のサイクルタイムを短縮 – リニアステージを使用した場合でも、スポット溶接間の移動は、数分の1秒で点から点へ移動できるスキャンヘッドに比べて遅くなります。 スポット溶接にスキャンヘッドを使用する典型的な例は、かつてすべてのディスクドライブに使用されていたフレクシャーアームであり、通常は1秒未満で25個のスポット溶接が行われます。
4. シームの寸法をカスタマイズ – シーム溶接の幅と深さを正確に制御するために、シームに沿って横方向の動きを重ね合わせることができます。 たとえば、パルスQCWまたはNd:YAGシーム溶接断面の深さは、中心線からエッジに向かって減少します。 シングルモードレーザとスキャンヘッドを使用すると、溶接の中心と端の溶け込みが同じになるような正方形の断面プロファイルを作成できます。 したがって、付き合わせ溶接や隅肉溶接の場合、溶接強度を低下させることなく、シーム接合部の位置ずれに対応できます。
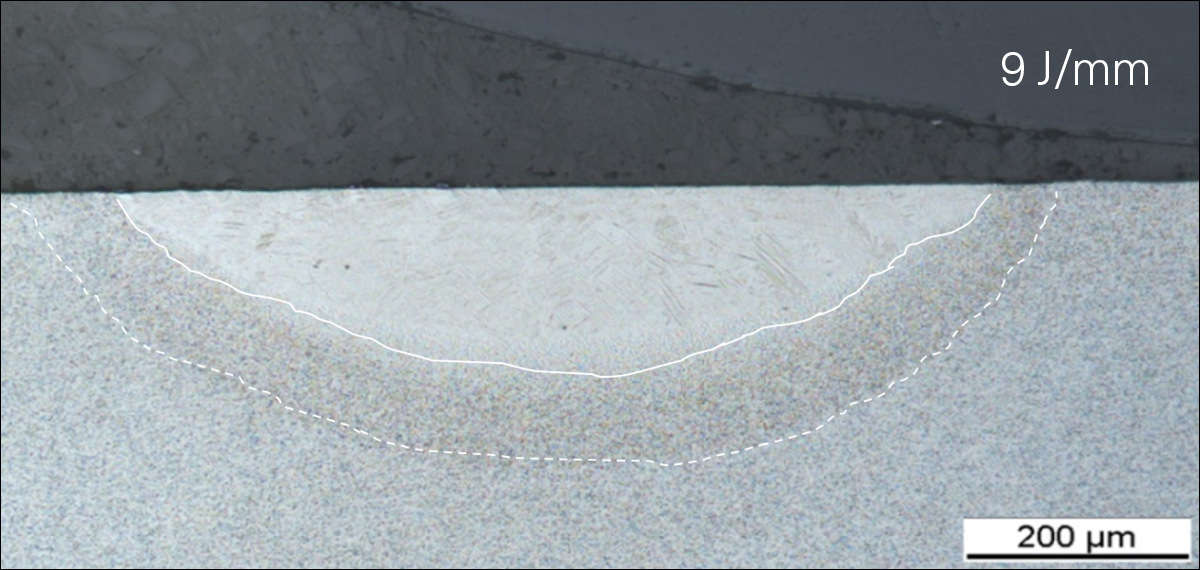
パルスレーザが施したスポットの通常の溶け込みと断面、スポットサイズ約800 µm。
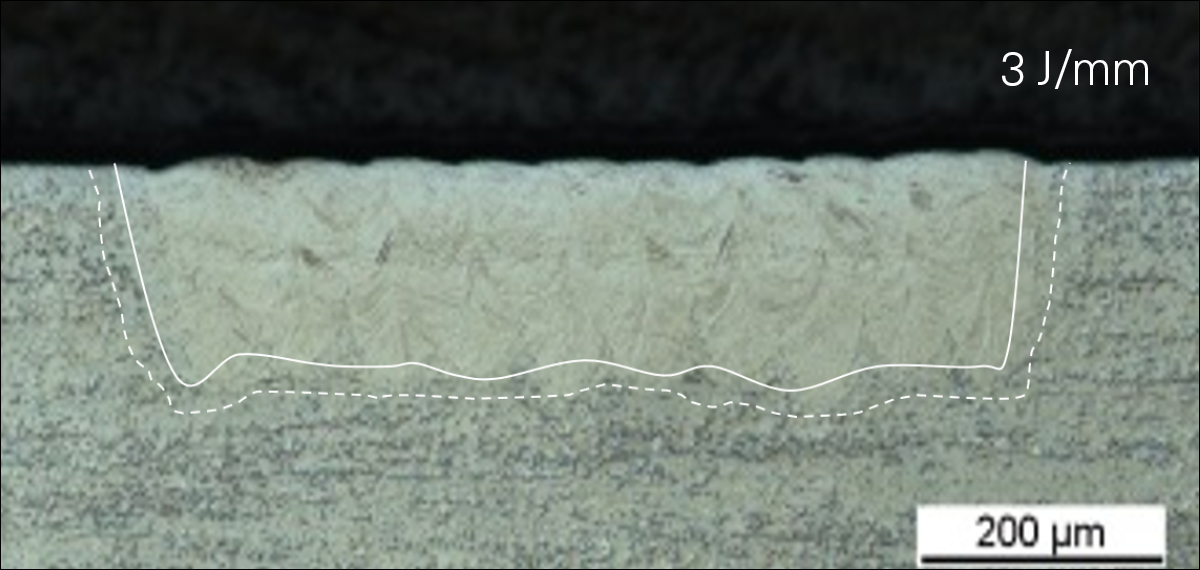
シングルモードレーザが施したスポットの溶け込みと断面、スポットサイズ約30 µm。材料内を急速に移動しています。
5. 最小限の入熱 – 入熱量は、熱源の強さと部品にとどまった時間に直接比例します。 熱源の横方向の影響は、そのサイズと相関します。 必要な形状に関わらず、部品上を高速で移動する25 µmのスポットを使用することで、入熱を正確に制御し、すべての制御レバーを最適化できるようになりました。
対象市場:エレクトロニクス/メディカル
材料:40 μmのステンレス箔から140 μmの金メッキ銅まで
用途:エレクトロニクス部品のPCBへの溶接
サブシステム:PowerLine FL 150 P、SmartWeld+
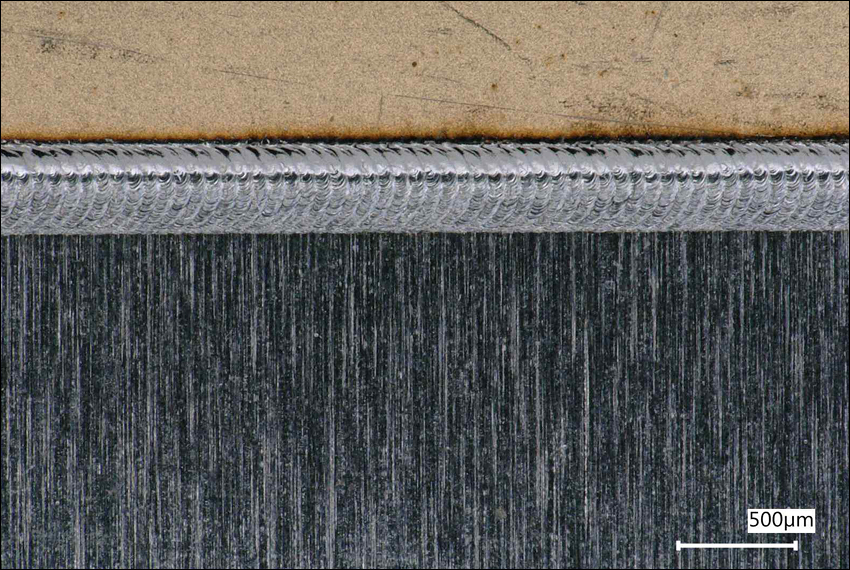
線速度:800 mm/分
溶接深さ:~45 µm
せん断強度:130 N/10 mm
均質なシーム、亀裂なし
PCBへの影響は見られません
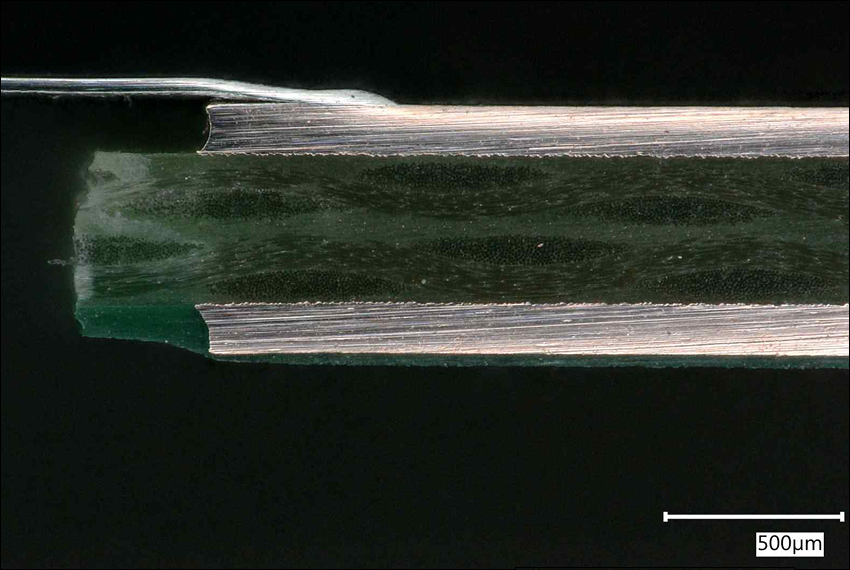
6. 大きなプロセスウィンドウ、より多くの溶接可能な材料 – 入熱を最小限に抑え、連続オン(ウェーブ)モードで動作するレーザにより、部品の冷却速度が低下し、溶接可能な材料の範囲が広がり、溶接割れの可能性が低減されます。
対象市場:医療機器
材料:ステンレス
用途:金網の溶接
サブシステム:PowerLine FL 150 P、SmartWeld+
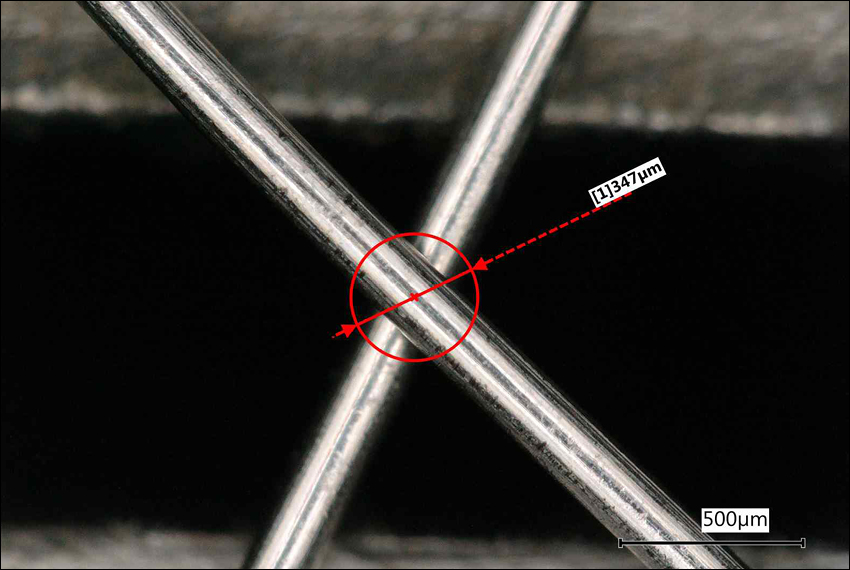
線径:200 µm
スポットサイズ:30 µm
パルス数:シングルパルス
ピーク:85 W
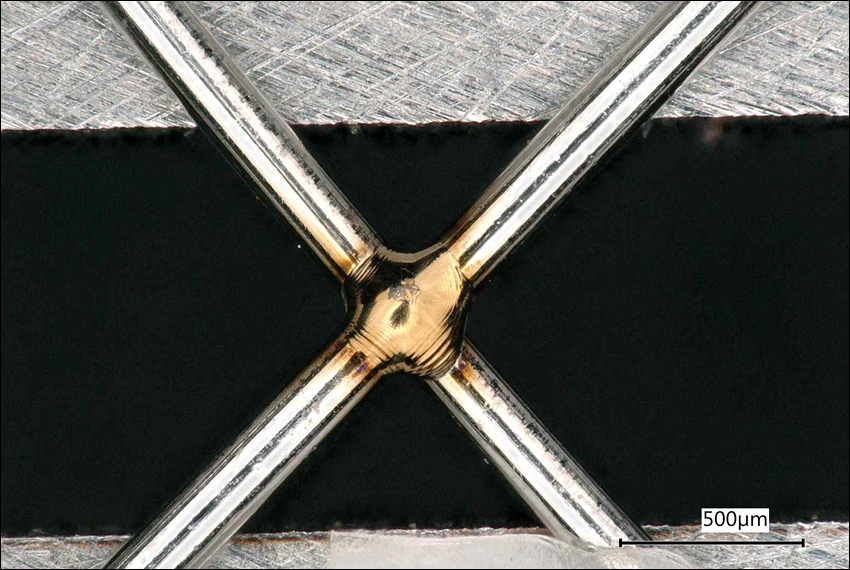
7. 3Dモーション機能 – スキャンヘッドに追加の動作軸を取り付けて、焦点面をZ軸に沿って動かすことができます。これによりさらに多くの機能を使用できます。
シングルモードファイバーレーザのメリット:
- レーザ出力が低い – 約25 µmの集束スポットサイズを使用すると、出力密度が増加します。これにより、必要な平均出力が低くなるため、必要なレーザのサイズが小さくなってコストの削減につながります。
- モーションのコストが安い – レーザマーキングは広く使われているため、スキャンヘッドは汎用品です。そのため、ハイテクスキャンヘッドはステージに比べて安価です。
- プログラミングが簡単 – レーザマーカーと同様、溶接パスは図面パッケージのように円と線の関数を使用して作成されるため、スキャンヘッドのモーションプログラミングにはGコードやMコードの知識は必要ありません。ソフトウェアが、溶接前のビジョンによる確認、インプロセスモニタリング、溶接後の検査を含めた生産工程リストを作成する手順をユーザーにガイドします。
- システムの設置面積が最小限 – 通常、スキャンヘッドのモーションは200 x 200 mm(8 x 8インチ)で、小さな靴箱ほどの大きさです。通常、ラックに取り付けられるファイバーからレーザが照射されるため、システム全体の設置面積は非常に小さくなります。
スキャンヘッドを超えて
スキャンヘッドの加速と減速は非常に高速ながらも存在します。つまり、特定の溶接パスで熱入力が高いまたは低い部分がある可能性があるということです。
当社のスマート「ウォブル」ヘッドであるCoherent SmartWeld+は、この問題を解決し、電力を調整します。その結果、熱入力をその場で調整することができます。 この完全に柔軟でプログラム可能なウォブル/電力パターンにより、溶接の加熱と冷却を正確に制御でき、シーム幅や溶け込み深さを含む溶接パラメータをより決定的に制御できます。
Coherent SmartWeld+についての詳細をご覧ください。
関連資料