Laser Marking Improves Product Traceability
Lasers produce high-quality marks that enable manufacturers in many industries to meet increasingly stringent traceability and compliance standards.
March 16, 2023 by Coherent
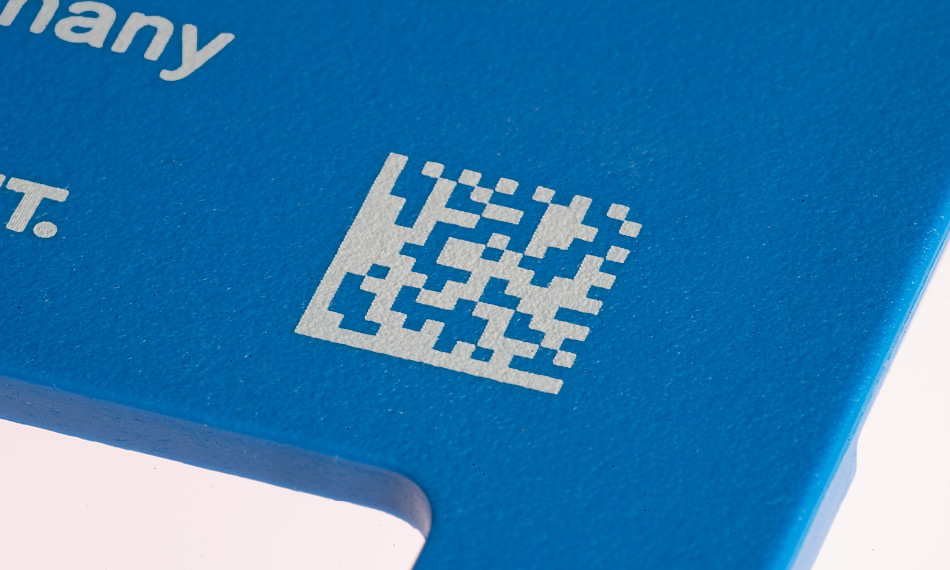
Across the globe, manufacturers in nearly every industry face increasing governmental requirements to provide detailed traceability and compliance data on their products. Plus, traceability has benefits for the manufacturers themselves. It can aid quality assurance, improve production yields, help maintain brand standards, and even shield companies from liability.
What is traceability?
Product traceability is the capability for identifying and tracking the various constituents of products as they move through the supply chain from raw materials to finished goods. For manufactured goods (as opposed to foodstuffs, natural materials, and the like), the most basic traceability information includes the name and location of the manufacturer, and a unique identifier (like a part number or SKU) for the product.
Traceability may also include data about the conditions under which product batches or individual units were produced. For example, it could contain detailed information about the specific equipment used to fabricate the item, and even their exact operating parameters at the time. It can also comprise information on how the product was inspected or tested.
Marking is a key tool for traceability. Specifically, this means the placement of unique marks on each individual unit which provide data or link it back to a manufacturer’s database containing the sorts of information mentioned previously.
The simplest mark could be just the part number or serial number of the product in the form of alphanumeric text or a traditional 2D barcode. More complex marks might contain web links, a MAC ID, and even features to prevent product counterfeiting.
The laser marking solution
For materials that can be marked by a laser – and there are very few that can’t – this technology represents the best way to implement traceability marking in a production environment. There are several reasons for this.
First, laser marking is particularly capable of producing complex marks which contain a large amount of data. And laser marks can also be quite small in size. This is because in most laser marking applications the beam is focused down to a spot that is in the microns or tens of microns diameter range. Marking with such a small “tool” makes it easy to render fine detail and create intricate patterns even at very small scales.
Laser marking can also readily accommodate changes in part position, orientation, or even shape in order to consistently place marks in the correct location. This allows it to correct for real-world variations in how the parts are presented to the marking system, and in the dimensional tolerances of the part itself.
Laser marking can accomplish this because it is usually implemented using some sort of scanning – typically based on galvanometer mirrors. Two-dimensional scanning enables the beam to be rapidly moved to any point over an area in order to create the mark. In practice, a vision system determines the actual part location and orientation, and then system software automatically adjusts to place the mark in the right location.
Adding dynamic focusing capability to a two-dimensional scanner enables marking on curved or multi-level flat surfaces. This so-called “3D scanning” substantially expands the usefulness of the technique.
Another advantage of laser marking is that it produces cosmetically attractive marks on nearly any material. Mark cosmetics can be particularly important on consumer products. A laser mark is also very durable, and won’t smudge, smear, or rub off.
Even though the laser heats the material to produce the mark, the process can still be performed on delicate or heat-sensitive parts, such as integrated circuits. The laser wavelength and pulse duration can be chosen to minimize the heat-affected area. For example, the nanosecond pulse duration of Q-switched lasers (e.g., the Coherent PowerLine E and PowerLine F series) limits the thermal exposure during marking to a few tenths of a millimeter. The temperature of the part beyond that remains essentially unchanged.
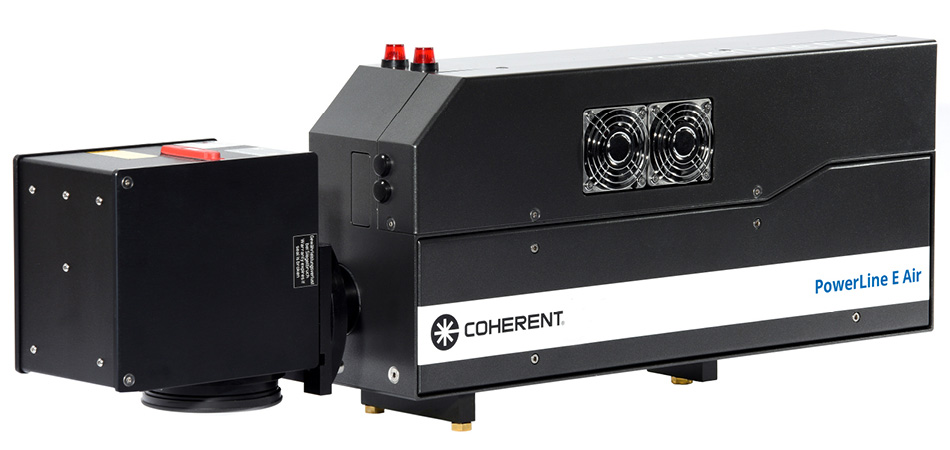
Coherent PowerLine Series laser marking engines integrate a laser source, scanning and beam delivery optics, and all the necessary control electronics and software. They are available with a variety of different lasers to support marking of nearly any type of material, including metals, semiconductors, polymers, glass, and more.
Laser marking is also fast. It’s quite possible to have the entire laser marking process take just a few seconds. And this includes vision tasks to measure and correct for part position, the marking process itself, and post-process inspection and verification steps.
No other marking technology involving printing or other mechanical methods delivers this same combination of benefits. Plus, there are no consumables in laser marking, whereas ink costs for traditional printing methods can be a significant factor in high-volume applications. For these reasons, laser marking has become extremely popular in a wide range of industries.
A framework for traceability marking
In the most advanced manufacturing environments – so-called “digital factories” – the laser marker is fully integrated with an enterprise-wide production automation system. This enables it to smoothly function with other production equipment, and also deliver all the functionality needed for complete traceability.
For example, the marking system might communicate with part handling equipment to indicate when it is ready to receive part. Then it can visually inspect the part using embedded vision, and let the system know it has verified that the correct part was supplied.
Next, it can connect with a production control system to get serial number and other part-specific data. After marking, it can transmit back information about the process. This can include process parameters, data showing that the mark was verified, a quality assessment of the mark, and so on.
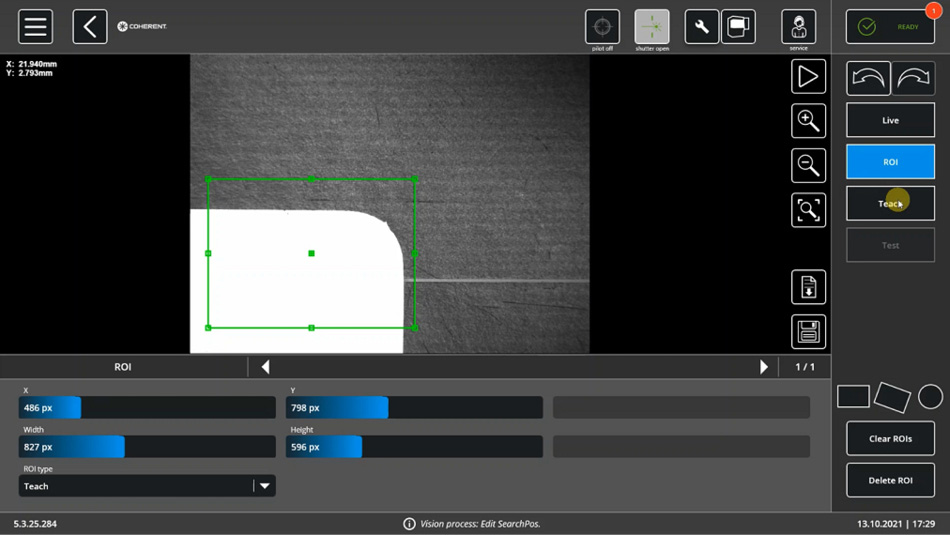
Laser FrameWork provides extensive machine vision capabilities. It can examine parts prior to marking to automatically locate features, or determine part position and orientation. It can also perform post-marking inspection.
Coherent developed the Laser FrameWork Software package to support this kind of digital manufacturing environment. It provides all the capabilities for creating new laser marking tasks, including vision, and then executing them in production. And it provides a “framework” (a software platform) for developing and implementing the specific routines needed to interface with other production automation systems. Coherent Laser FrameWork comes ready to make laser marking part of a digital factory right out of the box.
Traceability has the power to make products safer and enable manufacturers to cut costs and improve quality. Product marking is at the heart of implementing traceability for many manufacturers. And laser marking, powered by Coherent Laser FrameWork, provides an easy path to implementing it in a digital manufacturing environment.