WHITE PAPER
Designing Cost-Effective Freeforms
How to Design More Cost-Effective Freeform Optics
Freeform optics (having a shape without translational or rotational symmetry) have had a significant impact in airborne systems and other applications and are a key enabler for the compact spaceborne systems required for Proliferated Low Earth Orbit (LEO), in particular. This is because their complex shapes allow the production of optical systems with reduced physical size and weight, together with improved performance. But the sophisticated fabrication technologies that have enabled freeforms also give rise to fabrication challenges not encountered in the production of traditional, rotationally symmetric spherical and aspheric optics.
These challenges can significantly impact manufacturers, who typically pass along the associated costs and technical risks to their customers. Or worse, fabricators unknowingly charge ahead and endanger customer missions by their inability to deliver to specification or on schedule. This document is intended to help optical designers consistently produce freeform designs which can be readily fabricated in a cost-effective manner. Specifically, it presents a metric that can be used to predict manufacturability, and hence, lead time and cost.
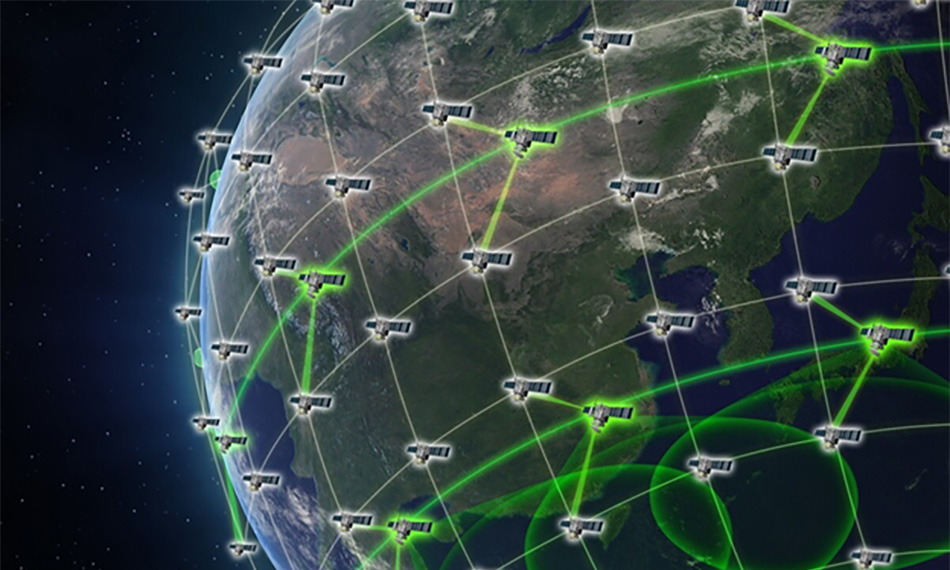
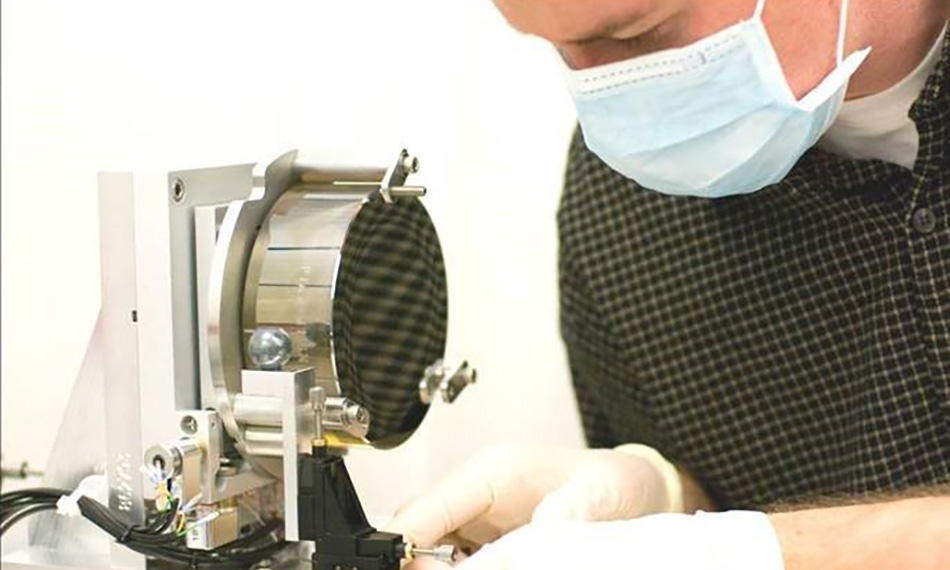
The Relationship of Surface Shape to Manufacturability and Cost
The goal of a fabricator is to produce an optical surface that conforms to the intended design. But real-world manufacturing processes are not perfect, so a design must always accommodate some tolerance for errors. And, of course, the greater the design tolerance for errors, the easier the polishing process becomes, which, in turn, reduces part cost and lead time.
For freeform optics fabricators, the most readily accessible way of quantifying shape accuracy is with low spatial frequency and mid-spatial frequency errors. Specifically, low frequency surface errors correspond to the traditionally used measures of large scale shape accuracy for spherical optics, such as power, irregularity and Zernike polynomials. Mid-spatial frequency (MSF) errors are on a smaller physical scale, and correspond to ripple, waviness and slope error. High frequency errors are essentially surface roughness, rather than shape errors.
In terms of design, what tends to cause low and mid-spatial frequency errors during manufacture? In other words, what can a designer do to avoid or minimize these errors and, therefore, create designs that are inherently easier to fabricate? Coherent, Inc. has decades of experience producing freeform optics, and has established that one of the most important predictors of freeform manufacturability is the rate of change of curvature of the optical surface shape. Specifically, rate of change of curvature is a useful surrogate metric for manufacturing complexity because it correlates directly to process parameters that affect polishing time and test complexity.
The next chart summarizes the relationship between surface error (combined low and mid-spatial frequencies) and the rate of change of curvature for a number of different actual optical components. It comprises measurements from optics fabricated at Coherent using various production methods and substrate materials.
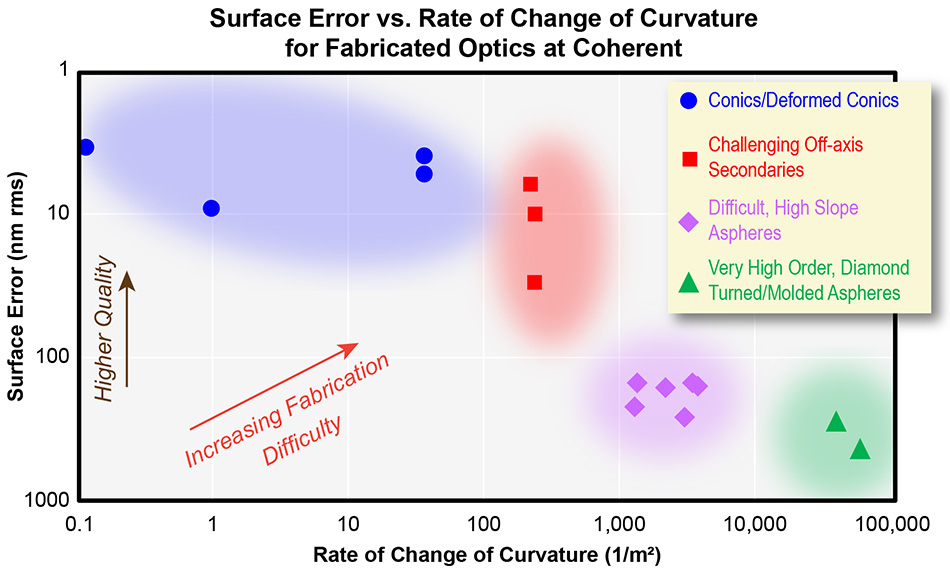
The y axis of the graph shows surface error decreasing vertically, so the closer a point is to the top of the graph, the better its overall surface accuracy. The x axis plots rate of change of curvature, not curvature. Note that both axes are logarithmic.
The inherent difficulty of fabrication increases from the lower left (lowest rate of change in curvature and most surface error) to upper right (most rapid rate of change of curvature and lowest surface error) in the graph. Predictably, the actual, measured data trends from upper left to lower right. Namely, the higher the rate of change of curvature, the larger the resultant surface error is in the finished optic.
What is not seen in this graph is the effort (e.g. time) required to obtain a given result. And, this is key, since it translates directly into cost. It is possible to produce the optics that would lie in the upper right quadrant of the graph (for example, “difficult, high slope aspheres”) at a higher surface quality level than shown here. But, accomplishing this in practice requires significantly more fabrication time, therefore stretching lead time and increasing cost. Thus, the graph portrays not so much what is “doable,” as what is “cost-effective.”
"The higher the rate of change of curvature, the larger the resultant surface error is in the finished optic. "
Results Discussion
This graph actually plots data from several distinct types of components, so it is worth reviewing each of those individually, to understand the key takeaways in each regime.
Conics/Deformed Conics
These relatively “simple” aspheric shapes are the easiest to fabricate. The data points shown here are for optical components in the 30 mm to 1.5 m size range. Optics of virtually any substrate material, including aluminum and silicon, can be fabricated to low residual figure error in this rate of change of curvature regime. The manufacture of optics in this range typically does not involve significant compromises in figure, roughness or MSF error in order to obtain the nominal shape. These surfaces can generally be made to virtually any desired quality level as long as the rate of change of curvature stays below ~100/m².
Challenging Off-axis convex freeforms or “Secondaries”
These data points were obtained for relatively small (≤ 50 mm diameter), typically convex mirrors in aluminum, glass, silicon, and silicon carbide. Typically used as a secondary mirror in many classical telescope designs, this class of components gets progressively more difficult to fabricate to a low surface error above a rate of curvature change of about 250/m². Also, convex mirrors can be challenging because they are frequently specified with a low freeboard (the distance from edge of the clear aperture to mechanical edge of part), and the need for a quick transition from optical surface to mechanical edge does not accommodate sufficient area to support the polishing tool as it moves around the edge of the clear aperture.
Difficult, High Slope Aspheres
These higher slope (rate of change of curvature) components are where tradeoffs between figure, roughness and MSF must often be made to yield a part within a reasonable time and cost constraint. While it is possible to improve the surface error (especially MSF) for this class of optics, the fabrication techniques for accomplishing this are more limited (due to the high slope). Therefore, tight specifications can drive up costs rapidly.
Very High Order, Diamond Turned/Molded Aspheres
Parts with shapes having a rate of change of curvature in this regime (>10,000/ m²) are typically fabricated using techniques such as diamond turning and molding, rather than traditional polishing. The diamond turning process, in particular, often produces so-called “color” in an optic.
Summary
The data presented in this document is an attempt to establish what constitutes “best practices” in designing freeform optics. With the continued focus on developing Optical Telescope Assemblies for Proliferated Low Earth Orbits (LEOs) which rely heavily on freeform optics, the quality requirements will become more demanding, as will meeting cost and time targets. The graph shown here by no means represents all that can be accomplished – given an unlimited amount of time and effort. Rather, it attempts to define some limits for what is readily manufacturable, and to highlight the factors that are most likely to drive up component cost or lead time. Coherent, in particular, routinely fabricates freeform optics over nearly all the surface error/rate of curvature change space shown in the graph. A primary goal is to assist customers in achieving their design objectives in the most cost-effective and timely manner possible, and the hope is that this discussion will in aid that objective. Companies with complex freeform optics requirements should meet with their optics partner early in the design phase in order to identify efficiencies or tradeoffs that could reduce cost overruns and project delays.