Lasers in Display Fabrication: Excimer Laser Annealing
Coherent excimer lasers perform a key process that enables brighter, higher-resolution, more energy-efficient displays.
October 4, 2022 by Coherent
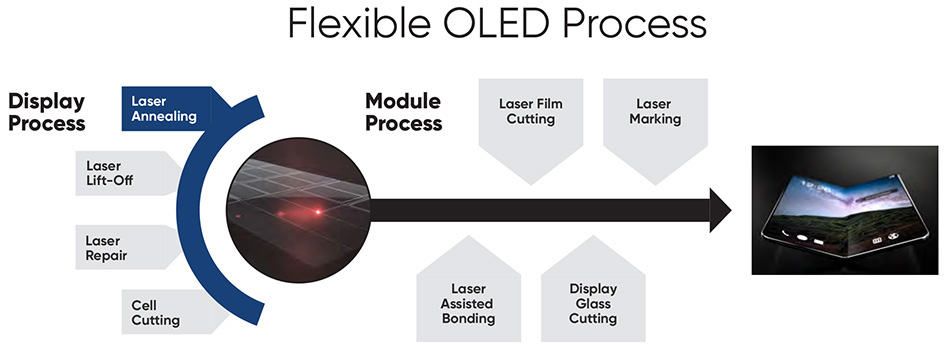
The AMOLED displays used in most cellphones today are utterly gorgeous – bright and sharp – and beneath the surface, manufacturers have engineered them to use less power. That’s important because the display typically uses more battery power than anything else in the phone. There’s an enormous amount of technology that’s been applied to actually make all this happen. And, Coherent lasers play an absolutely vital role in it. In this six-part blog series, we’ll look at some of the specific ways lasers are used to manufacture displays.
One of the most important processes powered by Coherent lasers occurs at the very first step in fabricating the device circuity. This is when a thin layer of silicon – the semiconductor at the heart of all modern solid-state electronics – is deposited on a large panel called the “mother glass.” Today, these mother glass panels are usually 1.5 m x 1.85 m (GEN 6.5), although phone makers want to make them even larger in order to lower the cost of individual displays.
Read the other blogs in this series on lasers in display fabrication |
|||
The problem is amorphous
But there’s a little problem with this layer of silicon. The chemical vapor deposition process used to create it produces amorphous silicon. In amorphous silicon, the individual atoms are arranged in an irregular and disordered fashion. Circuitry made from amorphous silicon doesn’t have good electronic properties, which means the display will be dimmer and use more battery power.
In contrast, the integrated circuits within the cellphone, and every other electronic device we use today, are made using single crystal silicon. The atoms are highly ordered in single crystal silicon; this arrangement yields really good electronic characteristics and is one of the reasons why modern microprocessors are so blazingly fast.
Unfortunately, the techniques used to create the single crystal silicon wafers used for microprocessors can’t be scaled up to make anything near the size of a mother glass panel. But it turns out there’s a third form of silicon – polycrystalline silicon – in which the atoms are fairly regularly ordered. The key metric here is electron mobility, and the electron mobility of polycrystalline silicon can be as much as 200 times higher than that of amorphous silicon (and single crystal silicon electron mobility is usually at least twice as good as polycrystalline silicon). The use of polycrystalline silicon is a major factor in why current displays are so fantastic.
A bright idea for display production
So, how do you get polycrystalline silicon? It’s not really all that hard – at least in theory. All that’s necessary is to heat up the amorphous silicon layer until it melts and then quickly cool it so that it resolidifies in the polycrystalline form.
The problem is that you need to heat the silicon up to about 600°C to melt it. But that high temperature, and the associated rapid thermal cycling, would damage panels made from regular glass and require the use of expensive, heat-resistant type glasses, instead. That would make displays much more expensive, especially as manufacturers scale up to ever larger glass panel sizes.
The solution is a technology called excimer laser annealing (ELA) which is used to create low-temperature polycrystalline silicon (LTPS). And it relies on Coherent excimer lasers.
The reason it uses excimer lasers is because they are the only source that can produce very powerful pulses of ultraviolet light. The silicon strongly absorbs ultraviolet light, and this, in combination with the high pulse energy, rapidly melts the thin silicon layer with just a few laser pulses. This near-complete melt is essential for getting the right polycrystalline formation and desired electronic characteristics.

The output of an excimer laser is formed into a thin line beam; this is rapidly scanned over the mother glass to efficiently perform ELA.
The high absorption of the silicon also prevents the UV light from penetrating much into the glass below – or polyamid (PI) layer in the case of flexible displays. So, the glass itself doesn’t get hot during ELA, even though the silicon is thoroughly melted. Because of this, ELA can be performed on standard, low-cost glass panels. This is why ELA is the only method for making LTPS for AMOLED cellphone displays.
To perform ELA on large mother glass substrates, the normally rectangular beam from the excimer laser is reshaped into a thin line beam that is usually the width as the panel. This thin line beam is focused down onto the glass panel and scanned over its entire length to achieve the desired melting and resolidification of the silicon.
Production ELA
About 1.5 billion cellphones are made every year. Each of the top manufacturers make about one million phones every single day. Needless to say, these companies want their production processes to be incredibly reliable and low-cost. Because at these volumes, anything that holds up the assembly line even momentarily, or creates scrap product, costs a tremendous amount of money.
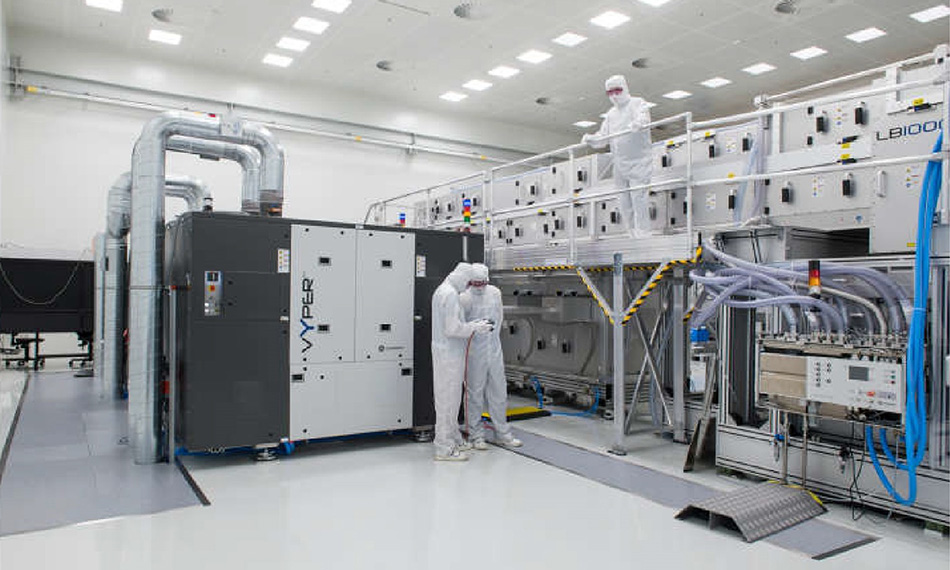
Coherent LineBeam systems are the cost-effective, high-volume ELA solution used by all major display manufacturers.
The only way for Coherent to really ensure that production ELA achieves the quality, reliability, throughput, and cost-characteristics that manufacturers demand is to supply integrated UV lasers and optical systems – our Coherent LineBeam. Because real world, high-volume ELA systems incorporate several different components, each of which has to perform well, and also has to work flawlessly with the other parts of the system. These components include:
- Excimer lasers – the Coherent VYPER series – which are built to deliver very high energy pulses at high repetition rates (to achieve the necessary throughput speeds), with extraordinary stability and long operational lifetime.
- LineBeam optics that take the rectangular excimer laser beam, reshape it into a long, thin line having extremely consistent intensity. This is necessary so that the characteristics of the ELA process don’t vary with position along the beam.
- Active monitoring and control systems to verify and guarantee process quality and consistency.
ELA is an indispensable tool in the production of high-quality flat panel displays. And, that’s not likely to change any time soon, because Coherent keeps scaling up our LineBeam systems to handle the larger sizes of mother glass that manufacturers want to use for the next generation of larger phone and tablet devices.