Los láseres de fibra avanzados ubican a los fabricantes de automóviles en el asiento del conductor
Los láseres de fibra de modo de anillo ajustable (ARM) de Coherent permiten la soldadura de acero de alta resistencia y otros materiales en estructuras livianas de asientos de automóviles.
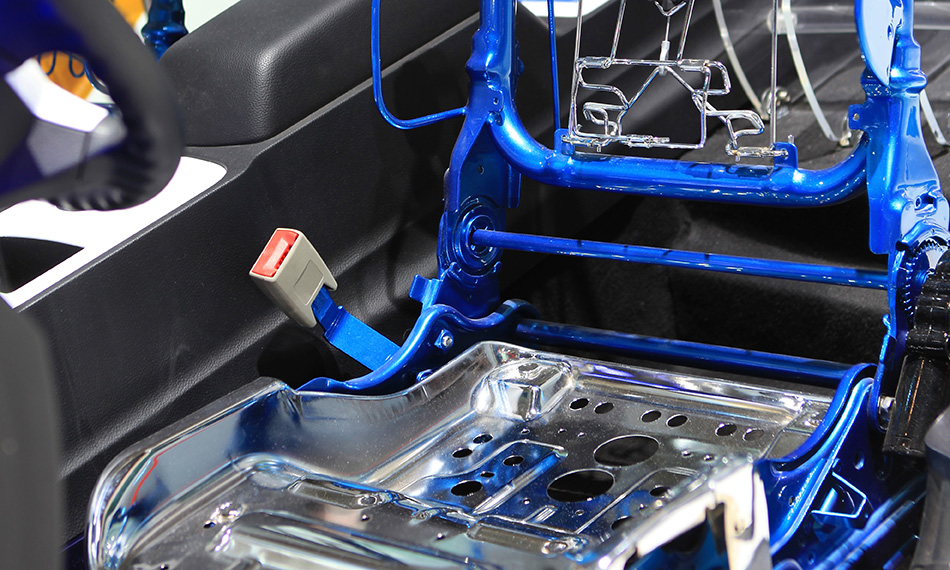
Cuando la mayoría de nosotros piensa en asientos de automóviles, nuestras preocupaciones suelen relacionarse con la comodidad u opciones de color, o tal vez opciones como la calefacción o masajes integrados. Sin embargo, para los ingenieros que diseñan y construyen asientos de automóviles, se trata de algo más que eso.
En primer lugar, por supuesto, está la seguridad. El conductor y los pasajeros se sujetan literalmente con correas a los asientos. En caso de accidente, la fuerza mecánica de la estructura del asiento es la primera línea de defensa para proteger a los ocupantes del vehículo y evitar lesiones.
Sin embargo, el otro aspecto a tener en cuenta es el peso. Ya que hacer una estructura más fuerte, por lo general, significa que también sea más pesada. A su vez, los fabricantes de automóviles tienen una presión terrible por reducir el peso del vehículo. Esto mejora la eficiencia de combustible y reduce las emisiones de los coches que funcionan con gasolina, además de aumentar la autonomía de los vehículos eléctricos. Lograr esto es tan importante en la industria automotriz que hasta existe un término específico para ello: “aligeramiento”.
Quítese un peso de encima con el acero de alta resistencia
¿Cómo puede hacer asientos de coches que sean resistentes y livianos? La clave es utilizar materiales que sean resistentes por naturaleza, como acero, titanio, y aleaciones de magnesio, para que los componentes individuales puedan ser más delgados y livianos sin sacrificar la resistencia mecánica. A su vez, utilizar plásticos, compuestos u otros materiales verdaderamente livianos para piezas que no contribuyen de manera significativa a la resistencia o rigidez del asiento.
Uno de los últimos desarrollos en el diseño de asientos para automóviles es el uso de acero de baja aleación y alta resistencia (HSLA) y acero avanzado de alta resistencia (AHSS). Estos materiales tienen una relación de resistencia y peso aún mayor que otros aceros, por lo que resultan muy útiles para alcanzar los objetivos de aligeramiento. Los fabricantes de automóviles los usan en marcos desde hace un tiempo y ahora también comienzan a emplearlos para los asientos.
El desafío de soldar acero de alta resistencia
Los asientos de coches modernos constan de una cantidad de piezas individuales ensambladas en estructuras bastante complejas. Muchas veces, el metal y otros materiales incluso se combinan en compuestos multicapa.
La soldadura por láser remota (donde el cabezal de procesamiento láser está a una distancia significativa de la pieza) ha demostrado ser una herramienta muy útil para la fabricación por varias razones. En primer lugar, puede procesar fácilmente las formas tridimensionales complejas de los componentes de los asientos. Y, en particular, si se la implementa con el uso de un láser de fibra de varios kW o un láser en estado sólido, brinda soldaduras uniformes y constantes con la profundidad de penetración necesaria para unir varias capas de metal grueso intercalado. Además, es un método rápido y flexible.
Sin embargo, existen problemas con la soldadura del acero de alta resistencia y el uso de láseres de fibra tradicionales. Uno de estos problemas son las salpicaduras. Las salpicaduras producen una soldadura con mucha porosidad y defectos, lo que se traduce en una resistencia mecánica deficiente. Las salpicaduras empeoran a medida que aumenta la velocidad de soldadura y esto limita el rendimiento de producción.
Otro problema es la profundidad de penetración inconsistente. Esto da como resultado una soldadura que no tiene la misma resistencia mecánica a lo largo de toda la línea.
El agrietamiento del material también es un problema con los láseres de fibra tradicionales y reduce la resistencia mecánica. El agrietamiento ocurre cuando el material se enfría demasiado rápido. Por lo general, ocurre en el extremo del cordón de soldadura, donde la potencia del láser se ha apagado de manera repentina.
Un problema adicional con el enfriamiento rápido del acero de alta resistencia es que, a veces, se genera una forma cristalina llamada martensita. Si bien es resistente, la martensita también es la forma de acero más frágil. Esto significa que se puede agrietar si se le somete a demasiada tensión durante el uso.
Los láseres de fibra de modo de anillo ajustable (ARM) no se agrietarán bajo la presión de la soldadura de acero de alta resistencia
La clave para evitar todas estas dificultades es distribuir la energía del láser en un área más grande y tener un control más preciso sobre la distribución de la energía del láser dentro de esa área. Esto permite gestionar con mayor cuidado tanto el gradiente de temperatura como la velocidad de enfriamiento del material. Si se realiza correctamente, esto elimina las salpicaduras, el agrietamiento y la formación de martensita.
Coherent ha desarrollado la tecnología de láser de fibra de modo de anillo ajustable (ARM) para brindar exactamente este tipo de control preciso sobre el calentamiento y el enfriamiento del material durante la soldadura. El láser ARM utiliza una salida de doble haz. Esto es un punto central rodeado de un segundo anillo concéntrico de luz láser. La potencia de cada uno de estos haces se puede configurar de forma independiente, lo que permite el control deseado. Los láseres ARM ya se utilizan en otras aplicaciones de unión automotriz exigentes, como soldadura de baterías y soldadura de cobre, que requieren este mismo tipo de delicadeza.
Recientemente, un fabricante de asientos automotrices solicitó a Coherent Labs que realizara una serie de pruebas de soldaduras en materiales de acero de alta resistencia. Específicamente, estas involucraban placas de HSLA de soldaduras de traslape de varios espesores, mediante un láser de fibra Coherent HighLight FL8000-ARM. Se utilizó una receta especial de terminación de soldadura que redujo de forma independiente la potencia en los haces central y de anillo.
En estas pruebas se demostraron con éxito soldaduras sin grietas ni salpicaduras a velocidades de proceso de hasta 8,8 m/min para la combinación de materiales más delgados (2 mm de espesor total) y 6,3 m/min para los más gruesos (5,7 mm de espesor total). Estas velocidades son sustancialmente más altas que las obtenidas con los láseres de fibra tradicionales. En todos los casos, la penetración de la soldadura fue muy uniforme gracias al control de potencia de circuito cerrado y la insensibilidad inherente a la retrorreflexión del láser Coherent FL-ARM.
En estos resultados de pruebas se muestra que Coherent HighLight FL-ARM puede brindar soldaduras de alta calidad y pocos defectos en aceros de alta resistencia. Las altas tasas de rendimiento logradas y la confiabilidad inherente de esta tecnología de láser de fibra la convierten en una solución rentable para aplicaciones de producción de asientos para automóviles. Esto ubica a los fabricantes de automóviles en el asiento del conductor al implementar los diseños más avanzados y les brinda tranquilidad a los consumidores con una sensación de comodidad y seguridad.
¿Desea obtener más información sobre esta aplicación? Obtenga más detalles en nuestro Resumen de la solución aquí.
Recursos relacionados