Fiber Lasers Power Battery Welding
Advanced laser technology delivers high-speed precision joining necessary for economical fabrication.
August 25, 2021 by Coherent
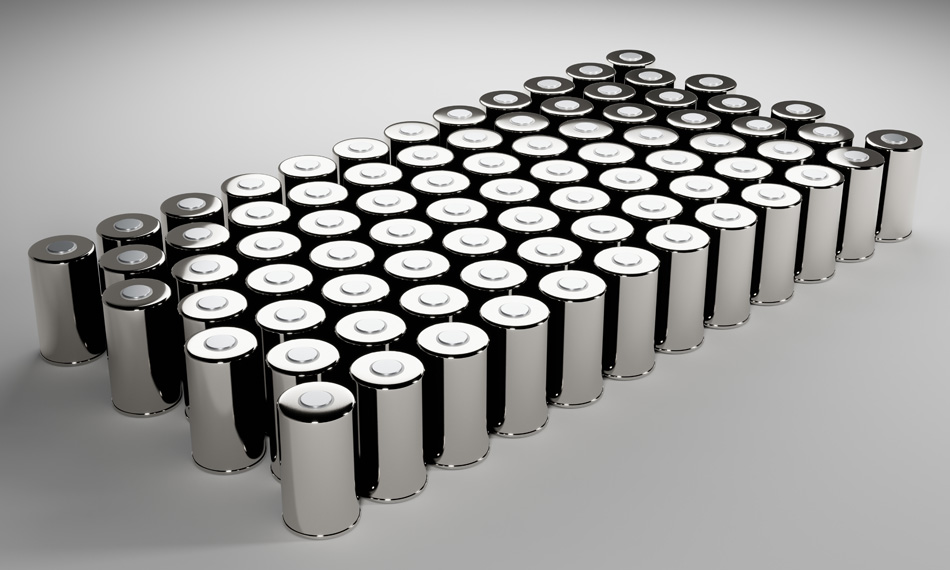
The design and construction of larger form factor cylindrical batteries for electric vehicles promises to deliver several benefits to auto manufacturers and consumers alike. For drivers, these include greater range, more power, faster charging times, longer lifetime, and better operation in cold weather. Manufacturers can look forward to more streamlined production and reduced costs.
Watts so tricky about making EV batteries?
There are a number of different large form factor cylindrical battery designs being pursued by various manufacturers. Each of these presents its own specific fabrication challenges, particularly for joining processes. For example, some electric vehicle battery designs incorporate current collectors, and these must be joined to the jelly roll with very precise control over weld depth. This is necessary in order to avoid damaging the separators, which could lead to a short circuit within the cell. Similarly, terminal-to-collector welding also requires careful penetration control. It’s particularly important to limit how much heat is pumped into the battery during this operation, because it could cause melting or damage of the polymer isolators.
Cap sealing is another joining process that has been successfully performed with mechanical crimping in the past on smaller form factor batteries. But, crimping doesn’t translate well to the larger cells, so a new approach is required.
What are the current requirements?
There are a number of other welding processes involved in making batteries, and again, these vary by manufacturer and design. But the most challenging and sensitive ones all share certain common requirements, including the need for:
- Minimal heat affected zone
- Accurate penetration depth control
- Spatter elimination
- High process speed (typically somewhere in the 200 – 500 mm/sec range)
Plus, some important battery joining processes also require welding of dissimilar metals.
Each of these requirements has presented difficulties in the past, and there really hasn’t been a single joining technology that could perform well on every single process. As a result, manufacturers have pursued a variety of solutions. These include green wavelength lasers for welding copper (to overcome the low absorption of this material with infrared sources), and non-laser based methods like ultrasonic welding for foil-to-tab joining.
Get ARMed with the right laser
Coherent has developed a new type of laser that is more broadly applicable than anything before. This is possible because this technology provides an unprecedented degree of control over how laser energy is delivered to the work surface – both in terms of spatial distribution and over time.
The key innovation is Adjustable Ring Mode (ARM) technology — a fiber laser whose beam consists of a central spot surrounded by another concentric ring of laser light, as opposed to the traditional single-spot output. Most importantly, the power in the center and ring spots can be independently controlled, and even modulated. The graphic shows how this approach delivers tremendous flexibility in exactly how the laser energy is distributed during welding.
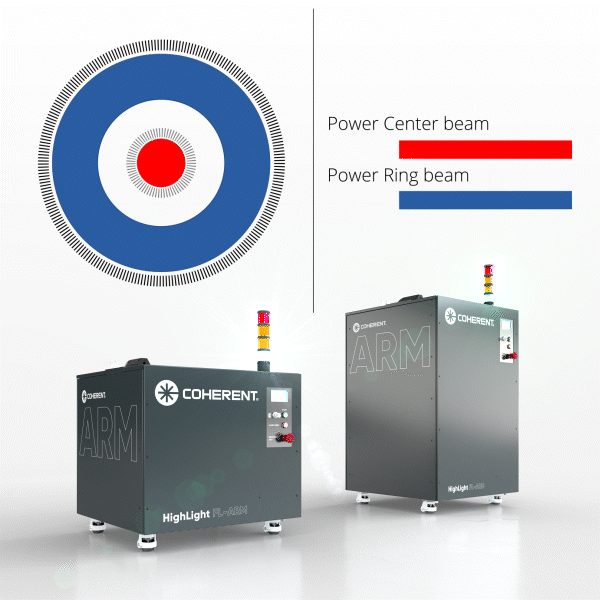
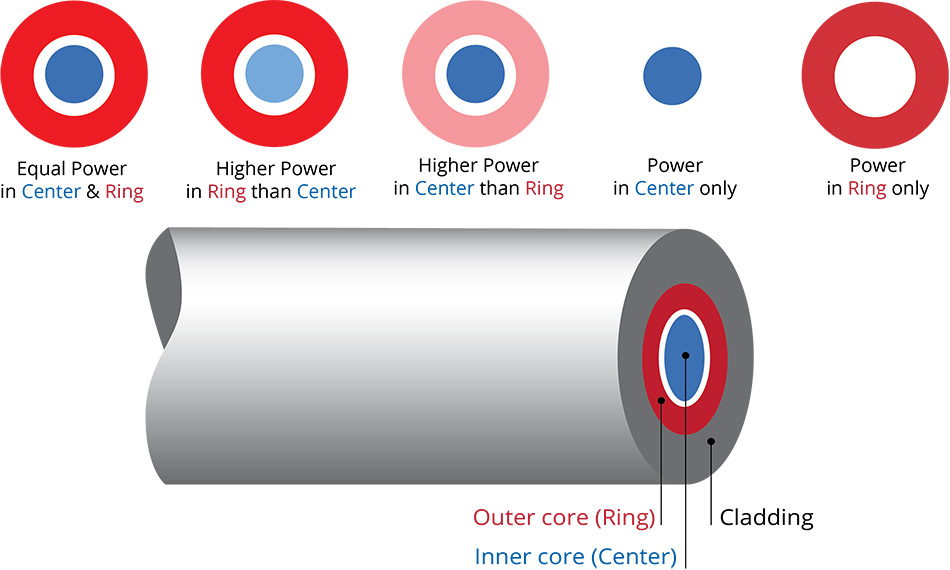
Image: Basic FL-ARM Focused Spot Power Patterns.
The benefit of ARM technology is that it enables very precise control over melt pool dynamics. This provides more consistent and controllable processing, and virtually eliminates spatter. This type of laser is particularly useful for welding copper, since the ring beam can be used to pre-heat the material, which substantially increases it’s absorption of infrared light. Also, a high-power density, center-beam option provides for reliable coupling of the IR light into the copper. Along with the practical and cost advantages of fiber lasers, this makes the ARM fiber laser a very attractive alternative to green solid-state lasers for copper welding.
Having a single type of laser source that can accomplish so many different tasks provides manufacturers with greater flexibility and economy. For example, the output from one laser can be shared between multiple processes using beam switches. This streamlines and simplifies production. Also, the use of a common laser type at multiple points in the production process reduces spare parts inventory, and it provides a redundancy that helps minimize maintenance or repair downtime.
Larger form factor EV battery designs promise to make electric vehicles more practical for drivers and less costly for manufacturers to build. But, these cells’ larger form factor, higher drive current, and increased production throughput expectations necessitate laser-based welding technologies. The Coherent ARM FL fiber laser offers the best and most economical solution for the precise and demanding joining tasks required for their production, and have already proven their effectiveness in other battery processing tasks.
Related Resources