CUSTOMER SUCCESS STORY
Versatile Laser Cutting for Neurological Sub-Assemblies
The Challenge
Motion Dynamics (Fruitport, MI) is a contract manufacturer specializing in custom micro springs, medical coils, and wire components. They have a hard-earned reputation for solving challenging problems in the shortest possible time, no matter how difficult or seemingly impossible. They have particular expertise in designing and manufacturing complex assemblies for neurovascular procedures – for applications such as steerable catheter devices, including “pull-wire” assemblies.
President Chris Witham states, “The company’s medical device business is based on a highly focused business model in neurovascular products, where we can offer differentiated results in terms of design, execution, and service. We need fast, versatile, and easy-to-use laser cutting machines to generate the components for high-value ‘difficult’ assemblies.” He explains that cutting flexibility and ease of use are critical machine requirements for Motion Dynamics, because these components are quite diverse in terms of size, shapes, and material, with only small to medium batches in most cases.
The Solution
The company had several years of experience using a StarCut Tube machine from Coherent. Until recently, this machine was available with a choice of either an ultrashort pulse laser with femtosecond pulsing, or a more traditional fiber laser featuring much slower pulsing. Witham explains that they chose a USP laser for this earlier machine, because it delivers superior edge quality and minimized kerf, which are critical in many of their components. In fact, the USP laser usually eliminates the need for mechanical post-processing. He adds that “There is no material we use that cannot yet be cut by a USP laser, including the tiny gold components used as radio-opaque markers in some of our products.”
When their market growth meant that even two 40-hour/week shifts was not enough to keep pace with demand for their neurovascular assemblies, they decided to purchase another StarCut Tube machine. However, some of the components used by Motion Dynamics are made of thicker (up to 20 thou) material and could be more economically cut by using the faster processing speed of a fiber laser.
The optimum solution was the latest StarCut Tube Hybrid machine that includes both a femtosecond laser and a fiber laser, all integrated in the same compact platform with the same user-friendly GUI.
The Result
Witham states that the new machine’s flexibility is proving to be a major advantage, “Now we can choose which overall process – USP alone or fiber and post-process – is the most cost-effective for each component. This machine is even allowing us to explore the possibility of mixed processing of the same component, particularly where larger diameters and wall thicknesses are involved: namely fast cutting with the fiber laser followed by fine cutting with the femtosecond laser.” He expects that the USP laser will still remain their first choice in many instances because the majority of their laser cutting involves stainless tubes with wall thicknesses between four and six thou.
“The StarCut Tube Hybrid allows to cost-optimize the cutting of every component, even individual cuts within the same component."
— Chris Witham, President, Motion Dynamics, Fruitport, Michigan.
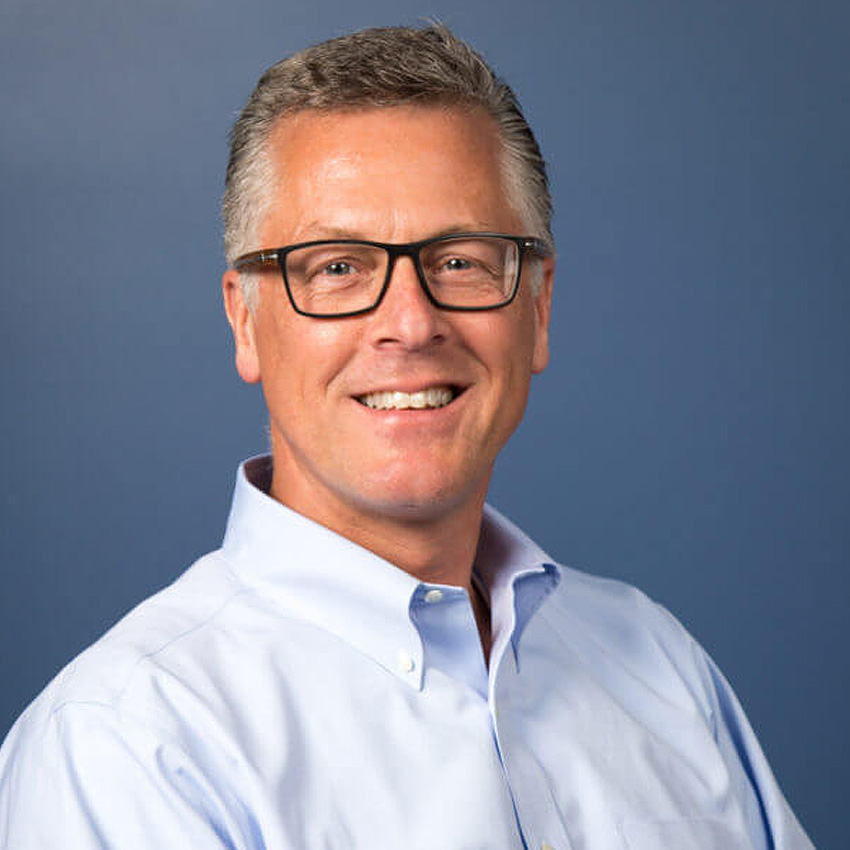
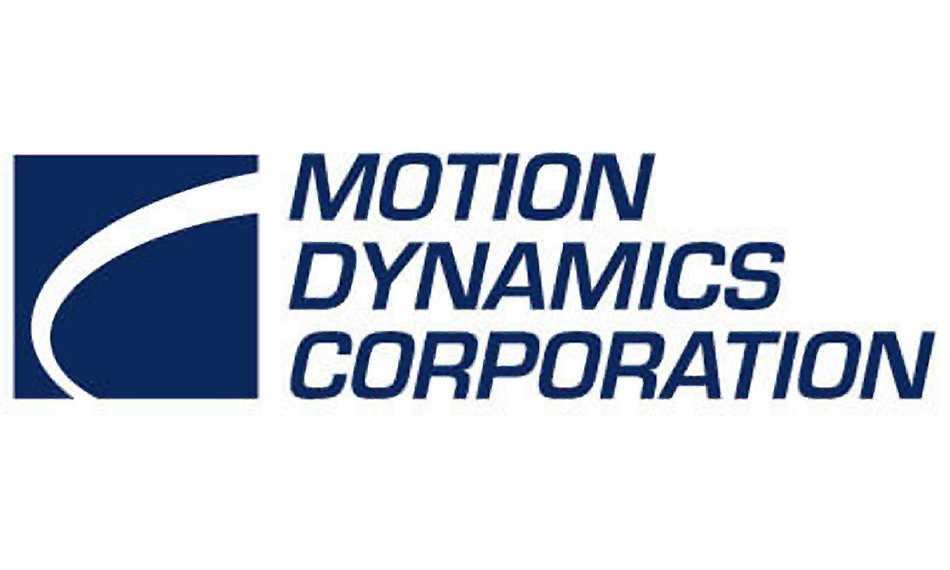
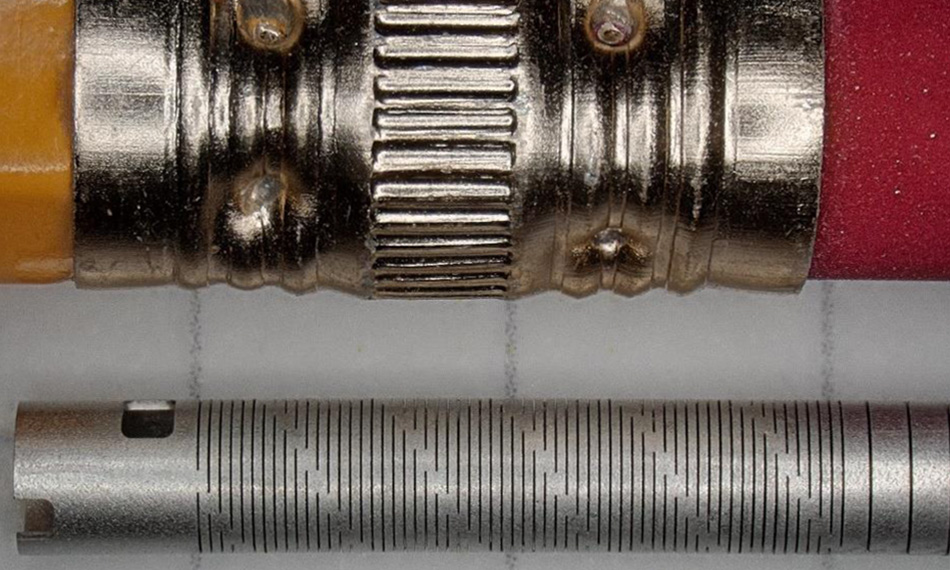
Figure 1: Laser cutting of flexible stainless steel delivery tubes with wall varying thicknesses.