Coherent Leads the Way to Larger Displays
Coherent picosecond USP lasers deliver the power needed for ultra-precision cutting of large displays at the high speeds required for economical production.
June 1, 2022 by Coherent
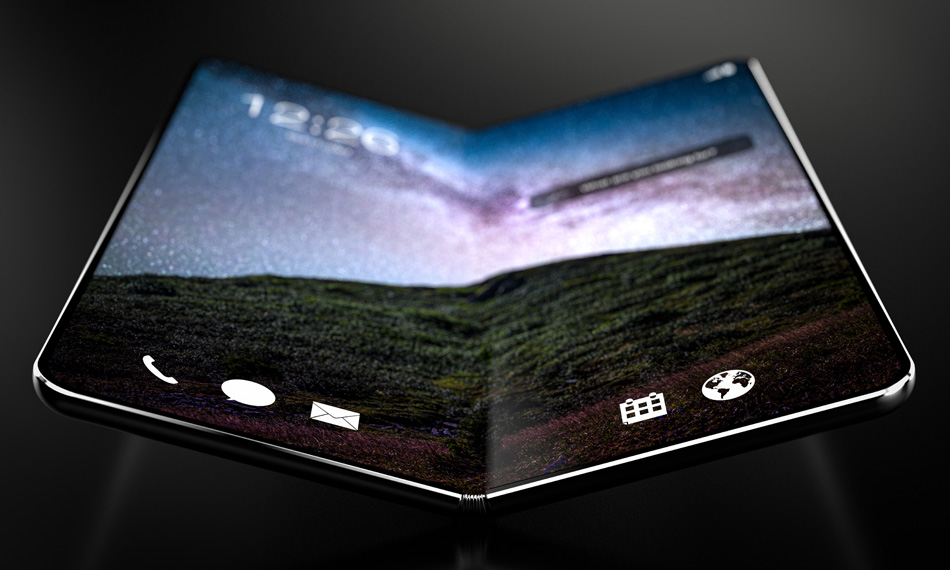
Organic light-emitting diode (OLED) technology is used to make the gorgeous displays currently used in most high-end smartphones. Now, some manufacturers would like to use those same OLED displays in larger devices, such as foldable smartphones and tablets.
The big difference between smartphones and TVs
Since there are already large-screen OLED TVs on the market, it might not seem difficult to make larger mobile devices having OLED displays, too. But, that’s not the case.
Part of the reason is that the OLED technologies used for phones and TVs are somewhat different. This is because these products don’t have the same requirements for electrical efficiency, lifetime, and other characteristics.
Another reason is economics. There are a few million large-screen OLED TVs produced every year. In contrast, well over half a billion smartphones with OLED screens are made annually.
As a result, various manufacturers have specialized in making one or the other of these types of products – but not both. And each has tuned and optimized every aspect of their technology and production methods for the type, physical size, and quantity of displays that they make.
Only USP lasers can really cut it
To understand the challenge that display manufacturers face, you need to know that they produce a large number of phone displays simultaneously on large glass panels. This panel is usually a couple of meters wide by a meter in length. The individual displays are eventually cut out of it.
Now, as display size increases, manufacturers can’t fit as many units on a fixed-sized glass panel. This makes larger displays inherently more expensive to produce because processing the large panel costs about the same amount no matter how many individual displays you get out of it. So, if you end up with fewer displays, the cost per unit is higher.
One way to improve the economics of this situation is to speed up production so that the same number of units is produced in a given time, even as the displays get larger. But, speeding up the step where the individual displays are cut out isn’t so easy.
This is because the display is a sandwich of numerous layers of different materials, many of which are delicate and heat sensitive. Plus, the active area of the display (the part that shows the image) on modern phones often goes right up to the physical edge of the device. So, the cutting process must not do anything to damage the display circuitry, or affect its functionality, or even change the cosmetics.
The process of cutting these displays out is so exacting that the only way to do it is using ultraviolet (UV), ultrashort pulse (USP) lasers. That’s because UV-USP lasers will process nearly any material equally well, so they have no trouble cutting something that consists of several layers of different materials. With longer pulse-length lasers, the different absorption characteristics of each separate material make this difficult to do. But, USP lasers utilize “non-linear” absorption, meaning that the absorption (and cutting ability) of the laser light doesn’t vary much by material.
Another benefit of USP lasers is that they cut with very little “heat-affected zone” (HAZ) – meaning that you can put circuitry right near the cut edge without difficulty. And, they cut glass with very high edge-quality, and this improves strength and break resistance. This is important because phone displays are touched frequently – and even sometimes dropped.
A big future for USP laser cutting
So, to cut faster – which is what’s needed to improve the economics of larger OLED display manufacturing – requires a USP laser with higher (average) output power. Coherent meets this need with our HyperRapid NXT products. In particular, our 50W UV HyperRapid NXT allows our customers to increase output power from their existing installed base of 30 W UV lasers.
The new high-power version is already being put into production by display manufacturers for some of the key steps in OLED cutting. This will allow them to future-proof their production lines, even if they move to larger displays. And, since they’re already familiar with Coherent picosecond lasers, and understand their operational and cost-of-ownership characteristics, they can make this move without concern that they’re staking their future on unproven technology.
Discover more about how Coherent is driving innovation in display manufacturing and performance.