ARM Fiber Lasers Enable Global Automotive Mass Production
With exceptionally accurate and consistent unit-to-unit output characteristics, ARM fiber lasers improve automotive production efficiency and reduce costs.
July 08, 2024 by Coherent
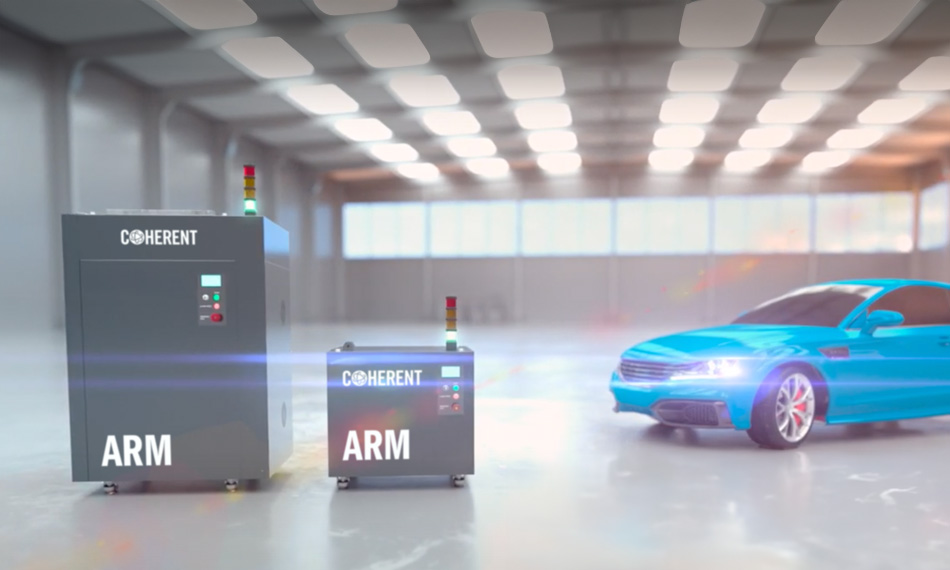
At Coherent, we hear it all the time. Automotive and other high-volume OEMs tell us that line-to-line inconsistencies in their laser welding systems drives them crazy.
The bottom line is this: manufacturers strive for uniform global production processes to minimize cost and, most importantly, safety and recall risks. In a production utopia, they would set up a new assembly line, integrate a laser and always get the same results. This means that every part or vehicle they make – regardless of location and date of manufacture – looks and functions identically.
If different welding lasers don’t perform in exactly the same way using identical settings, manufacturers must spend time and money “fine-tuning” each laser and process recipe to achieve consistent results between production lines. Plus, manufacturers want to readily disseminate process improvements that they’ve developed to all their facilities globally without a need to deploy experts to “fine-tune” each line.
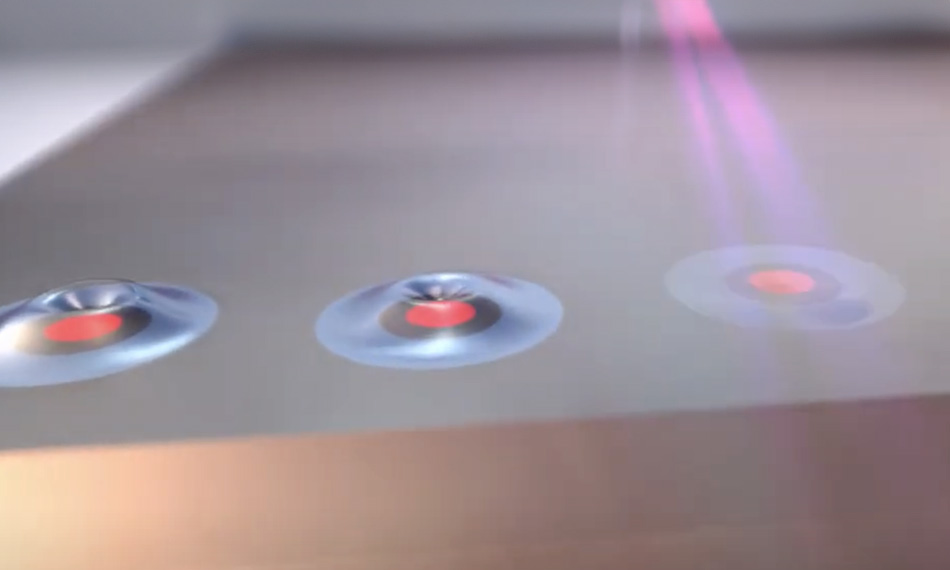
The exceptional output consistency of Coherent ARM lasers greatly simplifies implementation for automotive manufacturers.
Coherent ARM Fiber Lasers Ensure Consistency & Repeatability
Why do manufacturers come to Coherent with this problem? Because our unique, patent protected Coherent ARM FL Fiber Laser design ensures the necessary consistency. With our ARM Fiber Laser, no fine tuning or compensation of the process recipe is required from laser-to-laser or plant-to-plant.
How do we accomplish what other fiber laser makers can’t? Our ARM Fiber Lasers are designed from the outset to deliver the operational accuracy and consistency necessary to achieve low unit cost, high yield manufacturing without extraordinary effort. They ensure that, once a process recipe is developed, the laser will faithfully reproduce it in real-world use. Every individual unit will deliver consistent performance in the same way – day after day, and line to line.
How good are we really talking about? The graph shows actual test data for the output power of 90 different Coherent ARM Fiber Lasers. Each was set to deliver 2.575 kW. The standard deviation in power readings, measured with an external power meter, was 5.4 W – only 0.2%. This means that all these lasers would produce virtually identical results for a given welding task. Again, this ensures that a process recipe will be faithfully reproduced over time and across multiple lasers.
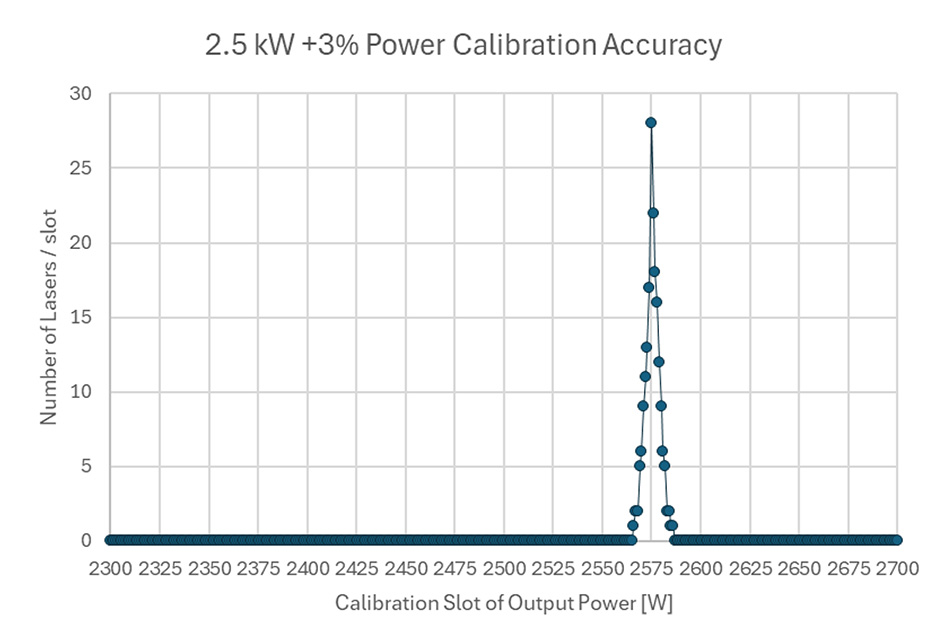
Test results from 90 separate Coherent FL-ARM lasers shows an extraordinary level of unit-to-unit output power consistency.
To achieve this high level of consistency, Coherent has implemented multiple features within the ARM architecture. One key feature is our patent-protected (USA, Europe, S. Korea, Japan, China) independent control of ring and center beam power – supported by highly sophisticated, separate closed-loop power control for each. The laser employs numerous sensors to measure and control the actual output power for each waveguide and continuously adjust it, thus maintaining extremely consistent welding performance.
Power control for high-speed applications requires very robust and fast control systems. In copper welding, for example, to maintain our industry-leading penetration depth consistency of 2% – even for very thin sheets – standard microprocessor control is no longer fast enough.
One way we increase the response of the ARM laser control electronics is by incorporating the same high-speed Field Programmable Gate Array (FPGA) technology that is enabling 5G telecom. This facilitates precision monitoring at not just one, but at the many wavelengths of light that lasers generate and encounter from the process.
At such high power, speed, and control, we must also employ some of the most sophisticated laser protection systems on the market. Passive back reflection protection is today largely considered “old news” for fiber lasers. But the traditional approach used by the rest of the laser industry – namely, to simply reduce laser output power when back reflections are detected – is insufficient for applications that demand high precision, yields, and repeatability. This is particularly true when welding copper and other bright materials.
Instead, our ARM laser cavity uses our own, IP-protected single resonator technology with an integrated, five-stage protection scheme. This approach delivers better stability and less operational sensitivity than the MOPA designs which some lower-cost systems rely on. In the case of ARM lasers, this level of stability and protection truly enables the optimal production performance for our customers.
The unmatched output consistency and back reflection immunity of Coherent ARM Fiber Lasers enables automakers and other high-volume OEMs to meet their most demanding welding challenges head-on.
Learn more about and how the Coherent ARM FL can power your production line.