Advanced Fiber Lasers Put Automakers in the Driver’s Seat
Coherent Adjustable Ring Mode (ARM) fiber lasers enable welding of high-strength steel and other materials in lightweight automobile seat structures.
Updated: Sep 22, 2022 by Coherent
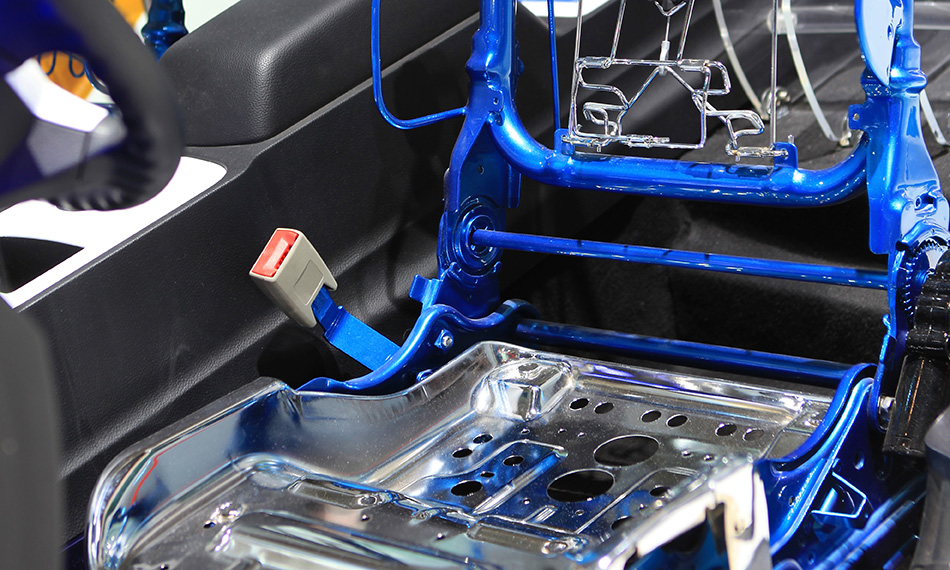
When most of us think about car seats, our concerns are usually about comfort and color choices, or maybe options like built-in heating or massaging. But, for the engineers that design and build automotive seating, there’s quite a bit more to it.
First of all, of course, is safety. The driver and passengers are literally strapped into their seats. In a crash, the mechanical strength of the seat structure is the first line of defense in protecting vehicle occupants and preventing injury.
But, the flip side of that is weight. Because making a structure stronger usually means making it heavier, too. And, auto manufacturers are under tremendous pressure to reduce vehicle weight. This improves fuel efficiency and cuts emissions for gas-powered cars, and increases the range of electric vehicles. Doing this is such a big deal in the automotive industry that there’s even a specific term for it – “lightweighting.”
Take a load off with high-strength steel
How do you make car seats that are both strong and light? The key is to use materials that are inherently stronger – like steel, titanium, and magnesium alloys – so that the individual components can be thinner and lighter without sacrificing mechanical strength. And, to use plastics, composites, or other really lightweight materials for parts that don’t contribute significantly to the seat’s strength or rigidity.
One of the latest developments in car seat design is the use of high-strength, low-alloy steel (HSLA) and advanced high-strength steel (AHSS). These materials have an even higher strength-to-weight ratio than other steels, so they’re really useful in hitting lightweighting goals. Automakers have already been using them in frames for some time, and now they’re making their way into seating, too.
The challenge of welding high-strength steel
Modern car seats consist of quite a number of individual parts assembled into fairly complex structures. Metal and other materials are even sometimes combined in multi-layer composites.
Remote laser welding (where the laser processing head is a significant distance away from the part) has proven to be a very useful tool for manufacturing these for several reasons. First, it can easily process the complex three-dimensional shapes of seat components. And, particularly when implemented using a multi-kW fiber laser or solid-state laser, it delivers uniform, consistent welds with the penetration depth needed to join several layers of thick, sandwiched metal. It’s also a fast and flexible method.
However, there are issues with welding high-strength steel using traditional fiber lasers. One of these is spatter. Spatter produces a weld with higher porosity and defects, which means poor mechanical strength. Spatter gets worse as welding speed increases, so this limits production throughput.
Another issue is inconsistent penetration depth. This results in a weld that doesn’t have the same mechanical strength along its entire line.
Material cracking is also a problem with traditional fiber lasers, and again reduces mechanical strength. Cracking happens when the material cools too fast. It usually occurs at the end of the weld seam where the laser power has been suddenly turned off.
An additional problem with the rapid cooling of high-strength steel is that it sometimes creates a crystalline form called martensite. While strong, martensite is also the most brittle form of steel. That means it can crack when subjected to too much stress in use.
ARM fiber lasers won’t crack under the pressure of welding high-strength steel
The key to avoiding all these difficulties is to spread out the laser energy over a larger area, and to have more precise control over the laser energy distribution within that area. This enables both the temperature gradient and cooling rate in the material to be managed more carefully. If done right, this eliminates spatter, cracking, and martensite formation.
Coherent has developed Adjustable Ring Mode (ARM) fiber laser technology to deliver exactly this kind of precise control over material heating and cooling during welding. The ARM laser utilizes a dual-beam output. This is a central spot surrounded by a second, concentric ring of laser light. The power in each of these beams can be independently set and even modulated, and this enables the desired control. ARM lasers are already finding use in other demanding automotive joining applications, like battery welding and copper welding, that require this same kind of finesse.
Recently a large manufacturer of automotive seating asked Coherent Labs to conduct a series of welding tests on high-strength steel materials. Specifically, these involved lap welding HSLA plates of various thicknesses using a Coherent HighLight FL8000-ARM fiber laser. A special weld termination recipe was utilized that independently ramped down the power in the center and ring beams.
This testing successfully demonstrated spatter-free, crack-free welds at process speeds of up to 8.8 m/min for the thinnest material combination (2 mm total thickness) and 6.3 m/min for the thickest (5.7 mm total thickness). These speeds are substantially higher than those achievable with traditional fiber lasers. In all cases, weld penetration was highly uniform thanks to closed-loop power control and the inherent back-reflection insensitivity of the Coherent FL-ARM laser.
These test results show that the Coherent HighLight FL-ARM can deliver high-quality, low defect welds in high-strength steel. The high throughput rates achieved, and the inherent reliability of this fiber laser technology makes it a cost-effective solution for automotive seat production applications. This puts automakers in the driver’s seat when implementing the most advanced designs, and allows consumers to rest easy with a feeling of comfort and safety.
Do you want to learn more about this application? Then read more about the details in our Solution Brief here.
Related Resources