WHITE PAPER
"Powering e-mobility: Welding copper with the Adjustable Ring Mode fiber laser
Overview
While fiber lasers are the dominant laser source for welding, their infrared output is highly reflected by some metals, especially copper, which limits their effectiveness with these materials. As a result, high-power, solid-state green lasers have emerged as a possible alternative for copper welding because these wavelengths are more strongly absorbed by that metal. But, these green lasers possess several practical limitations which ultimately result in higher cost of ownership. This document presents the results of recent copper welding tests which were performed successfully with a new type of adjustable ring mode (ARM) fiber laser having a high brightness center beam. Here, the high brightness ARM laser delivered excellent weld quality, and better penetration at various weld speeds, than commercially available kW class green lasers. These results indicate that this technology could bring all the cost, reliability, and practical advantages of fiber lasers to the demanding task of copper welding.
E-mobility manufacturing
The boom in E-mobility manufacturing is the main factor driving a significant increase in the demand for copper welding solutions. Copper possesses a number of desirable electrical, thermal, mechanical, and cost characteristics as compared to other metals, which is why it is employed throughout electric vehicles – in the stators of the electric motors themselves, in the power distribution system (busbars, etc.), and within batteries. And, manufacturing many of these components and systems involves welding copper.
However, the same high electrical and thermal conductivity characteristics that make copper ideal for these applications also make it challenging to weld with traditional fiber lasers. Specifically, its electronic properties make it highly reflective at the near-infrared wavelength of fiber lasers. And, it’s excellent thermal conductivity necessitates the input of a large amount of laser energy in order to melt the material and initiate the welding process.
As a result, when using a traditional fiber laser, very high power is typically required in order to achieve the power density necessary to initially melt the material. But, this “brute force” approach makes the welding process unstable, and extremely sensitive to minor variations in the work surface. In particular, the presence of localized surface oxidation or small-scale surface structure inhomogeneities can result in process instabilities. The final result may be inconsistent welds, poor surface quality, and porosity.
Solid-state green lasers
Copper is nearly an order of magnitude more absorptive in the green than the near infrared. Thus, the energy from a green laser can be more efficiently coupled into the work piece, resulting in a more stable and less sensitive process than possible with traditional fiber lasers. As a result, high power, solid-state, green lasers are being utilized by a few manufacturers, and evaluated by many more.
However, there are some significant practical issues with deploying high power green lasers in e-mobility manufacturing. Some of these derive from the inherent properties and construction of these green lasers themselves.
The laser materials used for solid-state green fiber or disk lasers produces near infrared light; frequency doubling is used to convert the infrared to green output. While this process is widely employed in lower power (sub-kW) with great success, it starts to run into some difficulties at the mulit-kW power levels required for most industrial copper welding tasks. Specifically, the frequency conversion process itself is only about 50% efficient. So, a 4 kW, single mode, IR laser is needed to yield 2 kW of green output power. The unconverted energy becomes heat which must be removed by a water-cooled heat sink. This makes these lasers energy inefficient (resulting in higher cost of operation due to higher electrical power consumption), and requires a high volume of cooling water. Additionally, the doubling crystals degrade over time because of the high powers involved, and can create reliability and downtime problems if not carefully managed. Some designs utilize complex beam shifters and crystal temperature stabilizers to compensate for this.
"…a 4 kW, single mode, IR laser is needed to yield 2 kW of green output power."
Another practical issue with green lasers is that the standard optical fibers used for beam delivery are more readily darkened by green light, thus reducing their useful lifetime. Specialized fibers for green light can overcome this problem, but are more expensive and less readily available. The darkening effect also increases with the length of the fiber. This currently limits fiber length to 10 m, which reduces the flexibility in laser placement in the production environment. Plus, commercially available green, high power, CW lasers are currently limited to 2 kW of maximum output.
Most industrial lasers output in the near infrared, so the entire infrastructure for supporting them is based on this wavelength.For example, the available selection of process heads for for green lasers is limited, and often they need to be customized. Similarly, auxiliary lenses, protective cover glasses and other optical components are mostly for infrared lasers. Thus, a manufacturer already employing infrared lasers might need to maintain a greater stock of spare parts and consumables in order accommodate the use of green lasers in their operation without experiencing service delays and downtime.
The HighLight ARM Fiber Laser
Fiber lasers are much more electrically efficient than solid state green lasers. That is, to deliver a given output power, they require less electricity and produce less waste heat. This reduces cost of ownership and simplifies cooling. Plus, fiber lasers are very reliable. And, their infrared output is readily fiber delivered. But, despite these desirable features, they haven’t been widely used for welding copper in particular because of the issues previously identified.
Coherent introduced HighLight Series adjustable ring mode (ARM) fiber lasers several years ago to bring the cost and practical benefits of these sources to applications that were not being adequately addressed by traditional technology. Typically, these are tasks in which the spatial distribution of power and power density at the work surface must be carefully controlled in order to yield good weld quality (low spatter, minimal cracking and reduced porosity). Typical examples are zero gap welding of galvanized steel, spatter free welding of powertrain components, and welding of aluminum hang-on parts with no cracking, without using filler wire.
This precise control over spatial power distribution is achieved through the unique output beam of the ARM laser, which consists of a central spot, surrounded by another concentric ring of laser light. The power in the center and the ring can be independently adjusted and modulated on demand, and this enables very careful control over the melt pool dynamics.
Coherent HighLight ARM lasers are available with various center-to-ring ratios and power levels which can be tailored to specific applications. The diameter of the center can be configured to be from 22 µm to 100 µm, and the ring outer diameter can vary from 140 µm to 200 µm.
For copper welding, a high intensity, high power center beam is needed. This provides the energy required to readily melt the material, despite its relatively low absorption coefficient, while the ring beam helps stabilize the keyhole. The result is that the welding process is initiated and maintained consistently, regardless of surface variations in the work piece, thus overcoming the limitations experienced with traditional fiber lasers.
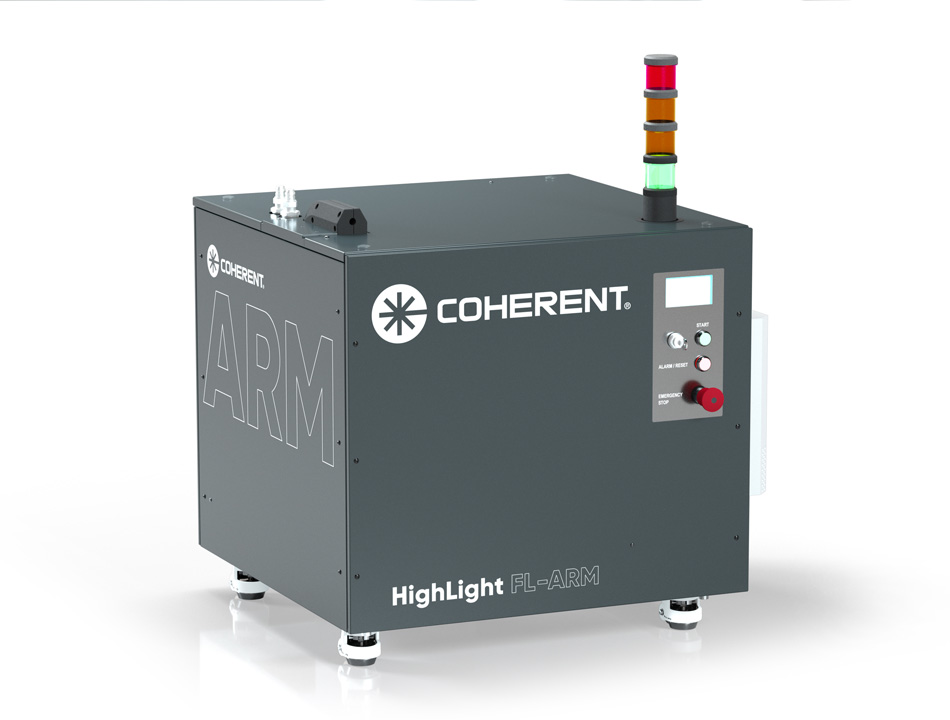
Figure 1: HighLight FL4000CSM-ARM fiber laser.
"For copper welding, a high intensity, high power center beam is needed."
Copper welding results
A series of copper welding tests were performed by Coherent applications engineers using an ARM laser having a high brightness center beam of 22 µm diameter, and a ring beam having an inner/outer diameter of 100 µm/170 µm. The laser was focused using a remote processing head with a magnification of 1.4, with nitrogen as shielding gas and cross jet. The material welded was pure copper. The laser power was 4 kW, with 1.5 kW in the center and 2.5 kW in the ring for all tests. The photo (Figure 2) shows the experimental setup.
Focus position was varied and it was determined that the best weld quality occurred with focus set 1.5 mm above the material surface. Specifically, this position was the best compromise between weld pentation and weld quality. The ARM laser produces deeper weld penetration if focused directly on the material surface, but the resultant weld surface quality and spatter are not sufficient for typical e mobility applications. The beam profile at the work surface using the optimum beam focus position (1.5 mm above the surface) is shown in the graphic.
"The infrared ARM laser delivers 2x the weld penetration"
The graph plots weld penetration on 2 mm thick copper as a function of speed under the conditions just described. A 2 kW green laser was also tested under the same conditions for comparison. Lower green power was used because a 4 kW infrared fiber laser only produces 2 kW of green output. The comparison shows that the infrared ARM laser delivers twice the weld penetration over a wide range of weld speeds.
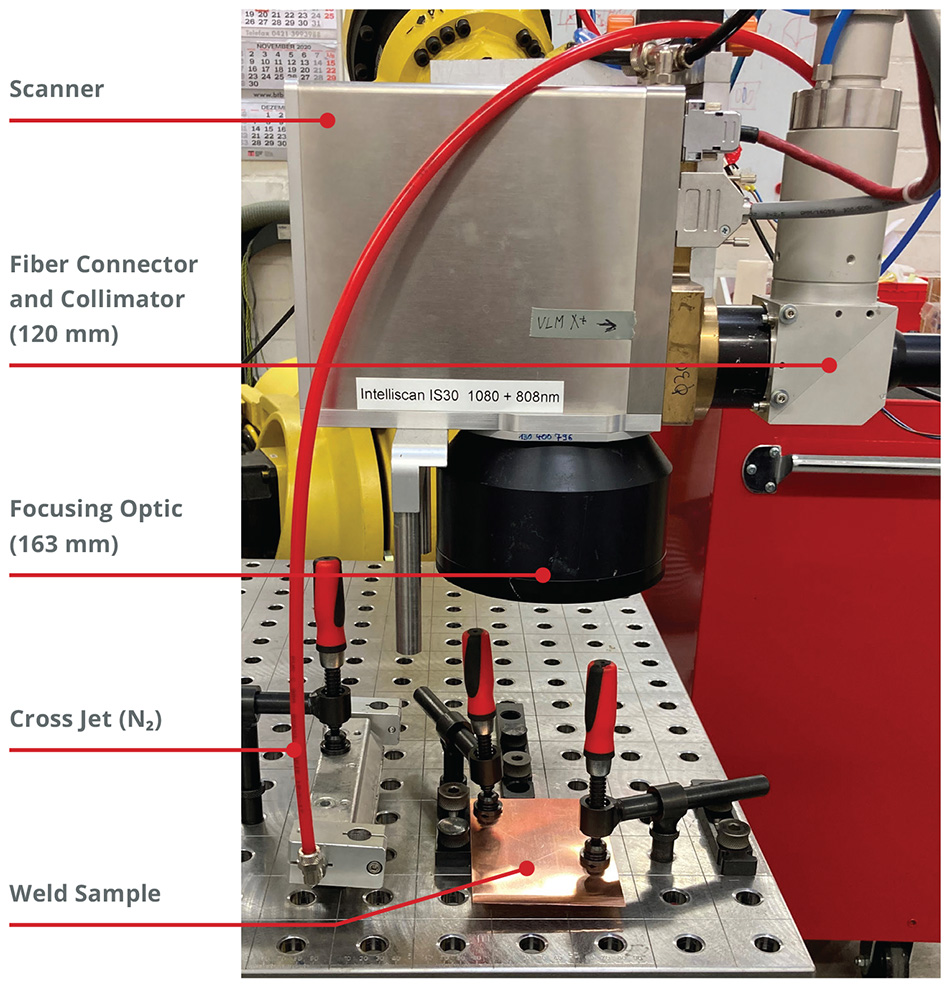
Figure 2: High brightness ARM fiber laser weld station with scanner and shielding nozzle.
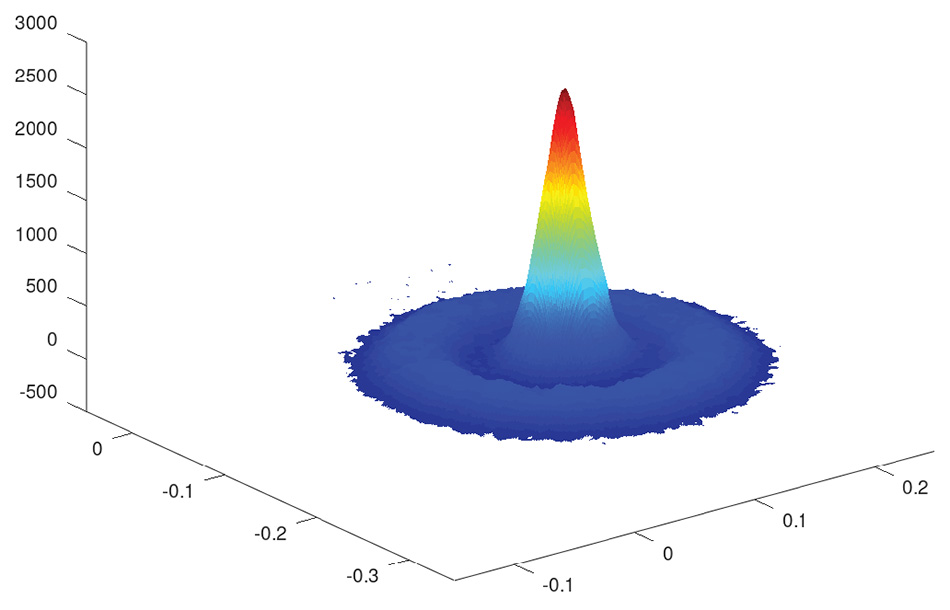
Figure 3: Beam profile of ARM at the work surface (1.5 kW center and 2.5 kW ring) with the laser focused 1.5 mm above the work surface.
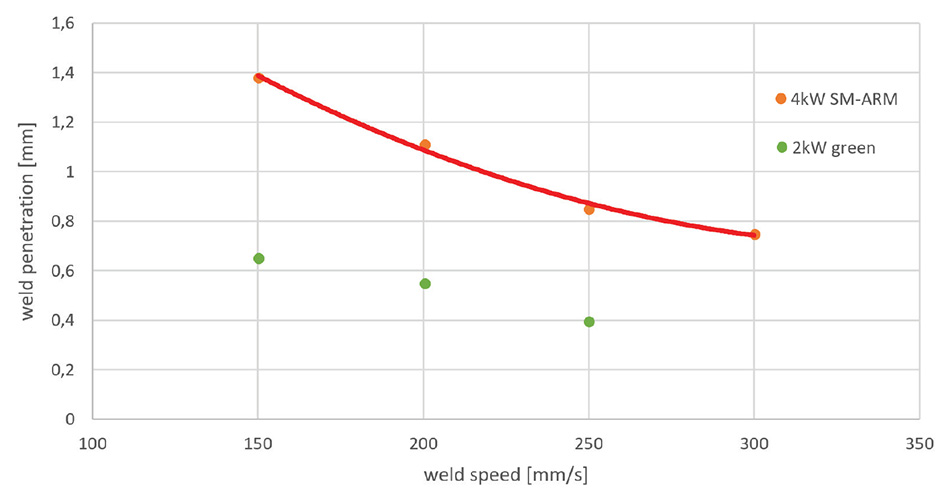
Figure 4: Weld penetration for a 4 kW, high brightness ARM as compared to a 2 kW green fiber laser.
Weld Efficiency
Weld efficiency of the ARM laser was also measured and compared with previously published weld results for a 2 kW green laser. Nitrogen was used as shielding gas for both welds. The published data for the green laser showed a (constant) weld cross section of 0.5 mm², and a penetration depth of about 1 mm. The ARM laser was configured to deliver these same results. Specifically, this required an output power of 3.5 kW and a weld speed of 300 mm/s, as compared a weld speed of 200 mm/s second for the 2 kW green laser. Normalizing these results gives a linear laser power of 10 J/mm for the ARM laser, compared to 11.8 J/mm for the green laser. Thus, the green laser offers slightly higher weld efficiency. However, the higher total power available from the ARM laser allows it to operate at much higher weld speeds, despite this small difference in efficiency.
Surface Quality
Another important consideration is the surface quality. Traditional fiber lasers are able to weld copper but are very sensitive to changes in the surface quality. The photograph shows weld beads for a high brightness ARM laser welding on sanded and polished copper. The process stays stable on both surfaces with no change in weld quality.
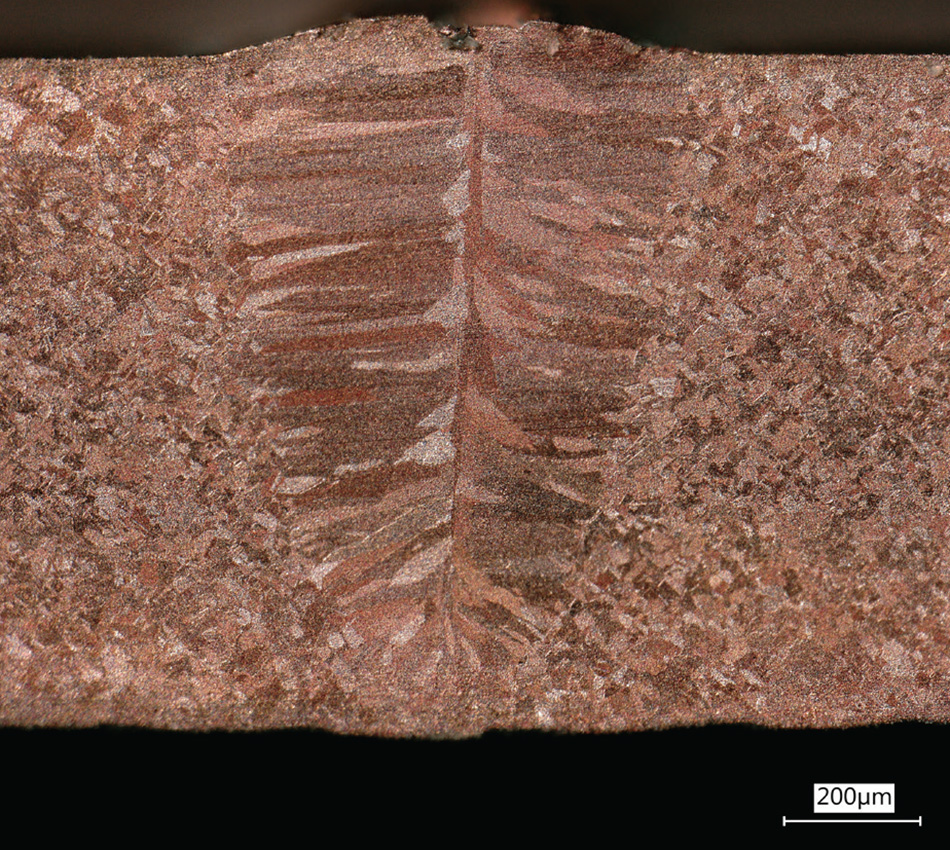
Figure 5: Cross-section of a copper weld produced by the high brightness, infrared ARM Laser, with an output power of 3.5 kW, at a welding speed of 300 mm/s.
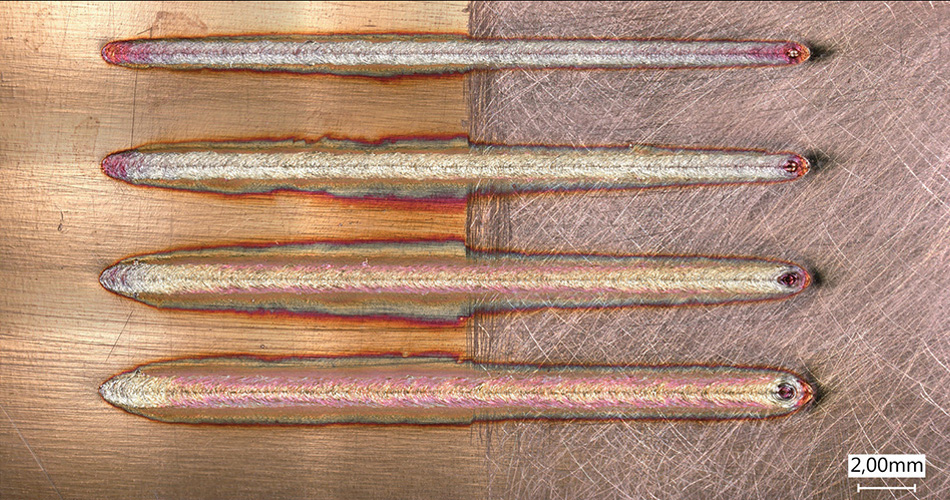
Figure 6: Figure 6: Consistent weld beads on smooth and sanded copper using the 4 kW ARM laser at various speeds (300-150 mm/s top to bottom)
Conclusion
These tests demonstrate that the unique, Coherent high brightness ARM laser is a practical solution for demanding copper welding applications in e-mobility. Weld penetration and process speed match or exceed current production requirements. And, the ARM laser avoids the sensitivity to surface quality and process instability problems that have limited the use of fiber lasers for copper in the past. Thus, this new ARM laser finally brings all the cost, reliability, and practical advantages that have made fiber lasers the choice for so many other industrial applications to the demanding task of copper welding
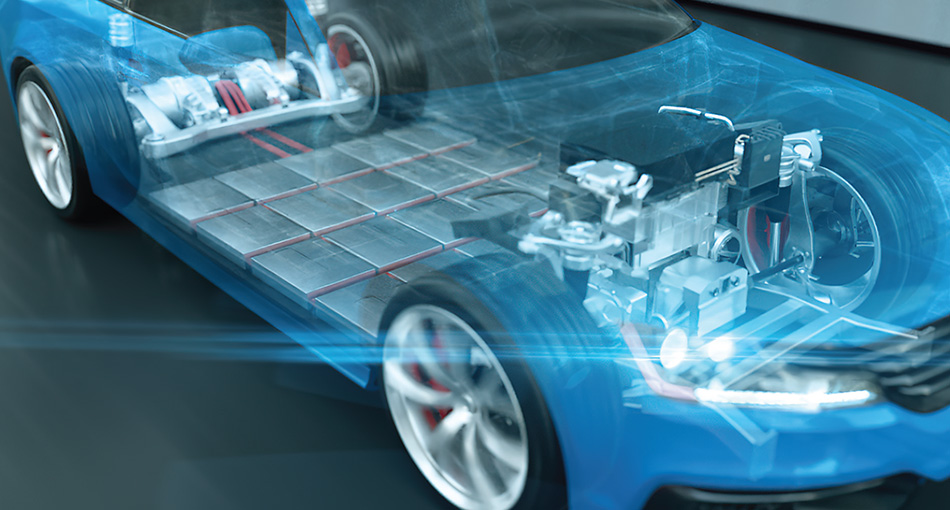