What is a Fiber Optic Gyroscope?
Fiber optic gyroscopes (FOGs) are highly precise and accurate rotation sensors. They are used in navigation and guidance systems in aircraft, spacecraft, ships, and other vehicles. They sense rotation by measuring the interference of laser light traveling within a coil of optical fiber.
Gyroscope Basics
A gyroscope is a device that can sense orientation and angular velocity. The basis for the simplest type of gyroscope is a spinning wheel held in a frame – familiar to many as a child’s toy. Angular momentum causes the wheel’s orientation to remain constant even as the frame around it rotates.
Gyroscopes became much more than toys with the development of flying vehicles – airplanes, and then rockets – in the 20th century. The reason for this is that flying vehicles have a navigational requirement that isn’t present in ground vehicles, or even ships. That is, they can freely rotate and move in all three dimensions. Pilots therefore need to continuously know vehicle orientation in three axes to control the aircraft.
Unmanned rockets and missiles have a further requirement. These craft need to know their orientation and position without a human pilot to monitor it. The solution to this is an inertial guidance system (IGS). The IGS uses gyroscopes to sense orientation and angular motion to continuously control the craft and calculate how far it has moved from its starting point.
Advantages of Fiber Optic Gyroscopes
The first gyroscopes were mechanical – a motor-driven spinning rotor and various sensors to read the angular velocity and orientation information and supply that to the human pilot or IGS. These mechanical gyros were relatively large and heavy. Their performance could be affected by vibration, and they required frequent calibration.
Interferometric fiber optic gyroscopes (IFOGs) were developed to overcome the limitations of mechanical gyroscopes. They use a coil of optical fiber, coherent light source, and photodetector to sense rotation, rather than a mechanical rotor. This yields smaller, lighter, and more accurate systems.
Inside the IFOG, the light source is split into two beams before entering the fiber coil. The two beams are coupled into the opposite ends of the fiber, so that one travels in the clockwise direction and the other travels in the counterclockwise direction.
If the coil is rotating in its axis, then the two beams will undergo a phase shift relative to each other. This is called the Sagnac effect. When the two beams exit the fiber, they are recombined. Any phase shift will produce interference fringes (a pattern of light and dark) in the combined beam. This pattern is sensed by the detector to determine the angular velocity of the rotation. Typically, three coils, each mounted at right angles to the other two, are used to sense rotation in all three axes simultaneously.
IFOG Construction
IFOG coils are typically made by winding a highly birefringent, polarization-maintaining optical fiber around a central axis, and then encapsulating the coil in a protective material. There are two main different types of encapsulation methods: wet and dry. Wet IFOG coils use a liquid, such as oil or water, to protect and support the optical fiber, while dry IFOG coils use a solid, such as a ceramic or glass, to protect and support the optical fiber.
Wet IFOG coils offer better temperature stability and can be used in a wider range of environments. But they are more complex and difficult to manufacture. Dry IFOG coils are simpler and easier to manufacture, but they are more sensitive to temperature changes.
The IFOG light source is typically a low-power, continuous-wave laser, superluminescent diode, or amplified spontaneous emission source. The detector is usually a photodiode or a photomultiplier tube.
There are almost limitless possible IFOG configurations – especially options for how the coil is wound and how it is packaged. Other variables are the total length of the fiber in the coil, various optical coatings, and features like radiation resistance (especially for spaceborne applications).
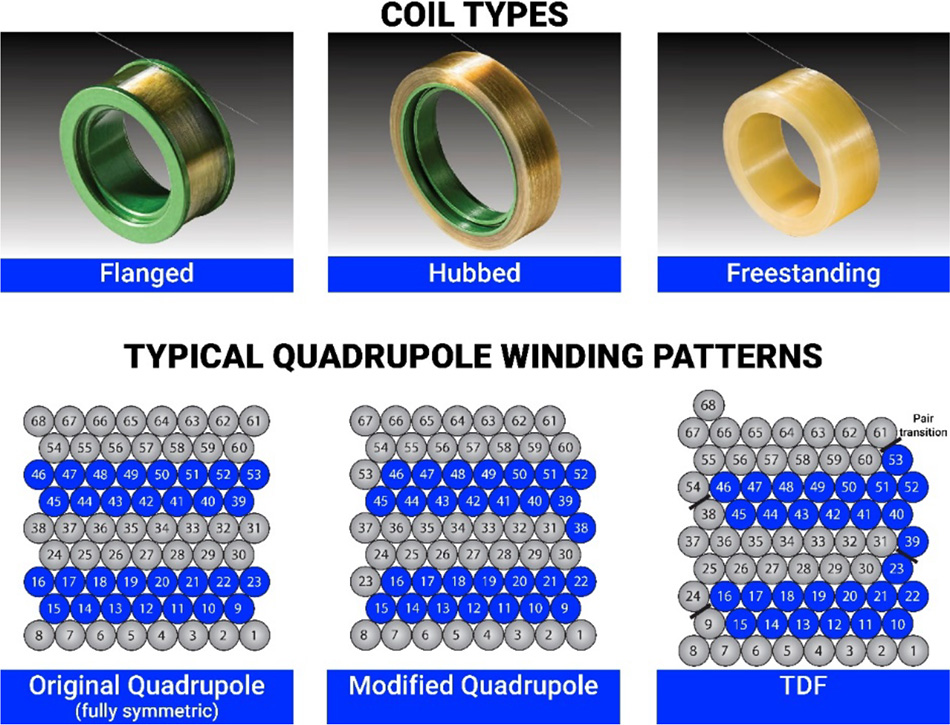
Figure 1. Commercial IFOG coils are available in a wide variety of configurations, with numerous options.
But all these different design forms have fairly similar requirements in terms of the fiber optic coil at the center of the system. In particular, there are certain parameters that are critical to proper IFOG performance. The most important ones are insertion loss, the polarization extinction ratio (PER), and wavelength dependent losses. Winding precision and encapsulation quality are also important.
Achieving good performance in these areas requires the ability to tightly control manufacturing of the fiber itself, and then the process of winding it into coil format. In particular, it’s essential that the fiber coil be wound in a manner that is perfectly symmetrical (so that the beams traveling in opposite directions experience identical conditions). Also, it’s important to minimize mechanical stress in the wound fiber.
There’s quite a bit of expertise and process experience required to perform these tasks repeatably. Coherent maintains a completely vertically integrated IFOG coil fabrication capability – from drawing the fiber optic cable through winding it into coils – in order to ensure the level of process control necessary to consistently produce high-performance IFOG coils.
There is no one “best” type of IFOG. The required performance level, the operating environment, and the acceptable size, weight, and power consumption must all be traded off against cost in any specific application.
IFOGs at work
IFOGs deliver several significant advantages over traditional gyroscopes, and even other non-mechanical technologies. For one, IFOGs are highly sensitive and can detect very small rotational movements – angular velocities at a resolution of a few nanoradians per second. This is several orders of magnitude better than mechanical gyroscopes. So, they deliver higher accuracy navigation and guidance.
In addition, IFOGs are relatively immune to vibration and electromagnetic interference, and having a long lifespan and low maintenance requirements. This makes them useful in a variety of “harsh” environments, or where access to the equipment is limited. This includes spaceborne applications, and in inertial measurement systems for seaborne and underwater vehicles and equipment.
IFOGs are also often used to stabilize stationary structures because of their high sensitivity and accuracy. For example, IFOGs can measure the rotational movement of a structure, such as a bridge, building, or antenna platform, and to feed the data back to a control system that compensates for any movement. This can help to maintain the stability of the structure, especially in high wind or seismic conditions.
In summary, IFOGs are a highly precise and accurate type of rotation sensor that have a wide range of applications. They are immune to electromagnetic interference, relatively immune to vibration, have a long lifespan and low maintenance requirements, and relatively small and lightweight. This makes them ideal for use in navigation, guidance, and control systems for aircraft, ships, and ground vehicles. Plus, they are useful in industrial automation and robotics.