CO2 LASERS AT 60 – STILL ALIVE & KICKING
Ongoing innovations in performance, reliability, and value keep one of the oldest laser technologies relevant.
January 20, 2025 by Coherent
Did you know that Coherent was the pioneer for CO₂ lasers, introducing our first commercial product in 1966? That’s only two years after they were first invented at Bell Labs. Over the next few decades, CO₂ lasers quickly established themselves as the most popular source for welding, cutting, marking and engraving applications across industries as diverse as automotive production, semiconductor and electrical and electronics manufacturing.
CO₂ lasers are sometimes thought to be a legacy technology. In fact, CO₂ lasers – now entering their seventh decade – are not headed for retirement at all. Instead, they are even more widely used in both existing and developing applications.
While the pre-eminence of Kilowatt CO₂ lasers decreased for metal processing after fiber lasers gained commercial traction around 2010, many applications for non-metals materials continue to rely on both low and high-power CO2 lasers.
WHERE DO CO2 LASERS SHINE?
Part of what keeps CO₂ lasers in the picture is basic physics. CO₂ lasers output a wavelength around 10 µm, which many different materials absorb very well – including plastics, organics like wood, cardboard and leather, natural and synthetic textiles, rubber, composites, glass ceramics. Conversely, almost all these materials do not absorb well the 1 µm wavelength light from fiber lasers.
In addition to these materials water strongly absorb CO₂ laser light making these lasers especially useful for surgical applications, as most tissue – even bone – contains a significant amount of water.
What doesn’t absorb 10 µm laser light well? The answer: conductive metals. That’s why Coherent produces high-performance laser mirrors and other reflective optics out of metal substrates such as copper and aluminum.
BETTER CO2 LASER TECHNOLOGY
Another reason that CO₂ lasers have stayed relevant is ongoing improvements in the technology. These make the CO₂ lasers of today far more efficient, reliable, and economical than their predecessors.
Early generations of multi-kW CO₂ lasers utilized a fast flow of gas either through or across the laser cavity that was simply a scaling up of the earlier lower power “slow flow” lasers. But this approach carries a high price tag in terms of operating cost, system size, efficiency, and reliability.
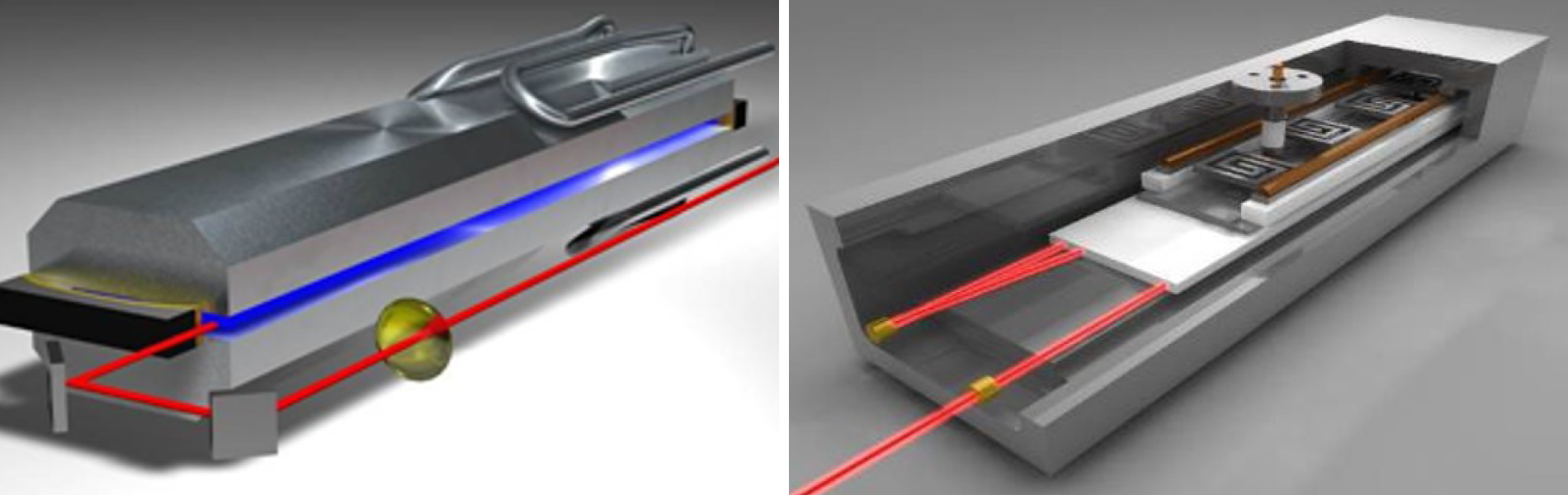
Figure 1. Slab laser design on the left, excellent for power scaling, and waveguide on the right, for lower powers; both laser resonator designs provide excellent mode quality and power stability.
The development of diffusion cooled (DC), slab CO₂ lasers like the high-power (1-8kW) Coherent DC and medium power (120-1000W) Coherent DIAMOND J-Series revolutionized the technology. In this design, the laser gas is confined between two large flat electrodes which are water cooled, enabling much more effective heat removal. This simplified design significantly reduced gas usage, increased wall-plug efficiency and increased reliability. To this day no other company produces multi kW CO2 lasers using this technology.
The bottom-line benefits of these slab lasers over traditional fast flow CO₂ lasers are more compact size, negligible gas consumption, and higher output beam quality. Slab lasers can be completely sealed at power levels of 1 kW or less and “semi-sealed” for multi-kW operation. This yields a smaller sized laser head and eliminates the need for large external gas storage cylinders. Together, this substantially simplifies integration and vastly reduces operational and maintenance costs.
Low power CO₂ lasers below 120 W like the Coherent DIAMOND C/Cx Series use the sealed waveguide construction that has been in use for many decades. But ongoing incremental improvements in every aspect of the design and operation of these lasers continue to deliver gains. That’s why DIAMOND C/Cx lasers today offer better reliability, performance, stability, and operational lifetime than ever before.
The functionality of our DIAMOND C/Cx Series CO₂ lasers has been extended by directly integrating modulators and even intra-cavity q-switching. This enables these lasers to service more demanding, higher precision applications, particularly in flat panel display and microelectronics manufacturing applications.
A RAINBOW OF APPLICATIONS FOR CO2 LASERS
The range of applications for CO₂ lasers is so broad and extensive that it’s not practical to list them all here. Following is an overview of some of their key applications segmented by industry:
Automotive & General Industrial
- Airbag Cutting: CO₂ lasers can cut the tough, tightly woven materials used in airbags with precision and speed. This ensures clean edges and maintains the material’s integrity, which is critical for the safety and reliability of the airbag system. The cutting process seals the cut edge such that no fraying of the airbag material occurs.
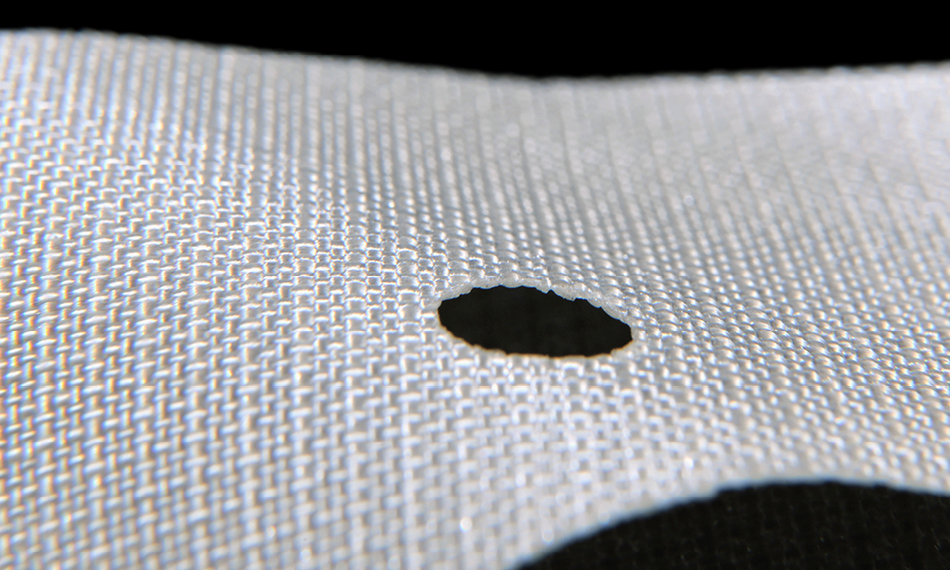
Figure 2: Airbag cutting is an excellent application for lasers that easily cut through the mechanically tough fabric and seal the cut edge so there is no fraying
- Dashboard Scoring: Strategic weaking /scoring of dashboards and airbag covers enables freedom in the design of car interior while ensuring the airbag’s functionality.
- Polymer Part Cutting: For sensors, fog lights, or other components, also the minor customization of volume production parts such as bumpers for different automotive models/options. Here the laser enables operational flexibility (hole patterns can easily be defined or changed) and produces cut edges that are smooth and free of defects.
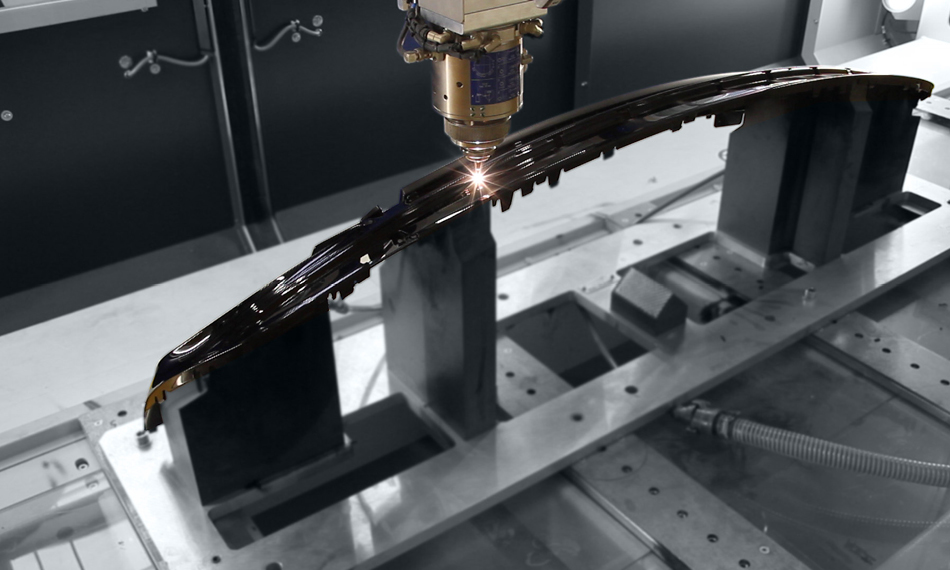
Figure 3: A CO2 lasers cuts a custom configuration into an injection molded bumper blank.
- Busbar stripping: CO₂ lasers can rapidly and efficiently remove insulation from busbars prior to welding. The lasers are often used in pairs to strip both sides of a busbar simultaneously.
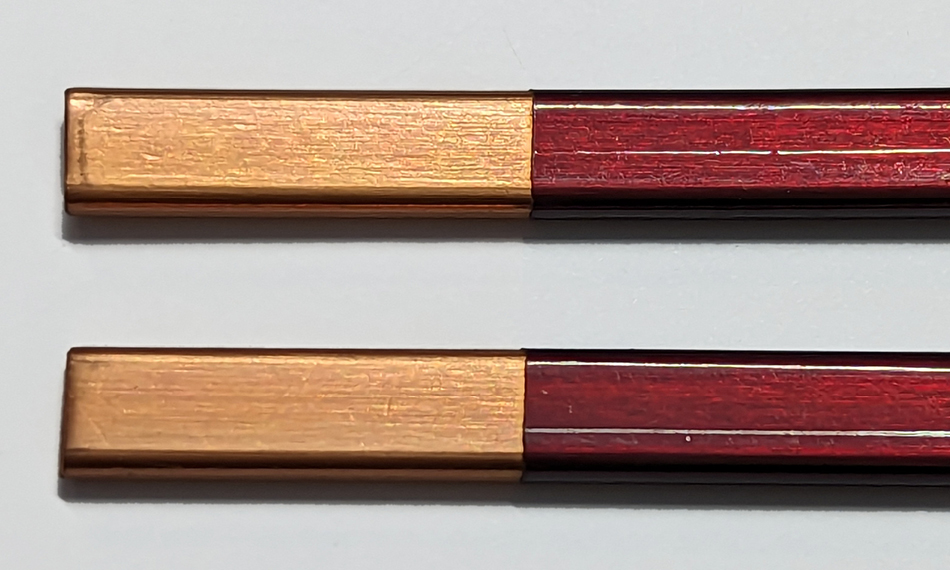
Figure 4: Removing insulation works well as the CO2 laser is absorbed by the insulating material but reflected by the underlying copper.
- Tube and profile welding: CO₂ lasers are utilized extensively for continuous welding seams on tubes to seal them up. This is one form of “profile welding,” a process commonly employed to create strong, seamless joints that follow the contour of the parts being joined.
Semiconductors & Electronics
- Cutting and drilling: CO₂ lasers are used for cutting (depaneling) and drilling holes (called “vias”) in printed circuit boards. They can also drill low temperature co-fired ceramics (LTCC). This material is used as a microelectronics substrate especially in the construction of thin, multi-layered devices, such as flash RAM.
- Laser Spike Annealing: High Power CO2 lasers enable wafer annealing, which is a step in the front end of line of (FEOL) in the IC fabrication
- Flat Panel Displays: Modulated and q-switched CO₂ lasers, provide minimal heat affected zone and excellent edge quality needed for cell and polarizer cutting in FPD production.
- Wire stripping: The precise material removal possible with a laser makes them especially useful for stripping insulation from small gauge wires.
Packaging
- Converting: This is the process of transforming paper, plastic, cardboard, foil, or film into finished packaging products. CO₂ lasers are used for numerous cutting tasks in converting because of their speed, flexibility, and reliability. Processing can be optimized by choosing a CO₂ laser with an output wavelength that closely matches the material absorption characteristics; Coherent offers CO₂ lasers with output at 9.3 µm, 10.2 µm, and 10.6 µm for this purpose.
- Cardboard/Cartboard: Increasing demand for cardboard packaging is driving more efficient and flexibility in box manufacturing, High power CO₂ laser provide a fast, efficient and flexible technology to mass produce boxes. This technology provides the capability for “box on demand” such that the precise size of box is created for the item to be shipped.
- Flexibles Slitting/perforating: CO₂ lasers can readily produce perforations in thin films and foils and are used extensively in the production of “easy open” packaging. They are also ideal for modified atmosphere packaging (MAP) – these are the arrays of small holes (micro perforations) made in plastic bags for prepackaged salads and other produce. They allow air circulation and extend product freshness.
- Dieboard cutting: High-volume converting applications often use dieboards to cut precise shapes or patterns into packaging materials. These are flat boards, typically made of plywood or composite material, into which metal cutting dies are embedded. CO₂ lasers are widely used for cutting slots in dieboards due to their precision and ability to create intricate, clean cuts with almost no taper.
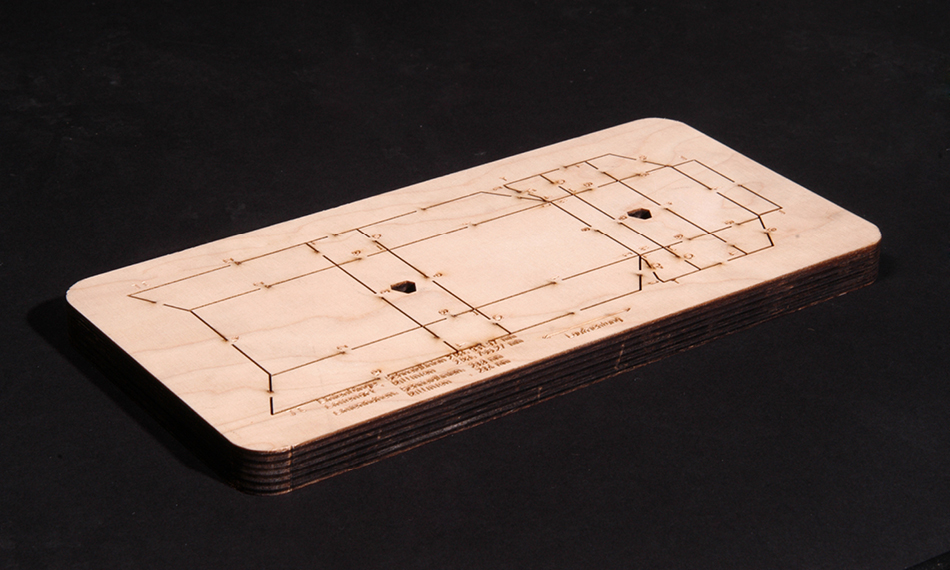
Figure 5: Cutting precise and parallel slots into thick dieboard.
- Digital Die Cutting: Directly cutting corrugated boards with high power CO2 lasers allows high flexibility enabling small series production for point-of-sale displays and creative packing solutions.
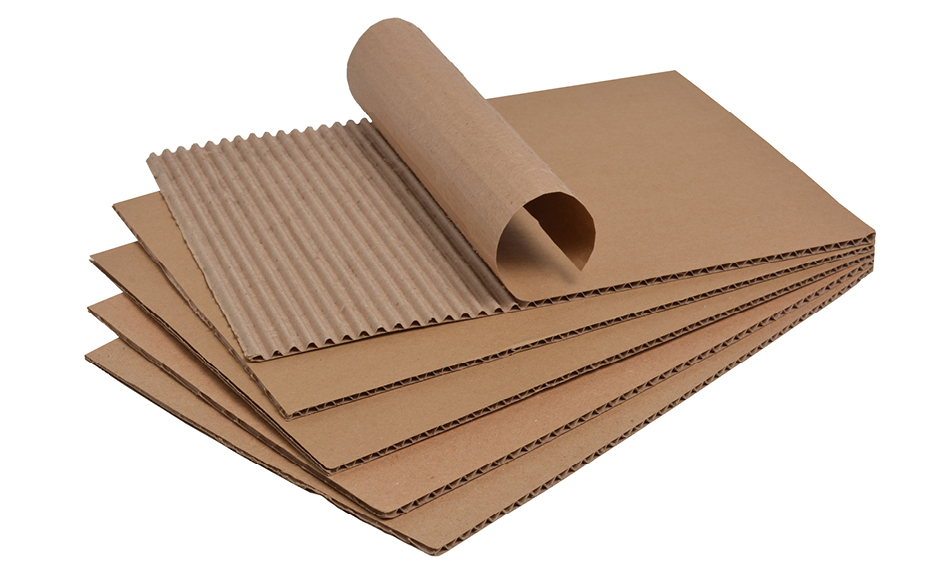
Figure 6: Direct cutting of cardboard provides flexible digital die cutting without the need for dieboard.
- Kiss cutting: The laser cuts through the top layer of a two-ply material without cutting through the bottom layer. This technique is commonly used in the production of labels, decals, and stickers, allowing the adhesive product to be easily peeled off the backing for application. CO₂ laser kiss cutting ensures precision and consistency, making it ideal for mass production of custom-shaped adhesive products.
- Marking: Many materials used in packaging, including polymers and ceramics, are efficiently marked with CO₂ lasers.
Textiles
- Cutting: Laser cutting of fabrics, leather and sailcloth offers high speed and precision.
- Fading / distressing: Lasers provide a fast, controllable and environmentally friendly method to mark jeans in a way that mimics the appearance of age. They can also be used to reproduce graphics and patterns on jeans and other fabrics.
Medical
- Surgery: The strong absorption of the CO₂ wavelength by water makes these lasers efficient surgical tools. They are especially used in dentistry and oral surgery to cut bone and tooth enamel, as well as soft tissue.
- Dermatology: CO₂ lasers enable precise removal of thin layers of skin without significantly affecting surrounding tissue. They are used to treat wrinkles, warts, birthmarks, and other skin conditions.
This is just a sampling of the applications serviced by CO₂ lasers today. Because they are the only practical source of long-wave infrared light, and since many materials absorb that light well, CO₂ lasers will remain a relevant tool for many years to come. So, after 60 years of service, CO₂ lasers are still far from retirement. Learn more about Coherent high-power and lower-power CO₂ lasers.