CUSTOMER SUCCESS STORY
Lasers Make the Cut in Wineglass Manufacturing
The Challenge
Many manufacturers produce goblet shaped wineglasses by placing a droplet of molten glass into a form that has the desired final shape of the bowl; air is then blown into the droplet to expand it until it fills the form. The glass cools in the desired hollow bowl shape, but still has a “cap” (the so-called moil) of material at the top. This cap is cut off in the final stage of glass production. But, traditional glass cutting methods don’t produce the desired smooth edge. This is critical, since this is where the drinker’s lips actually touch the glass. So, various post-cutting grinding, polishing and cleaning steps may have to be employed to smooth the rim of the glass. All these steps have cost, repeatability and yield impacts.
The Solution
“Filamentation” is a glass cutting method that exploits the very high-power densities that can be achieved with focused, ultrashort pulse (USP) lasers of even modest overall power. The tradename for the patented version of this energy-efficient process from Coherent is SmartCleave. It enables high-speed cutting of straight lines, curves, and insets, without taper, into transparent and brittle materials from 50 µm to 10 mm in thickness. Most importantly, SmartCleave delivers smooth surfaces, with a roughness (Ra) of less than 1 µm and with edge chip sizes less than 5 µm. SmartCleave cutting also yields a final bend strength that is measurably superior to mechanical processes.
The Result
IPROTec (Innovative Process Technology) GmbH, located in Zwiesel, Germany, builds automated equipment for drinking glass production. IPROTec designed and now supplies a fully automated system which implements SmartCleave cutting for glass cap removal. It utilizes a Coherent PowerLine SmartCleave sub-system, which incorporates a single HyperRapid NX laser having 50 W of average output power at a wavelength of 1064 nm. The sub-system also includes several optical components, beam switches, sensors, and electronics. Depending upon how the machine is configured and used, it can reach cutting speeds of 300 mm/s, enabling processing of up to 50 glasses per minute. Most importantly, the IPROTec system eliminates all the grinding, washing, and drying steps required with earlier glass cutting methods, along with their energy consumption, time, cost, and negative environmental impact. And, the system has already proven itself in actual use to deliver the 24/7 reliability required by high-volume drinking glass manufacturers.
“A major reason we selected Coherent as our supplier was that they were ready and able to partner with us in the development of the process and technology."
— Tobias Bredl, Sales and Project Manager IPROTec, GmbH
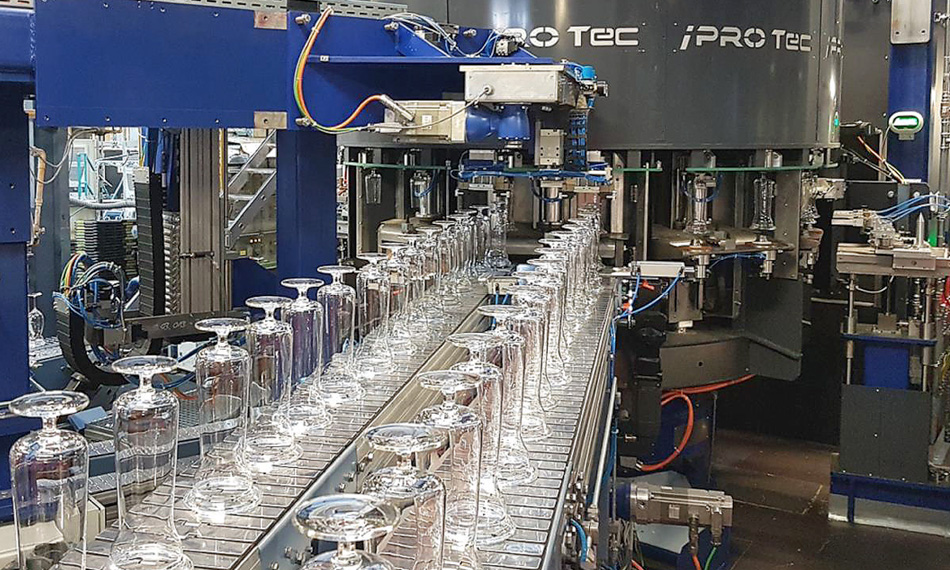