Faster Copper Welding for EV Production
A new Coherent HIGHmotion 2D remote welding head and Coherent HighLight FL-ARM laser both enable deep penetration copper welding over large working areas.
September 12, 2023 by Coherent
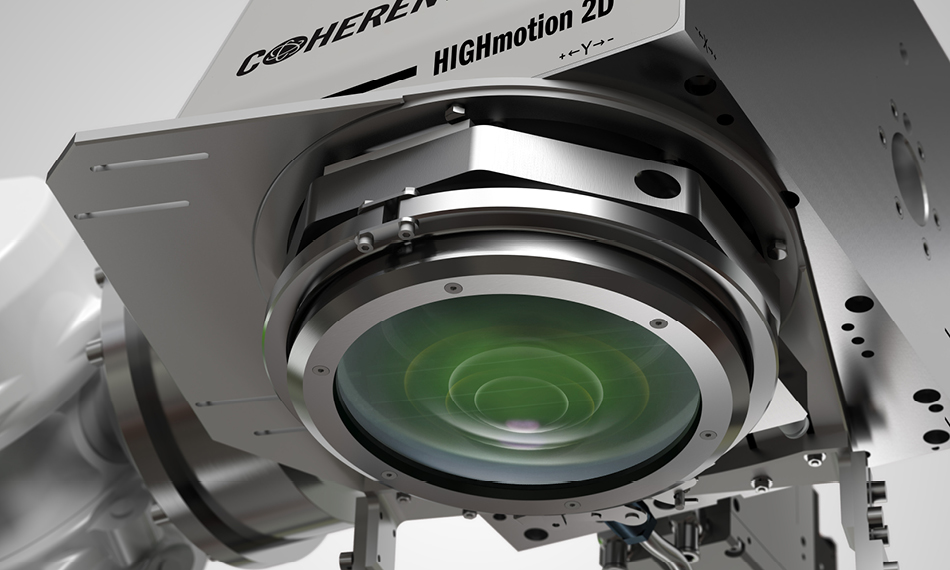
HIGH-motion 2D processing heads combine superior optical performance and exceptional operational reliability to enable cost-effective production welding.
Two new product introductions from Coherent enable deep copper welding (>3 mm) over a large scan field (100 mm x 140 mm). This allows high-speed processing of large parts – such as busbars – because the system can complete several welding tasks at widely separated locations without physically moving the process head or component.
The first of these new products is the extension of our existing Coherent HIGHmotion 2D remote welding head to include lower magnification options. When used with a low numerical aperture (NA) fiber laser, a lower magnification HIGHmotion 2D head will deliver a small, high brightness, focused laser spot over a bigger scan area with minimal focal shift. High brightness is critical to performing deep welding on copper, which is otherwise challenging to accomplish with an infrared laser. This approach provides a larger process window, meaning a more stable, robust, and repeatable process.
The new lower magnification HIGHmotion 2D maintains all the capabilities of this industry-proven laser welding scanner, including positioning precision, high power stability, and compatibility with both Coherent HIGHvision and SmartSense+.
The second product introduction is a lower numerical aperture (NA) version of our ARM FL fiber laser. This supplies precisely the required low NA input beam for optimum performance from the low magnification HIGHmotion 2D. Plus, it adds the ARM laser’s ability to separately control and modulate the power in the center and ring beams. This capability has proven valuable for eliminating spatter when welding copper. The HighLight FL-ARM also offers superior immunity to back reflections for greater operational reliability.
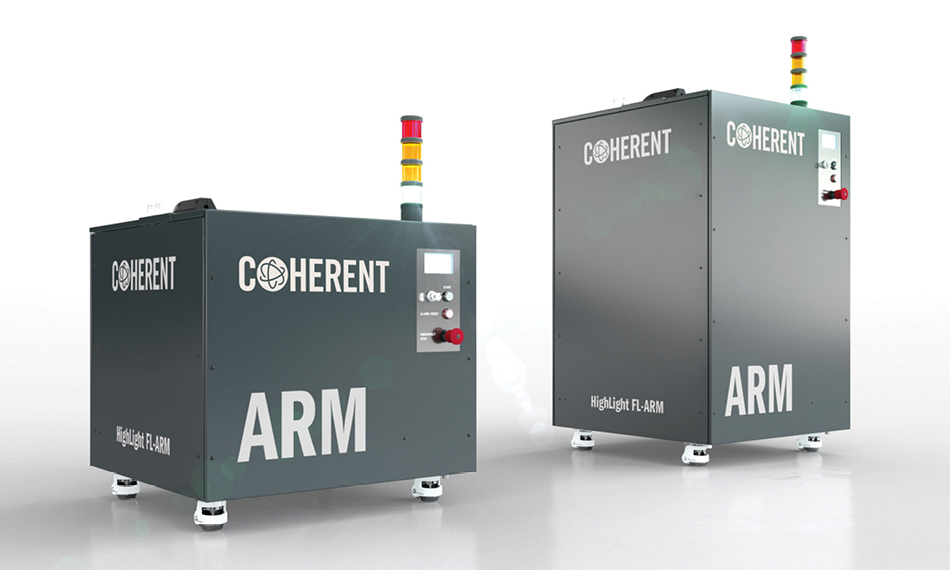
The Coherent HighLight™ FL-ARM series multi-kilowatt fiber lasers deliver superior results in a variety of challenging welding tasks.
Increased Throughput for Deep Penetration Welding
The HighLight FL-ARM laser has already had tremendous success in copper welding, in particular. As manufacturers push to scale up this success to produce the deep welds required for e-mobility tasks like busbar welding, they run into a “speed limit.”
One cause of this speed limit is the limited size of the F-theta lens scan field. This is the area over which the laser can produce welds without moving anything (other than the scan mirrors themselves). Moving the part or the welding head takes time, so the smaller the scan field, the more part motion required, and the slower the overall process throughput.
What prevents making the scan field larger? The problem is that increasing the field size of an Ftheta scan lens means increasing its focal length, which also makes the focused spot size larger (assuming everything else stays the same). But a small, high-brightness spot is essential to achieving the material penetration required for deeper welds. At some point, the spot gets too large to deliver the required brightness. This is illustrated in the animation.
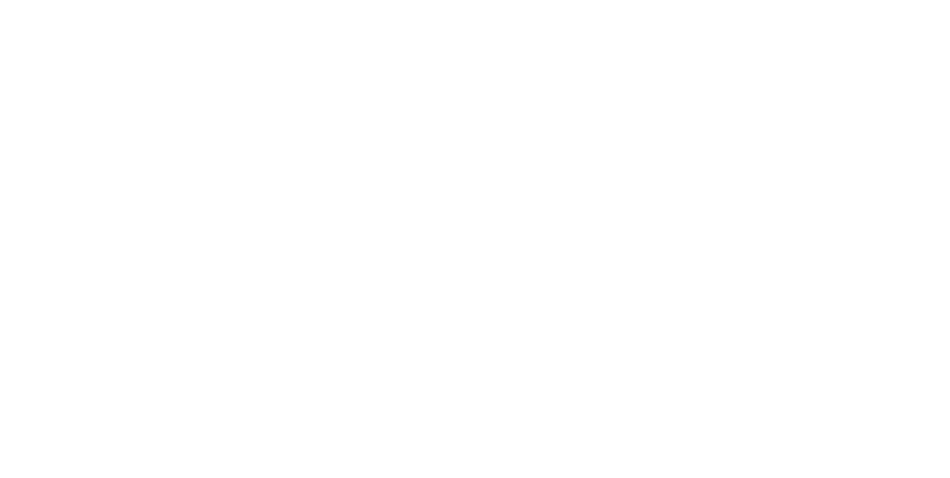
The spot size can be reduced back down by increasing the focal length of the input collimator; this is the lens system that gathers the diverging light from the laser and prepares it to go through the scan optics. Doing this lowers the magnification of the overall system.
The problem is that increasing the collimator focal means moving the laser source farther away from it. And, at some point, the diverging laser beam becomes too physically large in diameter to pass through the collimator and scan optics without being partially cut off. This is undesirable because throwing out any laser light lowers the focused spot brightness, putting us right back in the same hole.
The solution here is to reduce the divergence of the laser source to begin with. Or in optics terms, to lower its numerical aperture (NA) which is a measure of the beam divergence angle. This allows the use of a longer focal collimator without any light loss, which in turn permits the use of a longer focal length (a wider field-of-view) F-theta scan lens. This combination delivers a small focused spot (high brightness) over a large scan field. Problem solved.
Except, substantially lowering the NA of a fiber laser – without reducing its power or causing any other degradation in its output – isn’t so easy to do. Which is why Coherent is the first, and currently only, company that’s been able to accomplish it. And that’s why the new lower magnification HIGHmotion 2D process head, especially when paired with the new low NA HighLight FL-ARM laser, makes deep penetration copper welding go faster.
Learn more about the Coherent HIGHmotion 2D and Coherent ARM FL.