Lasers Put a Stop to Vehicle Pollution
A novel laser cladding method can substantially reduce fine particulate generation from disc brakes by creating a protective metal layer.
April 25, 2022 by Coherent
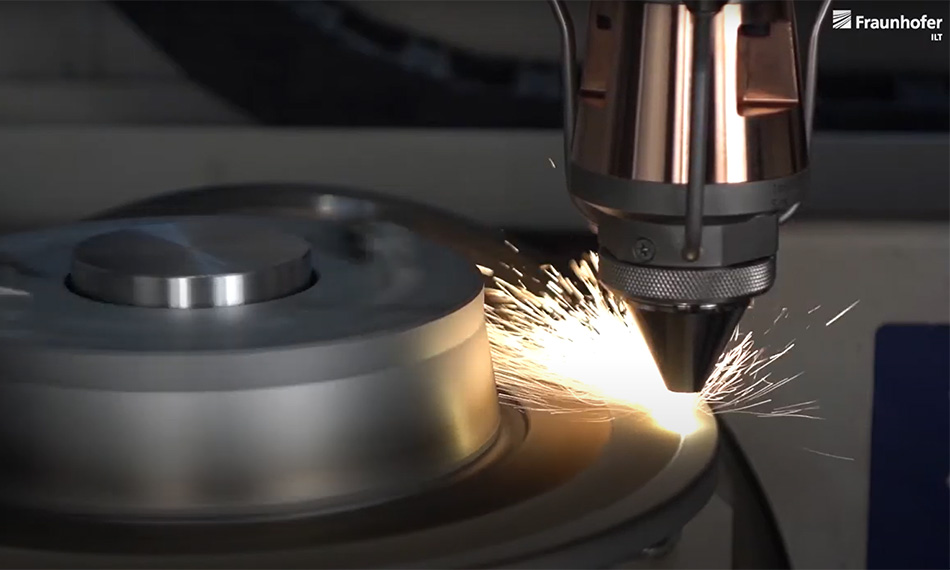
Did you know that 21% of the small particulate emissions from vehicles come from the brakes rather than the tailpipe? That’s because every time disc brakes are used a bit of material wears off the brake rotor and pad. Particles of this worn-off material that are less than 10 µm diameter (called PM10) can become airborne. But, unlike tailpipe emissions, there’s been no simple way to measure these emissions, and more importantly, no means to control them.
Braking up is hard to do
Most disc brake rotors are made from grey cast iron. This material can handle the high temperatures which brake components often reach, and it’s relatively inexpensive. But, grey cast iron wears easily, producing the particulates already mentioned. Plus, it corrodes.
An obvious solution is to put a thin coating of a harder material – like stainless steel – on the surface of the brake rotor to protect it from both wear and corrosion. But, none of the techniques usually used for making coatings like this are useful with disc brakes. For example, the coatings produced by electroplating and thermal spraying don’t metallurgically bond with the grey cast iron. That means that they can chip or flake off. Plus, these methods are expensive to implement.
Even traditional laser cladding (also called laser material deposition or LMD) doesn’t hold the answer. In this technique, powdered stainless steel is deposited on the surface of the part, and a high-power diode laser or fiber laser is used to melt both this powder and the part. This resolidifies to form a new coating layer having a strong metallurgical bond with the base material.
But the laser also melts enough of the grey cast iron that some of the carbon from it can migrate into the steel coating. This will make the coating brittle, or produce cracks or other defects in it that could shorten the life of the part.
Novel laser cladding technology brakes the cycle
A group of engineers at Fraunhofer Institute for Laser Technology ILT and RWTH Aachen University (both in Aachen, Germany) have developed a new laser material deposition process that offers the solution. Their method, called Extreme High-speed Laser Material Deposition (or its German acronym EHLA), introduces some key innovations into laser cladding.
Like traditional LMD, EHLA sprays powdered metal at the surface of the disc brake, and melts both with a high-power diode laser (HighLight DL series). But, EHLA uses a custom-designed nozzle that allows the cladding powder to be melted “on-the-fly" in the laser beam before reaching the part surface. So, liquid droplets land on the part in a very thin layer of melted grey cast iron. All this metal then rapidly resolidifies to form a thin coating.
EHLA doesn’t heat up enough of the brake rotor for a significant amount of carbon from it to migrate into the coating. So, it avoids all the possible problems with changes to the material itself. But it creates a strong, thin layer that is metallurgically bonded to the part. And, it’s much faster and more efficient in terms of powder usage than traditional cladding. All this makes it a viable commercial process for automotive manufacturers.
EHLA is the recipe for success
EHLA is a flexible method that can be tailored to meet the exact requirements of the application. For example, when coating brakes intended for gas-powered vehicles, it can be useful to deposit two different layers. The top layer combines steel with tungsten carbide, titanium carbide, or some other very hard material. The EHLA cladding nozzle has been specifically designed to allow more than one powdered material to be used at a time.
When creating this layer, the laser power is set so that the harder material doesn’t melt. Rather, the small powdered particles simply become embedded in the solid steel layer like blueberries in a muffin. This produces an extremely wear-resistant outer layer.
But this outer layer is brittle and therefore prone to cracking which can subsequently allow in moisture that corrodes the brake. So, an underlying layer of just pure stainless steel is put on first to “seal” the brake rotor and prevent moisture from reaching it.
Braking patterns in electric vehicles (EVs) are very different than for gas-powered autos. In particular, the use of regenerative braking slows the car without much need to use brakes, resulting in less wear. In fact, EVs create so much less wear that corrosion of the brake is a bigger consideration than particle generation (because the frequent braking in a gas vehicle wears any corrosion off the surface of the rotor).
In this case, a different recipe can be used for coating EV disc brakes. Namely, a single, pure stainless steel layer is sufficient to protect them from corrosion, and still provides an adequate level of particle reduction.
EHLA is faster and utilizes metal powder more efficiently than traditional laser cladding, meaning it’s more cost-effective. Plus, it’s useful with many other materials besides just grey cast iron and stainless steel. Don’t be surprised if this technology soon breaks out into other areas of manufacturing.
Discover how homogeneously a metal coating can be applied with the EHLA process – for example on a brake disc.
Related Resources