What are Fiber Sensors?
Fiber sensors are used to detect changes in physical, chemical, or biological parameters. Their unique combination of advantageous features has led to their use in fields as diverse as structural monitoring, oil and gas exploration, environmental monitoring, and medical diagnostics.
A fiber sensor is a device that measures physical, chemical, or biological parameters by detecting changes in the light transmitted through an optical fiber. Fiber sensors offer several advantages over other sensing technologies, including:
Long distance operation |
Fiber sensors can transmit signals over long distances without significant signal degradation or loss. This allows their use at remote locations or for monitoring very large structures. |
Compact and lightweight |
Fiber sensors are small and lightweight, making them easy to install and integrate into a wide range of systems. |
Low power consumption |
Fiber sensors require very little power to operate, making them ideal for remote and portable applications where power is limited. |
|
Multiple fiber sensors can be multiplexed on a single fiber, allowing for several different parameters to be measured simultaneously. |
High speed |
Fiber sensors can provide high bandwidth and fast response times, making them suitable for dynamic measurements and real-time control applications. |
This combination of desirable operating characteristics, together with the wide range of physical properties that fiber sensors can measure, enables their use for a diverse range of tasks in quite a few different industries and applications. Some of the most important of these are:
- Structural health monitoring of civil and aerospace structures, such as bridges, dams, buildings, pipelines and aircraft. The sensors can detect damage, deformation, or vibration.
- Environmental sensing, such as monitoring temperature, humidity, pressure, and the concentration of various chemical species in air or water.
- Medical diagnostics, including the measurement of blood glucose, blood oxygen, or pH levels in vivo.
- Industrial process monitoring and control. This can include measuring the level, flow, or composition of fluids or gases in pipes or reactors.
- Defense and security. Fiber sensors can be used to detect intrusion, the displacement of objects or structures, or seismic activity in border or military installations.
The types of fiber sensors currently in use – their operating principles and exact methods of implementation – are as diverse as the applications just listed suggest. But they essentially all rely on the same underlying principle. Namely, light is introduced into an optical fiber and propagates through it. Then, something about the physical, chemical, or biological characteristics of the medium surrounding the fiber causes some change in the light which can be detected. This change can be in the intensity, phase, wavelength, or polarization state of the light (or a combination of these), as well as the scattering characteristics of the fiber itself. It’s worth examining each of these sensor mechanisms in detail.
Wavelength-based sensors
Wavelength-based sensors – particularly those utilizing Fiber Bragg Gratings (FBGs) – are among the most popular and widely used type. An FBG is a periodic modulation in core’s refractive index along the axis of the fiber. The FBG is “written” into the fiber at the time it is manufactured. This periodic pattern creates a Bragg grating that reflects a specific, small range of wavelengths.
One application of FBGs is to make a “distributed” sensor. Here, a series of FBGs – each made to reflect a slightly different wavelength – is written at different locations along a single fiber. When light travels down the fiber, each FBG reflects some back towards the source. Any local changes in temperature or mechanical strain in the structure alter the period of the nearby FBG and therefore shift the wavelength it reflects. Measuring this wavelength shift thus provides spatially resolved information about the strain and temperature along the fiber. A fiber sensor like this can be embedded in a large structure, like a dam or bridge.
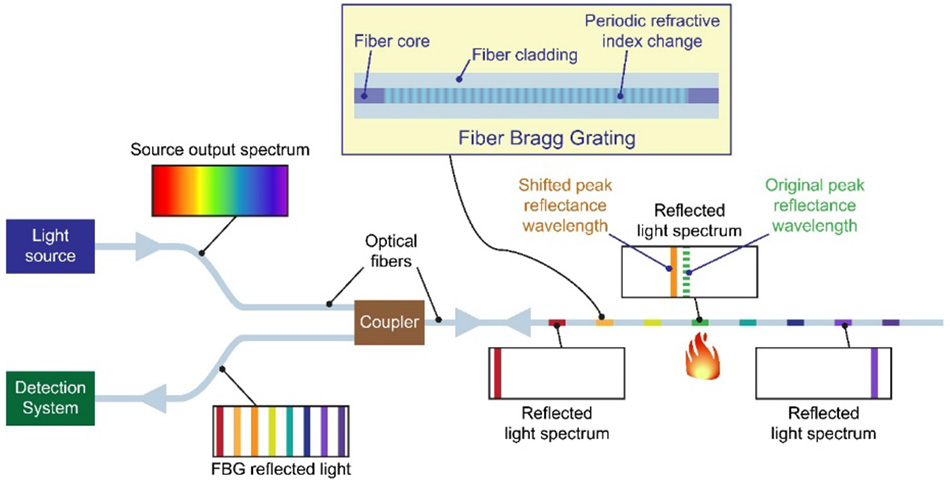
Figure 1. In a distributed fiber sensor, a series of FBGs along the fiber each reflect back a narrow range of wavelengths. Local temperature changes or mechanical strain shifts the peak wavelength of a nearby FBG. Analyzing the wavelengths of the returned light reveals which sensor has been perturbed, and by how much.
Wavelength-based fiber sensors also form the basis for a number of different types of biosensors. Many of these are based on surface plasmon resonance (SPR). This involves putting a thin metallic film (usually gold) directly on the fiber, or sometimes on an external optic located at the output end of the fiber.
Only a very specific wavelength will excite oscillation of plasmons at the metal-dielectric interface. This resonance wavelength will be less reflected than other wavelengths. This resonance wavelength is very sensitive to the refractive index of the metal layer.
To make a biosensor, the metal film is “functionalized.” That is, coated with a biomolecule (or even bacteria) which preferentially binds to, or uptakes, a particular target analyte. As analyte molecules bind to the sensor surface, they change its refractive index. This shifts the resonant wavelength. Analyzing the wavelength of the transmitted light thus provides a highly sensitive measure of the concentration of the target molecule.
Fiber biosensors provide several advantages, including fast measurement speed and high sensitivity. They do not require “labeling” of the analyte. As a result, they are used in numerous medical diagnostic processes, throughout biomedical research and drug development, and even in farming and food processing.
Phase-based sensors
Phase-based sensors are most commonly fiber optic interferometers. These measure the phase shift induced in an optical fiber or external optical cavity due to some change in the surrounding medium. Many different interferometer configurations are possible. The most popular are the Mach–Zehnder, Michelson, and Fabry–Perot interferometers.
Just as in their traditional free space counterparts, the Mach–Zehnder and Michelson interferometers both split the beam into two paths – a reference arm and a sensing arm. Only the sensing arm is exposed to the signal. Changes in physical length or refractive index within the sensing arm cause a relative phase shift between the paths which produce an interference fringe pattern at the detector. This provides the sensing signal.
The Fabry–Perot interferometer uses the fiber to supply light into an etalon (two, parallel, highly reflective surfaces separated by a distance), which is located at the point of measurement. Variations in optical path length within the Fabry-Perot cavity, caused by vibration, pressure, temperature, or refractive index (due to a gas or liquid entering the cavity) change the interference fringe pattern. This signal travels back through the fiber to the point of origin, where it is detected. This method is often used for measuring the downhole pressure in gas or oil pipelines or monitoring the strain or temperature of composite materials.
The fiber optic gyroscope is another type of phase-based fiber sensor. In this case, the fiber is in a tightly wound coil. The light source is first split into two beams, and then coupled into opposite ends of the fiber.
If the coil is rotating in its axis, then the two beams will undergo a phase shift relative to each other. This is called the Sagnac effect. When the two beams exit the fiber, they are recombined. Any phase shift will produce interference fringes in the combined beam. This pattern is sensed by the detector to determine the angular velocity of the rotation.
Polarization-based sensors
Most polarization-based sensors operate by introducing polarized light at 45° relative to the axis of a polarization maintaining optical fiber. Then, anything in the device under test which affects the fiber birefringence – typically temperature variations or mechanical strain – can be detected using a polarization analyzer at the output of the fiber. Many structural monitoring fiber sensors are polarization-based.
Polarization-based sensors can also be used to sense electric current. These rely on the Faraday effect, which produces a rotation in the polarization plane of light in the presence of a magnetic field. This can therefore be used to measure the magnetic field generated by an electric current. Fiber current sensors offer several advantages over traditional sensor types, including fast response speed, high accuracy, and small size and weight.
Intensity-based sensors
Intensity-based fiber sensors were actually the first type to ever be developed. They depend on a change in transmitted or reflected light intensity to make a measurement.
One simple intensity-based sensor is formed by embedding a fiber with a bend in it into a structure or mechanical component. Changes in the bend radius affect the light loss through the fiber. So, anything which causes a dimensional change in the object – pressure, acceleration, movement, thermal expansion – deforms the fiber and produces a signal.
Another way to produce an intensity change is to frustrate or reduce the amount of total internal reflection which the fiber depends upon to transmit light. Usually this happens when a refractive index change in the surrounding medium interacts with the evanescent field surrounding the fiber core. Typically, this involves removing some of the cladding over a length of the fiber allows the evanescent field to penetrate into the medium surrounding the fiber. Any change in this medium’s refractive index will then alter the fiber’s transmission properties. This can be used to sense liquid fluid levels or as a gas sensor.
While intensity-based sensors are generally simpler, and therefore lower cost than other types, they are not used extensively today. The problem is that anything which causes a change in optical power will generate a reading. While a reference system can minimize this, it’s difficult to eliminate noise and spurious readings from these sensors entirely.
Scattering-based sensors
A variety of different sensing techniques are based on Brillouin and Raman scattering within an optical fiber. These are used in combination with optical time domain reflectometry (OTDR).
Brillouin scattering occurs due to the interaction of light with acoustic modes in a medium. The peak wavelength for Brillouin scattering is strongly dependent on the refractive index of the material. This makes it sensitive to temperature or pressure changes in the surrounding medium.
To implement a Brillouin-based sensor, a pulse of light is sent down the fiber. The spectrum of the returned light is continuously analyzed. The time delay of any shift in the spectrum due to Brillouin scattering indicates how far along the fiber the scattering occurred, and therefore the location of the condition that caused it.
Raman scattering occurs when light interacts with molecular vibrations in the fiber. The Raman signal only depends on temperature. Raman sensing is implemented similarly to Brillouin sensing. Namely, a pulse of light is sent through the fiber, and the spectrum of returned light is analyzed as a function of time.
The great advantage of scattering-based sensors is that they utilize an intrinsic property of any silica fiber. This means they can be built using low-cost, commercially available optical fibers. Plus, both scattering techniques can work over very large distances – tens of kilometers. This makes them particularly useful for monitoring large or long structures.
Overall, the diverse capabilities and operational advantages of fiber sensors make them well-suited for a wide range of applications. Continuing advances in technology will certainly only increase their use in areas such as structural health monitoring, oil and gas exploration, biomedical sensing, environmental monitoring, industrial process monitoring, and many others.