ディスプレイ製造におけるレーザ:MicroLEDのリフトオフ、移設、修理
Coherent UVtransferシステムは、MicroLEDディスプレイの製造において重要な3つのステップを実行し、圧倒的な解像度と輝度を持つスケーラブルなディスプレイを実現します。
2022年10月4日、Coherent
フラットパネルディスプレイの製造工程を紹介する本連載の第6回は、レーザを用いてMicroLEDを用いた次世代ディスプレイの自動量産化について、未来に向けて考えてみたいと思います。
AMOLEDの技術は、スマートフォンやテレビの薄型ディスプレイを、素晴らしい色と解像度で提供しています。しかし、ディスプレイメーカーはすでに、ディスプレイの次の「大きなもの」である MicroLEDディスプレイ。
ディスプレイ製造におけるレーザに関する本シリーズの他のブログをお読みください |
|||
50ミクロン未満の小さな無機LEDをベースにしたこの新しい技術は、いくつかの利点があります。まず、有機ELの発光体に影響を与える可能性のある経年劣化の心配がありません。また、より高輝度、高コントラストを実現することができます。また、大型テレビやパブリックディスプレイをより経済的な価格で製造できるほか、VR/AR用途の超小型ディスプレイも製造できる可能性を秘めたスケーラブルな技術です。
MicroLEDディスプレイは、実は以前から限定的に存在していましたが、現在、ディスプレイメーカーがこれを本格的に生産する方法を見出しています。その結果、レーザはいくつかの重要な役割を担っていることがわかりました。見てみましょう
ウエハースケールエコノミー
無機(半導体)LEDは、自動車の高輝度ヘッドランプに使用されるなど、高い光量に対応しています。これにより、MicroLEDは非常に小さく、同時に非常に明るくすることができます。最先端のサイズは現在50×50ミクロン程度で、最終的には10×10ミクロンに近づくと予測されています。
このアクティブエミッターには、赤、緑、青の3種類があります。いずれも高密度にパターニングされたサファイアウェハー上に、エピタキシャル成長により量産されます。そのため、直径6インチのウエハーに数百万個のMicroLEDをパターン形成することができ、大規模な経済性を提供することができます。
これを最終的には、比較的安価な大型のガラスに必要な回路を載せて、薄型ディスプレイとして機能させます。複数のタイルで構成される大型ディスプレイでは、総表示面積が2メートル、画素ピッチが1ミリ以上になることもあります。1画素に3個の微小なエミッターを配置しても、ディスプレイの大部分はデッドスペースになってしまいます。大画面の場合、画素数が大きなコスト要因になるため、最終的なコストダウンが期待できます。
コンセプトはわかりやすいのですが、実際の実装は簡単ではありません。
リフトオフを実現する
実際に、これを実現するためには大きな課題があります。この数百万個のMicroLED(ダイ)を、作成したサファイアウェハーから移動させ、大型ディスプレイパネルに正確に配置する必要があります。信じられないかもしれませんが、初期の試作機では、個々の金型をバキュームロボットなどで機械的にピックアップし、配置していました。しかし、それでは最終的な生産に間に合いません。また、金型がさらに小さくなると、ハンドリング時に一部が破損するリスクもあり、迅速に行うことは困難です。8Kディスプレイの場合、3,000万画素以上、つまり1億個近いダイが必要となるため、歩留まりは非常に高くならざるを得ません。
その解決策として、本シリーズの以前のドキュメントで紹介した実績のある技術のいくつかに関連する自動多重化プロセスでレーザを使用することです。
実際には、リフトオフ、移設、修理という3つのプロセスが個別に必要です。まず、MicroLEDを成長させたサファイアウェハーから分離し、レーザリフトオフ(LLO)と呼ばれる従来のレーザを使った技術を使って、扱いやすいように仮のキャリアに移し替えます。キャリアに接着剤を塗布し、金型の上部に接触させます。エキシマレーザの紫外線をサファイアウェハーの裏側から照射し、ダイ形成前にウェハー上に蒸着された薄い犠牲層を蒸発させます。これにより、MicroLEDは一時的なキャリア上に残り、成長ウェハ上と同じ間隔で配置されます。
LIFT -ピッチを変える
次は、レーザ誘起前方転写送(LIFT)です。ここでは、紫外線(エキシマ)レーザからのパルスが、透明なキャリアの裏側から入ります。レーザ光はキャリアと接着剤を通過し、GaNに残ったバッファ層と相互作用します。これにより、転写残りがほとんどなく、短波長の紫外線を使用すれば、MicroLEDのユーザーとの接触面への影響もありません これにより、金型は物理的に吹き飛ばされ、最終的なディスプレイパネルに押し付けられます。ディスプレイパネルに密着させますが、衝突を避けるため、MicroLEDの厚みよりも大きなギャップを持たせる必要があります。最終的なガラスパネルの接着剤は、MicroLEDを所定の位置に保持します。
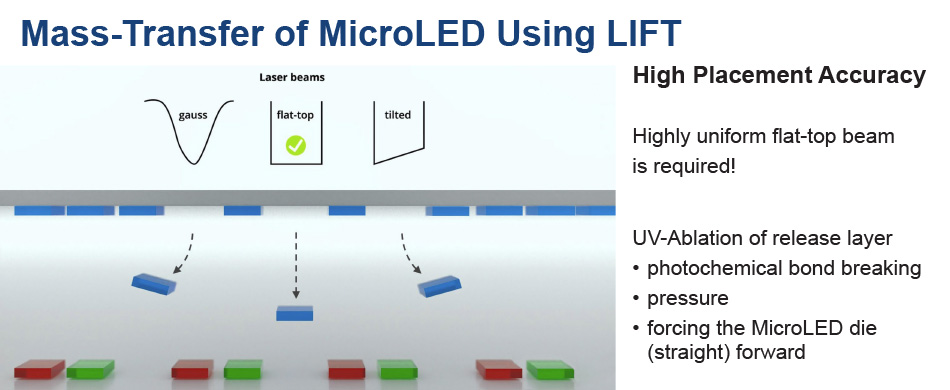
LIFTでは、大面積のレーザビームがフォトマスクを通過するため、特定のダイのみが解放され、ディスプレイ基板に押し付けられます。均一ないわゆるフラットトップビームは、完璧な配置に不可欠です。(縮尺どおりではありません)。
さて、肝心の「マジック」ですが、ピッチ(金型の間隔)を変更することになります。長方形のレーザビームは、穴のあいたマスクを通過します。そして、投影された穴のパターンが最終的なディスプレイの画素と同じ距離になるように、ビームを2.5倍または5倍に拡大解除します。これにより、EpiWafer上のLEDピッチの5分の1、10分の1、あるいはその他の整数倍が、レーザパルスによって数マイクロメートルの小さなギャップを越えてディスプレイに押し出されることになります。その後、キャリアは、固定ビームとマスクに対してごくわずかにMicroLEDの上を移動し、隣接するMicroLEDのセットに到達します。さらに表示パネルを移動させ、これを繰り返します。このステップと繰り返しが少し分かりにくいようであれば、わかりやすいビデオがありますので、ご安心ください。
また、一部のメーカーでは、EpiWaferからダイを持ち上げる際にピッチを変更する、少し変わったシーケンスに取り組んでいます。これは選択的LLOと呼ばれています。しかし、全体的な結果は同じです。
高スループットと修理
LIFTは、比較的小さなサファイアウェハー上に多数のマイクロLEDを経済的に製造し、それをより大きなセパレーション(ピッチ)で配置することで、1枚の大きなパネルを作ることを可能にするものです。そして、LIFTのもうひとつの大きなメリットは、高速であることです。1パルスで数千個のMicroLEDが動きます。
現在の研究開発では、エキシマレーザのパルスレートは最大20パルス/秒(20 Hz)で、最大640 mm2の面積を、わずか1秒でマイクロLEDで覆うことができます。しかし、このエキシマレーザ技術は、高い(1 J以上)パルスエネルギーと高い繰り返し率を使用するレーザアニーリング用途で実証されているように、極めて出力拡張性の高い技術です。LIFTでは、より高いパルスエネルギーを利用することで、より大きなマスクとフィールドサイズを実現することができます。
現在、無機マイクロLEDのような比較的簡単な半導体デバイスの歩留まりは、驚くほど高くなっています。しかし、各ディスプレイには数百万個のRGBデバイスが搭載されているため、ピクセルの欠陥や誤操作により、RGBデバイスの1つが正しく発光しない可能性がわずかながら存在します。その場合、自動化されたレーザプロセスでは、1つの穴が開いたマスクやスキャナーを使ったシステムを使って、交換用のダイを追加することで簡単に修復することができます。
Coherentはすでに、MicroLEDディスプレイの生産用にUVtransferというツールを提供していますが、このツールは、レーザリフトオフ(LLO)、レーザ誘起前転(LIFT)、欠陥画素の修復/トリミングの3つのプロセスをすべて実際に行うことができます。この3in1ツールにより、大型MicroLEDディスプレイの生産が実用的かつ経済的なものになります。
詳しくはCoherent UVtransferシステムをご覧ください。