激光器在显示制造中的应用:MicroLED 剥离、转移和修复
Coherent UVtransfer 系统可用于在 MicroLED 显示屏生产过程中执行三个关键步骤,助力生产出具有出色分辨率和亮度,且尺寸几乎没有限制的显示屏。
2022 年 10 月 4 日,作者:Coherent 高意
在平板显示屏生产系列的第六篇博客中,我们将展望未来,看看激光如何实现自动化批量生产基于 MicroLED 的下一代显示屏。
当前,AMOLED 技术为我们提供了适用于智能手机和电视的薄款显示屏,这些显示屏具有极为出众的色彩和分辨率。然而,显示屏制造商已经开始筹谋大批量生产新一代显示屏了,也就是 MicroLED 显示屏。
阅读“激光器在显示屏制造中的应用”系列博客中的其他博客 |
|||
这项快速兴起的技术基于小型(<50 微米)无机 LED,具有多种优势。首先,它没有过早老化问题。有些情况下,过早老化会对 OLED 发光体造成影响。此外,它可以提供更高的亮度和对比度。同时,这种技术可应用于大大小小的屏幕,既有可能实现以更经济的价格生产大型电视和公共显示屏,又可用于生产 VR/AR 设备的超紧凑型显示屏。
实际上,MicroLED 显示屏的面世已有一段时间,只不过产量有限。目前,显示屏制造商正在研究如何将其投入全面生产。事实证明,激光在其中发挥着几个关键作用。我们来详细了解一下。
晶圆助力实现规模经济
无机(半导体)LED 支持高光输出,比如它们可应用于高亮度汽车前照灯。因此,作为无机 LED 的 MicroLED 就可以做到尺寸虽小,但非常明亮。目前,较先进的 MicroLED 尺寸约为 50 微米 x 50 微米,预计最终将接近 10 微米 x 10 微米。
这些有源发光体分为三种:红、绿和蓝。每种类型的有源发光体都是在密集图案化的蓝宝石晶圆上批量生产的(采用外延生长技术)。因此,一个直径 6 英寸的图案化晶圆可以有数百万颗单独的 MicroLED,从而实现规模经济。
这些 MicroLED 最终被放置在一块相对便宜的大尺寸玻璃上,再配上必要的电路,就是一块薄款显示屏了。由几个单独的面板拼成的大型显示屏可能总共有两米宽,像素间距可能是一毫米或以上。即使在每个像素点有三个这样的微型发光体,显示屏的大部分区域都是空着的。对于发展大尺寸屏幕方面,主要成本驱动因素是像素数量,因此这种技术有望最终降低成本。
这个概念看似简单,但实际实施起来绝非如此!
实现剥离
实际上,要完成所有这些工作,存在一个贯穿始终的巨大挑战。必须将数百万颗 MicroLED(裸片)从制造它们的蓝宝石晶圆上移出,并精确地放置在大型显示面板上。也许您想不到,在早期的一些原型中,每颗裸片都是通过机械方式拾取和放置的,例如借助真空机器人。但这对于最终生产来说太慢了。而且,随着裸片尺寸变得更小,很难做到在快速拾取和放置的同时,避免在处理过程中损坏其中一些裸片。良率必须非常高,因为裸片数量非常大,以 8K 显示屏为例,它有超过 3000 万像素,也就是近 1 亿颗裸片。
解决方案是在自动化多重工艺(涉及本系列之前几篇文章中介绍的一些成熟技术)中采用激光技术。
实际上涉及三个独立的过程:起飞、转移和修复。首先,使用一项基于激光的传统技术,即激光剥离技术 (LLO),将 MicroLED 与生产它们的蓝宝石晶圆分离,然后将其转移到临时载体上,以便于处理。载体涂有粘合剂,并与裸片顶部接触。准分子激光器发出的紫外光从蓝宝石晶圆后射出,将在裸片形成之前沉积在晶圆上的可蒸发薄材料层汽化。这样一来,MicroLED 就以其在晶圆上生长时的间距转移到了临时载体上。
LIFT——改变间距
接下来是激光诱导前向转移 (LIFT)。在这一步,来自紫外光(准分子)激光器的脉冲会从透明载体的背面进入。激光穿过载体和粘合剂,并与剩余的 GaN 缓冲层发生相互作用。如果使用短紫外光波长,则可以实现几乎没有残留物的转移,并且对 MicroLED 面向客户的表面几乎没有影响!这实际上是将裸片从载体上吹离,并将它们推到最终显示面板上。最终显示面板是紧挨着放置的,但有一定间隙,这个间隙必须大于 MicroLED 的厚度以避免碰撞。最终玻璃面板上的粘合剂会将 MicroLED 固定在位。
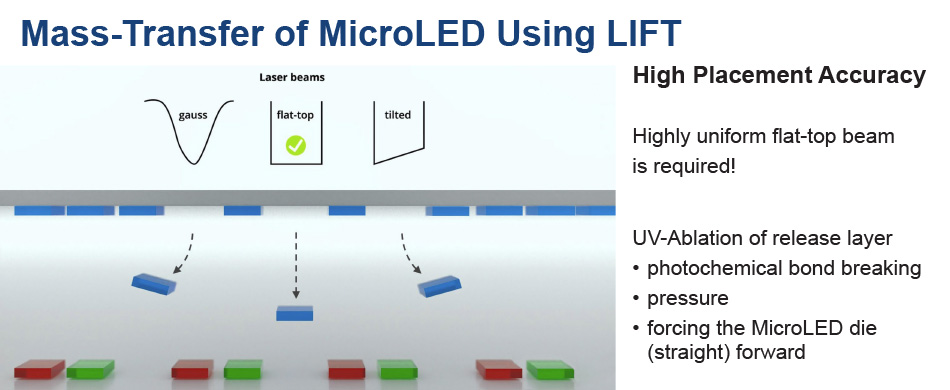
在巨量转移中,大面积激光束穿过掩膜板,以便仅释放特定芯片并将其推到显示基板上。所谓的均匀平顶光束对于精确放置来说至关重要。(不按比例)。
现在来到了“魔法”的关键部分,即改变间距(裸片间距)。矩形激光束穿过一个有孔的掩膜板。然后,将光束缩小 2.5 倍或 5 倍,以便投射的孔图案与最终显示屏中的像素间距相同。通过这种方式,可以按每 5 个,甚至每 10 个,或每任何其他整数个 LED 中只有 1 个被给定的激光脉冲推动的间距,将 EpiWafer 上的 LED 经过几微米的微小间隙推到显示屏。然后,载体相对于固定光束和掩膜板略微移动,以转到相邻的 MicroLED 组。显示面板则会移动较远的距离。然后再重复这一过程。如果您觉得上述步骤和过程重复听起来有点混乱,无需担心;我们有一段精彩的视频,可以帮助您轻松理解这些内容。
另外,一些制造商正在研究一种略微不同的方法,这种方法是随着裸片从 EpiWafer 上剥离而改变间距。这称为选择性激光剥离。但总体结果是一样的。
高吞吐量和强修复能力
LIFT 支持在相对较小的蓝宝石晶圆上经济地生产大量 MicroLED,然后以更大的间隔(间距)放置它们,从而制造出单个大幅面显示屏。此外,LIFT 的另一个显著优势是速度快。每次脉冲可以转移数以千计的 MicroLED。
在当前以研发为目标的实施中,准分子激光脉冲频率高达 20 脉冲/秒 (20 Hz),这意味着可以在一秒钟内用 MicroLED 覆盖高达 640 平方毫米的区域!而且在使用高(超过 1 J)脉冲能量和高重复频率的退火应用中,这种准分子激光技术也表现出了极为出色的可扩展功率水平。使用 LIFT 工艺,可以利用更高的脉冲能量来实现更大的掩膜板和场尺寸。
现在,对于制造相对简单的半导体器件(如无机 MicroLED),其良率已经达到了非常高的水平。但是每个显示屏上都有数百万个器件,因此存在像素有缺陷或处理不当的可能性,即其中一个 RGB 器件没有正确发光。不过这种可能性很小,并且有限。通过使用带有单孔的掩膜板或基于扫描仪的系统添加替换裸片,这很容易用自动激光工艺进行修复。
Coherent 高意现已提供一款名为 UVtransfer 的 MicroLED 显示屏生产工具。该工具可执行全部三项工艺:激光剥离 (LLO)、激光诱导前向转移 (LIFT) 以及缺陷像素的修复和修整。这款三合一工具将助力生产出实用且经济的大型 MicroLED 显示屏。
了解更多关于 Coherent UVtransfer 系统的信息。