大型精密オプティクスの高速加工
Coherentは、最新鋭の超音波工作機械を設置して、30 m望遠鏡の直径1.5 mのセグメント鏡の「ヘキシング」を高速化しています。
2023年8月24日、Coherent
望遠鏡のミラーに関して言えば、大きいほど優れています。光の基本的な物理学では、望遠鏡の口径が大きくなればなるほど、画像はより明るく、より高精細になります。ただし、これは理論上の話です。
実際には、鏡のサイズが大きくなるにつれて、高画質を得るのに十分な精度の表面形状で作ることが難しくなります。現在、鏡の大きさの実用的な限界は直径約8.5 mです。
しかし、科学者たちはこの制限を回避する非常に巧妙な回避策を開発しました。大きな望遠鏡の鏡を1枚作る代わりに、小さな鏡をモザイク状に並べ、1枚の大きな鏡のように使うのです。これらの個々のセグメント鏡は、非常に接近して配置できるように、通常は六角形として成形されます。
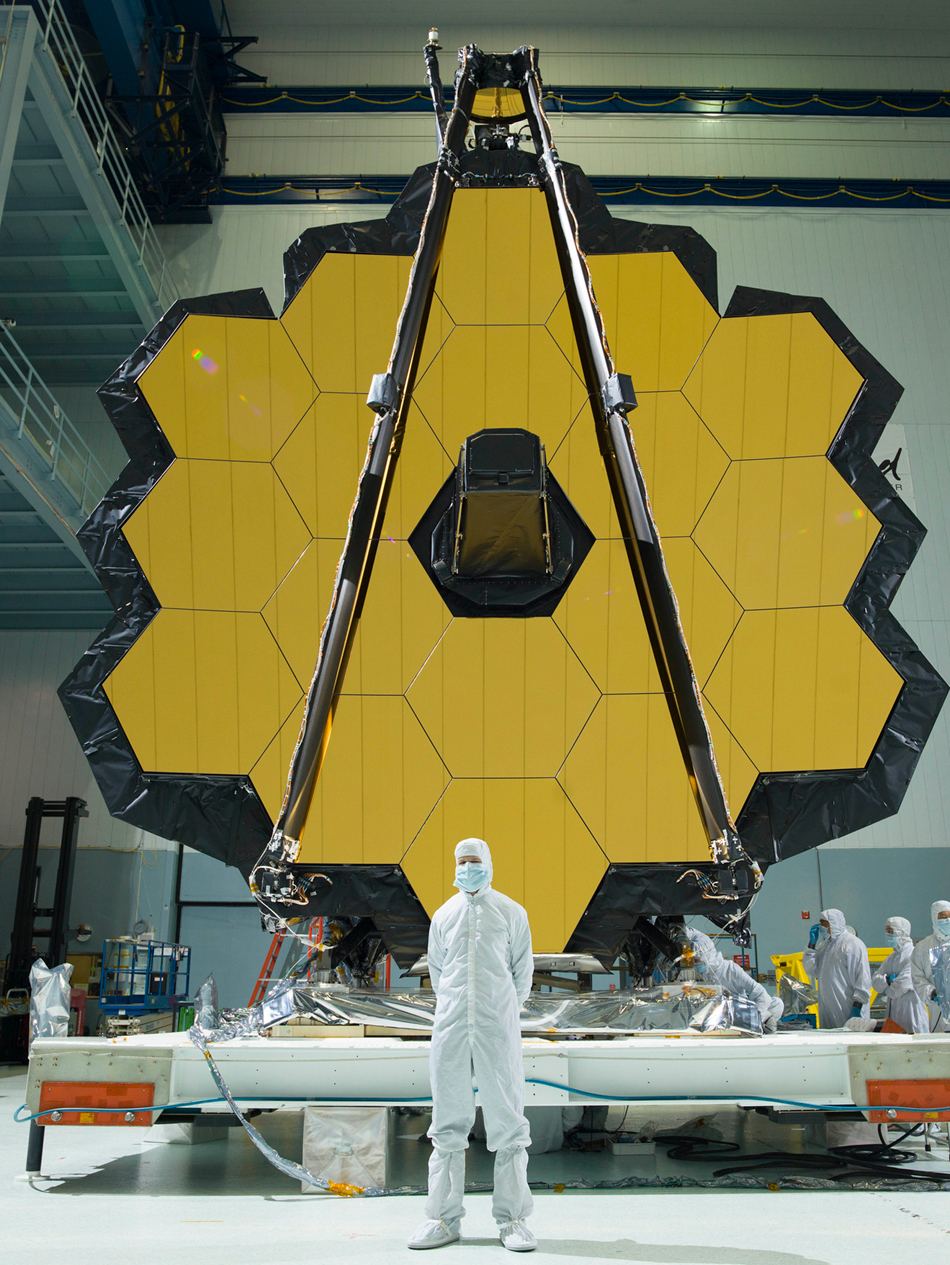
ジェイムズ・ウェッブ宇宙望遠鏡の主鏡のような大型望遠鏡の鏡は、多くの場合、近接して(2 mm以内)配置された多数の六角形のセグメント鏡で構成されています。画像提供:NASAゴダード宇宙センター。
これはまさに、30 m望遠鏡の建設に使用されているアプローチです。地上にあるこの天文台は、ハッブル宇宙望遠鏡の12倍以上、JWSTの4倍以上の鮮明な(赤外線)画像を提供することを目的としています。
30 m望遠鏡の主鏡は492枚の六角形のセグメント鏡で構成され、それぞれの隅から隅までの長さは1.44 mです。Coherentはこれらのセグメント鏡を230枚製造しています。
これらの鏡は、直径1.5 mの丸い形から始まります。その理由は、軸から外れた双曲線の自由曲面形状を作り出すために私たちが使っている「応力鏡面研磨」技術には、剛性が高い、対称的な丸い基板が必要であるからです。最初の研磨加工方法の後、この丸い鏡(「ラウンデル」)は六角形に仕上げられます(「ヘキシング」)。
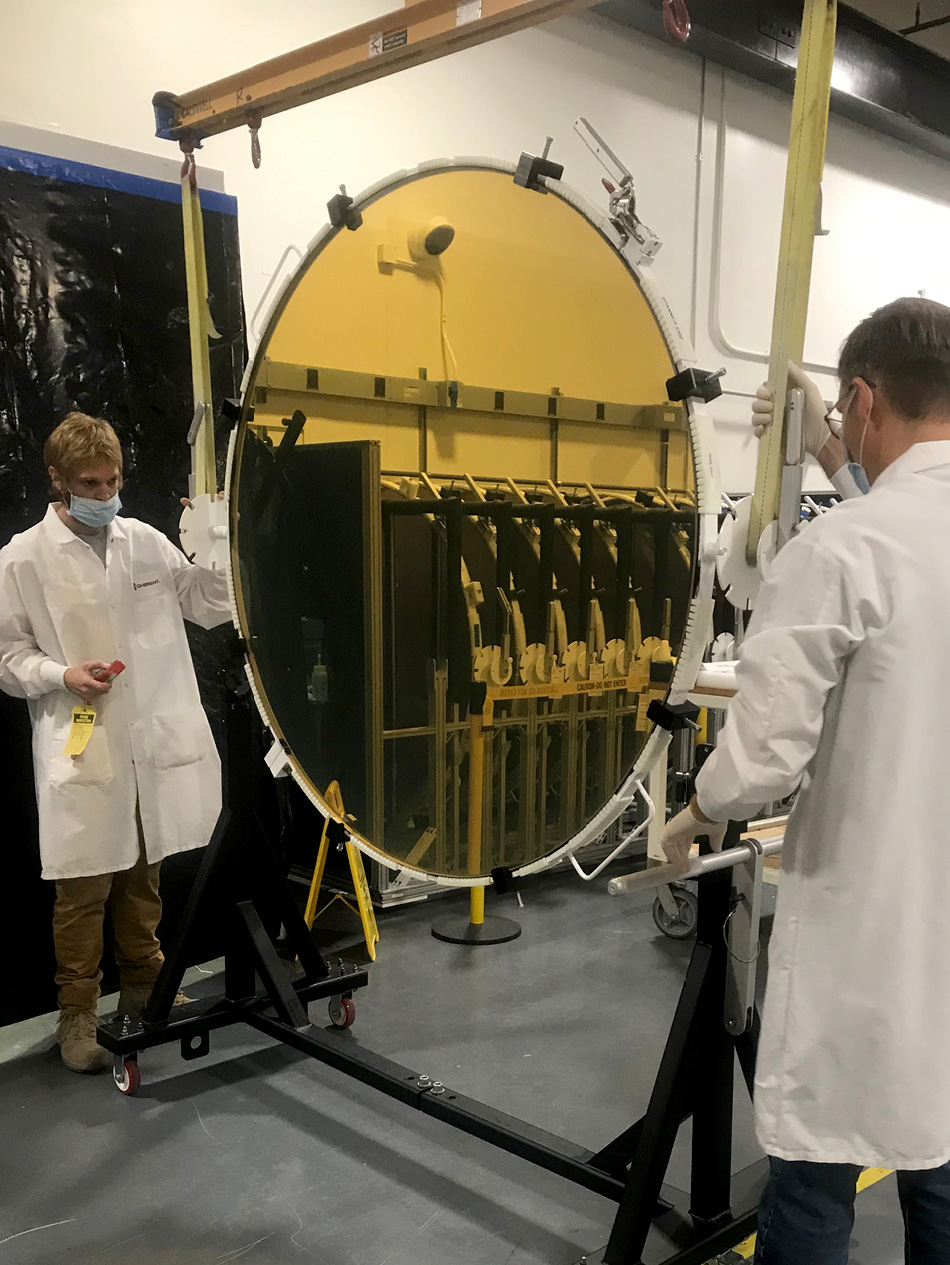
Coherentが製造する230枚のTMTラウンデルの直径は1.5 mで、その後、隅から隅まで1.44 mに「ヘキシング」されます。
この時、鏡の側面にも精密な取り付け機構が追加されます。具体的には、これらの「センサーポケット」は、最高の画質を維持するために鏡をリアルタイムで位置合わせするセンサーとアクチュエーターのネットワーク用です。これにより、地上のTMTは宇宙ベースの赤外線での空間分解能を上回ることができるようになります。
ガラスの加工
この種の成形は光学製造では一般的で、通常はコンピューター数値制御(CNC)の下で操作される、本質的に従来のフライス盤で行われます。ただし、光学部品に使用されるさまざまなガラス材料は非常に脆く、金属よりも加工が困難です。加工するにはダイヤモンドツールが必要です。
ダイヤモンド工作機械は1世紀以上も前から使われています。これらは非常に優れており、光学工業では広く使用されています。しかし、最新の自動化によってより速く、より効率的に作業できるようになったとはいえ、まだ比較的時間がかかります。これは、大型の光学部品から大量の材料を除去する際に問題となることがあります。
Coherent(旧Tinsley Optical Systems)のエンジニアは、TMT用に製造している230枚のラウンデルのヘキシングを任されたとき、この限界に直面しました。私たちは、今後数年かけて、このプログラムを完成させたいと考えています。
十分な時間だと思われるかもしれませんが、実際にはそれほど簡単な問題ではありません。各ラウンデルを連続的にヘキシングする場合(1台の機械で次々にヘキシングする場合)、従来のフライス加工システムでこれだけの数のヘキシングを行うには、通常10年はかかる可能性があります。
ヘキシングの高速化
ここ数年、マシンメーカーは最新鋭の超音波工作機械を組み込んだシステムを開発してきました。具体的には、標準的なツールの高速回転に加え、ダイヤモンドツールの軸に沿って小振幅の高速振動(数十kHzの範囲)を発生させます。
この技術には、いくつかの重要な利点があります。第一に、従来のダイヤモンドツールによるフライス加工よりもはるかに(6倍から10倍)高い材料除去率が得られます。また、超音波ツールは従来のツールよりも加工物に加える力が小さいため、通常、機械的応力がほとんど発生せず、部品の物理的な歪みを避けることができます。これにより、表面下の損傷が減少し、より滑らかな仕上がりが得られ、薄肉形状が製造できます。
また、力が小さいため、ツールの摩耗が少なく、ツールの寿命が延びます。さらに、超音波ツールは「セルフドレッシング」です。つまり、使用中に新しいダイヤモンド砥粒が自動的にツールに露出するため、切断力が維持されます。通常は、ツールを定期的に取り外して、別の作業でドレッシングする必要があります。ツールの交換やメンテナンスの頻度が減り、装置のダウンタイムが削減されます。
特に半導体業界では、大型で高精度の部品を製造するメーカーが超音波アシスト加工を採用しています。しかし、現在までのところ、この技術は航空宇宙や天文用途の大型光学部品には採用されていません。
超音波を使う準備をする
Coherentは、TMTラウンデルのヘキシングに十分な大きさの超音波アシスト加工システムを導入することで、これを初めて実現しました。また、切断加工方法中に光学部品をマシニングセンタ内に保持するための特殊なツールも開発しました。
直径1.5 mのラウンデルの重量は0.25メートルトン(550ポンド)ですが、厚さはわずか45 mmしかないため、このツールは非常に重要です。そのため、非対称的または局所的な機械的力を加えるような持ち方をすると、簡単に形状が歪みます。これにより、切断後に冶具から離したときに部品が「バネ」のようになり、加工された形状が仕様に合わなくなるほど形状が変わってしまう可能性があります。
そのため、「ゼロ応力マウント」を使用する必要があります。具体的には、ラウンデルの表面形状を歪ませないようにしながらも、加工方法の力に対して光学部品が剛性的に保持されるようにする加工方法です。
機械加工用に光学部品を取り付ける場合、真空チャックを使用するのが一般的です。しかし、この方法では、TMTラウンデルのようなサイズと精度の自由曲面(非対称・非球面)光学部品をゼロ応力でマウントすることはできません。鏡に合うような正確な形状の取り付け面を製作するのは不可能です。
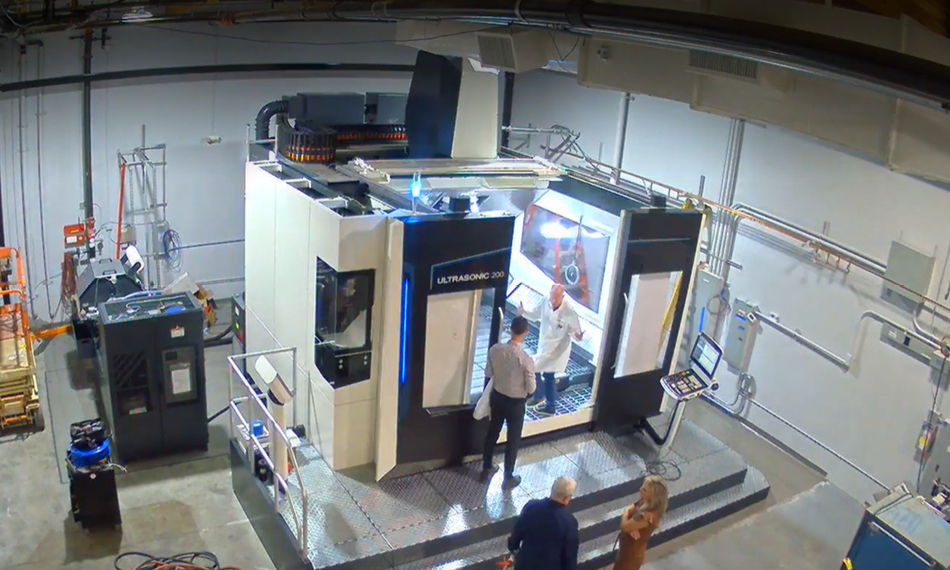
超音波アシスト加工システムは、現在Coherentで製造している230枚のラウンデルの精密ヘキシングに対応できるように構成される予定です。
その代わりに、Coherentのエンジニアは、サポートとクランプシステムのマルチテクノロジーネットワークを採用した独自のツーリングアプローチを開発しました。これにより、曲げを発生させることなく、あらゆる自由度で部品を固定することができます。
ラウンデルのヘキシングに必要な切断精度を維持するためには、マシニングセンタ全体が極めて安定した土台の上に配置されていることも重要です。また、周囲の環境条件も一定に保つ必要があります。一方で、この工作機械はピックアップトラックよりも大きく、重いということに留意する必要があります。
そのため、その機械を維持するための専用施設を構築する必要がありました。機械の重量を支え、必要な機械的安定性を確保するため、鉄筋で補強された新しいコンクリート製マウントパッドを打ち込むことから始めました。さらに、製造エリア全体の温度管理を改善し、周囲環境の変化をなくしました。
ヘキシングに先立つラウンデルの光学部品加工方法の詳細については、こちらをご覧ください。