Schnellere Verarbeitung für große Präzisionsoptiken
Coherent installiert eine fortschrittliche Ultraschall-Werkzeugmaschine, um das „Hexing“ der Spiegelsegmente des Thirty-Meter-Teleskops mit einem Durchmesser von 1,5 m zu beschleunigen.
24. August 2023 von Coherent
Wenn es um Teleskopspiegel geht, heißt es: je größer, desto besser. Die grundlegende Physik des Lichts schreibt vor, dass die Bilder mit zunehmender Öffnungsweite des Teleskops heller und detaillierter werden. In der Theorie.
In der Praxis wird es mit zunehmender Spiegelgröße schwieriger, eine Oberflächenform herzustellen, die präzise genug ist, um eine hohe Bildqualität zu erzeugen. Die derzeitige praktische Grenze für die Spiegelgröße liegt bei einem Durchmesser von etwa 8,5 m.
Doch Wissenschaftler haben eine sehr clevere Lösung entwickelt, um diese Einschränkung zu umgehen. Anstatt einen einzelnen großen Teleskopspiegel herzustellen, verwenden sie jetzt ein Mosaik kleinerer Spiegel, die wie ein einzelner, größerer Spiegel wirken. Diese einzelnen Segmente haben meist die Form von Sechsecken, damit sie sehr nahe beieinander platziert werden können.
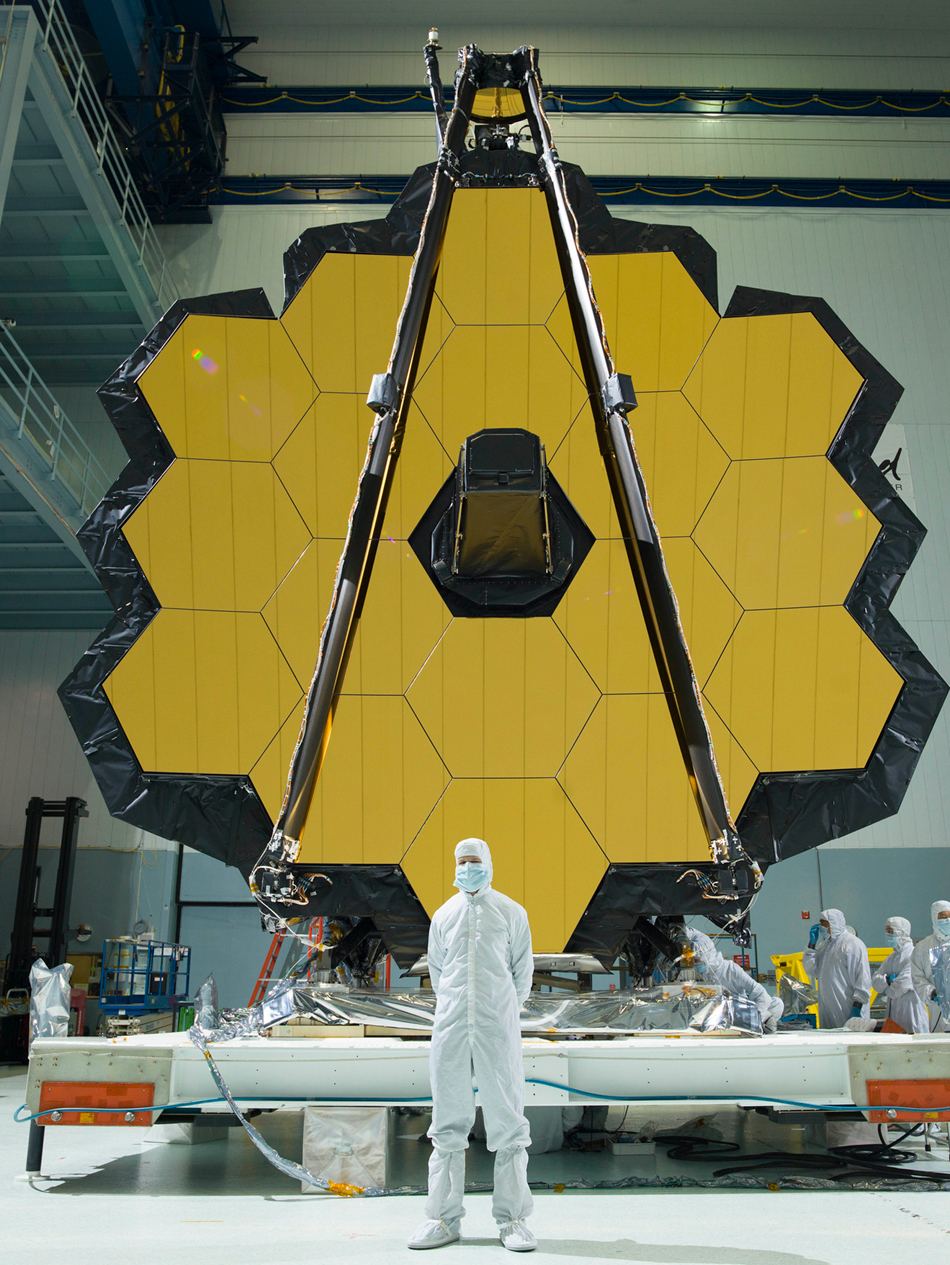
Große Teleskopspiegel, wie der hier gezeigte Primärspiegel des James Webb Space Telescope (JWST), bestehen häufig aus zahlreichen sechseckigen Segmenten, die nahe beieinander angeordnet sind (innerhalb von 2 mm). Bild mit freundlicher Genehmigung des NASA Goddard Space Center.
Genau dieser Ansatz wird beim Bau des Thirty Meter Telescope verfolgt. Dieses bodengestützte Observatorium soll (Infrarot-)Bilder liefern, die mehr als zwölfmal schärfer sind als das Hubble-Weltraumteleskop und viermal schärfer als das JWST.
Der Hauptspiegel des Thirty Meter Telescope wird aus 492 sechseckigen Segmenten bestehen, von denen jedes 1,44 m von Ecke zu Ecke misst. Coherent fertigt 230 dieser Spiegelsegmente.
Ausgangsform dieser Spiegel ist eine runde Form mit einem Durchmesser von 1,5 m. Dies ist notwendig, da die „Stress Mirror Polishing“-Technik, die wir verwenden, um ihre außeraxiale, hyperbolische freiförmige Form zu erzeugen, ein starres, symmetrisches, rundes Substrat erfordert. Nach dem ersten Poliervorgang werden diese runden Spiegel („Spiegelrundsegmente“) zu Sechsecken geformt („Hexing“).
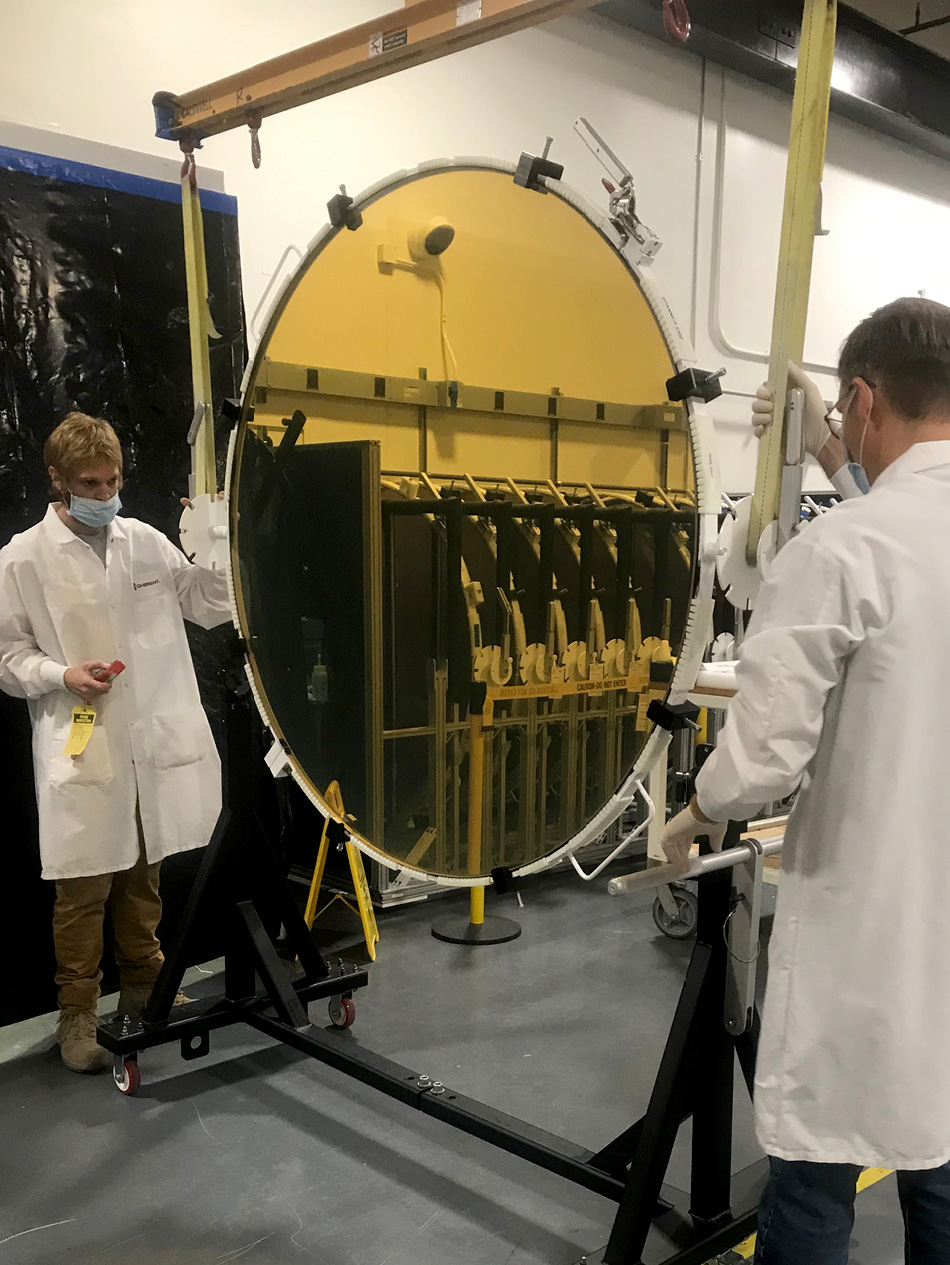
Jedes der von Coherent hergestellten 230 TMT-Spiegelrundsegmente hat einen Durchmesser von 1,5 m und wird anschließend von Kante zu Kante auf 1,44 m verkleinert.
Zu diesem Zeitpunkt werden auch weitere Präzisionsmontagefunktionen an den Seiten der Spiegel hinzugefügt. Konkret handelt es sich bei diesen „Sensortaschen“ um das Netzwerk aus Sensoren und Aktuatoren, die den Spiegel in Echtzeit positionieren, um die bestmögliche Bildqualität aufrechtzuerhalten. Dadurch wird es dem bodengestützten TMT möglich sein, die räumliche Auflösung im Infrarotbereich weltraumgestützter Instrumente zu übertreffen.
Bearbeitung von Glas
Diese Art der Formgebung ist in der optischen Fertigung üblich und wird typischerweise mit einer im Wesentlichen herkömmlichen Fräsmaschine durchgeführt, die normalerweise im Rahmen einer computergestützten numerischen Steuerung (CNC) betrieben wird. Allerdings sind die für Optiken verwendeten verschiedenen Glasmaterialien sehr spröde und schwieriger zu bearbeiten als Metall. Für die Bearbeitung werden Diamantwerkzeuge benötigt.
Diamant-Werkzeugmaschinen sind seit mehr als einem Jahrhundert im Einsatz. Sie funktionieren hervorragend und werden in der gesamten Optikindustrie häufig eingesetzt. Doch auch wenn sie dank moderner Automatisierung schneller und effizienter arbeiten können, sind sie immer noch relativ langsam. Dies kann manchmal zum Problem werden, wenn große Materialmengen von großen Optiken entfernt werden.
Die Ingenieure von Coherent (ehemals Tinsley Optical Systems) wurden mit dieser Einschränkung direkt konfrontiert, als sie mit dem Hexing der 230 Spiegelrundsegmente beauftragt wurden, die wir für das TMT herstellen. Dieses Programm möchten wir im Laufe der nächsten Jahre erfolgreich abschließen.
Das hört sich wahrscheinlich nach viel Zeit an. Das ist es nicht! Wenn jedes der Spiegelrundsegmente nacheinander in die sechseckige Form gebracht würde (eines nach dem anderen auf einer einzigen Maschine), würde es normalerweise fast ein Jahrzehnt dauern, bis so viele Spiegelrundsegmente mit einem herkömmlichen Frässystem verarbeitet worden wären.
Das Hexing-Verfahren beschleunigen
In den letzten Jahren haben Werkzeughersteller Systeme entwickelt, die eine fortschrittliche Form der Ultraschallbearbeitung beinhalten. Konkret handelt es sich dabei um eine schnelle Oszillation mit kleiner Amplitude (im Bereich von mehreren zehn kHz) des Diamantwerkzeugs entlang seiner Achse, zusätzlich zur standardmäßigen Hochgeschwindigkeitsrotation des Werkzeugs.
Diese Technologie bietet mehrere wichtige Vorteile. Erstens erreicht sie eine viel höhere Materialabtragsrate als das herkömmliche Fräsen mit Diamantwerkzeugen – etwa sechs- bis zehnmal schneller. Und da das Ultraschallwerkzeug weniger Kraft auf das Werkstück als ein herkömmliches Werkzeug ausübt, erzeugt es normalerweise nur eine geringe mechanische Belastung, wodurch eine physische Verformung des Teils vermieden wird. Dies reduziert Schäden unter der Oberfläche, sorgt für eine glattere Oberfläche und ermöglicht die Herstellung dünnwandigerer Eigenschaften.
Durch die geringere Kraft verringert sich auch der Werkzeugverschleiß, wodurch sich die Lebensdauer verlängert. Außerdem ist das Ultraschallgerät „selbst-aufbereitend“. Das bedeutet, dass durch den Gebrauch automatisch frische Diamantkörner auf dem Werkzeug freigelegt werden, wodurch dessen Schneidkraft erhalten bleibt. Normalerweise müssen Werkzeuge in regelmäßigen Abständen in einem separaten Arbeitsgang ausgebaut und aufbereitet werden. Durch den selteneren Austausch und die seltenere Wartung von Werkzeugen werden Ausfallzeiten der Geräte reduziert.
Aus genau diesen Gründen haben sich Hersteller von großen, hochpräzisen Teilen – insbesondere in der Halbleiterindustrie – für die ultraschallunterstützte Bearbeitung entschieden. Bisher wurde diese Technologie jedoch nicht für große optische Komponenten für Anwendungen in der Luft- und Raumfahrt sowie in der Astronomie eingesetzt. .
Vorbereitung für die Ultraschall-Nutzung
Coherent hat dies als Erster geschafft, indem es ein ultraschallunterstütztes Bearbeitungssystem installiert hat, das groß genug ist, um die TMT-Spiegelrundsegmente in die sechseckige Form zu bringen. Wir haben auch einige sehr spezielle Werkzeuge entwickelt, um die Optik während des Schneidvorgangs im Bearbeitungszentrum zu halten.
Dieses Werkzeug ist von entscheidender Bedeutung, da die Spiegelrundsegmente mit einem Durchmesser von 1,5 m 0,25 Tonnen wiegen, aber nur 45 mm dick sind. Dadurch kann ihre Form sehr leicht durch das Halten in einer Weise verzogen werden, durch die beliebige asymmetrische oder lokale mechanische Kräfte ausgeübt werden. Dies kann dazu führen, dass das Teil „springt“, wenn es nach dem Schneiden von der Vorrichtung gelöst wird, und sich dabei seine Form so stark verändert, dass die bearbeiteten Merkmale nicht mehr den Spezifikationen entsprechen.
Es ist daher notwendig, eine „spannungsfreie Montage“ zu verwenden. Konkret handelt es sich dabei um eine Montagemethode, die eine Verformung der runden Oberflächenform vermeidet und gleichzeitig sicherstellt, dass die Optik den Kräften des Fräsprozesses standhält.
Ein gängiger Ansatz bei der Montage von Optiken für die Bearbeitung ist die Verwendung eines Vakuumspannfutters. Allerdings gibt es bei dieser Methode keine Möglichkeit, eine spannungsfreie Montage einer Freiformoptik (asymmetrisch und asphärisch) in der Größe und Präzision der TMT-Spiegelrundsegmente zu erreichen. Es ist einfach nicht möglich, eine Montagefläche mit einer Form herzustellen, die genau genug ist, um mit dem Spiegel übereinzustimmen.
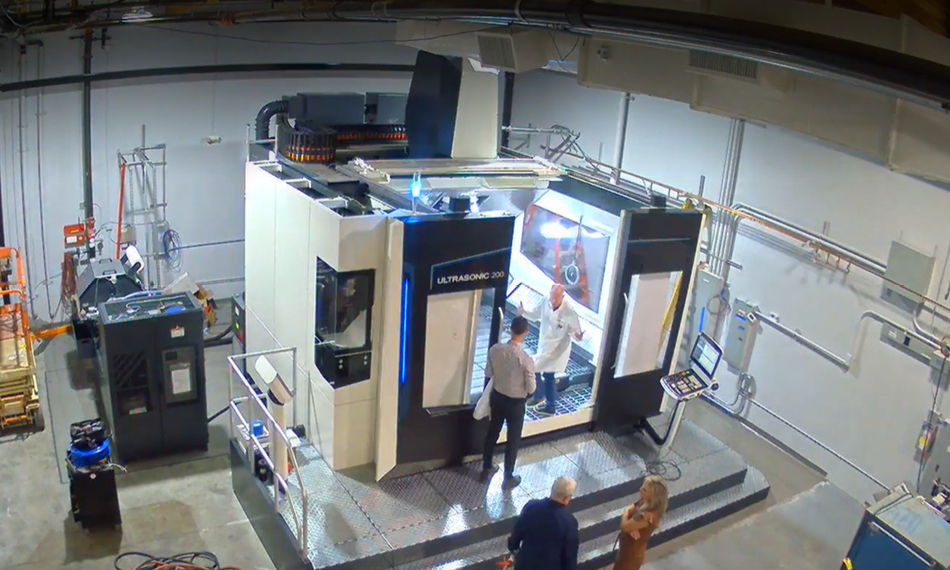
Das ultraschallunterstützte Bearbeitungssystem wird für die Präzisionssechseckbearbeitung der 230 Spiegelrundsegmente konfiguriert, die derzeit bei Coherent hergestellt werden.
Stattdessen haben die Ingenieure von Coherent einen proprietären Werkzeugansatz entwickelt, der ein Multi-Technologie-Netzwerk aus Stütz- und Spannsystemen nutzt. Diese sichern das Teil in allen Freiheitsgraden, ohne dass es zu einer Biegung kommt.
Um die beim Sechseckschneiden der Spiegelrundsegmente erforderliche Schnittgenauigkeit zu gewährleisten, ist es außerdem wichtig, dass das gesamte Bearbeitungszentrum auf einem äußerst stabilen Fundament steht. Und auch die Umgebungsbedingungen müssen konstant gehalten werden. Es ist jedoch zu bedenken, dass diese Werkzeugmaschine größer und schwerer als ein Pickup ist.
Daher mussten wir eine eigens dafür errichtete Anlage schaffen. Dies begann mit dem Gießen einer neuen Beton-Fundamentplatte für die Anlage, die umfassend mit Bewehrungsstäben verstärkt wurde, um das Gewicht der Maschine zu tragen und die erforderliche mechanische Stabilität zu gewährleisten. Darüber hinaus haben wir die Temperaturkontrolle im gesamten Produktionsbereich verbessert, um jegliche Änderungen in der Umgebungsumgebung zu verhindern.
Erfahren Sie hier mehr über den Herstellungsprozess der Spiegelrundsegmente in der Vorstufe zum Hexing-Prozess.