更快地加工大型精密光学部件
Coherent 高意安装了先进的超声波机床,以期更快地完成对直径为 1.5 米的三十米望远镜 (TMT) 镜段的六边形切割。
2023 年 8 月 24 日,作者:Coherent 高意
对于望远镜来说,反射镜尺寸越大越好。光的基本物理学原理表明,望远镜孔径越大,图像会更亮、细节也会更丰富。理论上是这样。
但实际上,如果反射镜尺寸加大,则会更加难以获得精确的表面形状来生成优质图像。目前反射镜尺寸的实际限制是直径约 8.5 米。
但科学家们已经研究出一种非常巧妙的解决方法来打破这种限制。他们现在不再制作一面大型望远镜反射镜,而是用一组小镜面拼合在一起,其作用等同于一个大镜面。这些小镜面的形状通常为六边形,以便可以将它们紧密拼合在一起。
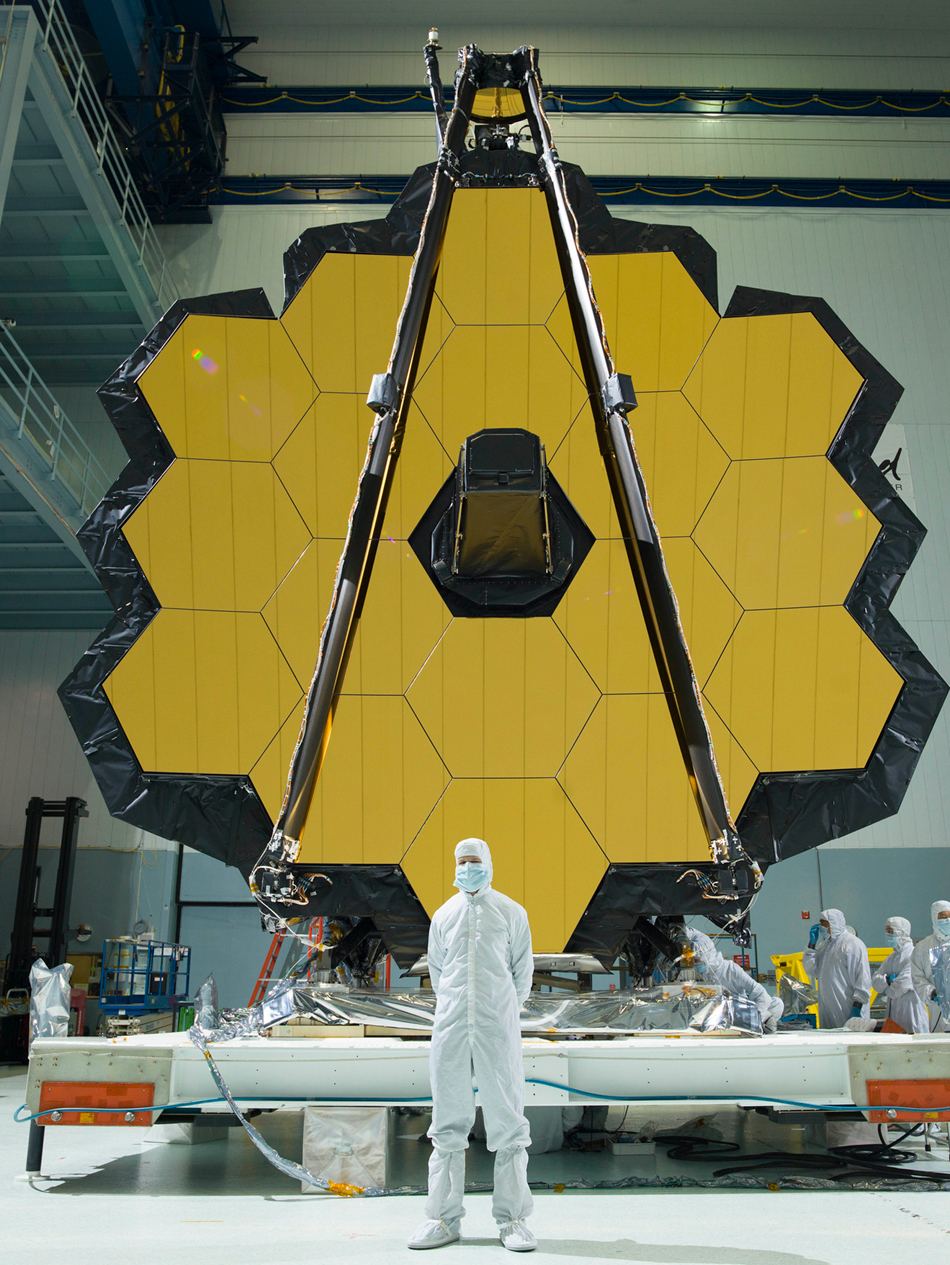
大型望远镜的反射镜(例如此处所示的詹姆斯·韦伯太空望远镜的主镜)通常由许多六边形小镜面(2 mm 以内)拼合而成。图片由美国国家航空航天局戈达德太空飞行中心提供。
三十米望远镜正是采用这种方法制造。该地面天文台旨在提供比哈勃太空望远镜清晰 12 倍以上、比詹姆斯·韦伯太空望远镜清晰四倍的(红外)图像。
三十米望远镜的主镜将由 492 个六边形小镜面拼合而成,每个镜面各个角之间的距离为 1.44 米。Coherent 正在制造 230 个这样的小镜面。
这些镜面最初均为圆形,直径为 1.5 米。之所以要用圆形镜面,是因为我们用来制作离轴、双曲线、自由形状的“应力镜面抛光”技术需要刚性且对称的圆形基材。经过最初的抛光工艺后,这些圆形镜面(“圆镜面”)被制作成六边形(“六边形切割”)。
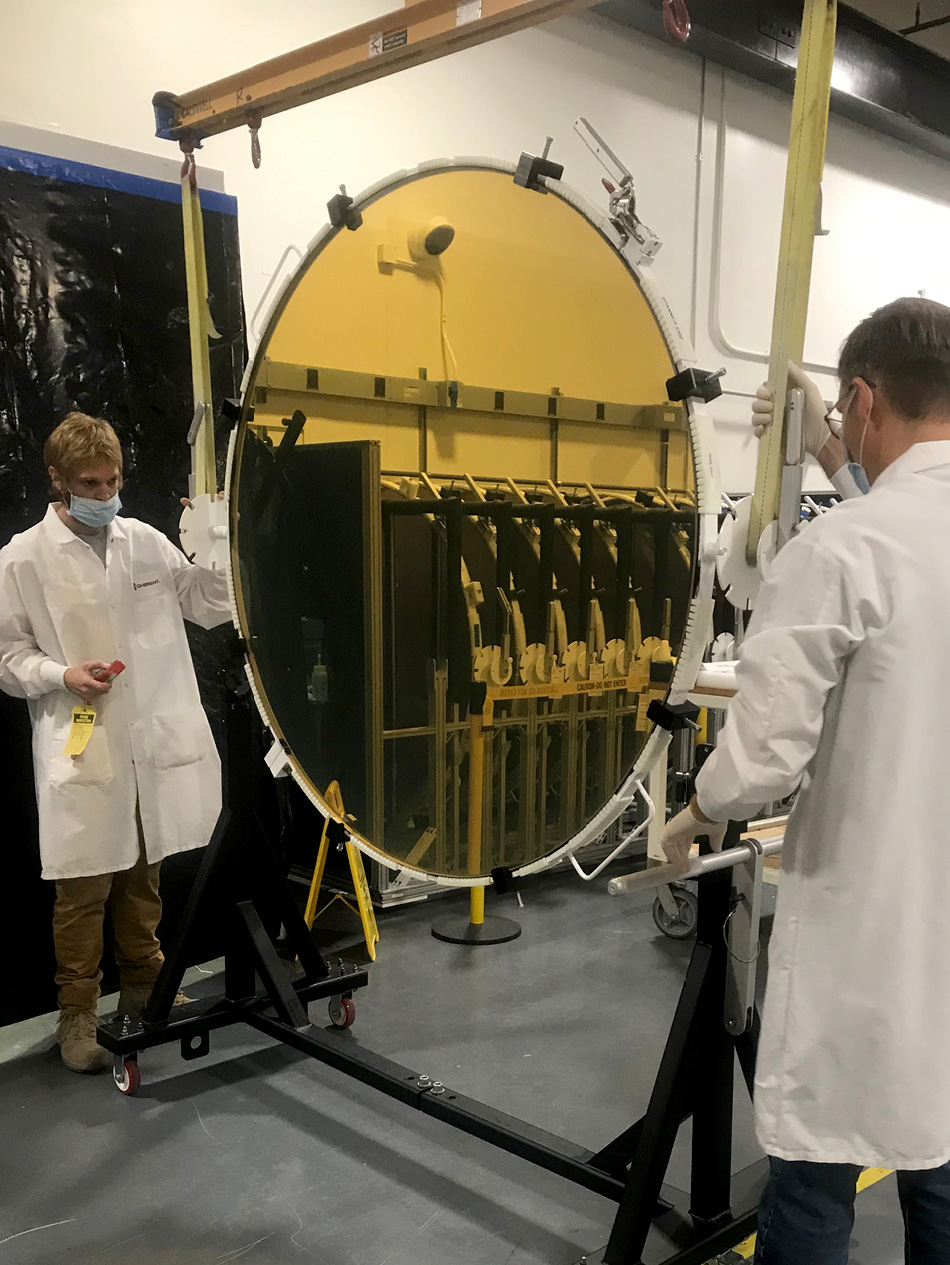
Coherent 制作的 230 个 TMT 圆镜面的直径均为 1.5 米,随后通过“六边形切割”,形成的各个角之间的距离为 1.44 米。
此时,镜子的侧面还增加了其他一些精密安装部件。具体来说,这些“传感器挖槽”用于传感器和执行器网络,实时定位镜面以保持优异图像质量。这将使地面 TMT 的空间分辨率高于天基仪器的红外空间分辨率。
加工玻璃
这种成形工艺在光学制造中很常见,通常使用传统铣床来执行,并且通常采用计算机数字控制 (CNC) 技术进行操作。然而,用于制作光学部件的各种玻璃材料非常脆,比金属更难加工。需要金刚石工具来完成加工。
金刚石机床已经使用了一个多世纪。这些机床表现很出色,在整个光学行业中得到广泛应用。但即使现代自动化技术使它们能够更快、更高效地工作,它们的速度仍然相对较慢。这有时会给从大型光学部件中去除大量材料造成困扰。
Coherent 高意(前身为 Tinsley Optical Systems)的工程师在对用于 TMT 的 230 个圆镜面进行六边形切割时,正是面临着这一限制。我们希望在未来几年内完成该计划。
这听起来似乎时间很充裕。事实并非如此!如果连续对每个圆镜面进行六边形切割(在一台机器上一个接一个地加工),那么使用传统铣削系统通常需要十年的时间才能完成如此多的六边形加工任务。
加快完成六边形切割
在过去的几年中,工具制造商开发出了采用先进超声波加工技术的系统。具体来说,除了采用标准高速刀具旋转技术之外,还涉及金刚石刀具沿其轴的小振幅、快速振荡(在数十 kHz 范围内)。
这项技术具有多项重要优势。首先,它比传统金刚石刀具铣削具有更高的材料去除率,高 6 到 10 倍不等。而且,由于超声波工具比传统工具对工件施加的力更小,所以它通常产生的机械应力也很小,从而避免了物理零件变形。因此,减少了亚表面损伤,带来更光滑的表面,并能够制作壁更薄的部件。
此外,力度小还可以减少工具磨损,延长工具使用寿命。而且,超声波刀具可“自我修整”。也就是说,在使用过程中,新鲜的金刚石颗粒会自动暴露在刀具上,从而保持刀具的切割力。通常,必须单独定期拆卸和修整刀具。刀具更换和维护频率较低,因而可缩短设备停机时间。
正是出于这些原因,大型高精度零件制造商(尤其是半导体行业)均已采用超声波辅助加工技术。但迄今为止,这项技术尚未应用于航空航天和天文学应用领域的大型光学元件。
准备使用超声波
Coherent 高意安装了足够大的超声波辅助加工系统来对 TMT 圆镜面进行六边形切割,成为率先使用超声波技术的公司。我们还开发出了一些非常专业的工具,用于在切割工艺中将光学部件固定在加工中心内。
这种工具至关重要,因为直径 1.5 米的圆镜面重 0.25 公吨(550 磅),但厚度仅为 45 mm。因此,固定它们时如果用力不对称或者局部用力,很容易导致其变形。这可能会造成切割后从夹具中松开零件时零件“弹起”,从而产生形变,导致加工部件不再符合规格。
因此有必要采用“零应力安装”方法。具体来说,采用这种安装方法可避免圆镜面表面变形,同时仍可确保光学部件在铣削工艺中牢固固定。
安装光学部件进行加工的常见方法是使用真空吸盘。但使用这种方法并不能实现自由形状(非对称和非球面)光学部件的零应力安装,获得所需的 TMT 圆镜面尺寸和精度。可能无法让安装表面的形状达到镜面所需的精度。
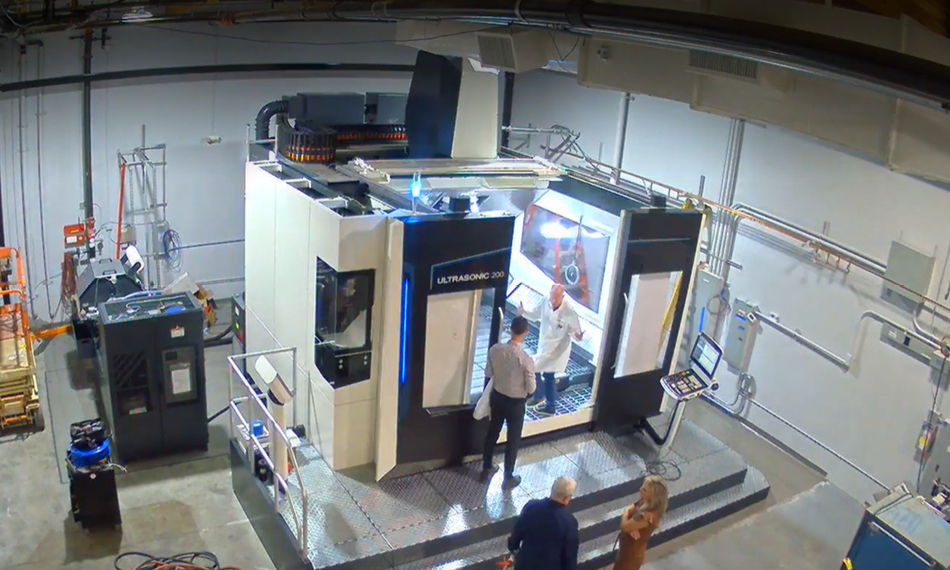
超声波辅助加工系统将会进行配置,以便对 Coherent 高意目前所制作的 230 个圆镜面进行精密的六边形切割。
相反,Coherent 高意工程师创建了一种专有的加工方法,该方法采用由支撑和夹紧系统构成的多技术网络。这些技术可以确保任何自由度下零件都不会产生任何弯曲。
为了保持圆镜面六边形切割所需的切割精度,还有一点至关重要,那就是整个加工中心必须建立在一个极其稳定的基础上。周围环境条件也必须保持恒定。但是,请记住,这台机床比皮卡车更大、更重。
因此,我们必须制造一个专门的设施来存放。首先需要浇筑一个新的混凝土安装垫,并用钢筋全面加固,以支撑机器的重量并提供所需的机械稳定性。另外,我们改进了整个制作区域的温度控制,以消除周围环境的任何变化。
点击此处详细了解六边形切割之前的圆镜面光学制造工艺。