EV向けレーザ加工の革新
Coherent ARMファイバーレーザとSmartWeld+は、従来のリモート溶接システムよりも優れており、きわめて要求の厳しいEVバッテリー製造の課題に対応できます。
2024年7月24日、Coherent
EV需要が高まる中、自動車メーカー各社は製造の精度をレベルアップするために競い合っています。
もちろん、自動車がどんどん複雑になり、洗練されるにつれて、ますます高い精度での製造が求められる傾向は、数十年前からありました。レーザはその変革の中で常に重要な役割を果たしてきました。今日、レーザは燃料噴射ノズルの、小さくて正確に成形された形の穴開け、高級合金鋼の溶接、自動変速機のギア溶接など、要求の厳しい処理で日常的に使用されています。
そうした処理の実行には多くの場合、新しい方法が必要でした。しかし、既存のレーザベースのシステムでは要件を満たすことができず、まったく新しいテクノロジーが必要になることもありました。
これは現在オンライン化されつつある、きわめて要求の厳しいEV製造作業の一部、特にバッテリーそのものの製造に関わる作業にまさに当てはまります。いくつかの工程において、きわめて薄く、熱に弱い材料を加工する必要があるためです。また、採算がとれるように、十分な速度と十分に高い歩留まりで実行できる処理でなくてはなりません。これまでは、そうしたニーズをすべて満たすレーザベースのツールがありませんでした。
Coherentは、非常に困難なEVバッテリー組み立て作業の要件を満たすために特別設計の新世代製品を開発した初のレーザサブシステムメーカーです。具体的には、CoherentのARMファイバーレーザとSmartWeld+加工ヘッドを使うと、パウチ型電池や角形電池の組み立てにおける重要な作業で製造工程数を削減でき、優れた成果を得られます。
フォイルからタブへの溶接
顕著な用途の例は、薄いアルミニウム箔と銅箔(電極スタック)をバッテリーの「タブ」に積み重ねることです。タブとは、電極材料からバッテリーの外側まで延びる導電端子です。
メーカーによってその処理方法はさまざまです。最も一般的な方法では、まず、貼り合わせた金属箔スタックを超音波溶接(通常、スタック溶接または予備溶接という)で仮留めします。 これによって金属箔が十分に固定され、その後の処理に耐えられる機械的安定性が得られます。しかし、これは組み立ての最終的な溶接ではありません。
次に、金属箔スタックのエッジを機械的な刃物でトリミングします。スタックのトリミングは、複数の重要な機能を果たします。トリミングをすることで、凹凸がなく寸法が正確な、均一なエッジになります。それによってバッテリーの組み立てが容易になり、一貫性が高まります。トリミングはエッジから酸化物などの汚れを除去し、その後の工程でもより良い結果をもたらします。
事前溶接とトリミングの後、フォイルスタックは、必要に応じて移動できるほど堅牢です。通常、次の工程では別のツールに移して、そこでタブに溶接します。さまざまなメーカーが、その工程では超音波溶接かレーザ溶接を用いています。
残念ながら、そのアプローチにはいくつか欠点があります。まず、超音波溶接は、必ずしも十分な強度の接合を生成するとは限らず、最も重要なことは、タブを完全に貫通する接合を生成することです。
超音波溶接では、使用できる箔の総数も制限されます。バッテリーのエネルギー貯蔵容量は金属箔の枚数が多いほど大きくなるため、これは無視できない点です。つまり、バッテリーメーカーにとっては、金属箔の枚数を自由に増やせるということが重要なのです。
また、超音波溶接には実用上の限界があります。超音波溶接に必要なツールは急速に摩耗するため、頻繁に交換する必要があるのです。つまり、製造のダウンタイムが多くなるということです。
金属箔とタブの接合においても、超音波溶接とレーザ溶接の両方に問題があります。この場合も、超音波溶接では溶け込みの深さに限界があるため、金属箔の枚数が限定されます。
金属箔とタブの溶接部で問題になるのは、割れや「マイクロネッキング」です。マイクロネッキングとは、金属箔が他より薄くなっている局所的な領域のことです。これは通常、溶接処理時に生じる引張応力が材料を引き伸ばすために発生します。金属箔には、この応力に応じて全体に均一に変形するほどの延性はありません。
マイクロネッキングは、機械的に弱いゾーンを材料にもたらし、その後さらに破断したり変形したりすることがあるため、深刻な問題です。また、金属箔の断面積が減少すると電気抵抗が増し、バッテリーの充放電特性が変わってしまう可能性があります。
革新的なアプローチ
この用途における超音波溶接と従来のファイバーレーザ溶接の限界を克服するには、プロセスにレーザ出力を供給する方法を高度に制御する必要があります。つまり、出力の分散を空間的に制御しながら、出力の経時的な変化も制御するのです。必要とされる制御のレベルは、元々自動車のボディやパワートレイン部品のようなもっと大きくて厚みのある部品の溶接用に設計された、従来のリモートレーザシステムで達成できるレベルを超えています。
このレベルの制御と精度を実現するために特別に設計されたのが、Coherent SmartWeld+です。Coherent SmartWeld+は、調整できるリングモードファイバーレーザと組み合わせたときに、その最大の可能性を発揮します。これは、SmartWeld+が幅広い「ビームウォブル」(高速振動)パターンを実装しているためで、レーザエネルギーを集光レーザスポットよりもはるかに広い範囲に分散させ、必要に応じて出力を空間的に変化させます。また、ARMビーム自体の出力分布も絶えず変化させることができるため、加工面にレーザエネルギーを堆積させる方法全体をさらに微調整できます。
この組み合わせのもう1つの大きな特徴は、高速であることです。SmartWeld+は、小型の低慣性ミラーを利用しています。このミラーは、視野範囲は狭いですが、従来のレーザ溶接ヘッドよりもはるかに速く(10倍程度)動きます。さらに、ARMレーザはセンタービームとリングビームをそれぞれ独立して高速変調させることができます。この変調は、スキャンミラーの動きと正確に同期させることもできます。その相乗効果で、レーザ出力の空間的・時間的な制御をこれまでになかったレベルまで引き上げました。
バッテリー溶接の改善
SmartWeld+の速度上の利点は、フォイルトゥタブ溶接に役立ち、溶接前作業とメイン溶接作業を1つのプロセスにまとめることができます。これを実現するには、Coherent ARM FLなどのシングルモードファイバーレーザと組み合わせることが一般的です。この用途では、スキャナの動きとレーザ出力変調の間の優れた同期が必要です。
Coherent Labsのアプリケーションチームは、ある角度から(直接頭上ではなく)スタックのエッジにレーザビームを集光させる革新的な特許取得済みのソリューションを開発しました。その後、SmartWeld+がビームを高速で振動させ、スタックとタブの厚み全体をカバーします。ARMビームの端から端までのレーザ出力と出力分布は、このビームの動きに同調して変化します。この方法が成功するかどうかは、スタックのエッジがどれだけ正確に切断されているかにかかっています。この前段階のスタック溶接作業の精度が重要である理由はここにあります。
溶接を斜めにすることがマイクロネッキングを回避する鍵だとわかっています。これは、SmartWeld+とARMファイバーレーザが、熱による応力を最小限に抑えながら、スタックに熱を加えることができるためです。その結果、マイクロネッキングの原因となる冷却時の金属箔の引っ張りがなくなります。
ARMビームの独立した変調は、溶接継手も強固にします。特に、溶接の「キーホール」を安定させるために必要な制御を実現することで、スパッタやポロシティを低減でき、欠陥の減少につながります。溶接継手自体の機械的強度が優れているため、導電率も良好になります。さらに、レーザ溶接では超音波溶接で問題となる金属粉が発生しません。
溶接品質の向上に加えて、実質的にあらゆる厚さのスタックに使用できることも、このエッジ溶接アプローチのメリットです。バッテリーメーカーは必要に応じて金属箔の枚数を増やし、セル容量を増やすことができます。
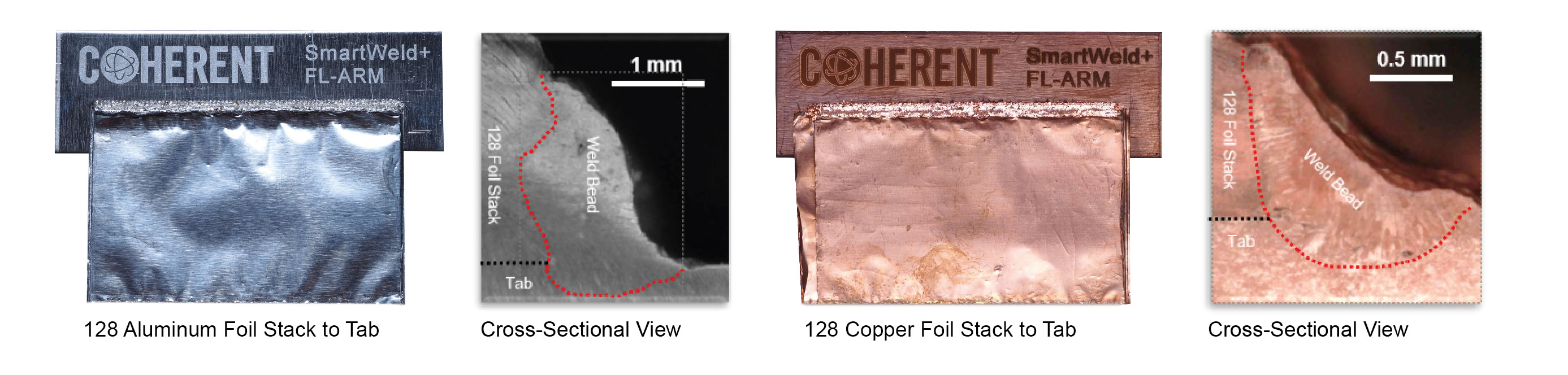
Coherent SmartWeld+とARMファイバーレーザは、マイクロネッキングとスパッタを抑え、伝導性が高い大きな溶接シームを作成します。
成功のためのパートナー
EV製造の課題への対応では、多くの場合、斬新で革新的なソリューションが求められます。これまで他の用途でうまく機能していた従来のツールは、その非常に要求の厳しいプロセスに求められる機能を備えていないことがあります。
成功の鍵は、まず、それぞれの用途で直面する特有の課題を理解することにあります。Coherentは、技術的専門知識を提供し、コミットメントを示して、メーカーと連携し、成功を左右する重要なパラメータを確認して、その特性を明らかにします。たとえば、バッテリーの金属箔とタブの溶接において、「マイクロネッキング」という現象は、当社がこの用途に取り組むまで業界で広く認識されていませんでした。Coherentのチームがそれを指摘し、解決策を見つけたのです。
Coherentのイノベーションを活用する方法についてご覧ください。