革新电动汽车激光加工
Coherent 高意 ARM 可调环模光纤激光器配备 SmartWeld+ ,超越传统远程焊接系统,克服电动汽车电池制造所面临的大难题。
2024 年 7 月 24 日,作者:Coherent 高意
随着消费者对电动汽车需求的增长,汽车制造商纷纷开始各显神通,力争快人一步达到更高水平的制造精度。
当然,由于汽车变得越来越复杂且精密,这种向更高精度制造发展的趋势已经存在了几十年。在这个转型历程中,激光发挥了关键作用。如今,激光通常被用于实现严苛要求的工艺,例如,在燃料喷射器喷嘴上钻出经过精确整形的小孔,或焊接高级钢合金,以及焊接自动变速箱齿轮等。
执行这些工艺往往需要新方法。但在某些情况下,现有的激光系统都无法满足要求,因此需要全新的技术。
如今出现的一些极其严苛的电动汽车制造任务正是如此,尤其是对于本身也参与电池制造的汽车制造商来说。这是因为制造过程的几个步骤需要加工非常薄的热敏材料。为了在经济上可行,这些加工必须以足够快的速度执行,还必须实现足够高的良品率。以往,没有激光工具能够满足所有这些需求。
Coherent 高意率先开发出了新一代激光子系统产品,专为满足严苛电动汽车电池组装操作的要求而设计。具体来说,在涉及组装袋型电池和方形电池的一些关键任务中,我们的 ARM 可调环模光纤激光器和 SmartWeld+ 加工头可减少生产步骤,并提供更好的加工效果。
箔片焊接
一个突出的应用示例是将薄铝箔和铜箔堆叠(电极堆叠)焊接到电池片上。极耳是导电端子,从电极材料伸出到电池外部。
每家制造商以不同的方式实施这些工艺。常用方法的第一步是,使用超声波焊接将组装好的箔堆固定在一起(通常称为成堆焊接或预焊)。这样可将箔片紧紧地固定在一起,使其具有足够的机械稳定性,以便进行后续处理。但这并不是整个组装过程的最后一道焊接。
接着,要使用机械刀片修整箔堆的边缘。这样的修整有多个重要作用。其中一个作用是,使边缘变得均匀,没有不规则和尺寸不精确问题。这样可实现更轻松且更一致的电池组装。修整还可去除边缘上的任何污染物(例如氧化物),从而在后续步骤中实现更好的加工效果。
预焊接和修整后,必要时箔片堆叠足够坚固,可以移动。通常,下一步是将箔堆转移到其他工具,以便将箔堆焊接到极耳。在这一步,很多制造商会使用超声波焊接或激光焊接。
然而,这种方法有一些缺点。首先,超声波焊接并不总是产生足够强的拉拔力,最重要的是,这种粘合会穿透电池片。
超声波焊接还限制了可以使用的箔片总数。这是一个大问题,因为使用的箔片越多,电池储能容量越大。因此,电池制造商必须能够自由地增加使用的箔片数量。
此外,超声波焊接有一些实际局限性。这种焊接所需的工具磨损得很快,需要频繁更换。这意味着生产停机。
超声波焊接和激光焊接都难以很好地将箔片与极耳焊接在一起。正如刚才所说,超声波焊接在熔深方面有局限性,继而限制了可用的箔片数量。
箔材焊接可能存在开裂和“微塌陷”现象。这种现象是指局部区域的箔片变薄。之所以会出现这种现象,通常是因为焊接过程中产生的拉伸应力拉伸了材料,但箔片的延展性不够高,无法在其整个宽度范围内均匀地变形以应对这种应力。
塌陷是一个严重问题,因为这种现象会在材料中产生机械强度较弱的区域,这样的区域随后可能会进一步破裂或变形。减小箔片的横截面积也会导致箔片的电阻增加,继而可能会改变电池的充电和放电特性。
一种创新的方法
要克服超声波焊接和传统光纤激光焊接在这些应用中的局限性,需要严格控制向工艺输送激光功率的方式——包括功率的空间分布方式以及功率随着时间的变化方式。所需的控制水平超过传统远程激光系统所要求的程度。传统远程激光系统主要用于焊接较大、较厚的部件,例如车身组件或动力总成组件。
Coherent SmartWeld+ 专为提供这种控制水平和精度而设计,与可调环模光纤激光器配合使用时效果更佳。这是因为 SmartWeld+ 实现了多种“光束摆动”(快速振荡)模式,可在比聚焦激光光斑大得多的区域内分布激光能量,而且功率可在空间上根据需要而变化。ARM 光束中的功率分布也可以发生很大变化,以进一步微调激光能量在工作表面上的总体沉积方式。
这种组合的另一大特点是速度快。SmartWeld+ 使用小型的低惯性反射镜。这些反射镜覆盖的视场较小,但移动速度比传统的激光焊接头快得多(高达 10 倍)。不仅如此,ARM 可调环模激光器可以快速调制,而且可以独立调制中心光束和环形光束。这种调制可以非常准确地与扫描镜运动同步。种种因素共同起作用,实现了对激光功率输送过程前所未有那么高水平的空间和时间控制。
改进电池焊接
SmartWeld+ 的速度优势可用于使箔对焊片焊接受益,使预焊接和主焊接操作能够组合到一个工艺中。为此,它通常与 Coherent ARM FL 等单模光纤激光器配对。该应用需要在扫描仪移动和激光器功率调制之间实现出色的同步。
Coherent 高意实验室应用团队开发了一种创新的专利解决方案,将激光束从一个角度(而不是直接架高)聚焦到堆叠边缘。然后,SmartWeld+ 会快速振荡光束,以覆盖箔堆和极耳的整个厚度。ARM 光束中的激光功率和功率总体分布会随着这种光束运动同步变化。这种方法的成功取决于箔堆边缘的切割准确度,因此,之前的成堆焊接操作的精度至关重要。
事实证明,以一定角度进行焊接是避免微塌陷问题的关键。其原因在于,这样使 SmartWeld+ 和 ARM 可调环模光纤激光器能够以热生应力极低的方式为箔堆加热。因此,箔片在冷却过程中不会出现拉伸情况——这种拉伸是导致微塌陷问题的原因。
ARM 光束的独立调制也有助于产生质量更好的焊缝。具体来说,这种调制可提供必要的控制来稳定焊接“匙孔”,从而减少飞溅和缺陷,并降低孔隙率。这样产生的焊缝本身具有出色的机械强度,这意味着良好的导电性。此外,激光焊接不会产生金属粉尘,超声波焊接则有这个问题。
除了改进焊接质量,边缘焊接方法的另一个优势是,它适用于几乎任何厚度的箔堆。这使电池制造商可以根据需要增加箔片数量来提高电池容量。
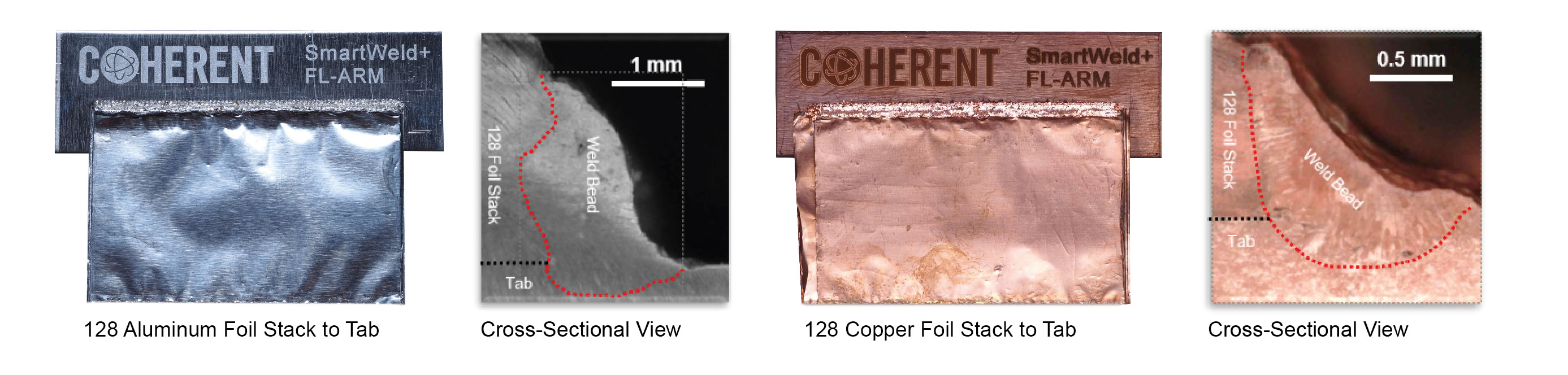
Coherent 高意的 SmartWeld+ 和 ARM 可调环模光纤激光器可消除微塌陷和飞溅问题,并产生高导热性大焊缝。
携手迈向成功
要克服电动汽车制造所面临的难题,通常需要新颖的创新解决方案。在其他应用中一直以来性能良好的传统工具有时并不具备这些高要求工艺所需的能力。
成功的关键在于了解每种应用所面临的独特挑战。Coherent 高意提供技术专业知识,并致力于与制造商携手合作,确定并概括决定成败的关键参数。例如,对于电池箔材焊接,在我们着手研究这种应用之前,业内甚至尚未广泛认识“微塌陷”现象。但我们的团队查明了这种现象,并开发出相应的解决方案。
了解利用 Coherent 高意的创新来助您一臂之力。