お客様事例
生産溶接のギャップを埋めるSmartWeld+
生産自動化を専門とするteamtechnikは、生産溶接システムの開発を請け負い、レーザの専門知識を持つCoherentに注目しました。 そして、顧客に継続的なサポートを提供するパートナーを得たのです。
teamtechnikは生産自動化を専門とし、製造、組み立て、テストに関して、手動から完全自動のターンキーシステムまで広範囲にわたるサービスを提供しています。 e-モビリティ業界を中心に、部品の取り扱い、各種テスト方法、接合プロセスなど、その専門性は非常に多岐にわたります。 2019年、teamtechnikは手持ち電動工具用のバッテリパックのメーカーから生産溶接システムの開発を依頼されました。
特に、teamtechnikは11種類の接続部の溶接に関する自動化ソリューションの提供を任され、 その中には、さまざまな材料を溶接するタスクが含まれていました。 多くの工程を短時間で開発する必要に迫られ、レーザ溶接に関する豊富なノウハウを社外に求めたteamtechnikは、Coherent Labsに支援を依頼しました。
よりスマートな溶接方法
Coherentチームに材料サンプルが提供され、 CoherentのSmartWeld+加工ヘッドと、1 kWのシングルモードファイバーレーザ(HighLight FL1000CSM)を組み合わせた一連のテストで、すぐに、これらの材料の加工が可能であることが実証されました。
SmartWeld+は、多彩な振動パターンを含む高度なビーム整形を組み込んだ特殊な溶接ツールです。 また、溶接時に照射されるレーザエネルギーの精密な制御ができます。 これにより、溶接シームの幅、深さ、溶け込みプロファイルの慎重な管理が可能になり、 熱に弱い材料や、銅とアルミニウムまたは鉄など、異種材料の組み合わせの溶接時に特に役立ちます。 さらに、反射性や発揮性の高い材料でも、スパッタ、空孔(ポロシティ)、ひび割れの発生を抑えて溶接することが可能です。
難易度が高い材料
SmartWeld+は、「難易度が高い」材料、つまり従来はレーザ溶接では対応できなかった材料の加工も可能にしました。 バッテリパックの構造に使用される材料の一部が、そのような材料に該当します。
たとえば、厚さ0.5 mmの亜鉛塗装銅片を厚さ1.0 mmのニッケル塗装銅に接合する溶接です。 亜鉛は融点が低く、従来のレーザ溶接では問題が生じていました。 特に、銅を溶かすために必要な温度に達すると、無秩序に泡立ってしまうため、 完成した溶接シームに空隙やポロシティが生じ、また、大量のスパッタが発生します。
この部品に関しては、両端を溶接する必要がありました。 しかし、一方の端は平らで、もう一方の端は90度に曲がっており、 この条件の違いのために各溶接を最適化するには別個のパラメータセットを開発する必要が出てきました。 さらに、部品には、溶接時に加熱してはいけないプラスチック片が埋め込まれていました。
この部品には、溶接の正確な形状を調整できるSmartWeld+の機能が非常に役立ちました。 その機能により、プラスチック片に近づきすぎることなく、必要なレベルの電気接続と機械的強度を提供するのに十分なサイズの接合部を作成することに成功しました。 部品の両端で似たような溶接経路を使用しますが、適用される方向は異なります。 teamtechnik PolandとCoherentの開発チームは、片方の溶接部について、部品間のギャップが小さい場合に最適な溶接結果が得られることを発見しました。
どちらの溶接でも、解決策の鍵となったのはダイナミック出力変調でした。 これにより、溶接中の溶融プールを安定させ、ポロシティを除去することに成功し、 スパッタも大幅に削減されました。
加工のばらつきへの対応
また、厚さ0.3 mmのSIGMACLAD®片2枚の溶接タスクもありました。 SIGMACLADは、パック内のリチウムイオンバッテリの電気接続を行うために特別に設計された複合材料です。 Ni|ステンレス|Cu|ステンレス|Niからなる5層サンドイッチ構造になっています。 この構造により、各金属を個体で使用するよりも望ましい特性が享受できます。 具体的には、銅が優れた電気伝導性と熱伝導性(放熱性)を提供し、ステンレス層が材料の溶接を容易にして溶接部の強度を高めます。 また、外側のニッケル層は、はんだ付けを容易にし、優れた耐食性をもたらします。
SIGMACLADはレーザ溶接との互換性を考慮して特別に設計されているため、teamtechnik、Coherentの開発チームはともに、この接合が大きな課題になるとは予想していませんでした。 しかし実際には、材料の厚さの違い、個々の層の厚さの違い、および部品全体の寸法公差の低さのために加工にばらつきが生まれ、一貫性を持った適合が難しいことが分かりました。 テストの結果、溶接の成功率100 %を達成するには、2つの部品間の隙間を0.05 mm未満に保つために固定する必要があることが判明しました。
この場合の溶接部全体は1 mm x 2.5 mmです。 集束レーザ光は溶接部全体よりもはるかに小さいため、SmartWeld+は各スキャン間で垂直方向にわずかにステップしながらビームを数回前後に往復させ、領域全体をカバーします。 さらに、移動中にレーザを変調する必要があることもテストから判明し、変調がない場合はスキャンの端に過剰なスパッタが発生することも分かりました。
また、エンドユーザーの施設に機器を設置し、試運転をした後に調整されたプロセスもありましたが、 Coherentアプリケーショングループは、これらの問題について、継続的にサポートを行いました。
たとえば、1つの溶接では厚さ0.3 mmのSIGMACLADが、厚さ1.0 mmのニッケル塗装銅に接合されています。 この問題は、機器が設置され、エンドユーザーが2年間にわたり機器を正常に動作させた後で発生しました。 その後、材料サプライヤーによる配合の変更や、銅の清浄度によっても問題が生じました。 当初は問題なく採用されていた加工方法レシピを使用しても、相当量のスパッタが発生するようになったのです。
しかし、SmartWeld+の柔軟性が、この問題では特にその価値を発揮しました。 特に、治具のハードウェアを変更することなく、ソフトウェア制御を通じて溶接パラメータを容易に変更できる機能が光りました。 Coherentは新しいテストサイクルを行い、この工程にレーザ出力変調を実装すると問題が解決することを確立しました。
成功のためのパートナー
Coherent開発チームと提携することで、teamtechnikは、得意分野である自動化に集中することができました。 「顧客から与えられた時間とコストの制約内ですべてのレーザ溶接プロセスを開発するには、パートナーが必要でした」と、teamtechnik POLANDの溶接技術スペシャリストであるマチェイ・ザボロウスキ氏は話します。 「特に、材料をテストしてすべてにレーザ溶接が使えるかを判断し、生産に耐えうる特定の加工方法レシピを開発するための専門知識と設備を備えた企業を見つけたいと考えていました」
「Coherentはこれらすべての点で期待に応えてくれました。 しかも、私たちの提携は、この初期プロセス開発だけにとどまりませんでした。 材料に変更があり、それまで順調に機能していた工程に生産上のばらつきが生じた場合も、Coherentのサポートは継続しました。 このようなレベルで、プロセスへの責任を引き受けてくれるレーザベンダーは他にはいません」
「SmartWeld+は素晴らしい結果をもたらし、工程の変更にもフレキシブルに適応します。 しかし、私たちがCoherentを選んだ本当の理由は、そのサポート力です。 エンドユーザーの要件を確実に満たすために必要な開発作業を行ってくれるサプライヤーは、彼らをおいて他にはいませんでした」
— teamtechnik POLAND 溶接技術スペシャリスト、マチェイ・ザボロウスキ
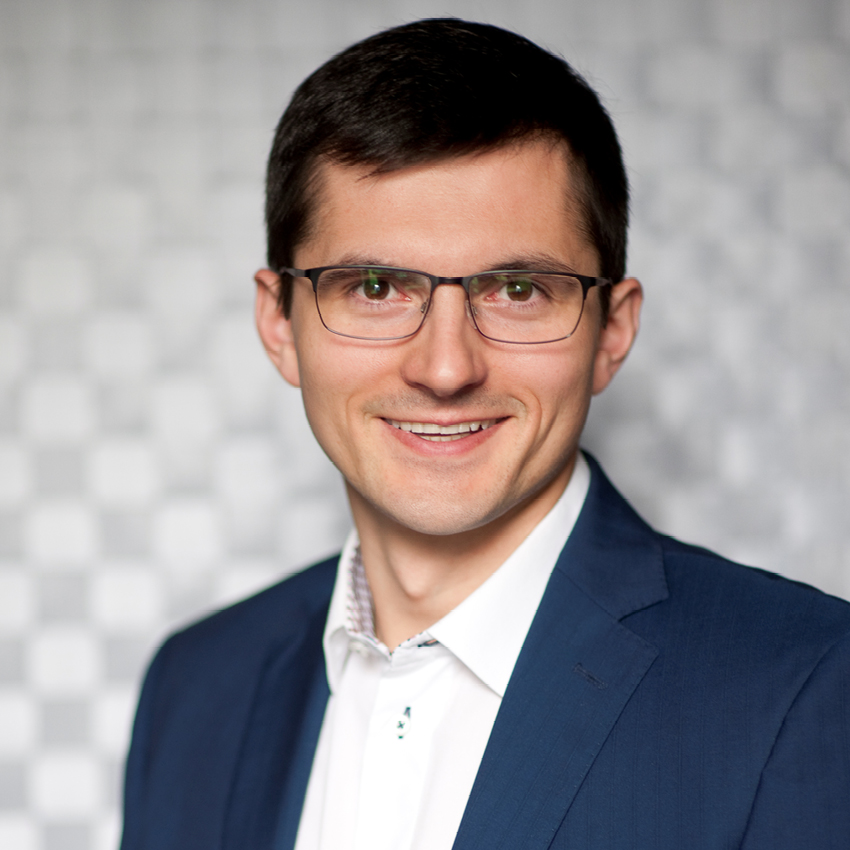
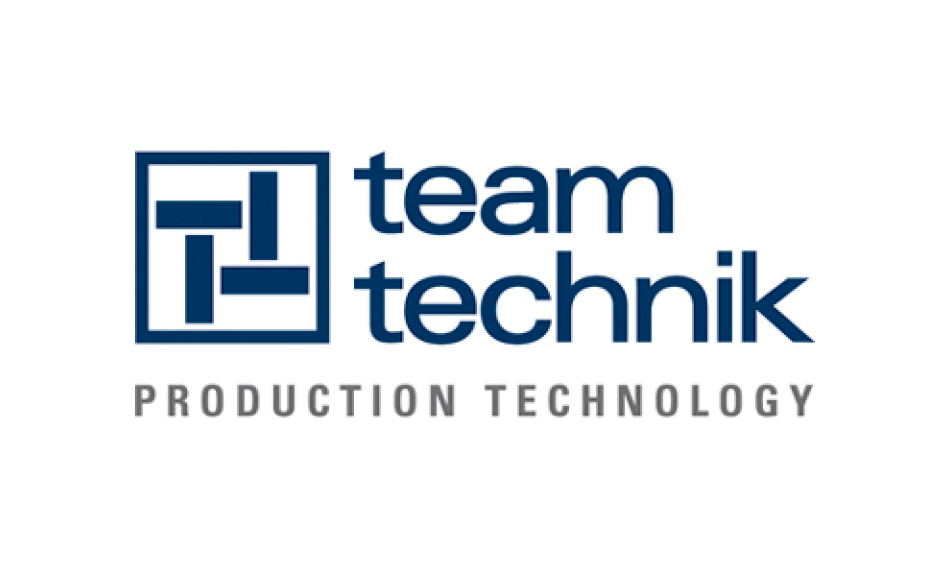
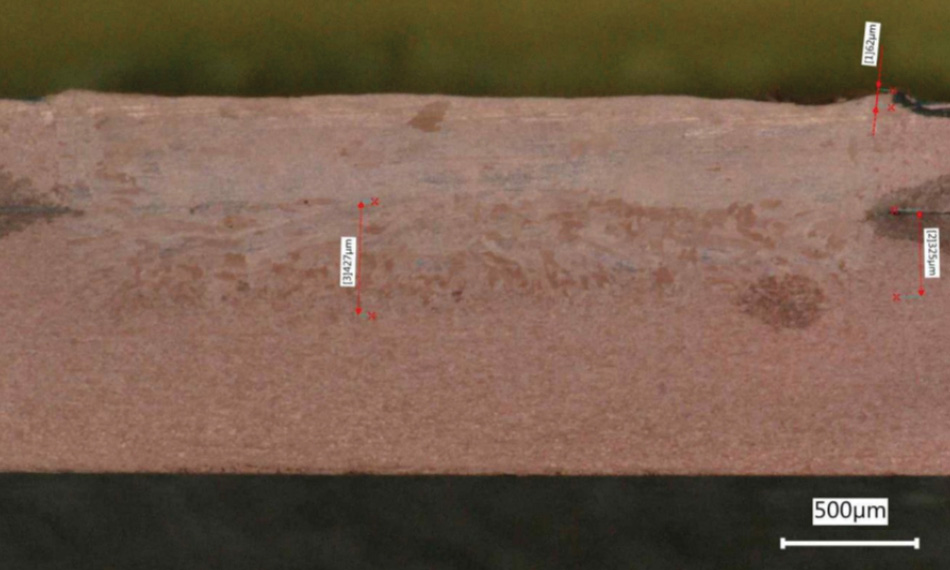
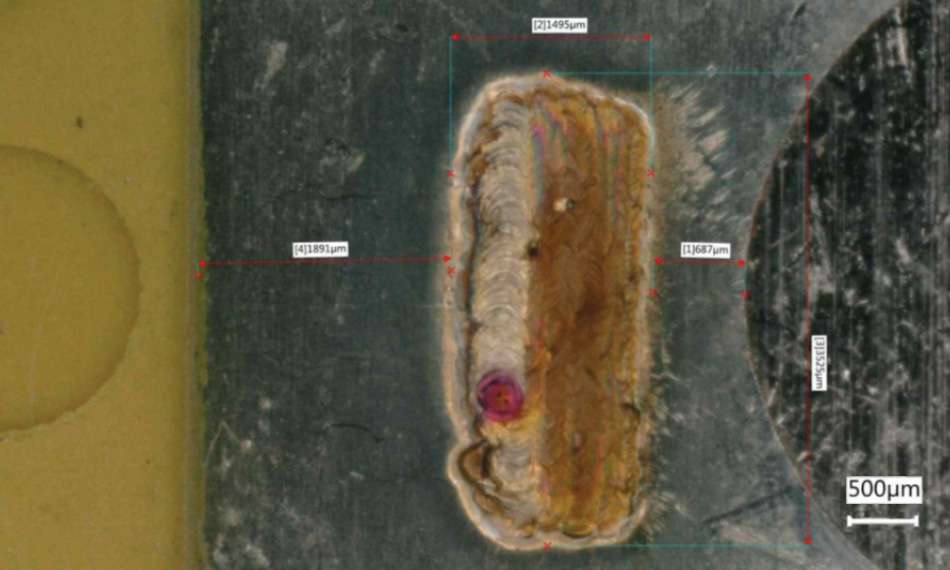
図1. 0.5 mm亜鉛塗装銅と1.0 mmニッケル塗装銅溶接の断面図と平面図。
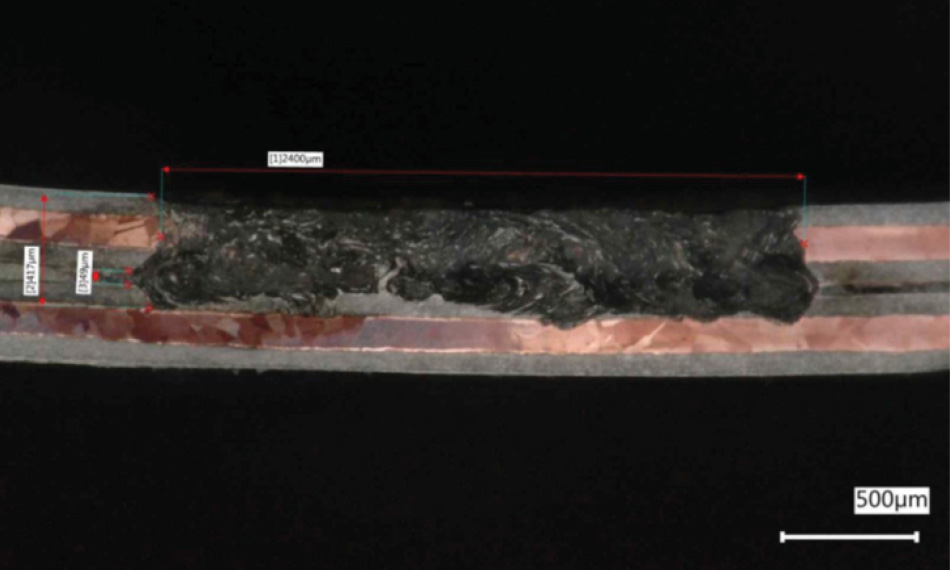
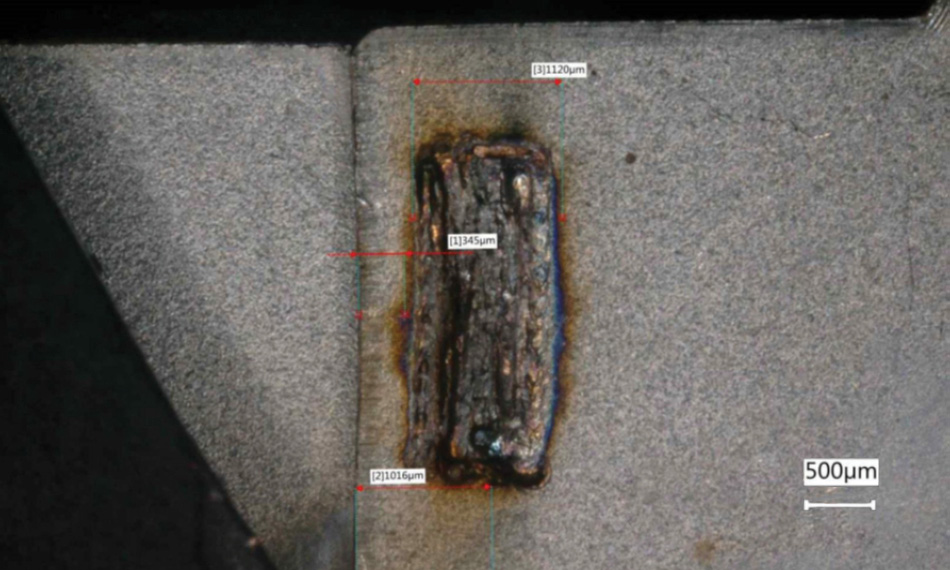
図2. 3 mm SIGMACLADと3 mm SIGMACLAD溶接の断面図と平面図。
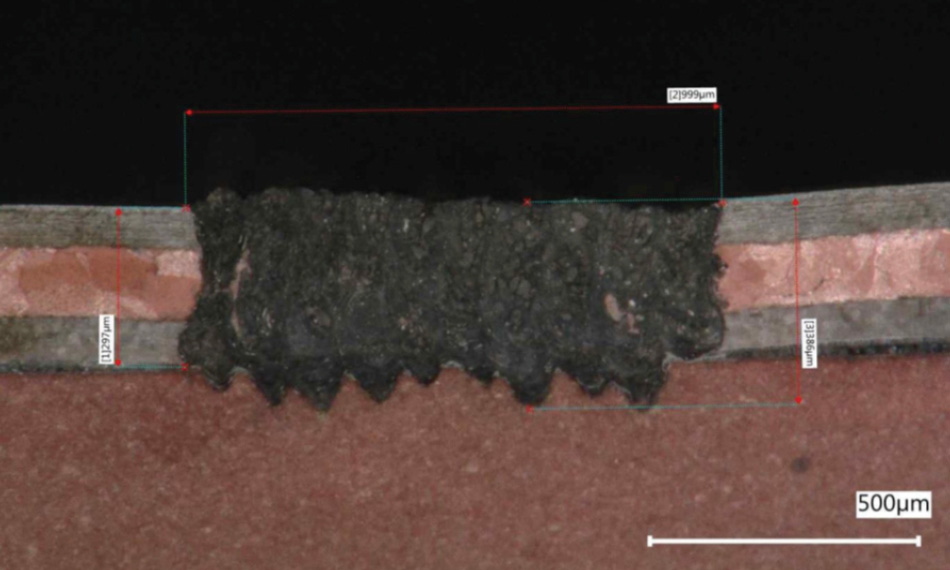
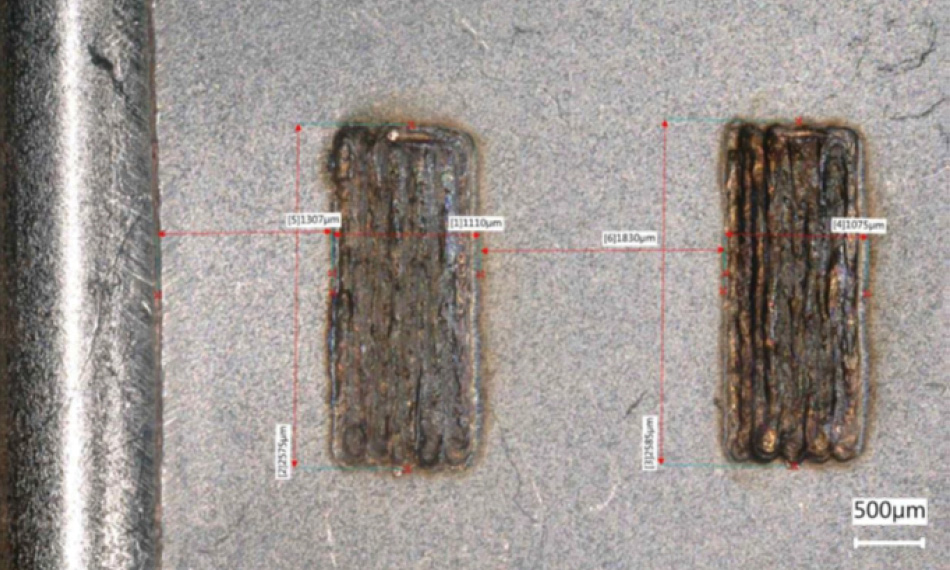
図3. 3 mm SIGMACLADと1.0 mmニッケル塗装銅溶接の断面図と平面図。