より良い熱管理による半導体パッケージングの改善
SiCなどの先端材料は、今日の薄型マイクロエレクトロニクスコンポーネントに必要な新しいアセンブリ方法を可能にします。
2023年12月20日、Coherent
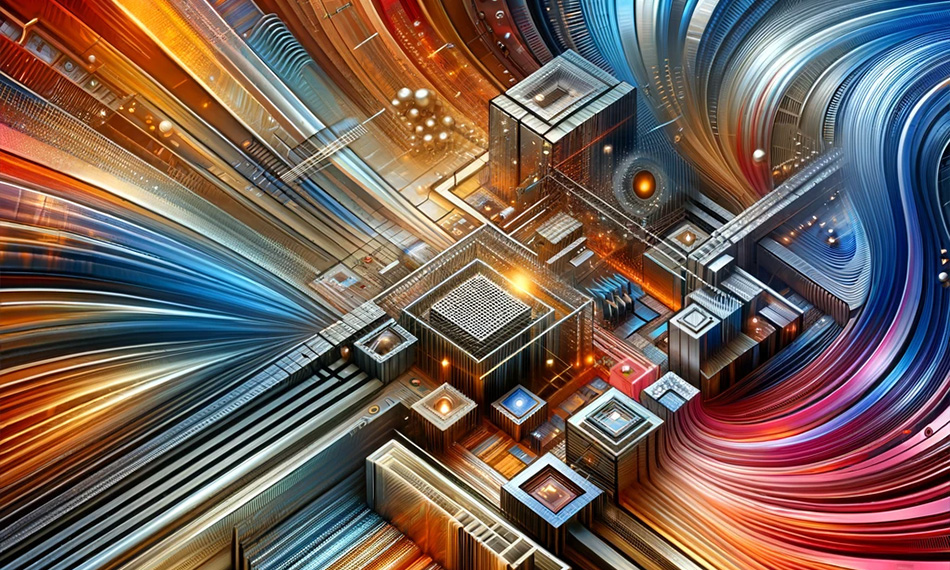
マイクロ回路の微細化に伴い、より小さく、より薄い回路に対応してより高い精度を実現するために、その製造に使用されるすべての加工方法を再設計または置き換える必要があります。これは特に「先端パッケージング」において顕著で、個々の集積回路(「ダイ」と呼ばれる)を基板または回路基板にマウントし、電気的に接続してその後封入する製造工程です。
フリップチップの基本
広く採用されている先端パッケージング技術の1つは「フリップチップ」と呼ばれます。この方法は、ワイヤボンディングなどの古い方法に比べていくつかの利点があるため、過去10年間で広く採用されるようになりました。これらの利点には、コストの削減、パッケージングの高密度化、信頼性の向上などがあります。
フリップチップ用の回路を準備するには、まず半導体ウエハの上面にある導電性パッドに、導電性材料(一般的には、はんだや金)の小さなバンプを堆積させます。その後、ウエハは個々のチップに切断されます(ダイシンギュレーションと呼ばれます)。
次に、個々のダイをピックアップし、接触面が下を向くように回転させ、マウントする基板上に配置します。この基板は、最も一般的にはプリント基板です。チップは、チップ上のバンプが基板上の対応する導電性パッド(上向き)と一致するように、非常に正確に位置合わせされます。チップバンプを基板パッドに接触させます。
その後、このアセンブリをオーブンに入れて、はんだ(またはバンプを構成する材料)の融点以上に加熱します。はんだは溶けて「リフロー」し、ダイと基板の両方の導電性パッドに張り付きます。最後にオーブンが冷えてはんだが凝固し、チップと基板の間に電気的および機械的結合が形成されます。
サーマルコンプレッションボンディング – 薄型ダイのソリューション
フリップチップ加工方法は、ICと基板の両方が薄くなり、はんだバンプのサイズと間隔(ピッチと呼ばれる)が100 μm未満になると問題に直面し始めます。具体的には、加熱サイクルによってICや基板に反りが生じる可能性があります。これは、加熱サイクル中のコンポーネント間の温度勾配や、さまざまな部品間の熱膨張係数(CTE)の不一致が原因で発生します。
部品の反りがかなり大きい場合、ダイと基板の間に位置ずれが生じることがあります。その結果、開回路(無接続)、または場合によっては回路の短絡(はんだボールのブリッジ)が発生することがあります。
サーモコンプレッションボンディング(TCB:Thermo-Compression Bonding)は、フリップチップの機能を拡張するために特別に開発された技術です。具体的には、TCBは薄型ダイの大量チップマウントをより確実に行う方法です。
従来のフリップチップボンディングとTCBの違いは、TCBでは全作業中にダイと基板の温度、加える力、位置、向きを極めて高い精度で能動的に監視および制御することです。加工方法の各段階は、次の段階に進む前に検証されます。このすべての制御により、より優れた、信頼性の高い結合が実現し、ユニット間の一貫性が向上します。
これらを実現するために採用されたTCBシステムの主要な要素を図に示します。これには、1 μmの精度でダイを垂直に位置決めすることができる空気ベアリング軸のリニアサーボモーターが含まれます。また、チップとダイの共平面性を維持するための角度位置決め用のチップチルトステージもあります。ヒーターとクーラーはともにダイの温度とその温度の上昇速度または下降速度を正確に制御します。コンポーネントのこのスタックの底部は、ダイ自体を保持する真空チャックまたはノズルです。また、ダイと基板の温度、加える力、位置と幾何学的配置を連続的に監視する一連のセンサーが組み込まれています。
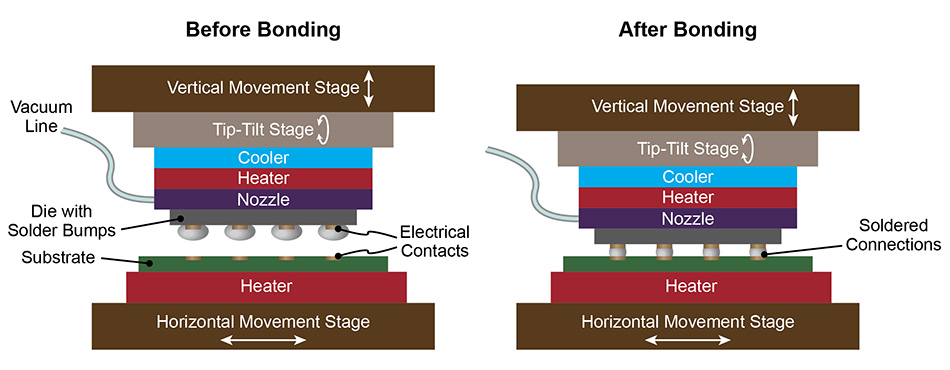
サーマルコンプレッションボンディングシステムには、ダイと基板を位置決めして向きを設定するステージ、温度を制御するヒーターとクーラー、ダイを保持する真空ノズル、加工方法を監視および制御する各種変換器やビジョンシステム(非表示)が含まれます。
TCB加工方法は、従来のフリップチップと同じように始まります。つまり、はんだバンプを備えたダイを準備します。次に、ダイをピックアップして基板と位置合わせし、バンプが基板に接触するまで降ろします。この後、加熱とダイの移動サイクルが始まります。
はんだが溶けるにつれて、ダイは最初に基板に向かって移動し、次に基板からわずかに遠ざかり、最後に再び基板に向かって戻ります。また、温度や加える力も変化させます。これにより、ダイと基板間の良好なアライメントと接合、均一なはんだ接合高さ、欠陥のない接続が確保されます。
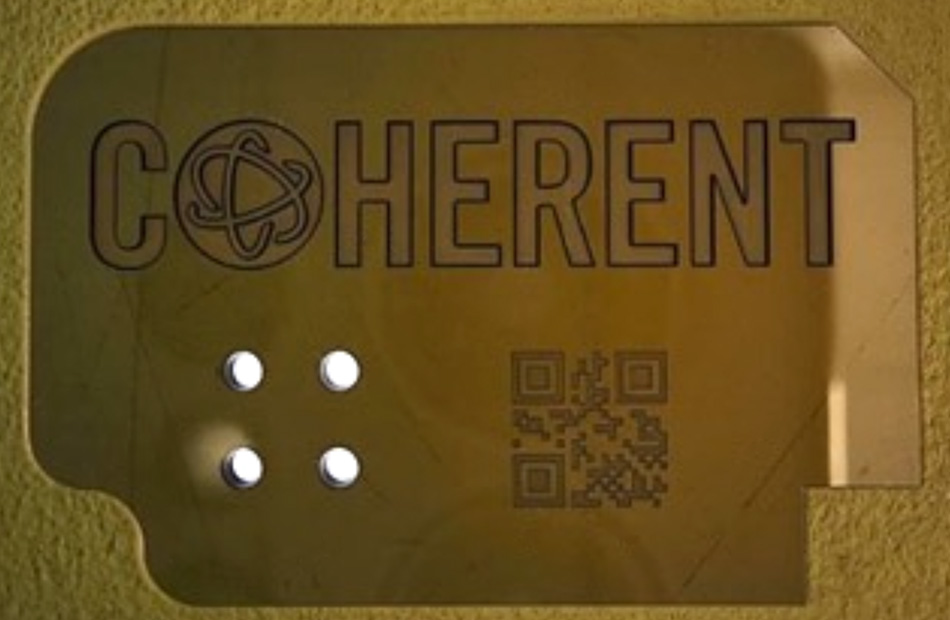
Coherentは、TCBノズルの材料と完成したコンポーネントの垂直統合メーカーです。当社は、表に示す4H SiC部品のように、さまざまなサイズや形状、内部構造を持つノズルを製造できます。
ノズル向けの先端材料
ステージ、熱デバイス、センサーに加えて、TCBシステムのもう1つの重要な要素はノズルです。これは3つの重要な機能を果たします。まず、真空チャックとして機能するように、エアフロー用のさまざまな孔やチャネルがあります。第二に、加工方法全体でダイの平坦性を維持することができます(真空によって部品がその表面に対して確実に保持されるため)。最後に、TCBシステムの加熱および冷却エレメントが熱を伝導してダイの温度を変化させます。
これらの要件を満たすために、理想的なノズルは、非常に滑らかで平坦な部品を製造できる、機械的に剛性の高い材料から製造される必要があります。これは、ダイにかかる力が変化しても、加工方法全体でダイをしっかりと保持し、平らな状態を保つために必要です。
さらに、ノズル材料は高い熱伝導率を備えている必要があります。これにより、ヒーターとクーラーによって発生した温度変化がダイに迅速に伝わります。ダイの温度を正確に制御し、素早く熱サイクルを行う能力は、加工方法の成功と、全体のタクトタイムの最小化の鍵となります。
これらの条件をすべて満たす材料はほとんどありませんが、Coherentは3種類の材料を製造しており、どの材料からでもTCBノズルの完成品を製造することができます。これらの材料は、反応結合炭化ケイ素(SiC)、単結晶SiC、多結晶ダイヤモンドです。それぞれの特徴や利点を表にまとめています。
材料 |
熱伝導率 |
表面粗さ |
光透過性 |
電気絶縁体 |
コスト |
反応結合SiC |
255 W/m-K |
<25 nm |
X |
X |
低 |
単結晶SiC |
370 W/m-K |
<2 nm |
はい |
4H:X 6H:はい |
中 |
多結晶ダイヤモンド |
2200 W/m-K |
<10 nm |
はい |
はい |
高 |
これらの材料はすべて、他の物質と比較して高い熱伝導性を備えており、ダイヤモンドはあらゆる材料の中で最も高い熱伝導性を備えています。反応結合SiCの重要な特徴の1つは、必要な貫通孔や内部チャネルを容易に製造できることです。また、レーザ加工により、非常に高い平坦度と低い表面粗さを実現することができます。
ダイヤモンドと単結晶SiCの利点は、いずれも可視光と近赤外線を透過することです。これにより、最終部品の平面度、厚さ、平行度の測定に幅広い測定技術を使用できるようになり、より高い精度の製造を行うことができます。
多結晶ダイヤモンドと6H単結晶SiCは電気絶縁体です。この特性は、静電気放電(ESD)による損傷から半導体ダイを保護するなど、いくつかの理由で役立ちます。
これら3つの材料から製造されたノズルのコストにも違いがあります。ノズルは定期的に交換される消耗品であるため、これは重要です。
Coherentは、TCBノズルの垂直統合メーカーです。当社は独自の材料を製造することから始め、完成部品の製造まですべてを行っています。当社の製造能力の重要な要素は、非常に平坦な表面を製造する能力であり、この平坦度を検証するための広範な計測機器を備えています。
Coherentの反応結合炭化ケイ素(SiC)、単結晶SiC、多結晶ダイヤモンドの詳細をご覧ください。