Besseres Wärmemanagement verbessert das Halbleiter-Packaging
Hochentwickelte Materialien wie SiC ermöglichen verbesserte Fertigungsverfahren, wie sie für die dünneren Mikrolektronikbauteile von heute erforderlich sind.
20. Dezember 2023 von Coherent
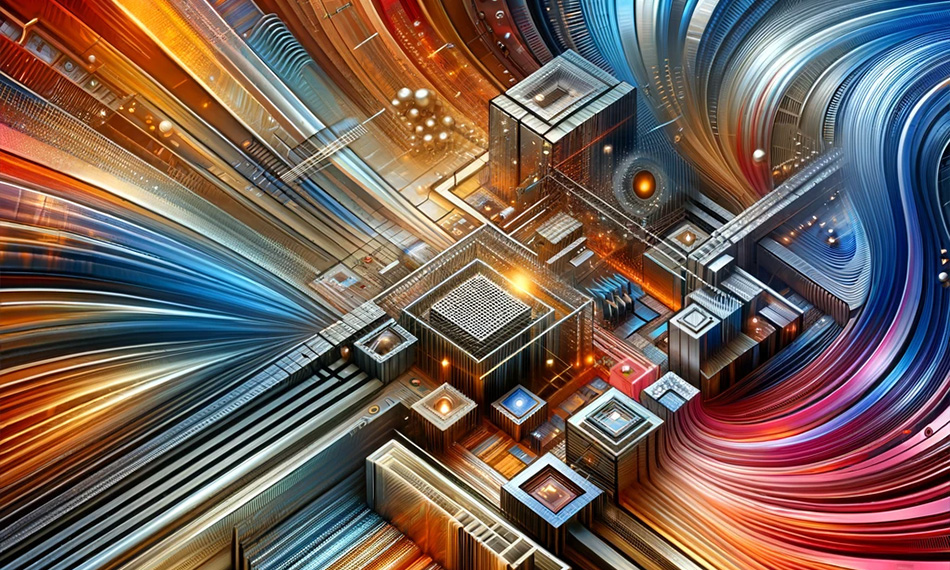
Die Mikroschaltkreise werden zunehmend kleiner. Um mit kleineren, dünneren Schaltkreisen arbeiten zu können und eine höhere Präzision zu erzielen, müssen deshalb alle in der Herstellung verwendeten Prozesse umgerüstet oder ersetzt werden. Dies gilt insbesondere für das „Advanced Packaging“. Dies ist ein Produktionsschritt, bei dem einzelne integrierte Schaltkreise (genannt „Dies”) montiert und elektrisch mit dem Substrat oder der Leiterplatte verbunden und anschließend eingeschlossen werden.
Flip-Chip-Grundlagen
Eine weit verbreitete hochentwickelte Packaging-Technologie ist „Flip-Chip“. Diese Methode wurde in den letzten zehn Jahren zunehmend beliebter, da sie gegenüber älteren Methoden wie dem Drahtbonden mehrere Vorteile bietet. Zu diesen Vorteilen zählen niedrigere Kosten, die höhere Packungsdichte und die erhöhte Zuverlässigkeit.
Um Schaltkreise für Flip-Chip vorzubereiten, werden zunächst kleine Höcker aus leitendem Material – typischerweise Lot oder Gold – auf leitenden Pads auf der Oberseite des Halbleiterwafers aufgebracht. Anschließend wird der Wafer in einzelne Chips zerschnitten (genannt „Die-Vereinzelung”).
Als nächstes wird ein einzelner Die aufgenommen, so gedreht, dass die Kontaktseite nach unten zeigt, und dann über dem Substrat positioniert, auf dem er montiert werden soll. Bei diesem Substrat handelt es sich in der Regel um eine Leiterplatte. Der Chip ist sehr präzise ausgerichtet, sodass die Höcker auf dem Chip mit den entsprechenden leitfähigen Pads auf dem Substrat (die nach oben zeigen) übereinstimmen. Die Chip-Höcker werden mit den Substratpads in Kontakt gebracht.
Diese Baugruppe wird dann in einen Ofen gegeben, wo sie über den Schmelzpunkt des Höckermaterials (Lot oder anderes Material) erhitzt wird. Das Lot schmilzt, fließt zurück und bleibt an den leitfähigen Pads auf dem Chip und dem Substrat haften. Mit dem Abkühlen des Ofens verfestigt sich das Höckermaterial und bildet sowohl elektrische als auch mechanische Verbindungen zwischen dem Chip und dem Substrat.
Thermisches Kompressionsbonden – die Lösung für dünne Dies
Der Flip-Chip-Prozess stößt an Grenzen, da sowohl die Schaltkreise als auch die Substrate dünner werden und sobald die Größe der Löthöcker und der Abstand zwischen ihnen (genannt „Pitch”) auf unter 100 µm sinken. Insbesondere kann der Erwärmungszyklus zur Verformung von Schaltkreis und Substrat führen. Dies kann aufgrund von Temperaturgradienten zwischen diesen Komponenten während des Erwärmungszyklus und aufgrund unterschiedlicher Wärmeausdehnungskoeffizienten der Teile auftreten.
Wenn die Verformung des Teils erheblich genug ist, kann es zur Fehlausrichtung von Chip zu Substrat kommen. Dies kann zu offenen Schaltkreisen (keine Verbindung) oder in manchen Fällen sogar zu Kurzschlüssen (Lötkugelbrücken) führen.).
Das Thermo-Compression Bonding (TCB) ist eine Technologie, die speziell die Fähigkeiten von Flip-Chip erweitert. Insbesondere kann TCB zuverlässiger Dies in großer Stückzahl an Chips befestigen.
Der Unterschied zwischen herkömmlichem Flip-Chip-Bonden und TCB besteht darin, dass letzteres die Temperatur, die ausgeübte Kraft, die Position und die Ausrichtung von Chip zu Substrat während des gesamten Vorgangs aktiv und mit äußerst hoher Präzision überwacht und steuert. Das Ergebnis jeden Prozessschritts wird überprüft, bevor der nächste eingeleitet wird. All diese Kontrollen führen zu besseren, zuverlässigeren Verbindungen und einer größeren Konsistenz von Einheit zu Einheit.
Die Hauptelemente des TCB-Systems, mit dem all dies erreicht wird, sind in der Zeichnung dargestellt. Dazu gehören lineare Servomotoren auf luftgelagerten Achsen, die den Die mit einer Genauigkeit von 1 µm vertikal positionieren können. Weiterhin wird in einem Tip-Tilt-Schritt die Winkelpositionierung durchgeführt, um die Koplanarität von Chip und Die aufrechtzuerhalten. Sowohl eine Heizeinheit als auch eine Kühleinheit steuern präzise die Temperatur des Die und die Geschwindigkeit, mit der die Temperatur zunimmt oder abnimmt. Die Unterseite dieses Komponentenstapels ist ein Vakuumspannfutter oder eine Düse, die den Die selbst hält. Eine Reihe eingebetteter Sensoren überwacht während des gesamten Vorgangs kontinuierlich die Temperatur, die ausgeübte Kraft sowie die Position und die Ausrichtung des Die auf das Substrat.
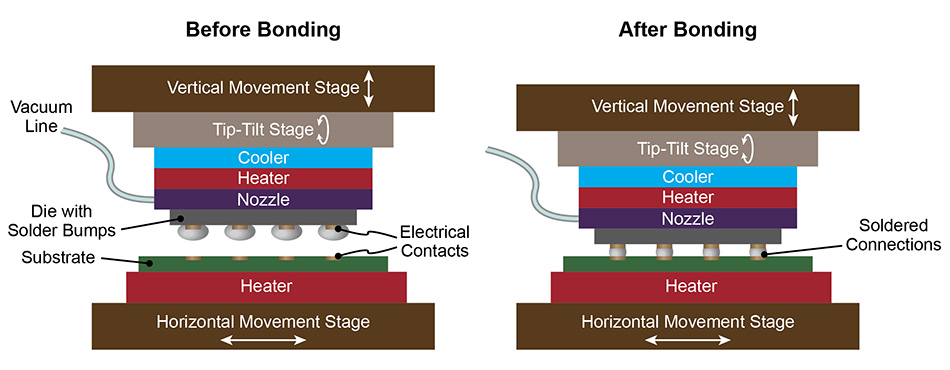
Zu einem System für das Thermokompressionsbonden zählen die Prozessstufe des Positionieren und Ausrichten des Die am Substrat, Heiz- und Kühlelemente zum Steuern der Temperatur, eine Unterdruckdüse zum Halten des Die sowie diverse Transducer und Optiksysteme (nicht dargestellt zum Überwachen und Steuern des Prozesses.
Der TCB-Prozess beginnt auf die gleiche Weise wie das herkömmliche Flip-Chip. Es wird nämlich ein Die mit Löthöckern vorbereitet. Dann wird der Die aufgenommen, am Substrat ausgerichtet und nach unten gefahren, bis die Höcker in Kontakt mit dem Substrat treten. Danach beginnt für den Die der Zyklus des Erwärmens und Verfahrens.
Das Lot schmilzt und dabei wird der Die zunächst in Richtung Substrat verfahren, dann leicht von diesem weg und schließlich wieder hin zum Substrat verfahren. Auch die Temperatur und die ausgeübte Kraft werden dabei variiert. Alle diese Schritte sorgen für die gute Ausrichtung und Verbindung von Die und Substrat, die gleichmäßige Höhe der Lötstellen und eine fehlerfreie Verbindung.
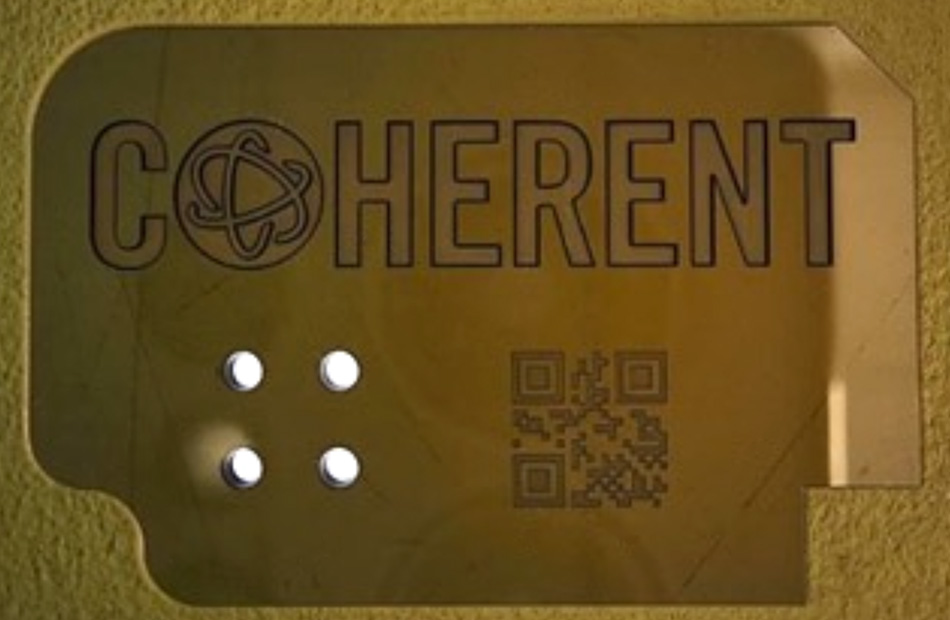
Coherent ist ein vertikal integrierter Hersteller von Materialien und Endkomponenten für TCB-Düsen. Wir fertigen Düsen diverser Größen und Formen sowie mit internen Merkmalen wie diese 4H SiC-Komponente.
Hochentwickelte Materialien für Düsen
Neben den Prozessstufen, den thermischen Geräten und Sensoren des TCB-Systems ist die Düse ein weiteres kritisches Element. Sie erfüllt drei Schlüsselaufgaben. Sie enthält erstens diverse Öffnungen oder Kanäle für den Luftstrom, die es ihr ermöglichen, als Vakuumspannfutter zu dienen. Zweitens erhält sie während des gesamten Prozesses die Ebenheit des Die (da das Vakuum das Teil sicher an der Oberfläche hält). Schließlich leitet sie die Wärme, damit die Heiz- und Kühlelemente des TCB-Systems die Temperatur des Die variieren können.
Um diese Vorgaben zu erfüllen, muss die ideale Düse aus einem mechanisch steifen Material gefertigt sein, das sowohl zu sehr glatten als auch sehr flachen Teilen verarbeitet werden kann. Dies ist erforderlich, um den Die auch bei sich ändernden einwirkenden Kräften während des gesamten Prozesses fest und flach zu halten.
Darüber hinaus muss das Düsenmaterial sehr wärmeleitfähig sein. Dies stellt sicher, dass durch die Heiz- und Kühleinheit ausgelösten Temperaturänderungen schnell auf den Die übertragen werden. Der Schlüssel zum Prozesserfolg und zur Minimierung der Gesamttaktzeit ist die Fähigkeit, die Temperatur des Die präzise steuern zu können und sie zyklisch schnell anpassen zu können.
Nur sehr wenige Materialien erfüllen alle diese Vorgaben, aber Coherent produziert drei davon her und stellt aus diesen einsatzbereite TCB-Düsen her. Diese Materialien sind: reaktionsgebundenes Siliziumkarbid (SiC), Einzelkristall-SiC und polykristalliner Diamant. Jedes weist spezifische Eigenschaften und Vorteile auf, die in der Tabelle zusammengefasst sind.
Material |
Wärmeleitfähigkeit |
Oberflächenrauigkeit |
Optisch durchlässig |
Elektrisch isolierend |
Kosten |
Reaktionsgebundenes SiC |
255 W/(m·K) |
< 25 nm |
Nein |
Nein |
Niedriger |
Einkristallines SiC |
370 W/(m·K) |
< 2 nm |
Ja |
4H: Nein 6H: Ja |
Mittel |
Polykristalliner Diamant |
2200 W/(m·K) |
< 10 nm |
Ja |
Ja |
Hoch |
Alle diese Materialien sind im Vergleich zu anderen Substanzen hochgradig wärmeleitend – Diamant hat die höchste Wärmeleitfähigkeit aller Materialien. Ein wesentliches Merkmal von reaktionsgebundenem SiC ist, dass es problemlos mit allen benötigten Durchgangsöffnungen oder Kanälen hergestellt werden kann. Außerdem ist es laserbearbeitbar, um somit den sehr hohen Grad an Ebenheit und geringer Oberflächenrauheit zu erreichen.
Ein Vorteil von Diamant und einkristallinem SiC ist, dass diese Materialien im Bereich des sichtbaren Lichts und nahen Infrarotlichts durchlässig sind. Dies ermöglicht den Einsatz einer breiten Palette von Messtechniken zum Ermitteln der Ebenheit, Stärke und Parallelität der Endteile und somit Fertigungsverfahren mit höherer Präzision.
Polykristalliner Diamant und 6H-Einkristall-SiC sind elektrische Isolatoren. Diese Eigenschaft ist aus mehreren Gründen nützlich, unter anderem schützt es den Halbleiter-Die vor Beschädigung durch elektrostatische Entladung.
Auch die Preise der aus diesen drei Materialien hergestellten Düsen unterscheiden sich. Dies ist relevant, da Düsen Verschleißteile sind, die regelmäßig ersetzt werden.
Coherent ist ein vertikal integrierter Hersteller von TCB-Düsen. Die Integration umfasst das Züchten unserer eigenen Materialien bis hin zur Produktion der einsatzbereiten Teile. Eine Schlüsselkomponente unserer Fertigungskompetenz ist unsere Fähigkeit, sehr ebene Oberflächen herzustellen. Zudem besitzen wir die umfangreiche Messausrüstung, um diese Ebenheit auch zu überprüfen.
Erfahren Sie mehr über reaktionsgebundenes Siliziumkarbid (SiC), Einzelkristall-SiC und polykristallinen Diamant.