ホワイトペーパー
準同時レーザポリマー溶接を使用する理由
透過型レーザ溶接(TTLW)を使用した準同時溶接手法を用いると、多くの用途で他の方法より良い結果が得られます。 特に、部品の歪みが少しも許されない場合や、複雑な溶接シーム形状を伴う部品の場合にこの傾向が顕著です。 しかし、準同時溶接加工で最高の品質を得るには、高度な加工方法の制御が必要です。 これは、拡張性に優れ、複数の生産ラインで再現できる、安定した一貫性のある加工方法を維持するために特に必要です。 この実現には通常、閉ループ締め付け力制御とそれに続くサーマルイメージングを必要とします。
ポリマーは、機械的特性、耐腐食性、生体適合性、電気・熱絶縁性など、独自の特性を備えています。 ポリマーは通常、他の素材よりも安価です。 これらの理由により、さまざまな製品での利用が進んでいます。
多くの場合、ポリマー部品は製造時に接合させる必要があります。 特に医療機器や自動車および産業用途で使用されるセンサーなど、より高価値の製品では、この接合を高い機械的精度、歪みのない部品、最小限の微粒子状屑の生成、および優れた接合強度で実現することが求められます。
ポリマーとの組み合わせ
大量生産の場合、接合は通常、何らかの溶接手法を用いることで実現されます。 特に最も要求の厳しい用途に対しては、望ましい技術としてレーザ溶接が選ばれるようになりました。
レーザ溶接は多くの場合、他の方法と比較して、溶接品質や強度、精度に優れ、再現性が高く、微粒子を発生せず、熱的影響や機械的影響が少なくなります。 しかし、実際はレーザポリマー溶接にはいくつかの異なる手法があり、それぞれに特定の実装方法があります。
これらのほとんどは、「透過型レーザ溶接」(TTLW)の形式をとっています。 この方法では、レーザ波長に対して透明な部品と不透明なプラスチックを接合します。 この2つの部品は、透明な部品を上にして接触するように配置されています。 レーザは、透明な部品から入って、不透明な部品に向かって集束します。 不透明な部品を加熱して溶融し、接合させます。
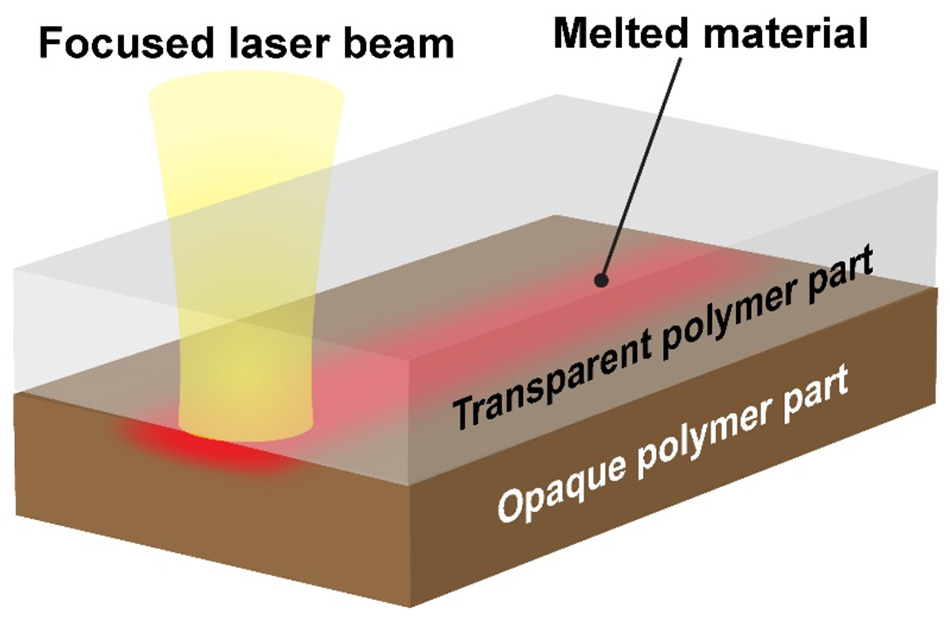
図1. TTLWでは、レーザ光が上の透明な部品を通過し、その下の部品を溶融して接合を形成します。
最も一般的なTTLW手法の概要について説明します。
輪郭: 従来の金属のレーザ溶接と同じように、レーザビームは溶接経路を1回だけトレースします。 このため、溶接経路の小さな部分のみが常に溶融されます。
準同時: この場合、レーザビームは溶接経路を何度も高速にトレースします。 これは非常に高速に実行されるため、溶接シーム全体が一度に溶融されます。
ライン: この場合、レーザビームは部品の幅と同じ長さの細いラインに成形されます。 このラインは、部品の表面全体に1回掃引されます。 常に溶接経路の一部のみが溶融されます。
同時: レーザは溶接シームの形状と一致する静的なパターンで投影されます。 これにより、溶接シーム全体が一度に溶融されます。
この表は、これらの各方法のさまざまな機能、利点、および欠点をまとめたものです。
方法 |
利点 |
欠点 |
典型的な用途 |
輪郭 |
部品サイズの制限がない。 あらゆる形状の部品を溶接し、3D溶接を生成できる。 柔軟性が非常に高く、簡単に変更できる。 |
部品が局所的に加熱されると、変形が生じる可能性がある。 |
自動車のテールランプ |
準同時 |
熱ストレスを最小限に抑えて部品の歪みを防ぐ。 柔軟性が非常に高く、簡単に変更できる。 |
最大部品サイズは一般的に400 mm x 400 mm。 2D溶接に限られる。 |
高精度の医療機器や電子センサー |
線 |
導入が容易である。 比較的大きな部品に対応できる。 |
レーザ出力やビーム速度を局所的に変更できない。 柔軟性がない。 部品が局所的に加熱されると、変形が生じる可能性がある。 |
医療用部品の大量生産 |
同時 |
サイクルタイムが短い。 熱ストレスを最小限に抑えて部品の歪みを防ぐ。 |
加工できる部品の形状が非常に限られている。 線や円などのいくつかのシンプルなシーム形状に限られる。 柔軟性がまったくない。 マルチファイバー構成を使用した場合のエネルギー分布が不均一で不安定。 |
消耗品の大量生産 |
準同時溶接
準同時(QS)溶接は、最も単純なシーム形状以外の要素(放射状溶接や円形パターンなど)を持つ精密な高価値の部品を接合するために最も広く使用されている手法です。 QS溶接は、溶接シーム全体を一度に均等に加熱するため、高品質の接合を実現し、部品の歪みを防ぎます。 実用的な観点からは、ソフトウェア制御によって簡単に変更できる柔軟性の高い加工方法です。 QS溶接はコスト効率に優れた方法であるため、短いサイクルタイムを必要とし、バッチサイズが小規模から大規模に変化する可能性がある製造環境に適しています。
QS溶接の重要な形式の1つが、「コラプス・リブ」法です。 次の図は、この手法の主な要素を示しています。 この手法では、下部に薄い突起状のリブがあり、このリブは上の部品の対応する溝と嵌合します。 ただし、溝はリブよりも少し広めです。
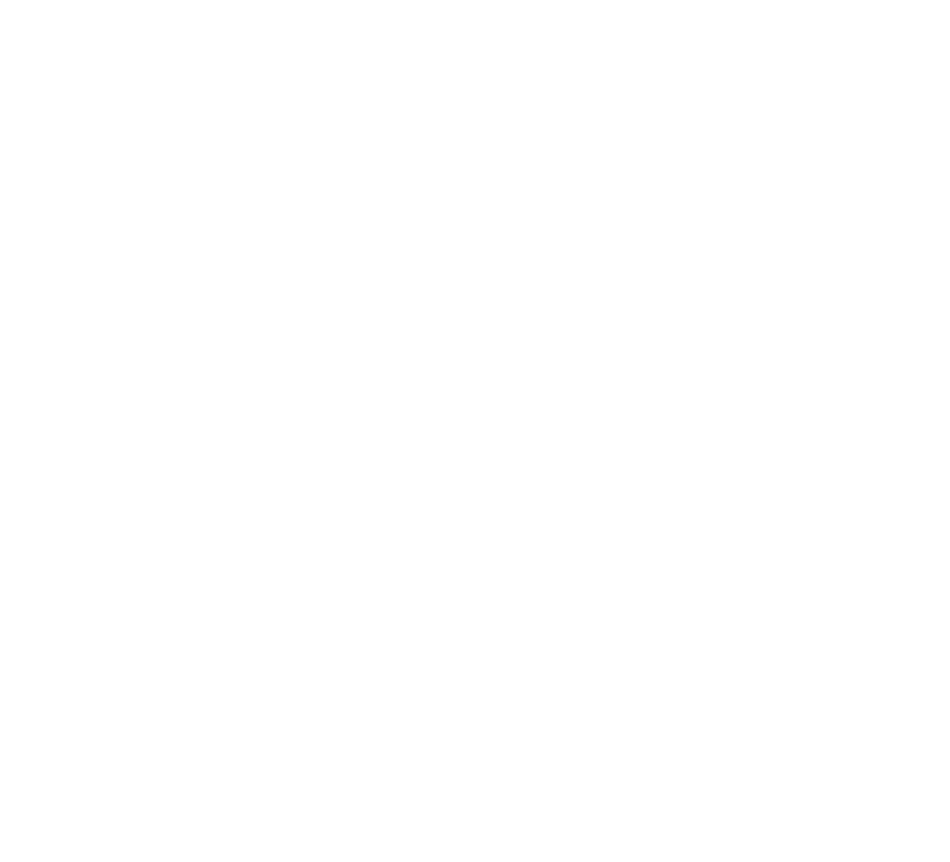
図2. 準同時TTLWの「コラプス・リブ」法の主要ステップの模式図。
クランプで2つの部品を能動的に押し付けながら、レーザで下側のリブを部分的に溶かして溶接します。 溶けた材料が流れ、上下の部品の隙間の一部に充満します。 その後、これが再固化して溶接継手になります。 この特定のタイプのTTLWは、部品が完全な平面でない場合や、公差が厳しい場合でも、良好な溶接継手を実現できる点で特に有用です。
QS溶接加工方法の監視
シームの品質と歩留まりに関して、QS溶接の利点を最大化するには、正確な加工方法監視が必要です。 特に「コラプス・リブ」法においては、「コラプス制御」がこれを成功させる重要な要素の1つとなります。
「コラプス制御」は通常、溶接中に上の部品が下がる量である「コラプス(つぶれ)高さ」の能動的な監視と管理で構成されます。 具体的には、自動部品のコラプス高さ測定は、閉ループ締め付け力(および速度)制御と、レーザ出力の調整に使用されます。
Coherentでは、ポリマー溶接システムに、より精巧なバージョンの「コラプス制御」を採用しています。 高さの測定だけでなく、サーボモーター駆動のクランプの閉ループ制御に、統合された力検出変換器を使用します。 この方法を採用しているメーカーは他にありません。 一部のメーカーはサーボモーターの電流をフィードバック信号として使用していますが、これでは同じ測定精度や動的制御の度合いが得られません。 サーボモーターをまったく使用していないメーカーもあります。 こうしたメーカーは、一般的に最適な結果を得るために必要な精度や応答速度を備えていない空気圧アクチュエーターを使用しています。
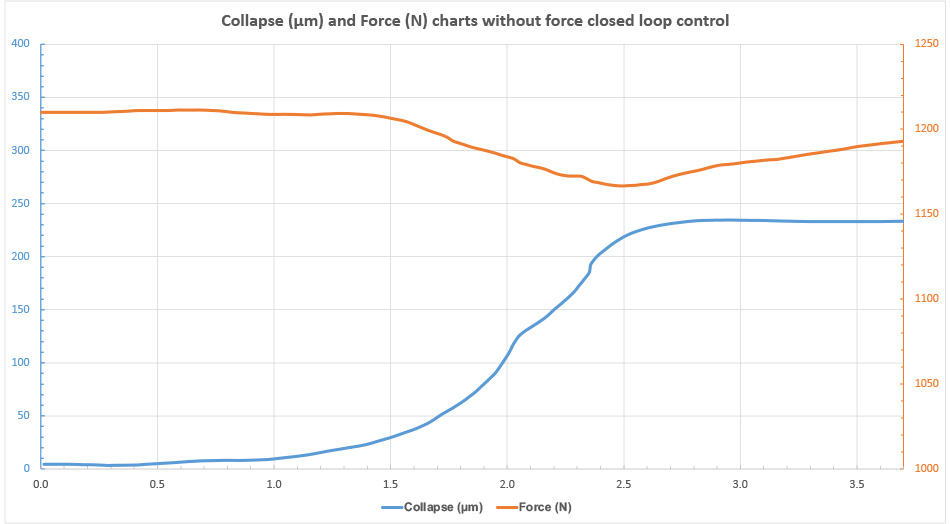
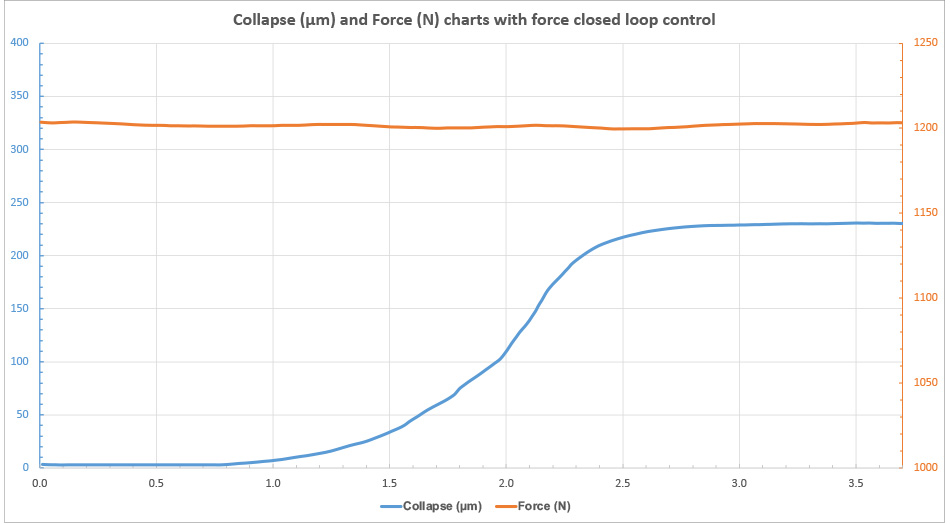
図3. 高精度リアルタイム閉ループ力制御なし(左)とあり(右)のQSポリマー溶接。 この方法を使用すると、コラプス距離と加えられた力の両方を加工方法ウィンドウの中央に維持することができます。 これにより、部品ごとに材料や寸法などのばらつきがある場合でも、一貫した溶接を行うことができます。
このフィードバックにより、部品間の寸法の偏差や、材料の吸収特性の不一致を補正することができます。 周囲の環境や部品自体の変化があった場合でも、加工方法の一貫性が向上し、加工方法ウィンドウが拡張されます。 また、機械間の差異を簡単に補正することもできます。 これにより、ある場所で開発された加工方法を別の場所で使用しても、同じ結果を確実に得ることができます。
サーマルイメージング
溶接が完了したら、サーマルイメージング(赤外線)カメラシステムを使用して溶接品質を評価できます。 サーマルイメージングは、実際には溶接シーム自体の内部ではなく、上の透明な部品の表面温度を測定します。 ただし、この表面温度データは、溶接シームの温度を直接測定した場合よりも、溶接品質に関するより有効な情報を提供します。
この理由を理解するには、レーザが下の不透明な部品のみを直接加熱していることを思い出してください。 上の透明な部品は、下の部品と接触しているため伝導によって溶融されます。
そのため、溶接後に上の部品の表面温度を測定すると、2つのことがわかります。 1つは、下の部品がどれだけレーザエネルギーを吸収し、どれだけ十分に溶融したかです。 もう一つは、この熱を上の部品に伝導させて溶融させるために、部品全体にクランプ力がどの程度一貫して適用されたかです。
サーマルビジョンチェックで溶接シーム全体を画像化します。 溶接パスに沿った途切れは、溶接シームの隙間を示しており、線の太さの変化は、溶接の弱いスポットを示しています。
一般的に、サーマルビジョンは、溶接後の品質分析ツールとして使用されます。 これにより、不良部品を即座に特定し、排除することができます。 これにより、不良部品にさらに経費をかけることがなくなるため、メーカーの経費削減につながります。 もちろん、不良部品をお客様に出荷することも防げます。
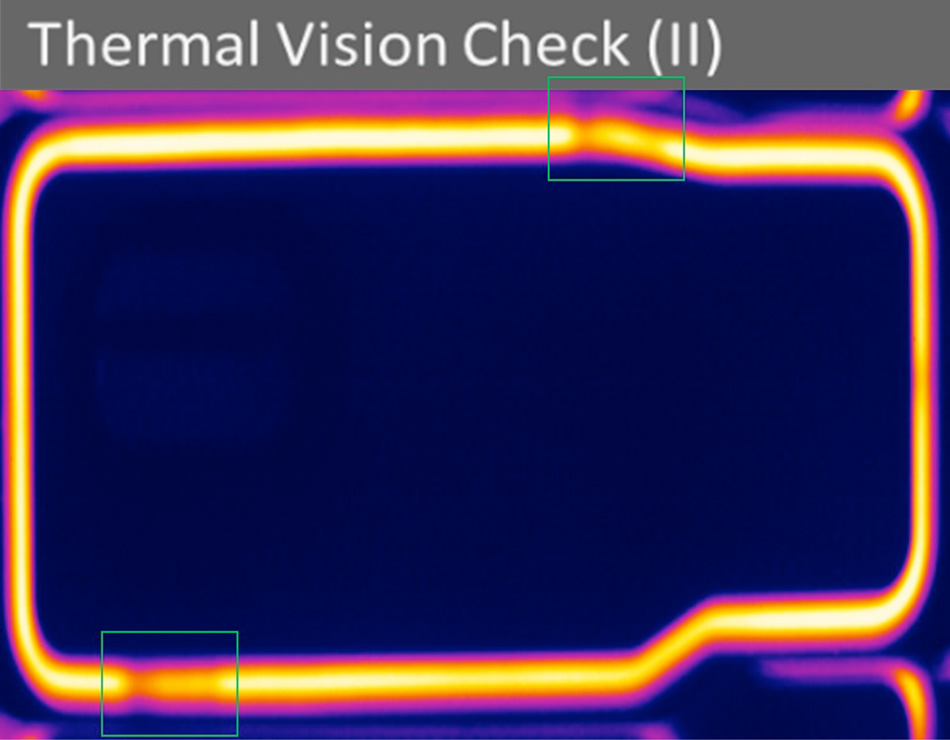
図4. リアルタイムサーマルモニタリングにより、溶接欠陥(緑色の枠で表示)を即座に特定し、多くの場合その場で修正できます。
まとめ
準同時TTLWは、要求の厳しいポリマー接合用途に対して、特に有用な方法です。 複雑な形状の溶接においても、高い溶接精度、美しい外観、優れた機械的特性を実現できます。 正しく設計されていれば、部品の歪みや微粒子の発生がなくなり、後処理も不要になります。 特に、閉ループ締め付け力制御やサーマルモニタリングを使用して実装すると、堅牢で信頼性が高く、モジュール式で拡張可能な加工方法が実現されます。