Laser Pas de Deux、EVモーター溶接を次のレベルに引き上げ
密閉型CO2とUV固体レーザを組み合わせることで、大量EVモーター製造に必要な高品質で、費用対効果の高いヘアピンストリッピングとクリーニングが可能になります。
2025年2月12日、Coherent
EVメーカーは、品質を向上させながら、運用を最適化し、コストを削減するという圧力が高まっています。これらの取り組みは、EV市場シェア、特に総所有コスト(TCO)の感度が高く、ICE車両が依然として普及している大量市場に必要な拡大に不可欠です。
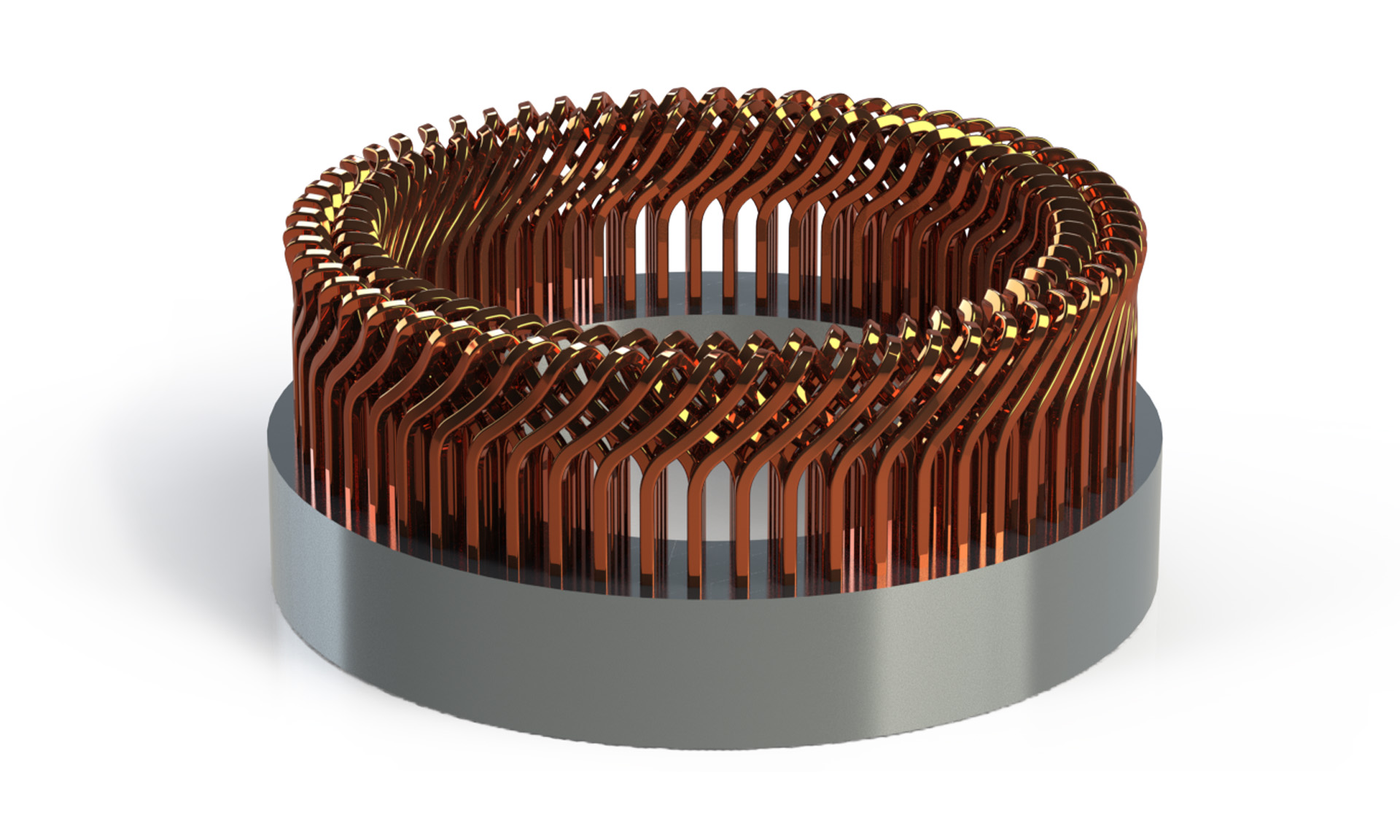
溶接ヘアピンの例。
EVエンジンやモーターの製造には、ヘアピン溶接の最適化が欠かせません。ヘアピン溶接は、モーターの信頼性と性能に不可欠なプロセスです。従来の機械的ストリッピング方法は、多くの場合、不足しているため、表面の損傷、工具の摩耗、製造の遅れなどの加工方法の非効率性が生じ、コストが上がり、加工方法の再現性に影響します。
レーザストリッピングとクリーニングは、機械ストリッピングの限界を克服しながら、全体的なコストを抑えながら優れた結果をもたらすことができる、革新的な代替手段を提供します。ここでは、CO2をUVレーザと組み合わせて使用して、手つかずの溶接可能なヘアピンを生成するCoherentの革新的な2段階プロセスについて説明します。ここに示すデータは、このアプローチがEVメーカーに、優れた品質の溶接を実現するコスト効率の高い方法を提供することを示しています。
ヘアピンハードル
EVモーターの巻線は通常、個々の銅線から形成されます。これらは“U”形状に曲げられ(したがって“ヘアピン”という名前)、アセンブリに配置されます。次に、隣接する各ヘアピンの端を隣り合わせに溶接し、電気的に接続して、単一の連続巻線を生成します。さらに、一部の代替設計では、波状のパターン(波巻きまたはS巻き)に形成された連続的な平坦なワイヤが使用され、溶接前にステータスロットに挿入されます。
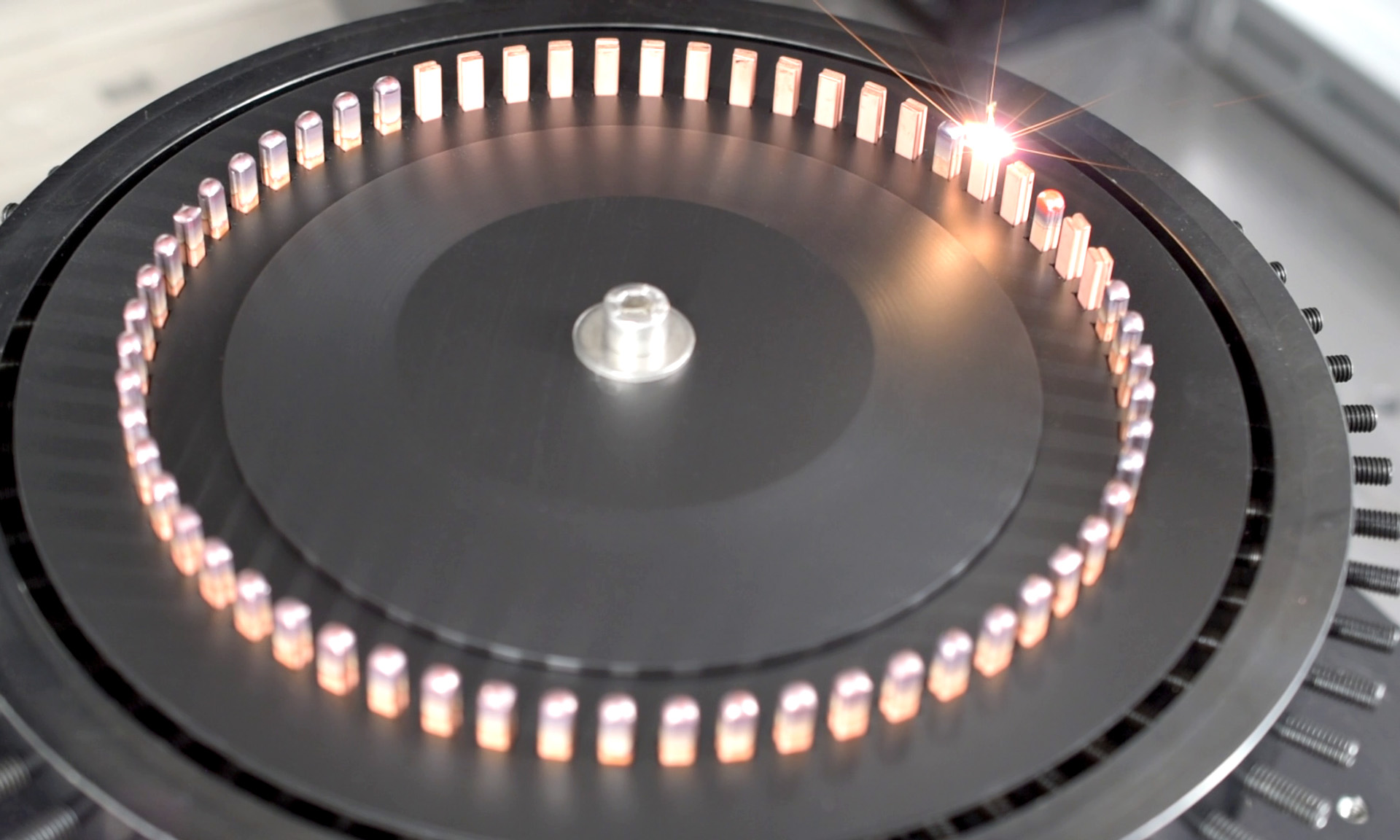
CoherentのARMファイバーレーザHIGHmotion 2Dスキャナでレーザ溶接されているヘアピンペアの例。
巻線はすべての電気モーターで絶縁されています。ヘアピンモーターでは、小型設計と電気自動車に典型的な高電圧要件に対応するため、絶縁材をより厚く、より堅牢にする必要があります。
溶接の前に、各ヘアピンの両端から少量のこの絶縁材を取り外す必要があります。これは、高品質の電気的および機械的接続を確保するために重要です。
従来、この作業は主に機械的方法を使用して行われており、IR(1um)パルスレーザを用いたシングルステップレーザ加工も使用されてきました。機械的ストリッピングには、ワイヤー表面に直接接触する切断ツールを使用して絶縁材をこすり落とします。これらのアプローチは長年にわたって標準でしたが、電気自動車(EV)製造のペースが速い世界では大きな課題となっています。
たとえば、機械的ストリッピングに必要な物理的接触により、ピンから銅の層が除去され、テクスチャ表面が残り、ピン間にギャップや部品フィットの問題が生じ、溶接の完全性と一貫性が損なわれます。さらに、機械工具は摩耗を経験し、プロセスの不整合、頻繁なメンテナンス、予定外のダウンタイム、潜在的な生産中断につながります。これらの問題は、EV製造の大量需要に追いつくのに苦労するプロセスの速度が遅いことで悪化しています。
2段階レーザストリッピングは、上のカットです
レーザは、絶縁ストリッピングなど、幅広い用途で材料の除去に使用されます。この文脈では、レーザ加工の利点として、以下が挙げられます。
- 溶接品質の向上: 銅線に損傷を与えることなく絶縁体を完全に除去することで、表面がきれいになり、最適な溶接品質が得られます。
- メンテナンスと機器のダウンタイムの削減: 工具の摩耗がなく、機械の詰まりの可能性を排除することで、中断のない生産フローが実現します。
- スループットの向上: ワイヤー供給中の連続ストリッピングにより、生産効率が向上します。
- 一貫性の向上: 摩耗や接触がなければ、レーザ加工は安定し、再現性があります。
レーザ加工が加工方法を改善できることは、容易にわかります。しかし、本当の問題は、「最適なレーザですか」です。つまり、このプロセスを実行することができる多くの可能なレーザ光源と実装のうち、大量EVモーター製造用途で品質、速度、コストのバランスが最も良いのはどれですか?
レーザ加工方法の最適化
Coherentは、ほぼすべての種類の産業用レーザのリーディングプロバイダーとして、1つの技術に固有の好みを持たずに、この用途を客観的に調査できる独自の立場にあります。
実際、ヘアピンストリッピングに最適なレーザは見つかりませんでした。その代わりに、当社のアプリケーションエンジニアは、最適なコーティング除去を実現するための2レーザプロセスを開発しました。このアプローチは、今日、お客様に最もコスト効率の高い方法で最高の溶接済み表面品質を提供します。2レーザプロセスを調査する主な動機は、シングルステップレーザストリッピングプロセスの問題を克服することでした。
シングルステップレーザ加工は、コーティングの吸収と下層銅の間の妥協点です。ファイバーレーザのほぼ1 μmのIR波長は、コーティングによって容易に吸収されないため、界面で加熱され、コーティングから浮遊粒子に剥がれ落ちます。粒子が入ってくるレーザビームに干渉し、ピンの清浄度に影響を与える可能性があり、システムに閉じ込められ、機器の洗浄のために頻繁に停止する可能性があります。 さらに、ファイバーレーザの透過IRビームは、銅表面からポリマー残留物を完全に除去することはできません。銅線の表面を溶かし、水素や炭素などの絶縁体ポリマーの成分を露出させる可能性があります。これにより、表面が汚染され、その後の溶接品質に影響が及ぶ可能性があります。
Coherentの2段階レーザベースのヘアピン調製プロセスには、以下が含まれます。
- バルクストリッピング: 絶縁体の大部分は、中出力CO2レーザを使用して迅速に除去されます。このタイプのレーザは、高スループットの非金属材料の除去に最適です。
- 最終クリーニング: 次に、パルス低出力ナノ秒UV固体レーザを使用して、絶縁残渣を除去します。これにより、溶接のための手つかずの表面が得られます。UV固体レーザの短波長は精密の材料加工に優れており、ポリマー、その他の有機材料、銅などの幅広い材料を除去するのに特に効果的です。
バルクストリッピング工程では、Coherent J-5-10.6 μmレーザが理想的な光源であることが証明されています。ヘアピン絶縁にはさまざまな材料(ポリイミド、ポリエーテルイミド、ポリエステル、ポリエステルイミド、ポリアミド、ポリエーテルエーテルケトン、エポキシ樹脂、さまざまなフルオロポリマーなど)が使用されていますが、これらはすべてこのレーザの10.6 μm出力波長を強く吸収します。また、これらすべての材料では、9.4 μmや10.2 μmなど、当社が提供している他の利用可能なCO2レーザ波長よりも10.6 μmで吸収が高くなります。
Coherent J-5-10.6 μmには、望ましい実用的な特性もあります。これは、400 W以上の平均出力を生成する完全密封パルスCO2レーザであり、高スループットのストリッピングを実行できます。また、自動機器への統合に最適な、内蔵型のコンパクトなパッケージです。
最終洗浄ステップでは、Avia LX 355-30-60 HEが出力パラメータの適切な組み合わせを示しています。これは、355 nmで30 Wの平均出力を出力する周波数トリプル半導体レーザ励起固体レーザです。最も重要なのは、最大300 kHzの繰り返し速度と最大500 μJのパルスエネルギーでの動作をサポートすることです。これにより、この用途に必要な速度で高精度精密アブレーションが可能になります。
Avia LX 355-30-60 HEは、簡単に統合できるように設計されています。また、Coherent PureUVのアクティブレーザ洗浄エンジンを組み込むことで、並外れた寿命とメンテナンスフリーの動作が実現します。
溶接結果
アプリケーションラボは、前述の2段階の組み合わせに到達する前に、さまざまなプロセスを調査しました。CO2、ナノ秒パルスIRファイバーレーザ、ナノ秒UVレーザなど、さまざまなレーザを個別に、また組み合わせて検査しました。絶縁ヘアピンの処理結果を詳細に分析し、最も有望なソースが特定されると、特定のプロセスパラメータが最適化されました。
試験の一環として、X線光電子分光法(XPS)を使用して表面化学を分析し、汚染物質を特徴付け、定量化しました。ここで、レーザ溶接の前に銅表面からすべての残留元素を除去する最も効果的な手段は、2段階レーザストリッピング加工(CO2とUVレーザの組み合わせ)であることがわかりました。
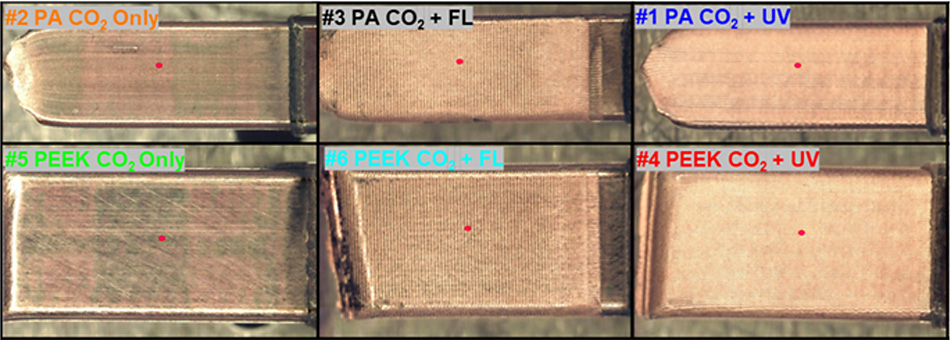
この一連の写真では、CO2、ns IRファイバー(FL)、ns UV固体レーザを使用したさまざまな除去技術を比較しています。写真の上段では、絶縁材はポリアミド(PA)であり、下段では、絶縁材はポリエーテルエーテルケトン(PEEK)でした。純粋な目視検査でさえ、CO2 + UVレーザの組み合わせが両方のケースで最適に見えることを示しています。これは、実際の溶接試験によって確認されました。
もちろん、最も重要な指標は、コーティング除去プロセス後に得られる溶接の品質です。次の図は、溶接されたヘアピンの一連のX線画像を示しています。これにより、2段階(CO2 + UVレーザ)加工により、最終的に優れた溶接が得られることがわかります。2段階CO2 + UVレーザストリッピングにより、溶接前に表面のポリマー残留物を除去することで、溶接の多孔性を最小限に抑えます。ポリマー残留物は、水素、炭素、その他の有機元素を含んでおり、溶融金属プールに液体状態で入り、溶接固化プロセス中に空隙を形成することが知られています。多孔性は、溶接の機械的および電気的性能に影響を与えます。
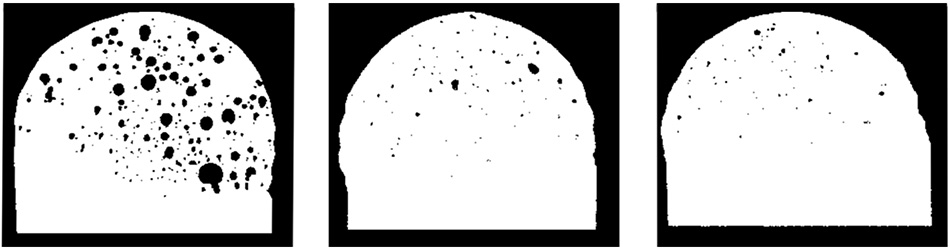
3つの除去方法を使用した溶接ビーズのX線画像。CO2 + UV固体レーザは、最高の溶接品質(最小の多孔性含有量)を明確に示します。