随着汽车制造商加紧生产更多电动汽车 (EV),电动汽车生产的各个方面都在改进。当然,他们的目标是在降低成本的同时提高车辆的可靠性和性能。
电动汽车的一个重要部分是分配整车电力的电缆。这些电缆称为汇流排。由于需要承载的电流量很大,所以汇流排不仅仅是电线。它们是厚带状金属导体,包裹着绝缘层(典型尺寸范围是 12 毫米宽、3 毫米厚)。最常用的金属是铜,有时也用铝。绝缘层是塑料材料(通常是聚酰胺 PA12)。
绝缘汇流排材料通常长度较长,成卷供货,就像传统电线一样。汽车制造商切割出需要的长度并将汇流排弯曲成所需的形状。汇流排的形状可能非常复杂,因为它们必须绕过汽车内各种其他零件和结构,将电力输送到需要的地方。
在生产中,有时必须从汇流排的两端去除(剥离)一些绝缘层。这是将汇流排电气连接到其他部件所必需的步骤。汽车制造商对此工艺有一些具体要求。
首先,绝缘层剥离的速度必须要快,这样才能具有成本效益,而不是成为生产瓶颈。这意味着要在几秒钟内去除大约 25 毫米(1 英寸)的绝缘层。
其次,必须彻底去除绝缘层。因为剥离区域中的任何残留绝缘层都会干扰电气连接,导致电力浪费(降低车辆效率)。此外,汇流排的末端通常需要焊接到其他导体或蓄电池上。留在导体表面的任何塑料都会污染焊缝,从而降低其电气和机械性能。
最后,导体本身不能因剥离而损坏。这可能会降低导体机械强度,从而形成可能发生故障的点。
出于所有这些原因,使用任何机械方法(如刀片或刮刀)去除绝缘层几乎都满足不了要求。此外,很难使用刀片去除弯曲或异形表面的绝缘层。
汇流排激光剥离横空出世
为了满足这些相同的要求,激光器成为剥离汇流排绝缘层的上佳工具。这是因为激光工艺完全是非接触式加工,并且可以很轻松地配置,来实现弯曲零件的加工。因此激光加工快速而灵活。
二氧化碳激光器尤其适合这项任务。这是因为二氧化碳激光器产生远红外光。大多数用于绝缘的塑料都会非常强烈地吸收这种光,但铜对此类光的反射率却很高。
这意味着激光会迅速蒸发绝缘层,但在到达导体时会自动停止去除材料(因为铜只是将激光反射回来而不会吸收)。因此,它可以很轻松地去除绝缘层,同时保持铜完好无损。
生产中的汇流排激光剥离
为了实际执行绝缘层剥离,激光束会聚焦到汇流排上的一个小点以集中能量。该聚焦光束来回快速扫描,以便覆盖必须去除绝缘层的整个区域。
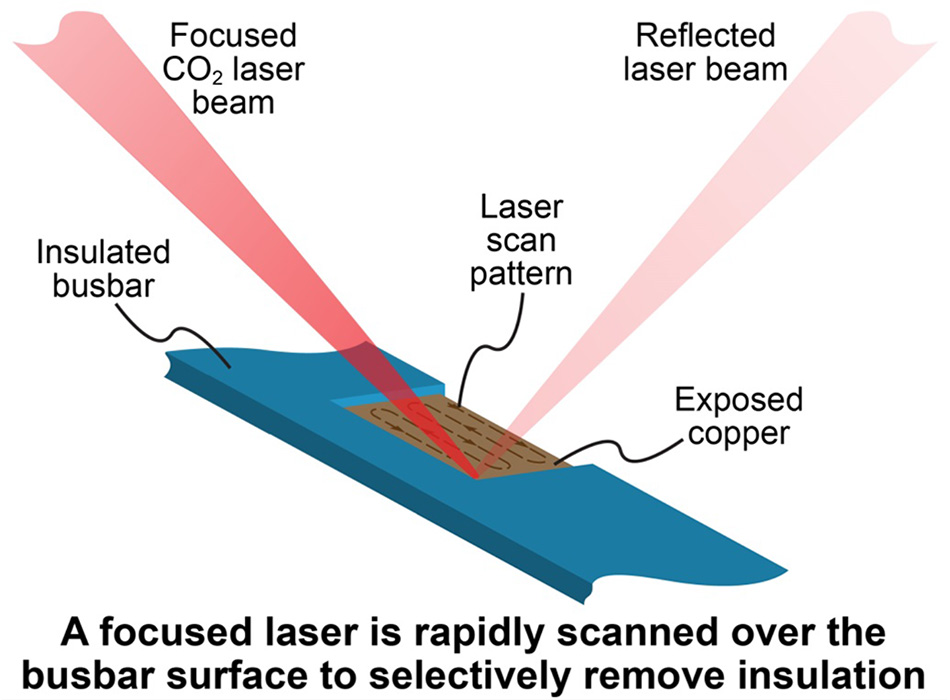
在生产环境中实施此方法时,有一些重要的实际考虑因素。例如,为了获得必要的工艺产量,使用了两台激光器。每台激光器从汇流排的一侧剥去绝缘层(因此,图中将有第二道激光从下方射出)。这样一来,无需翻转零件就能处理两个面,操作得以简化。
此外,最好让激光束以一定角度照射汇流排。这有两个作用。首先,这可以避免任何激光反射回来并损坏光束传输系统。其次,这样激光就能够同时去除汇流排顶部和边缘的绝缘层(因为倾斜的激光束可以“看到”汇流排的侧面)。
汇流排系统是剥离汇流排的完整解决方案。它包括两个 PowerLine C 子系统,以及所有相关的扫描和光束传输光学器件,以及所有必要的控制电子器件和软件。
PowerLine C 可以在大约 6 秒内从 6 毫米宽的汇流排两侧去除 30 毫米长、0.5 毫米厚的聚酰胺。绝缘层可以完全去除,而不会对导体造成任何损坏,从而实现了工艺的高良品率。
有两种不同的汇流排剥离系统可供选择 - 内联版本和独立版本。内联系统与提供连续汇流排的线轴进料机构集成在一起。激光在切割和最终弯曲操作之前对汇流排进行剥离。PowerLine C 甚至支持“实时”剥离,即在不减慢或停止汇流排运动的情况下执行剥离。在独立版本中,机械臂拾取预先切割并弯曲的汇流排并将其放置到系统中,然后进行激光剥离。
查看高速、高效的汇流排剥离如何工作。
相关资源