ERFOLGSGESCHICHTE EINES KUNDEN
Neues Excimer-Verfahren erzeugt in kurzer Zeit ultraharte DLC-Schichten bei niedrigen Temperaturen
Die Herausforderung
Diamantharter (DLC) Kohlenstoff wird häufig verwendet, um hochverschleißfeste Beschichtungen zu erzeugen. Aktuelle DLC-Beschichtungsverfahren weisen jedoch verschiedene Nachteile auf. So ist beispielsweise tetraedrischer amorpher Kohlenstoff (ta-C) ein wünschenswertes wasserstofffreies DLC-Material, das sowohl für seine extreme Härte (> 40 GPa) als auch für seine geringe Reibung bekannt ist. Bei den üblichen Herstellungsverfahren entstehen jedoch Folien mit hohen inneren Spannungen, die ihre Leistung beeinträchtigen. Hagen Grüttner und seine Kollegen von der Firma Antacon, einer Ausgründung der Hochschule Mittweida, haben sich zum Ziel gesetzt, ein neues Verfahren zu entwickeln, mit dem spannungsarme Folien hergestellt werden können, die für die industrielle Produktion geeignet sind. Ihr Verfahren basiert auf der gepulsten Laserabscheidung (PLD) unter Verwendung der einzigartig hohen Pulsenergie von Coherent 248 nm Excimerlasern.
Die Lösung
Der Schlüssel zur Entwicklung eines erfolgreichen Niedertemperatur-Produktionsverfahrens war die Kombination zweier Excimer-basierter Verfahren: Gepulste Laserabscheidung (PLD) und Annealing. Grüttner erklärt: „Excimer-basiertes PLD ist ein bekanntes industrielles Verfahren zur Herstellung von Funktionsschichten, wie z. B. supraleitenden Hochtemperaturschichten. Außerdem kann es mit Niedertemperatur-Substraten verwendet werden. Wenn jedoch der PLD-Prozess (oder irgendein anderer Prozess) für ta-C verwendet wird, enthalten die Beschichtungslagen oft große Mengen (z. B. 12 GPa) an Restspannungen, was ihre mechanische Festigkeit stark beeinträchtigt.“
Grüttner und Kollegen haben dieses Problem gelöst und mit Hilfe von zwei Coherent LEAP Excimerlasern dicke (Mikrometer) ta-C-Beschichtungen mit einer Restspannung von nur 0,1 GPa erzeugt. Der erste Excimer wird auf das Graphit-Target innerhalb der auf nur 90 °C erhitzten Vakuum-PLD-Produktionskammer fokussiert. Die hohe Fluenz und die Photonen im tiefen UV erzeugen Kohlenstoffionen mit der hohen kinetischen Energie, die benötigt wird, um dichte ta-C-Schichten auf dem Substrat zu erzeugen. Damit wird eine bis zu 100 nm dicke ta-C-Schicht über dem Substrat aufgebaut. Die dünne Schicht wird dann mit einem Puls aus dem zweiten Excimer bestrahlt, der eine Fläche von einigen mm2 abdeckt. Dadurch wird die gesamte 100 nm große neue Schicht aus ta-C geglüht und die Restspannung abgebaut. (Großflächige Beschichtungen werden durch schrittweises Verändern der Strahlposition während des Pulsens geglüht). Der PLD-Prozess wird dann wiederholt, um weitere 100 nm ta-C zu erzeugen. Wichtig ist, dass das Team durch die Anpassung der Laserparameter in der Lage ist, die resultierende Filmhärte, den Youngschen-Modul und das Ausmaß des intrinsischen Spannungsabbaus zu variieren. Sie haben diesen Aspekt genutzt, um abgestufte Schichten auf Materialien wie Stahl zu erzeugen, die sowohl eine hervorragende Haftung als auch eine sehr harte Deckschicht gewährleisten.
Das Ergebnis
Unter Verwendung optimaler Abscheidungsparameter hat das Mittweida-Team eine Härte von bis zu 70 GPa mit Youngschen-Modulen von 700 bis 800 GPa erreicht, was zu einer extrem hohen Betriebsverschleißfestigkeit führt. Und dank der geringen mittleren Oberflächenrauheit (Ra) von <100 nm und dem niedrigen Reibungskoeffizienten (≤ 0,1) sind diese Schichten auch für tribologische Anwendungen sehr gut geeignet. Die Forscher wollen das Verfahren nun kommerzialisieren. Grüttner fasst die Vorteile der Excimerlaser zusammen: „Die hohe Pulsenergie des LEAP-Excimers ermöglicht großflächiges Annealen. Wir haben die hohe Wiederholrate (150 Hz) verwendet, um eine schnelle ta-C-Abscheidung zu unterstützen, und planen eine Hochskalierung auf 300 Hz. Die stabile Leistung und das gleichmäßige Strahlprofil ermöglichen uns eine präzise Steuerung sowohl des Abscheidungs- als auch des Annealing-Prozesses.“
„Die hohe Pulsenergie von LEAP ermöglicht eine schnelle Abscheidung und Aushärtung. Die stabile Leistung und das flache Profil des oberen Strahls ermöglichen uns eine präzise Kontrolle sowohl über die Abscheidung als auch über den Annealing-Vorgang.“
- Hagen Grüttner, Antacon GmbH, Mittweida, Deutschland
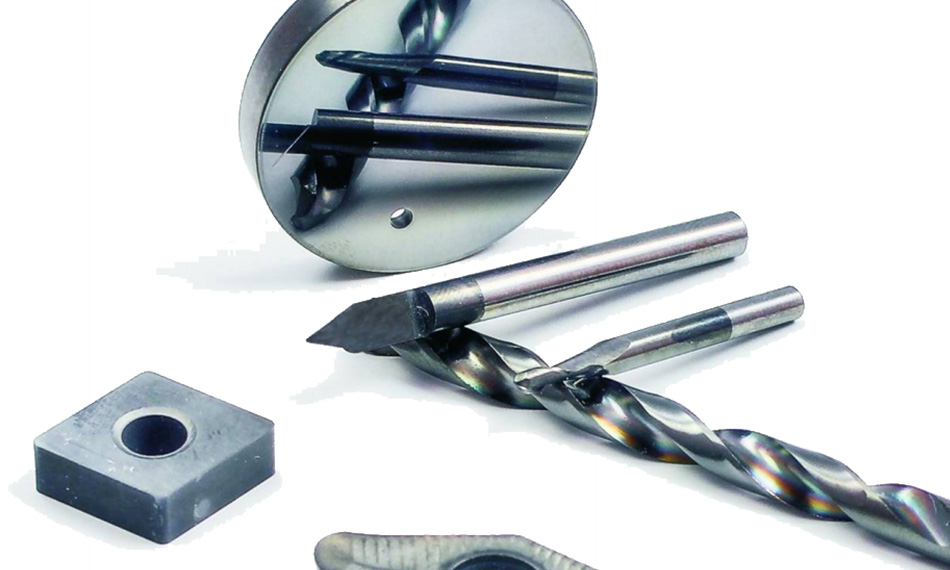