Laser in der Displayherstellung: MicroLED Lift-Off, Transfer, and Repair
Coherent UVtransfer-Systeme führen drei kritische Schritte bei der Herstellung von MicroLED-Displays durch, die zu skalierbaren Displays mit beeindruckender Auflösung und Helligkeit führen.
4. Oktober 2022 von Coherent
In diesem sechsten Teil unserer Serie über die Herstellung von Displays werfen wir einen Blick in die Zukunft und sehen, wie Laser die automatisierte Serienproduktion von Displays der nächsten Generation auf der Basis von MicroLEDs ermöglichen.
Die AMOLED-Technologie ermöglicht uns heute dünne Displays für Smartphones und Fernseher mit fantastischen Farben und Auflösungen. Aber die Displayhersteller arbeiten bereits an der Serienproduktion des nächsten „großen Wurfs” bei den Displays: MicroLED-Displays.
Lesen Sie die anderen Blogartikel in dieser Serie über Laser in der Displayherstellung |
|||
Basierend auf kleinen (<50 Mikrometer) anorganischen LEDs verspricht diese schnell aufkommende Technologie mehrere Vorteile. Erstens ist sie immun gegen vorzeitige Alterung, die OLED-Emitter manchmal beeinträchtigen kann. Darüber hinaus kann sie eine höhere Helligkeit mit höherem Kontrast liefern. Darüber hinaus handelt es sich um eine skalierbare Technologie mit dem Potenzial, große Fernsehgeräte und öffentliche Display zu einem günstigeren Preis zu produzieren sowie ultrakompakte Displays für VR/AR-Anwendungen.
MicroLED-Displays gibt es bereits seit einiger Zeit in begrenzter Stückzahl, aber jetzt finden die Displayhersteller heraus, wie sie diese Technologie in die volle Produktion bringen können. Es stellt sich heraus, dass Laser mehrere entscheidende Rollen spielen. Werfen wir einen Blick darauf
Wirtschaftlichkeit im Wafer-Maßstab
Anorganische (Halbleiter-) LEDs ermöglichen eine hohe Lichtausbeute – wie z. B. in hellen Autoscheinwerfern. Dadurch können MicroLEDs sehr klein und gleichzeitig sehr hell sein. Die heutige Größe liegt bei etwa 50 x 50 Mikrometern, und es wird vorhergesagt, dass sie irgendwann bei 10 x 10 Mikrometern liegen wird.
Es gibt drei Arten dieser aktiven Strahler: rot, grün und blau. Jeder Typ wird in Massenproduktion (durch epitaktisches Wachstum) auf einem dicht strukturierten Saphir-Wafer hergestellt. So kann ein Wafer mit einem Durchmesser von 6 Zoll mit vielen Millionen einzelner MicroLEDs gemustert werden, was die Wirtschaftlichkeit der Skalierung ermöglicht.
Diese werden schließlich auf einem großen, relativ preiswerten Stück Glas mit den notwendigen Schaltkreisen platziert, um als dünnes Display zu funktionieren. Bei einem großen Display, das aus mehreren separaten Kacheln besteht, kann die gesamte Displayfläche zwei Meter groß sein, und der Pixelabstand kann einen Millimeter oder mehr betragen. Selbst mit drei der winzigen Emitter in jedem Pixelbereich ist der größte Teil des Displays toter Raum. Für die Skalierung großer Formate bedeutet dies, dass der Hauptkostentreiber die Anzahl der Pixel ist, was wiederum niedrigere Kosten verspricht.
Das Konzept ist zwar einfach, aber die praktische Umsetzung ist es definitiv nicht!
Abheben lassen
Eigentlich gibt es eine große übergreifende Herausforderung, damit das alles funktioniert. Millionen dieser MicroLEDs (Chips) müssen von dem Saphir-Wafer, auf dem sie hergestellt werden, auf das große Display-Panel gebracht werden. Ob Sie es glauben oder nicht, bei einigen frühen Prototypen wurden die einzelnen Chips mechanisch aufgenommen und platziert, z. B. durch Vakuumroboter. Aber das ist einfach zu langsam für die Endproduktion. Und da die Chips immer kleiner werden, ist es schwierig, dies schnell zu tun, ohne zu riskieren, dass einige von ihnen bei der Handhabung beschädigt werden. Die Ausbeute muss wegen des unglaublich hohen Volumens sehr hoch sein – bei einem 8K-Display sprechen wir von über 30 Millionen Pixeln, d. h. von fast 100 Millionen Chips.
Die Lösung ist der Einsatz von Lasern in automatisierten Multiplex-Prozessen, die mit einigen der bewährten Techniken verwandt sind, die in früheren Artikeln dieser Serie beschrieben wurden.
Es handelt sich um drei verschiedene Prozesse: Lift-Off, Transfer und Reparatur. Zunächst werden die MicroLEDs von dem Saphir-Wafer, auf dem sie gezüchtet wurden, abgelöst und auf einen temporären Träger übertragen, um die Handhabung zu erleichtern. Dies geschieht mit einer konventionellen, laserbasierten Technik namens Laser-Lift-Off (LLO). Der Träger ist mit einem Klebstoff beschichtet und wird mit den Oberseiten der Chips in Kontakt gebracht. Das ultraviolette Licht eines Excimerlasers wird von hinten auf den Saphir-Wafer gerichtet und verdampft eine dünne Opferschicht aus Material, das vor der Herstellung der Chips auf den Wafer aufgebracht wurde. Dadurch bleiben die MicroLEDs auf dem temporären Träger mit dem gleichen engen Abstand wie auf dem Wachstumswafer.
LIFT – das Spielfeld wechseln
Als Nächstes kommt der Laser-induzierte Vorwärtstransfer (LIFT). Hier dringen die Pulse eines ultravioletten (Excimer-)lasers durch die Rückseite des Trägers ein, der transparent ist. Das Laserlicht passiert den Träger und den Klebstoff und interagiert mit der verbleibenden Pufferschicht des GaN. Dies ermöglicht eine nahezu rückstandsfreie Übertragung und keine Beeinträchtigung der MicroLED-Oberfläche beim Kunden, wenn kurze UV-Wellenlängen verwendet werden! Dadurch werden die Chips physisch abgesprengt und auf das endgültige Display-Panel geschoben, das in engem Kontakt, aber mit einem gewissen Abstand, der größer als die Dicke der MicroLEDs sein muss, um Kollisionen zu vermeiden, platziert wird. Der Kleber auf der letzten Glasplatte hält die MicroLEDs an ihrem Platz.
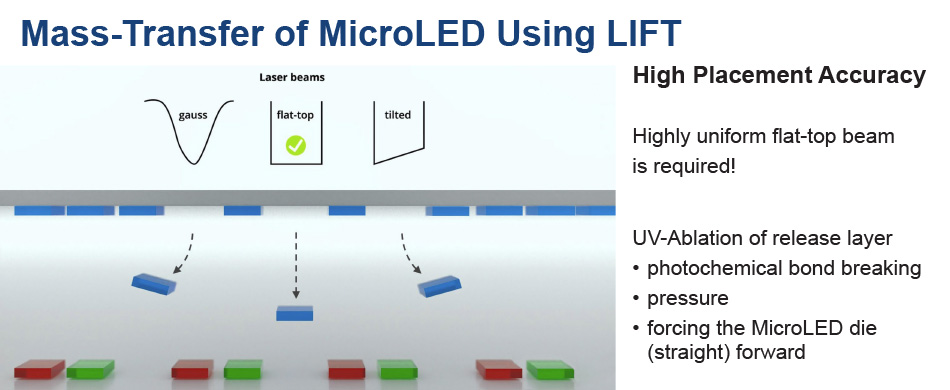
Bei LIFT durchdringt ein großflächiger Laserstrahl eine Fotomaske, sodass nur bestimmte Pixelelemente freigegeben und auf das Displaysubstrat geschoben werden. Ein gleichmäßiger, so genannter Flat-Top-Strahl ist entscheidend für eine perfekte Platzierung. (Nicht maßstabsgetreu).
Jetzt kommt der entscheidende Teil der „Magie”: die Änderung des Abstands (des Chipabstands). Der rechteckige Laserstrahl durchläuft eine Maske, die mit Löchern versehen ist. Der Strahl wird dann 2,5- oder 5-fach vergrößert, so dass das projizierte Lochmuster den gleichen Abstand hat wie die Pixel auf dem endgültigen Display. Auf diese Weise wird nur jeder 5. oder sogar jeder 10. oder ein anderes ganzzahliges Vielfaches des LED-Abstands auf dem EpiWafer durch einen bestimmten Laserpuls über einen winzigen Spalt von wenigen Mikrometern zum Display geschoben. Der Träger wird dann relativ zu dem festen Strahl und der Maske nur ganz leicht über das MicroLED bewegt, um zu den benachbarten MicroLEDs zu gelangen. Das Display-Panel wird eine größere Strecke bewegt und der Vorgang wird wiederholt. Machen Sie sich keine Sorgen, wenn dieser Schritt und die Wiederholung ein wenig verwirrend klingen; wir haben ein tolles Video, das es ziemlich einfach verständlich macht.
Alternativ arbeiten einige Hersteller an einer leicht abweichenden Sequenz, bei der der Abstand geändert wird, während die Chips vom EpiWafer abgehoben werden. Dies wird als selektive LLO bezeichnet. Aber das Gesamtergebnis ist das gleiche.
Hoher Durchsatz und Reparatur
LIFT ermöglicht die kostengünstige Herstellung einer großen Anzahl von MicroLEDs auf einem relativ kleinen Saphir-Wafer, die dann mit viel größeren Abständen (Engl.: Pitch) platziert werden können, um ein einziges großes Panel zu erzeugen. Und der andere große Vorteil von LIFT ist, dass es schnell ist. Tausende von MicroLEDs werden durch jeden Puls bewegt.
In der aktuellen, auf Forschung und Entwicklung ausgerichteten Implementierung beträgt die Pulsrate des Excimerlasers bis zu 20 Pulse/Sekunde (20 Hz), was bedeutet, dass eine Fläche von bis zu 640 mm2 in nur einer Sekunde mit MicroLEDs bedeckt werden kann! Aber diese Excimerlaser-Technologie ist in ihrer Leistung extrem skalierbar, wie sich bei Annealing Anwendungen gezeigt hat, die hohe (über 1 J) Pulsenergien und hohe Wiederholraten verwenden. Bei LIFT können höhere Pulsenergien genutzt werden, um größere Masken und Feldgrößen zu ermöglichen.
Die Ausbeute bei der Herstellung von relativ einfachen Halbleiterbauelementen wie anorganischen MicroLEDs ist jetzt unglaublich hoch. Aber es gibt Millionen von ihnen auf jedem Display, so dass die Möglichkeit besteht, dass ein defektes oder falsch behandeltes Pixel bedeutet, dass einer der RGB-Bausteine nicht korrekt emittiert. Das lässt sich in einem automatisierten Laserprozess leicht reparieren, indem man einen Ersatzchip mit Hilfe einer Maske mit einem einzigen Loch darin oder eines scannerbasierten Systems hinzufügt.
Coherent bietet bereits ein Tool namens UVtransfer für die MicroLED -Displayproduktion an, das alle drei dieser Prozesse durchführt – Laser-Lift-Off (LLO), Laser-induzierter Vorwärtstransfer (LIFT) und Reparatur/Trimming für defekte Pixel. Dieses 3-in-1-Tool macht die Produktion von großen MicroLED-Displays praktisch und wirtschaftlich.
Erfahren Sie mehr über Coherent UVtransfer-Systeme.