Laser in der Displayherstellung: Laser Lift-Off
Die UVblade-Systeme von Coherent führen diesen entscheidenden Schritt bei der Herstellung der dünnen, flexiblen AMOLED-Displays durch, die in vielen Smartphones, Tablets und anderen mobilen Geräten zu finden sind.
4. Oktober 2022 von Coherent
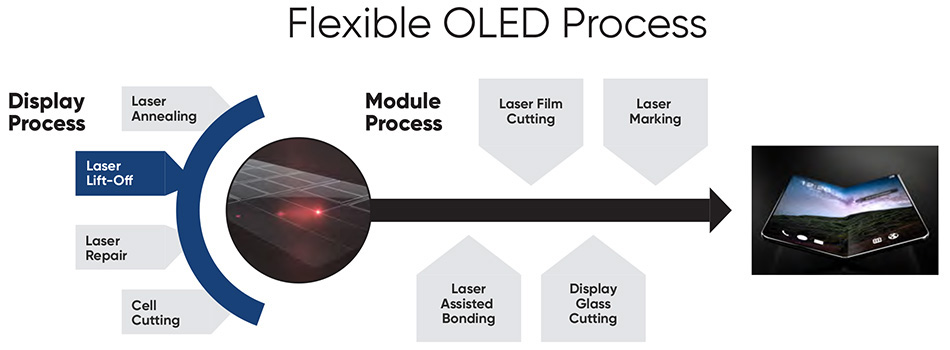
Wie tragen Laser dazu bei, dass die heutigen Displays so erstaunlich dünn und leicht sind? Denn jeder, der alt genug ist, um sich an die ersten Fernsehgeräte zu erinnern, weiß zu schätzen, wie weit sich die Displaytechnologie von diesen unglaublich sperrigen Bildröhren entfernt hat.
Die ersten Flachbildschirm-Fernseher und -Monitore basierten alle auf Flüssigkristallanzeigen (LCDs). Diese Technologie war ein großer Fortschritt gegenüber den alten Fernsehröhren.
Aber der interne Aufbau von LCDs ist tatsächlich etwas komplex. Das LCD-Panel selbst strahlt kein Licht ab. Sie benötigen also eine Hintergrundbeleuchtung, einen Polarisator und eine Schicht von Farbfiltern, um die roten, grünen und blauen Pixel zu erzeugen. All dies schränkt die Möglichkeiten ein, diese Geräte zu miniaturisieren und vor allem flexibler zu gestalten.
Lesen Sie die anderen Blogartikel in dieser Serie über Laser in der Displayherstellung |
|||
Keine Panik, es ist organisch
Um noch dünnere und flexiblere Displays zu erhalten, entwickelten die Hersteller die OLED-Technologie (Organic Light Emitting Diode). Jedes Pixel in einem AMOLED-Display enthält drei Lichtemitter (rot, grün und blau), so dass es keine Hintergrundbeleuchtung benötigt. Dadurch kann ein AMOLED-Display nur einen Bruchteil eines Millimeters dick sein. Und das ist die Gesamtdicke, selbst wenn Sie weitere Schichten für die Touchscreen-Funktionalität und die Kontrastverbesserung hinzufügen. Da AMOLED-Displays so dünn gemacht werden können, ist es sogar möglich, sie flexibel oder faltbar zu machen.
Aber die Herstellung solch dünner Displays stellt die Hersteller vor ein Problem. Bedenken Sie, dass zahlreiche Displays gleichzeitig auf einem einzigen Substrat von etwa 1,5 m x 1,9 m hergestellt werden. Es wäre unpraktisch, etwas in dieser Größe zu verarbeiten, das nur den Bruchteil eines Millimeters dick ist. Etwas, das so groß und dünn ist, ist schwierig zu handhaben. Außerdem ist es entscheidend, dass das Display flach bleibt. Auch das ist bei etwas Großem und sehr Dünnem schwer zu machen.
Das Geheimnis für dünnere Displays
Um dieses Problem zu lösen, werden die Displays auf einem dickeren und steiferen „Mutterglas“ aufgebaut. Der erste Produktionsschritt besteht darin, eine dünne Polymerfolie auf dieses Mutterglas zu kleben. Diese Polymerschicht wird der Boden des fertigen Displays sein. Als Nächstes wird Silizium auf dieses Polymersubstrat aufgebracht, gefolgt vom Excimerlaser Annealing (ELA), der Erstellung der elektronischen Schaltkreise und dem Aufbringen der anderen Displayschichten.
Ganz am Ende dieses Prozesses wird das Display vom Mutterglas getrennt. So erhalten Sie ein hauchdünnes Display.
Die Displays sind fast fertig, wenn sie vom Mutterglas getrennt werden. Zu diesem Zeitpunkt sind die meisten Kosten bereits eingebracht. Die Verschrottung von Teilen in diesem Stadium ist also teuer. Das bedeutet, dass der Trennungsprozess sowohl präzise als auch schonend sein muss.
Es gibt zwei Dinge, die besonders vermieden werden müssen. Erstens kann der Trennungsprozess keine nennenswerte mechanische Kraft oder Belastung ausüben, da die Displays zu empfindlich sind. Zweitens darf der Prozess nicht zu viel Hitze in das Display einbringen, da dies die Elektronik beschädigen könnte.
Excimerlaser bringen OLED-Produktion in Gang
Das Trennverfahren, das derzeit von den großen Herstellern von AMOLED-Displays verwendet wird, heißt Laser Lift-Off (LLO). Um LLO zu starten, wird die gesamte Platte umgedreht, so dass das Mutterglas nun oben liegt. Dann wird das Licht eines ultravioletten (UV) Excimerlasers mit hoher Pulsenergie zu einem langen, dünnen Linienstrahl geformt. Dieser Linienstrahl wird durch das Glas hindurch genau auf die Schnittstelle zwischen dem Mutterglas und dem dünnen Polymersubstrat, das die Display-Schaltung enthält, fokussiert.
Der Strahl wird schnell über die gesamte Fläche des Mutterglases gescannt. Das ultraviolette Licht durchdringt das Glas, wird aber von dem Klebstoff, der das Mutterglas mit dem Polymer verbindet, und dem Polymer selbst stark absorbiert. Dadurch wird das Ganze so stark erhitzt, dass der Klebstoff praktisch sofort verdampft und das Display vom Mutterglas gelöst wird. Aber – und das ist der wirklich wichtige Punkt – das Laserlicht dringt kaum in das Polymer-Display-Substrat selbst ein, so dass es im Gerät keine große Erwärmung verursacht. Der Display-Schaltkreis wird durch den LLO-Prozess nicht beeinträchtigt.
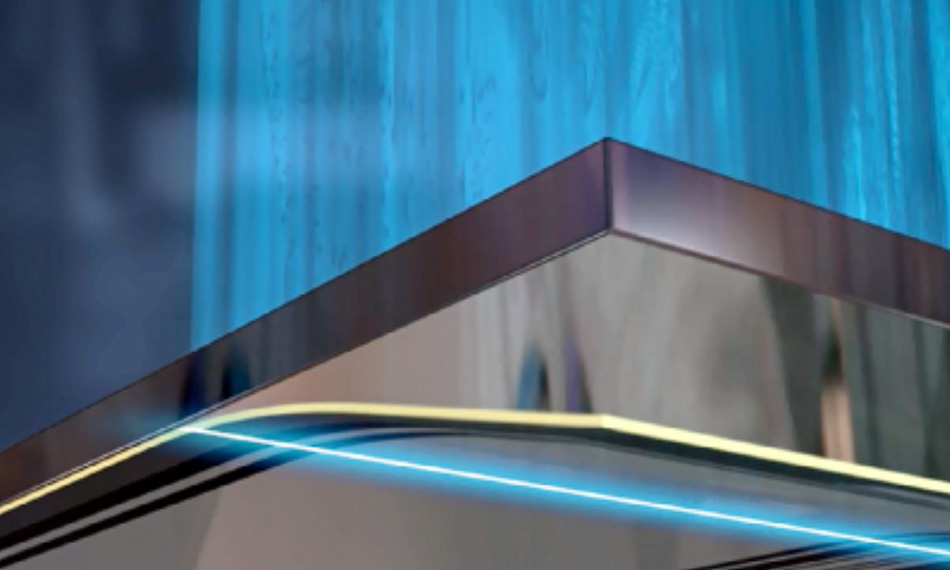
Durch schnelles Scannen des Excimerlaser-Linienstrahls können die empfindlichen Display-Schaltkreise sanft von der Mutterglasplatte getrennt werden, auf der sie hergestellt wurden.
Genau wie bei ELA bietet der Excimerlaser die ideale Quelle für LLO. Dafür gibt es zwei Hauptgründe. Erstens erzeugt der Excimerlaser eine höhere Pulsenergie im ultravioletten Bereich als jeder andere Lasertyp. Dieses UV-Licht wird vom Klebstoff stark absorbiert, und die hohe Laserleistung bewirkt eine schnelle Zersetzung des Klebstoffs. Dies ermöglicht es LLO, mit der für die Display-Produktion erforderlichen Geschwindigkeit zu arbeiten. Geschwindigkeit ist wichtig, denn die großen Displayhersteller produzieren jeden Tag über eine Million Mobiltelefone!
Außerdem eignet sich der Excimerlaserstrahl dazu, zu einem langen, dünnen Linienstrahl geformt zu werden. Außerdem kann er so umgewandelt werden, dass er ein gleichmäßiges (flaches) Strahlprofil hat und nicht die Gauß'sche Intensitätsverteilung, die die meisten Laser erzeugen. Das flache Strahlprofil ermöglicht ein viel größeres Prozessfenster als ein Gauß'scher Strahl es bieten könnte. Das macht die LLO-Produktionslinie weniger anfällig für geringfügige Änderungen der exakten Fokusposition des Lasers, für kleine Abweichungen bei den Abmessungen des Mutterglases und toleriert eine gewisse Verformung des Mutterglases.
Die LLO-Systeme von Coherent werden von großen Displayherstellern weltweit eingesetzt. Diese kombinieren einen hochstabilen Excimerlaser mit unserem einzigartigen optischen System UVblade, das den endgültigen Linienstrahl erzeugt. Wir können alle gängigen Displaygrößen unterstützen, von einer einzelnen Zelle bis hin zu einem großen Substrat. Und die Optiken von Coherent UVblade sind skalierbar, um die Produktionsanforderungen der nächsten Generation von flexiblen und faltbaren Displays zu erfüllen.
Erfahren Sie mehr über Coherent-Excimer-UV-Lasersysteme.