Automatisiertes MDM-Laserschweißen steigert den Ertrag
Die flexiblen Optionen von Coherent maximieren die Kosteneffizienz der Maschinenautomatisierung.
17. August 2023 von Coherent
Qualifiziertes Personal verursacht nicht nur für Einstellung und Ausbildung hohe Kosten, es wird beim aktuellen Arbeitsmarkt auch immer schwieriger, geeignete Mitarbeiter zu finden und zu binden. Automatisierte Laserschweißsysteme reduzieren den Bedarf an Fachpersonal erheblich. Sobald beispielsweise ein Ingenieur oder Techniker die vielfältigen Aspekte einer Schweißanwendung mit der Software der Maschine definiert und gespeichert hat, kann der Bediener den Prozess mittels eingeschränktem Zugriff über die GUI sicher einleiten.
Die Eliminierung der subjektiven Wahrnehmung durch den Bediener in Kombination mit dem Einsatz von In-situ-Vision, Prozessüberwachung, Laserüberwachung und Nachbearbeitungsprüfung sorgt für eine zuverlässige Produktion mit höheren Erträgen und weniger Ausschuss. Sobald ein Teil des Prozesses in Richtung der festgelegten Grenzwerte abweicht, nimmt die Maschine die erforderlichen Anpassungen vor oder hält den Prozess an und warnt den Bediener. Dies ist offensichtlich für jede Anwendung von Vorteil. Besonders vorteilhaft ist es beim Schweißen von Teilen, bei denen die eigentliche Wertschöpfung bereits zuvor im Prozess stattgefunden hat oder die aus sehr teuren Materialien bestehen.
Weil insgesamt die Profitabilität steigt. Jeder dieser Automatisierungsvorteile trägt direkt oder indirekt zu niedrigeren Gesamtkosten pro Teil bei.
Automatisierte Funktionen und Vorteile
Wir wollen nun einige Schlüsselaspekte erörtern, die sich in einer vollständig automatisierten Lösung als kritische Komponenten erweisen können.
Automatisierte Teilebestückung/-entnahme: Erhältlich sind vielfältige Zuführoptionen wie Schüttvorrichtungen, Förderbänder oder Setzpacker, die mit Robotern verbunden werden, um Teile in das oder aus dem System zu leiten. Automatisierung reduziert die Lohnkosten ebenso wie die Auswirkungen der Arbeit auf die Qualität erheblich. In einigen Fällen können die Pick-and-Place-Roboter auch eingesetzt werden, um den Prozess anzutreiben. Dies geschieht üblicherweise in Verbindung mit einem 3D-Vision-System. Diese automatische Schweißnahtpositionierung sorgt für zusätzliche Kosteneffizienz.
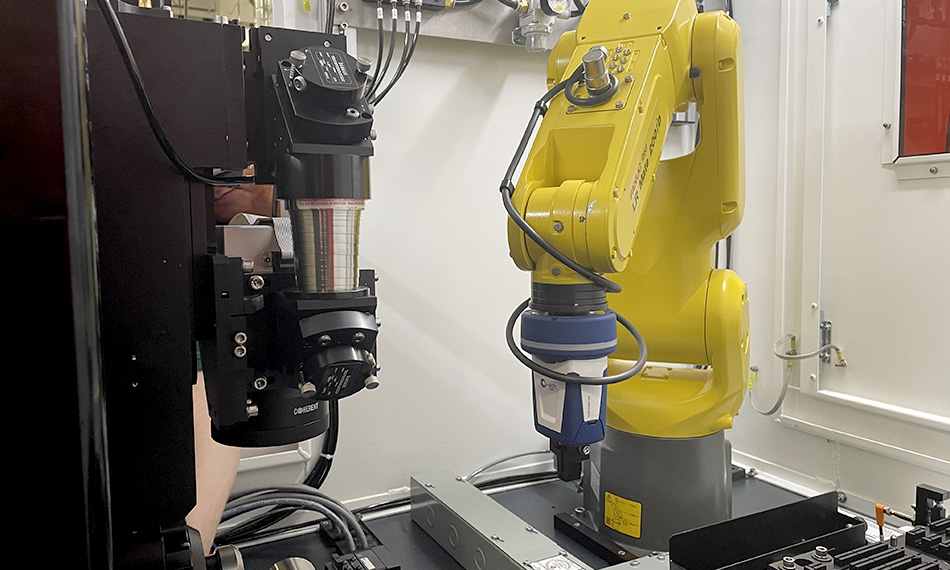
Automatisierungslösungen führen das Teil in das und aus dem System und senken die Lohnkosten.
Pre-Prozess-Vision: Dient der Verifizierung des Teils und seiner Positionierung vor jedem Schweißvorgang. Diese Prozessvorbereitung kann in Abhängigkeit von der Passung des Teils über das Fortsetzen des Prozesses entscheiden. In einem manuellen Prozess platziert der Bediener Teile in einer Vorrichtung und spannt sie vor dem Schweißen sicher ein. Gelegentlich kann diese Allerweltstätigkeit mit einem Drehtisch beschleunigt werden, der gleichzeitiges Schweißen sowie Be- und Entladen ermöglicht. In einem automatisierten System kann das Machine-Vision-System die Teile separat betrachten: in einer Schüttvorrichtung, auf einem Förderband und/oder in einem Setzpacker. Es kann eindeutige physische Details und Justiermarken und/oder Barcodes oder ähnliche Kennungen identifizieren.
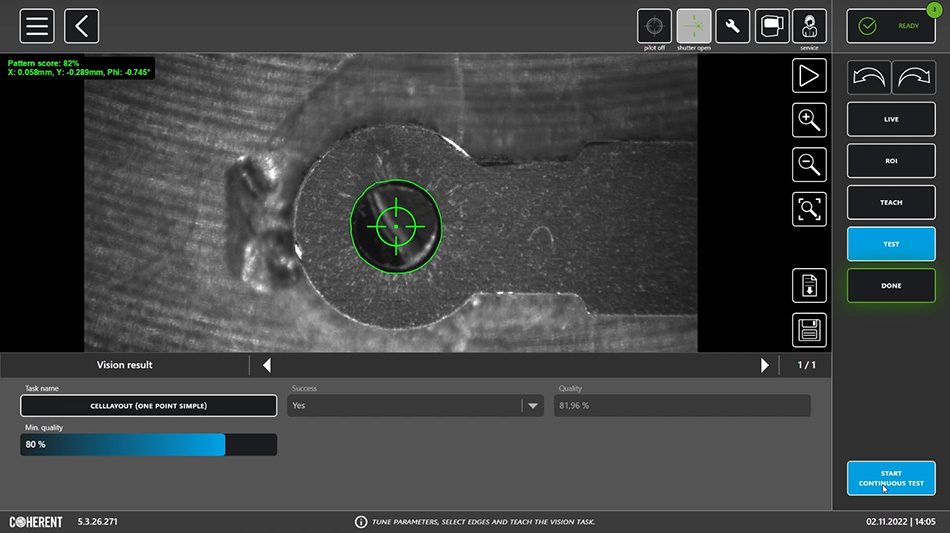
PartVision von Coherent sorgt bei jedem Schweißvorgang für die Verifizierung des Teils und seiner Positionierung.
Prozessinterne Überwachung: Bei Prozessvariationen werden Alarme ausgegeben. Zudem können präventive Wartungsarbeiten geplant oder die Produktion kann gestoppt werden, bevor fehlerhafte Teile montiert werden. Statt auf Lösungen von Drittanbietern zu vertrauen, hat Coherent ein eigenes System namens Coherent SmartSense+ speziell für das Mikroschweißen entwickelt, das eine wirtschaftliche und umfassende prozessinterne Überwachung ermöglicht. Eine wichtige Komponente von SmartSense+ ist ein einzigartiges optisches System, das reflektiertes Laserlicht sowie vom Prozess selbst ausgestrahltes Licht erfasst und analysiert. Auch akustische und andere Signale können berücksichtigt werden. Anhand dieser Daten kann festgestellt werden, ob der Schweißprozess tatsächlich stattgefunden hat, wie groß der Spalt zwischen Teilen in horizontaler und vertikaler Richtung ist und wie sich der Prozess und – bei Verwendung von Gas – die Schutzgasdurchflussrate ändern. Zudem können die Schweißnähte auf Löcher, Hohlräume und Mikrorisse untersucht werden.
Ein zusätzlicher Vorteil unserer prozessinternen Überwachung besteht in der Verwendung der Signale zur Optimierung des Schweißplans – wann wird das Plasma gebildet, wann ist die Schweißung instabil – und in deren Verknüpfung mit den Parametern von Laser und Optik. Unsere Anwendungstechniker haben die Nützlichkeit bei vielen Gelegenheiten unter Beweis gestellt, sogar für Benutzer mit jahrzehntelanger Schweißerfahrung!
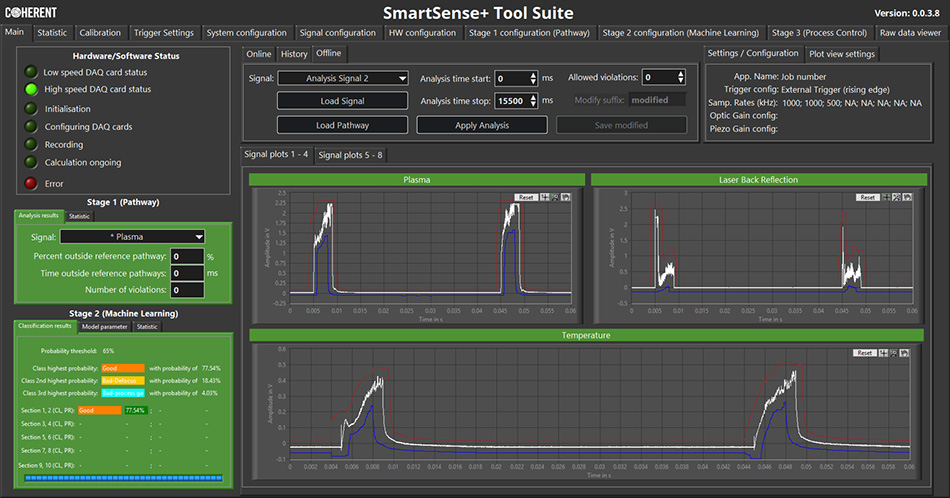
Mit proprietären Algorithmen können die Sensorsignale analysiert werden, um eine Rückmeldung (OK/Nicht OK) sowie Hinweise auf den wahrscheinlichen Schweißfehler bereitzustellen: falsche Positionierung, zu geringe Leistung, zu wenig Schutzgas, Verunreinigung usw.
Datenerfassung vor dem, im und nach dem Prozess: Die Datenprotokollierung ist heute ein Eckpfeiler der Produktion, weil die Daten die Analyse der Anlagenleistung und des Prozesses sowie die Maximierung des Ausstoßes ermöglichen. Alarme des Systems oder des Prozesses können Aktionen auslösen, bevor das Prozessfenster endet. Beispiele hierfür sind industrielle Vision-Systeme, die Alarme vor dem Schweißen ausgeben, wenn Passungstoleranzen überschritten werden, prozessinterne Überwachungen, die Prozessabweichungen oder Bedingungen des Typs OK/Nicht OK melden, sowie die Aufnahme der Schweißnaht per Bildverarbeitung und das Anhängen der Aufnahme an die Produktionsdaten. Unsere Systeme unterstützen alle wichtigen Kommunikationsprotokolle und wir verfügen über jahrzehntelange Erfahrung in der Entwicklung von Schnittstellen, die solche Daten für unsere Kunden bereitstellen.
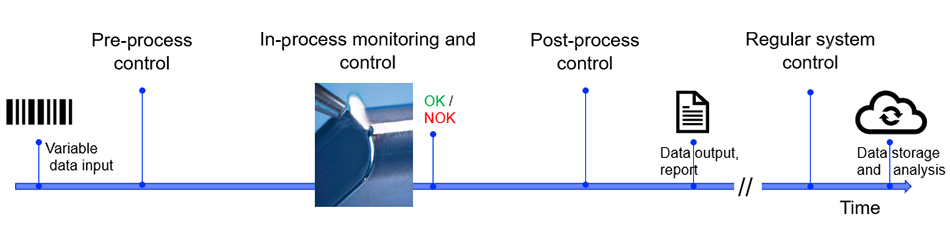
Die automatisierte Inspektion und Datenverfolgung/-protokollierung eliminiert die zeitlichen Risiken und die Fehlerrisiken, die bei menschlicher Inspektion und manueller Datenerfassung relevant werden.
Einfache leistungsstarke Steuersoftware: Diese Automatisierung erfolgt mithilfe verschiedener Technologien und Methoden, deren separate Integration mutmaßlich große Probleme verursachen würde. In einem vollautomatischen Laserschweißsystem von Coherent wird jedoch jeder Aspekt des Schweißens von Coherent Laser FrameWork kontrolliert. Dabei handelt es sich um eine Softwareplattform der nächsten Generation mit benutzerfreundlicher GUI und objektbasierter Prozesseinrichtung/-ausführung. Die Zugriffsbeschränkungen dieser Software verhindern, dass ein Bediener vergisst, eine der Automatisierungs- oder Datenprotokollierungsfunktionen aufzurufen oder zu starten.
Wirtschaftliche Lösungen
Automatisierte Laserschweißsysteme können die Kosten vieler MDM-Anwendungen senken. Sie dürfen aber andererseits den Kapitalaufwand nicht übermäßig erhöhen. Insbesondere trägt es nicht zur Wertschöpfung bei, Funktionen und Merkmale zu kaufen, die für Ihre Anwendung nicht benötigt werden. Deshalb bietet Coherent mit vielfältigen Optionen – von den Zuführoptionen bis zum Einsatz von RFID-Lesegeräten – maximale Flexibilität. Wir liefern nicht einfach Komplettsysteme, sondern optimierte Systeme – optimiert für exakt Ihre Anforderungen.
Weitere Informationen über Coherent-Lösungen für MDM.
Verwandte Ressourcen