白皮书
激光切割手术用海波管
综述
海波管是一种薄金属管,在许多现代医疗手段中使用。 全自动工作站激光加工是制造这种精密医疗产品的首选方法,能够保证必要的精度、产量和产能。 借助针对应用优化的软件,该工艺可以变得简单且非常高效。
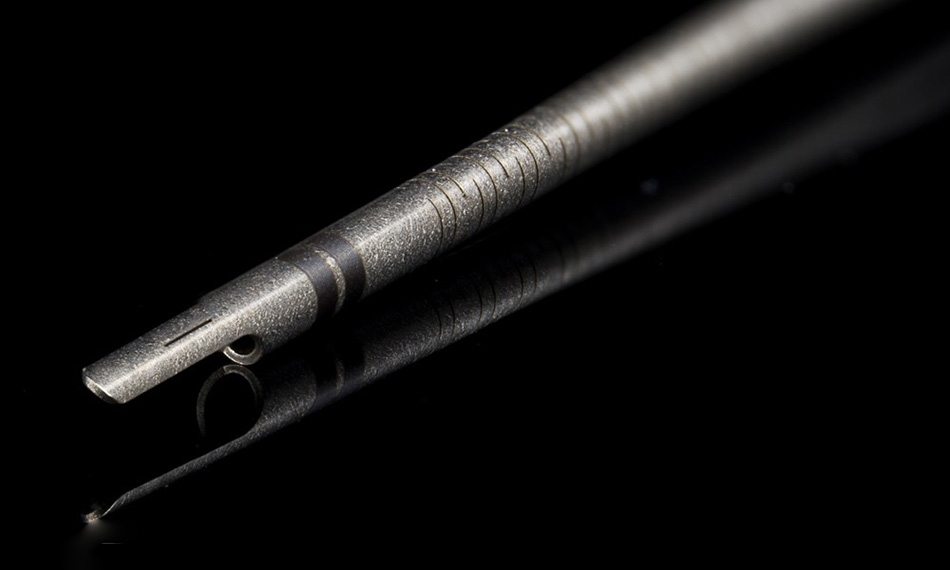
海波管: 一项拯救生命的技术
微创手术具有许多优势,在许多此类医疗手段中,都要使用海波管(有时称为导丝)这一关键设备。 这些海波管需要小而柔韧,才能进入人体血管。 而且它们需要是中空的,以便控制工具或输送药物。
海波管必须满足许多复杂的要求。 其边缘必须无毛刺,而且其所包含的材料应柔软且易于消毒。 其远端设计可以是简单的切口,也可以是复杂的微加工部件。 为了能够可靠运行,海波管在承受一定扭矩时应具有柔韧性,并且必须能够承受扭结和推动。
金属海波管通过其管壁上的切口图案获得柔韧性。 间断螺旋图案是实现柔韧性的方法之一。 切口长度和切口间距决定了管的剩余刚度。 切口精度对于确保海波管在手术中正确工作至关重要。
”切口精度对于确保海波管在手术中正确工作至关重要。“
海波管的精确高效加工
通常,海波管采用先进的激光技术进行加工。 激光系统必须执行不同的任务,例如在金属管壁上或壁内打标、切割和钻孔。 目前,主要采用中等功率光纤激光器执行这些任务。 所有边缘必须无毛刺,这可能需要在进行激光加工后进行一些后处理。
然而,越来越多的用户现在选择飞秒激光器,而不是光纤激光器。 这种超短脉冲 (USP) 激光将其能量快速积聚到材料中,导致热量无法扩散,并且在材料蒸发的过程中最大限度缩小热影响区域。 因此,USP 激光器能够产生相对光滑的边缘,而后处理水清洗通常就足够了。 但反过来,USP 激光器虽然非常精确,但速度比光纤激光器要慢一些。
图 1 显示了使用相干公司 StarCut Tube 加工的海波管样品。出于演示目的,我们使用了同时配有光纤激光器和飞秒激光器的 StarCut Tube Hybrid。 仅配备光纤激光器或飞秒激光器的 StarCut Tube SL 也可以完成该任务,同时占用空间更小。
样品是从一个外径为 0.7 mm 的不锈钢管中切出来的。该管的壁厚为 100 µm。 在左端切掉了一个称为削皮的部分。 在削皮内切出了一个小测试切口。 此外,海波管上还打标了两个黑色环。 这三个步骤均使用相干公司的 Monaco 飞秒激光器执行。
“样品是从一个外径为 0.7 mm 的不锈钢管中切出来的。该管的壁厚为 100 µm。”
图 1 显示了使用相干公司 StarCut Tube 加工的海波管样品。出于演示目的,我们使用了同时配有光纤激光器和飞秒激光器的 StarCut Tube Hybrid。 仅配备光纤激光器或飞秒激光器的 StarCut Tube SL 也可以完成该任务,同时占用空间更小。
样品从外径为 0.7 mm 的不锈钢管上切下。 该管的壁厚为 100 µm。 在左端切掉了一个称为削皮的部分。 在削皮内切出了一个小测试切口。 此外,海波管上还打标了两个黑色环。 这三个步骤均使用相干公司的 Monaco 飞秒激光器执行。
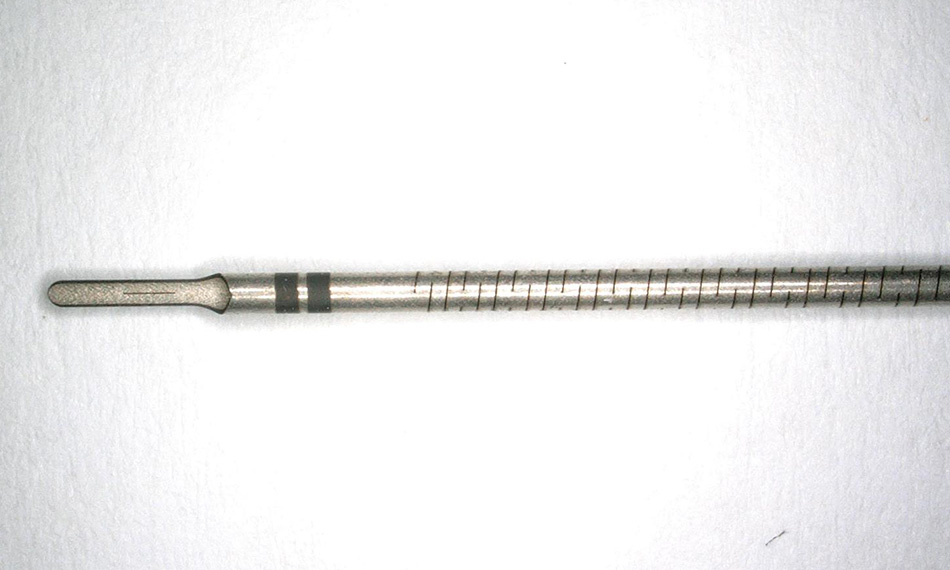
图 1:使用相干公司 StarCut Tube Hybrid 制作的海波管样品。 外径为 0.7 毫米。
下一步,一个长长的间断式螺旋被刻入管壁。 对于此工艺,系统切换到此混合工作站的第二个激光源: 功率适中的相干公司 PowerLine FL。 螺旋图案是“即时”切割的,即在当管子不断高速移动时。 在这个过程中,每次切割开始时都会精确地触发激光计时。
图 2 显示的是光纤激光加工的效果。 海波管的轴有两种典型样式: 间断式螺旋或所谓的砌砖样式。 砌砖样式由平行的间断切口组成,类似于砖墙上的石头。 典型的海波管长约 1.5 米,使用动态切割程序可以非常快速地处理海波管的较长部分。 该样品的周期时间仅为 35 秒。
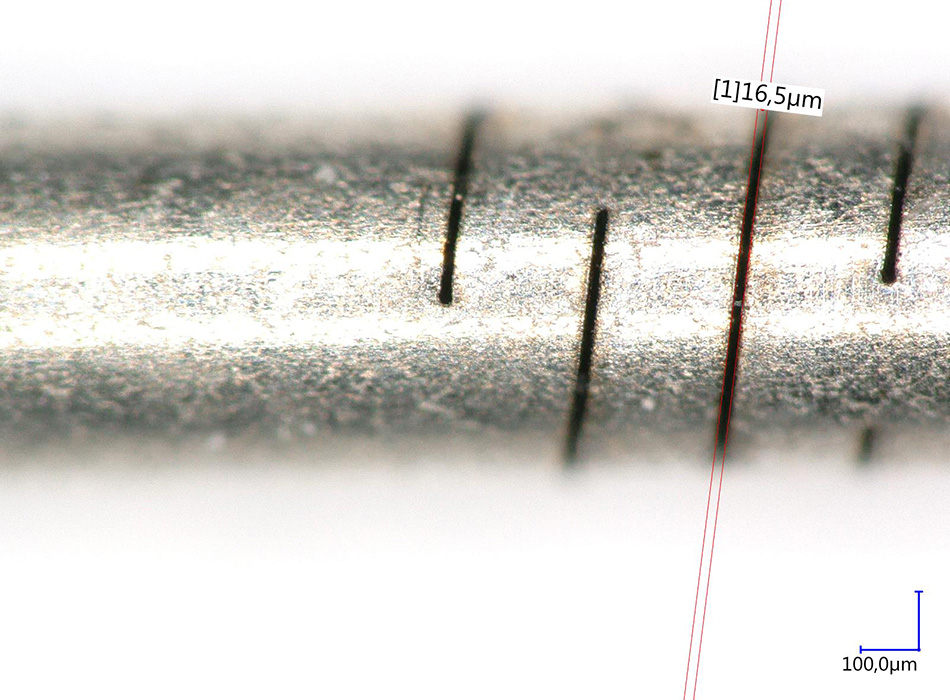
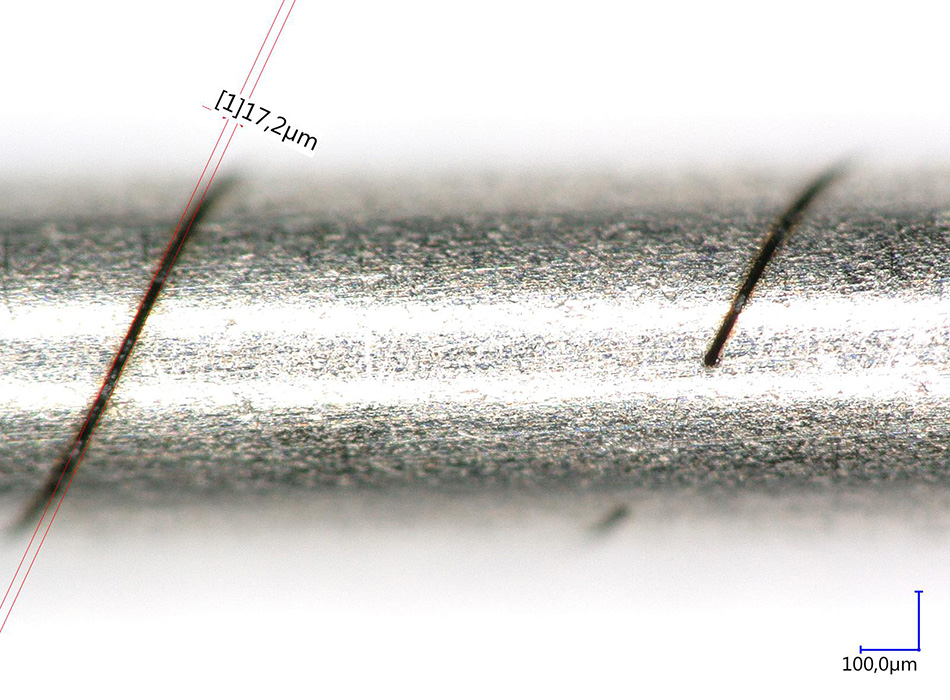
图 2:相干公司 PowerLine FL 光纤激光器以砖砌图案(左)或断续螺旋(右)进行动态切割,切口宽度小于 20 µm。
易于使用的即时激光切割软件
相干公司 StarCut Tube 的用户界面专为轻松加工小批量和大批量医疗器械产品而开发。 Cagila 软件经过优化,可轻松编程处理程序。 为了加快工作流程,其中集成了一些附加功能,例如 "Strobe" 功能。 此功能支持在管材切割过程中自动生成断续螺旋设计或砖砌图案。
"Strobe" 是 StarCut Tube 系统的附加功能,可实现激光的“即时”触发,而不会产生导致穿孔的延迟。 触发信号输出与旋转轴位置同步生成。 因此,激光器的开关命令延迟和抖动都降至了极低的水平。 可以使用基于表格的输入(参见图 3)或从导入的 CAD 数据生成螺旋或砖砌设计的几何形状。 然后就可以自动加工几何形状。 可以纳入后处理功能,例如在定义距离后自动重新夹紧,以及开始后或最终切断位置之前添加额外的弯头。
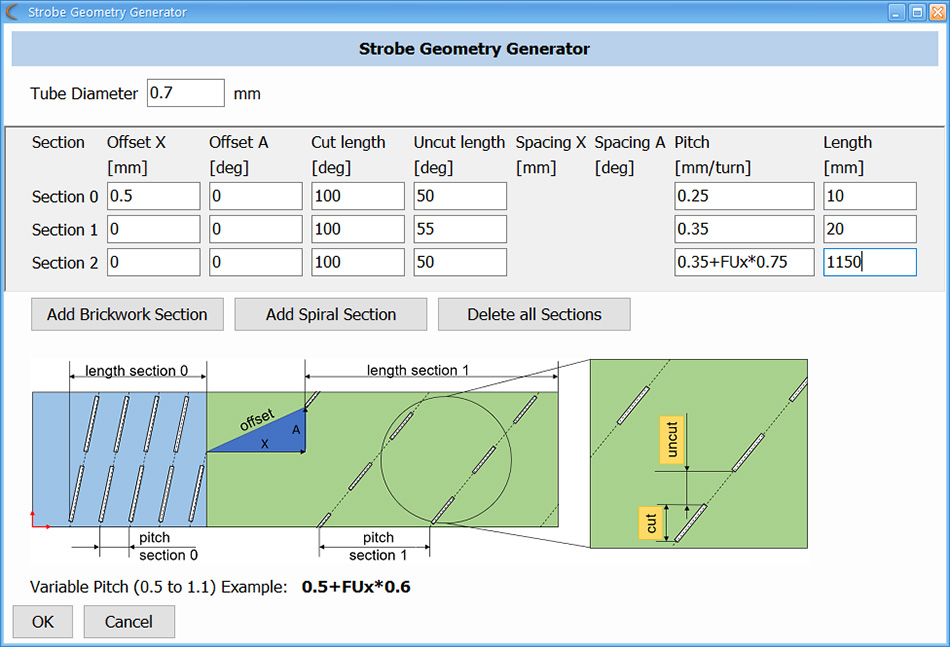
图 3:控制软件中的频闪几何形状生成器可以非常轻松地生成螺旋或砖砌结构。
“Strobe 是 StarCut Tube 系统的附加功能,可实现激光的“即时”触发,而不会产生导致穿孔的延迟。”
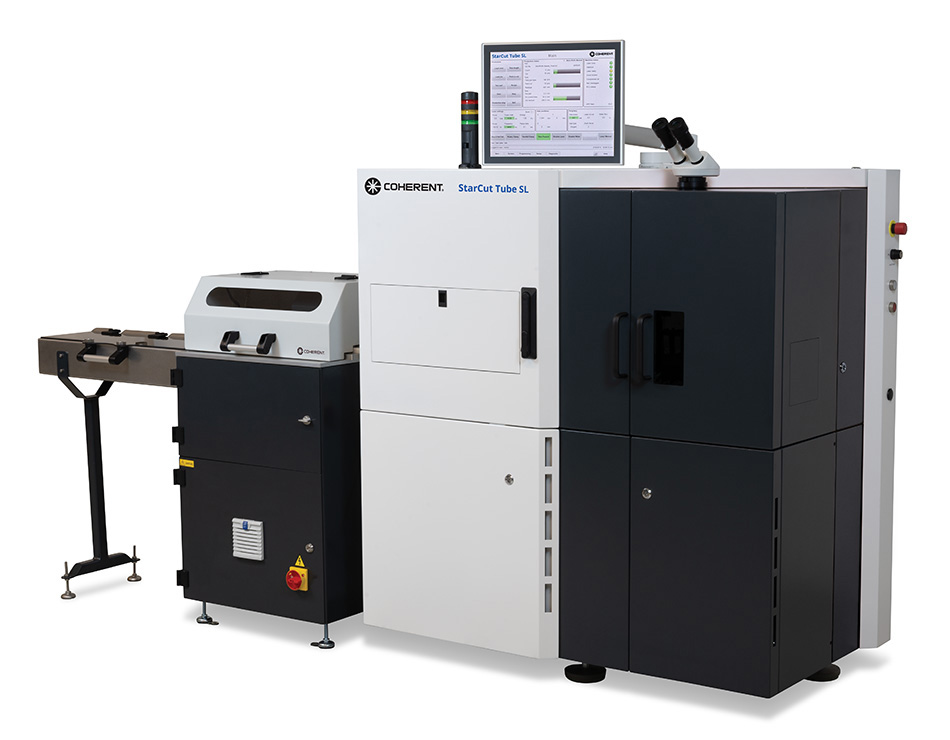
图 4: 相干公司 StarCut Tube SL 可以配备光纤或飞秒激光器,且在市场同类产品中占用空间最小 (2,200 mm x 760 mm)。 可配备多个进料和卸料模块,实现全自动加工。
“......飞秒激光加工的产品的边缘质量非常好,通常不需要进行电解抛光等后处理。 ”
占地面积小的自动化加工
医疗器械通常在成本高昂的洁净室中制造。 相干公司 StarCut Tube SL 在同类激光机中占用空间最小,最大限度减少了使用的宝贵洁净室空间。
StarCut Tube 可以配置为手动加工和自动加工,并且可以配备光纤激光器、飞秒激光器或同时配备两者。 可以添加多个进料器和卸料器模块,以获得全自动解决方案。 例如,借助 StarFeed S,机器可以自动装载外径小至 0.3 mm 的取栓导管等导管。其他导管装载模块可容纳的直径范围为 1 mm 至 20 mm、长度为 3 m,实现了全自动的无人值守生产。
StarCut Tube 可以采用相干公司的 PowerLine FL 激光器,其可调节脉冲宽度为 10-50 微秒,或者采用极为先进的 USP 激光器,相干公司的 Monaco,其脉冲宽度小于 350 飞秒。 光纤激光器非常适合切割较厚材料和管材,因为在切割这类材料时,速度非常重要。 飞秒激光器更适合切割极薄部件或精密部件,对于这些部件而言,表面光洁度非常重要,并且必须避免热副作用。
激光加工精度优于+/- 5 µm。 事实上,飞秒激光加工的产品的边缘质量非常好,通常不需要进行电解抛光等后处理。 该机器可以处理管状基材(直径最大为 30 mm)和平板基材,因此具备更高的实用性和价值。 该机器可进行 2 轴、3 轴或 4 轴作业。
该软件经过优化,易于操作,并可以实现快速加工。 不同操作员可以根据其熟练程度获得不同的访问权限。 工艺和工件参数可以记录,以便进行追溯。 在混合系统中,机器可以在使用一个 CNC 文件的同一作业中的两个激光器之间进行切换。 对于全自动加工,有一个专用模块可用于自动发短信;每当出现问题或工作完成时,它都会向操作员发送一条短信。
总结
相干公司的 StarCut Tube 能够极大提高加工灵活性且占用空间小。 在需要时,可以通过使用多功能软件和以机械方式集成不同激光源,实现高精度和高产量。 该设备专为小批量和大批量医疗器械部件的自动化生产而设计,可以提供自动进料和下料选件。
相干公司的应用专家汇集了超过 25 年的医疗产品制造专业知识。 客户可以通过不同的方式受益于这种经验。 例如,他们可以寄送样品进行测试和工艺开发。 我们为从入门到专业技能水平的操作员提供定期培训,以便分享专业知识。