ERFOLGSGESCHICHTE EINES KUNDEN
Brillenhersteller sieht bessere Ergebnisse mit Laserschweißen
Die Herausforderung
Der österreichische Premium-Brillenhersteller Silhouette International behauptet seinen Wettbewerbsvorteil durch die Herstellung von Brillen, die überragenden Komfort und Funktionalität sowie ein stilvolles Erscheinungsbild bieten. Ihre nur 1,8 Gramm schweren „Titan Minimal Art“-Fassungen (TMA) waren die ersten schrauben- und scharnierlosen Brillen aus Titan, und der Erfolg dieses Produkts hat Silhouette International dazu motiviert, den scharnierlosen Ansatz auf viele andere Designs auszuweiten. Diese Konstruktion stellt jedoch mehrere Herstellungsherausforderungen, einschließlich der Notwendigkeit, eine Vielzahl von Materialien wie Titan und andere spezielle Legierungen zu verbinden. Und diese Fugen müssen ästhetisch ansprechend sein, d.h. sie sind optisch nicht erkennbar und bewirken auch keine spürbare Strukturveränderung. Schließlich müssen die Gelenke stark und sehr flexibel sein und die Fähigkeit haben, viele, viele Male ohne Formänderung oder Verschlechterung der mechanischen Festigkeit zyklisch gefaltet und geöffnet zu werden. Das traditionelle Widerstandsschweißen hat in all diesen Bereichen Mühe, seine Leistung zu erbringen.
Die Lösung
Das Laserschweißen ist ein etabliertes Verfahren, das die Grenzen des Widerstandsschweißens überwindet. Das Laserschweißen für diese Präzisionsanwendung in der Serienfertigung kosteneffektiv umzusetzen, erforderte jedoch einige technische Innovationen. Eine Verbesserung, die sich für Silhouette International als entscheidend erwiesen hat, ist die Verwendung von „Beam Wobble“, d.h. einer schnellen Bewegung des Balkens sowohl entlang als auch senkrecht zur Schweißnaht. Coherent hat eine fortschrittliche Implementierung der Strahlbewegung namens SmartWeld entwickelt, die eine flexiblere und präzisere Steuerung der vom Laser erzeugten Wärmeverteilung ermöglicht. Diese beinhaltet komplexe Strahlmuster, einschließlich Kreise, Ellipsen oder sogar Zickzacklinien. SmartWeld verbessert die Schweißqualität und Prozesskonstanz und kann auch größere Spaltweiten in den Schweißteilen überbrücken. Dies reduziert die Anpassungstoleranzen und Anforderungen, was die Produktion beschleunigt und die Kosten senkt.
Das Ergebnis
Silhouette International installierte ein automatisiertes Coherent MPS Rotary Schweiß-, Schneid- und Bohrsystem, das eine 200-W-Faserlaserquelle und eine Scanneroptik enthält. Insgesamt wurden die Werkzeug- und Fertigungskosten gesenkt, indem mehrere Prozessschritte in einer Maschine ausgeführt werden konnten, was zu verbesserten Energieeinsparungen und Produktivität führte. Außerdem hat der Einsatz von SmartWeld eine verbesserte Schweißnahtqualität, insbesondere Verbindungen mit höherer Festigkeit (aufgrund des geringeren Wärmeeintrags in das Teil) sowie einer verbesserten Elastizität hergestellt. Der MPS Rotary unterstützt auch die Notwendigkeit des Unternehmens, die Markteinführungszeit für neue Designs sowie begrenzte Losgrößen (typischerweise 150–300 Stück) zu verkürzen.
„Der Wechsel vom Widerstandsschweißen zum Laserschweißen war ein enormer Erfolg, der zu einer Gesamtkosteneinsparung von etwa 80 % führte. Und die verbesserte Präzision und Wiederholbarkeit waren entscheidend dafür, dass wir modernste Brillenfassungen erfolgreich in die Produktion einbringen können.“
— David Illitz, Prozessleiter Rohteilfertigung Silhouette International Schmied AG
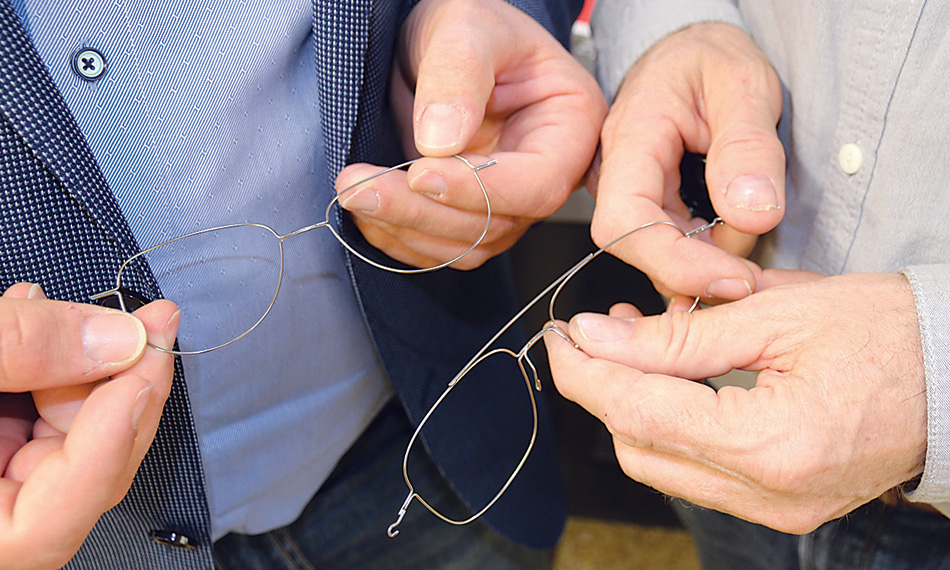