ERFOLGSGESCHICHTE EINES KUNDEN
Der bessere Weg, Platin zu schneiden
Dank seines hohen Schmelzpunktes ist Platin das Material der Wahl für Hochtemperaturprozesse. Ein moderner Faserlaser ist das beste Tool zum Schneiden von Platin, mit einer fast 100%igen Materialausnutzung.
Platin ist ein faszinierendes Material. Es ist genauso selten wie Gold, aber wegen seines hohen Schmelzpunktes viel schwieriger zu bearbeiten. Der Durchbruch in der Platinverarbeitung wurde 1856 von dem Hanauer Chemiker und Apotheker Wilhelm Carl Heraeus erzielt. Nach vielen Experimenten fand er ein Verfahren, bei dem größere Mengen Platin geschmolzen und mit einem Knallgasbrenner verarbeitet werden konnten.
Aus dem von ihm gegründeten Unternehmen ist inzwischen der Heraeus-Konzern geworden, ein internationaler Konzern mit einem Umsatz von 31 Milliarden Euro. Der Konzernbereich Edelmetalle des Heraeus-Konzerns ist einer der größten Edelmetalldienstleister der Welt. Auch heute noch wird Platin am Standort Hanau verhüttet und zu vielen verschiedenen Produkten wie Blechen oder Draht verarbeitet.
Der Markt boomt – und braucht Platin
Thomas Link ist seit 17 Jahren bei Heraeus und begann als Vorarbeiter in der Produktion. Derzeit ist er im Bereich der Verfahrenstechnik für die Beschaffung von Ausrüstung und Prozessunterstützung zuständig. „Wir verarbeiten hauptsächlich Platinblech zu anspruchsvollen Produkten.“
Seit mehr als 160 Jahren wird in Hanau Platin verarbeitet. Link sorgt dafür, dass die Prozesse weiterhin den höchsten modernen Standards entsprechen. „Bis vor Kurzem haben wir Komponenten erodiert oder gestanzt, zum Beispiel aus 0,15 mm Platinblech.“ Leider konnte Link in seinem eigenen Produktionsbereich nicht erodieren, und eine Nacharbeit war erforderlich, wenn das Dielektrikum zwischen die Blechschichten geriet. Der gute alte CNC-Stanzer hingegen brauchte immer eine Haltekante, so dass die Ausnutzung des Materials nicht optimal war. Es geht nichts verloren, aber auch das Recycling von Platin ist mit zusätzlichen Kosten verbunden.
Es gab also gute Gründe, das Laserschneiden mit einer ersten Komponente zu versuchen. „Wir begannen mit einer Komponente, die aus drei Teilen bestand, die wir mit dem Laser ausschnitten. Sie werden noch gebogen und geschweißt, dann geht es an den Kunden.“
Beim EDM werden bis zu 50 Blätter übereinander gestapelt. Mit einem Coherent ExactCut 430 Lasersystem werden die Teile aus Blechen mit einer Größe von bis zu 400 x 500 mm geschnitten. Die Anordnung der Schnitte auf dem Blech wird mit der Nesting Tool Software optimiert, was zu einer deutlich verbesserten Materialausnutzung führt.
In der Werkstatt
Zum Zeitpunkt der Erstellung dieses Artikels ist die ExactCut 430 bereits seit sieben Monaten in der Produktion und Link ist begeistert: „Wir bekommen das Material geliefert, es geht zur Maschine, der Arbeiter spannt es ein, schneidet die Teile zu, misst sie und geht dann zum Schweißen über.“ Der Abfall wird erheblich minimiert, und alles geschieht, ohne dass Sie in eine andere Abteilung von Heraeus wechseln müssen. Wie sieht es mit Nacharbeit aus? „Das kommt auch vor, aber es ist eher unbedeutend. Dies sind kleine Partikelablagerungen oder Spritzer. Sie können leicht von Hand entfernt werden, und wir können die Teile noch verwenden.“
Ein weiterer Vorteil beim Schneiden von Edelmetallen mit dem Laser ist, dass das Werkzeug keinen direkten Kontakt mit dem Material hat. Der Laserstrahl schießt sanft durch sie hindurch. In der Schneidbox werden die Partikel aus dem Schneidspalt gesammelt und eins zu eins in den Kreislauf zurückgeführt. Es gibt keine Verunreinigung durch Öl oder Schmutz. Die feinsten Partikel werden in einem Abgassystem aufgefangen. Auch sie werden der Wiederaufbereitung zugeführt. Die Materialausnutzung liegt sogar bei fast 100 %.
Bei der Auswahl eines Anbieters ließ sich Thomas Link Zeit und sprach zunächst mit drei Unternehmen. „Coherent war in der Lage, Muster in sehr kurzer Zeit zu schneiden und lieferte sofort ein passendes Ergebnis.“ Der Preis stimmte und ein Mitarbeiter wurde bei Coherent geschult, so dass er sofort mit der Maschine beginnen konnte.
Mehr Aufgaben für die Maschine
Und wie geht es weiter? „Wir prüfen derzeit, welche Komponenten wir auf dieser Maschine bearbeiten können“, sagt Link. „Es wäre natürlich toll, wenn wir noch größere Formate schneiden könnten.“ Im Moment ist die speziell angepasste Schneidbox die Einschränkung, aber der Projektleiter bei Coherent hat signalisiert, dass dies zu schaffen ist.
Thomas Link denkt auch über die Drehvorrichtung in der Maschine nach: „Das haben wir noch nicht genutzt – wir könnten dort einfache rotationssymmetrische Teile schneiden. Das steht in den nächsten Monaten noch auf der Tagesordnung.“
Alles in allem ist Link sehr zufrieden. Das neue Verfahren spart Zeit und innerbetrieblichen Transport, und die Maschine ist einsatzbereit. Laserschneiden ist sauberer als Stanzen oder Erodieren, und die Materialausnutzung liegt bei 100 %. Wenn Wilhelm Carl Heraeus die modernen Bearbeitungsmethoden von heute sehen könnte, würde er sich sicher darüber freuen.
„Ich war beeindruckt, als ich sah, wie schnell Coherent den Schneideprozess umsetzte und gute Muster lieferte.“
- Thomas Link, Prozessingenieur, Heraeus Precious Metals
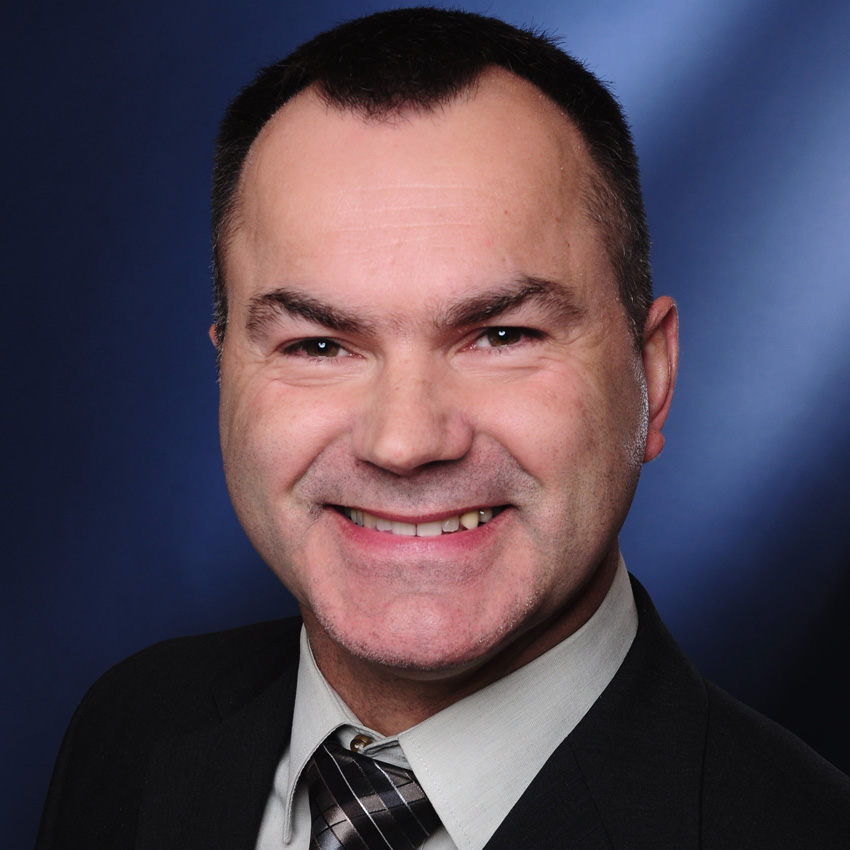
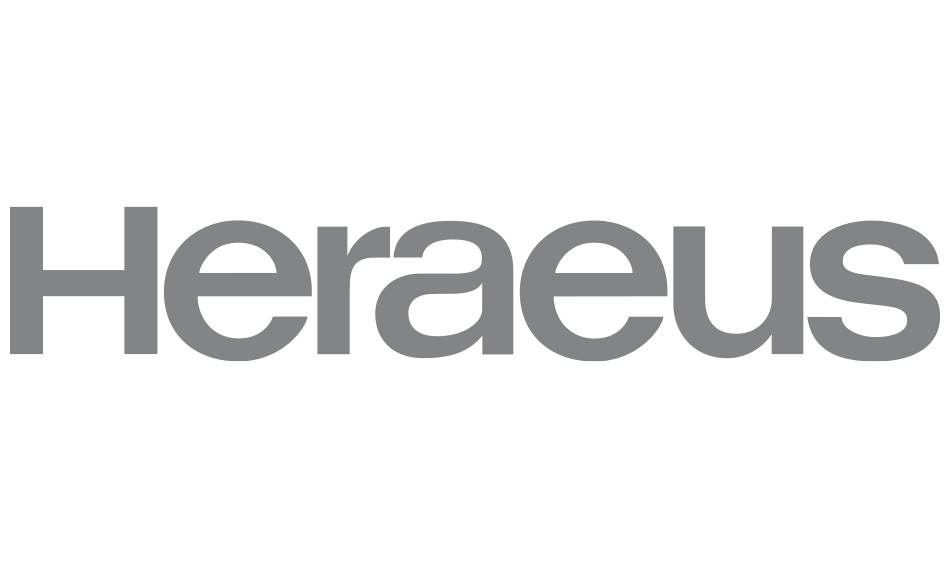
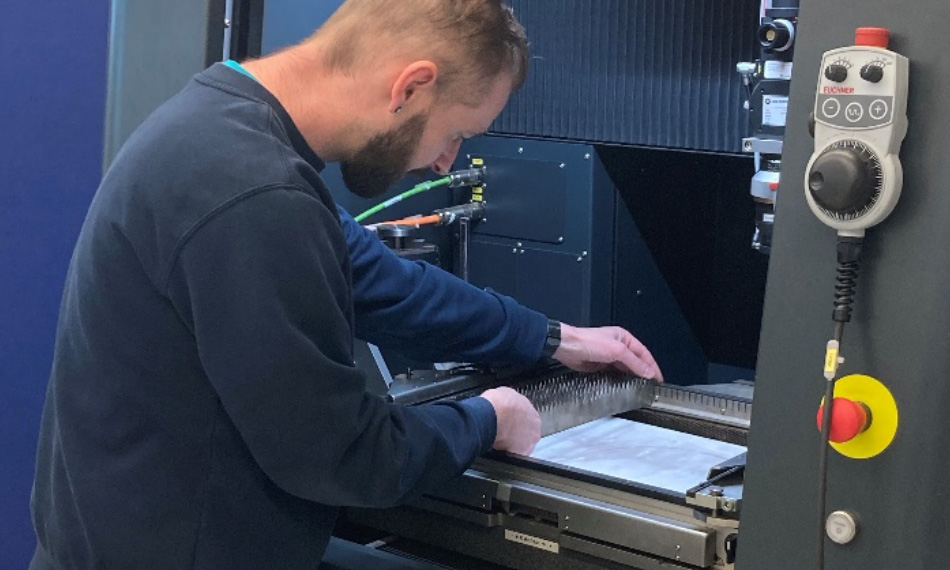
Abbildung 1: Der Übergang vom Erodieren zum Laserschneiden brachte eine Reihe von Vorteilen mit sich, zum Beispiel wird das Material optimal ausgenutzt und der Abfall ist frei von Verunreinigungen.
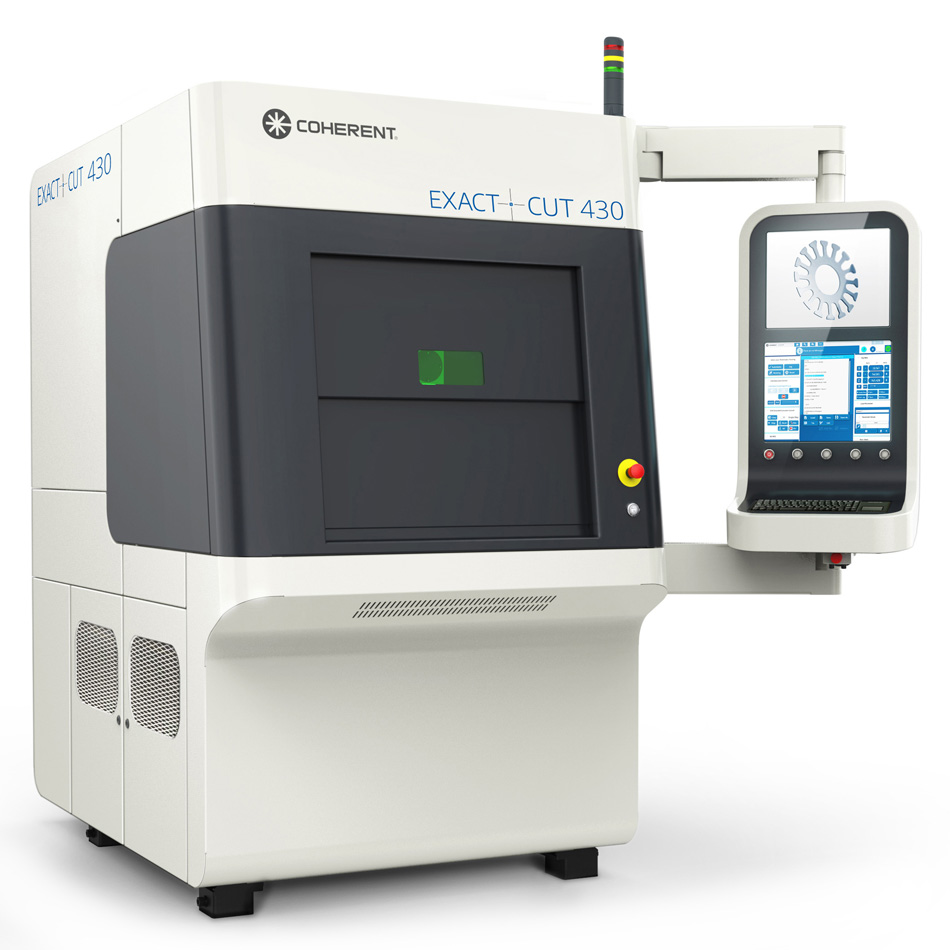
Abbildung 2: Die Coherent ExactCut 430 ist ein Präzisions-Laserschneidsystem für die automatisierte Bearbeitung von dünnen und dicken Metallen und Legierungen sowie spröden Materialien wie Saphir, künstlichen Diamanten und Keramiken.