Faserlaser: Warum wir das Schweißen in der Elektromobilität mit Finesse und nicht mit roher Gewalt angehen
Der Erfolg bei den schwierigsten Schweißaufgaben in der Automobil- und Elektromobilitätsbranche erfordert eine präzise Kontrolle darüber, wie die Laserleistung auf das Werkstück übertragen wird.
26. Oktober 2021 von Coherent
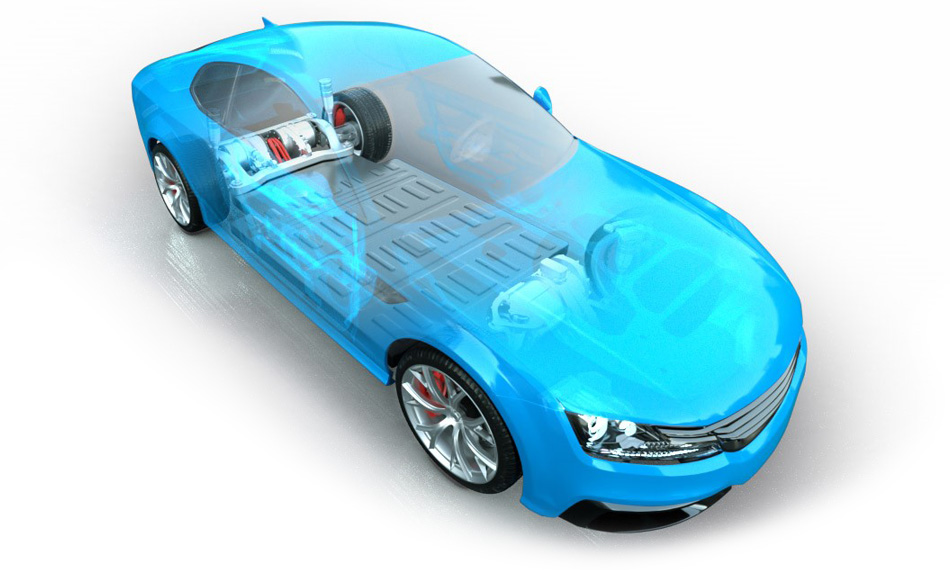
Der Einsatz von Faserlasern in der Automobilproduktion ist eine große Erfolgsgeschichte – und sie werden für zahlreiche Schweiß- und Schneidanwendungen eingesetzt, darunter Rohkarosserien, Anbauteile, Antriebsstrangkomponenten und vieles mehr. Das verwundert nicht. Faserlaser bieten mehrere Vorteile gegenüber den meisten bisher eingesetzten Technologien – und zwar sowohl gegenüber solchen mit Laser als auch solchen ohne Laser.
Die Automobilindustrie ist jedoch nach wie vor eine große Quelle der Innovation. Während Hochleistungs-Faserlaser in der Automobilproduktion schon seit einiger Zeit erfolgreich eingesetzt werden, erfordern die kniffligen Schweißprozesse, die jetzt zur Unterstützung der E-Mobilität und des Leichtbaus in Betrieb genommen werden, mehr als nur rohe Leistung und Kraft. Zwar gibt es eine ganze Reihe unterschiedlicher Einzelanwendungen, aber die meisten davon sind in der Regel:
- Sehr dünnes oder hitzeempfindliches Material
- „Schwer“ zu schweißende Materialien wie Aluminium, Kupfer und hochfester Stahl
- Fügen unterschiedlicher Materialien
Um diese anspruchsvollen Aufgaben erfüllen zu können, muss ein Laser vor allem zwei Fähigkeiten bieten. Erstens eine ausreichende Leistung, um den erforderlichen Produktionsdurchsatz zu erreichen. Eine hohe Leistung ist auch erforderlich, um eine angemessene Materialdurchdringung bei der Bearbeitung dickerer Teile zu erreichen. Zweitens die Fähigkeit, die Verteilung der Laserleistung auf der Arbeitsfläche präzise zu steuern – sowohl räumlich als auch zeitlich.
Leistung mit Präzision
Coherent hat den Adjustable Ring Mode (ARM) Faserlaser speziell entwickelt, um sowohl Leistung als auch Präzision zu liefern. Um dies zu erreichen, nutzt der ARM einen doppelten Strahlenausgang – er erzeugt einen zentralen Punkt, der von einem weiteren konzentrischen Ring aus Laserlicht umgeben ist. Die Leistung sowohl des zentralen als auch des Ringspots kann unabhängig voneinander gesteuert und sogar moduliert werden.
HighLight-Faserlaser der FL-ARM-Serie von Coherent sind mit einer Gesamtleistung von bis zu 10 kW erhältlich. Das ist mehr als genug, um praktisch alle kritischeren Fügeaufgaben mit brauchbaren Durchsatzraten auszuführen. Die meisten der empfindlichsten und anspruchsvollsten Produkte benötigen sogar weniger als die Hälfte dieser Menge. Die ARM-Laser von Coherent bieten also die Möglichkeit, ausreichend Laserleistung genau dorthin zu leiten, wo sie benötigt wird, und zwar genau dann, wenn sie benötigt wird.
Ein Beispiel dafür, wie dies funktioniert, ist das Kupferschweißen. Einige Hersteller haben sich beim Schweißen von Kupfer für grüne Laser entschieden, weil diese Wellenlänge von Kupfer besser absorbiert wird als die Infrarotstrahlung eines Faserlasers. Aber das gilt nur bei Raumtemperatur. Sobald Kupfer erwärmt wird, absorbiert es IR-Licht gut, und sobald ein Keyhole vorhanden ist, wird es noch besser. Die geringere Absorption ist sogar ein Vorteil, denn sie ermöglicht eine tiefere Durchdringung des Laserlichts, wodurch dickere Substrate leichter geschweißt werden können.
Das Szenario für das Schweißen von Kupfer mit einem ARM-Laser beginnt also damit, dass nur der Ringstrahl mit Energie versorgt wird, um das Material zu erhitzen, bis es schmilzt. Anschließend wird der Kernstrahl mit hoher Leistung eingeschaltet, um das Keyhole zu erzeugen. Während des Schweißens wird jedoch ein Teil der Leistung im Ring beibehalten, da dies das Keyhole stabilisiert und es weniger turbulent und chaotisch macht. Dies reduziert Spritzer und sorgt für gleichmäßigere Ergebnisse. Wenn der Strahl das Ende der Schweißnaht erreicht, wird die Ringleistung vollständig abgeschaltet und die Kernleistung sanft heruntergefahren, um ein sauberes, gleichmäßiges Ende zu erzeugen.
Dieselbe Fähigkeit – das Heizprofil auf das Material abzustimmen, um die Stabilität und Konsistenz des Keyholes zu maximieren, und die Leistung am Ende der Schweißung hoch- und runterzufahren – bietet ähnliche Vorteile beim Schweißen anderer schwieriger Materialien, wie Aluminium und verzinktem Stahl. Außerdem ermöglicht es das hochpräzise Schweißen von dünnen, empfindlichen oder hitzeempfindlichen Materialien.
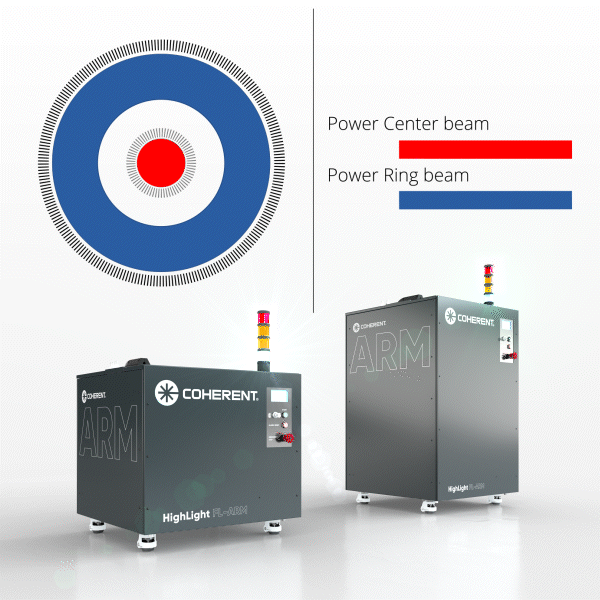
Überwältigende Logik
Einige Hersteller von Faserlasern, die dem ARM von Coherent ähnlich sind, weisen darauf hin, dass bei ihren Produkten 100 % derGesamtleistung in den Kern- oder Ringstrahl verlagert werden können, als ob dies ein Vorteil wäre. Das ist aber nicht der Fall, denn die ganze Magie des ARM-Lasers besteht darin, dass durch die Aufteilung der Leistung zwischen Kern- und Ringstrahl die Wärmeeinbringung in das Teil so verteilt wird, dass bessere Ergebnisse erzielt werden als mit einem einzigen Strahl – genau wie bei dem zuvor beschriebenen Beispiel des Kupferschweißens. Warum sollte man sonst nicht gleich einen normalen (und preiswerteren) Einstrahl-Faserlaser verwenden?
Sie haben auch die Befürchtung geäußert, dass die ARM-Architektur von Coherent nicht „flexibel“ sei. Um diese Behauptung zu verstehen, muss man wissen, dass ARM-Laser in Wirklichkeit aus zwei oder mehr Faserlasermodulen bestehen, von denen jedes entweder in den Kern oder in den Ring eingekoppelt wird, um verschiedene maximale Leistungsverhältnisse zu erreichen. (Im Betrieb kann dann die Leistung in jedem Modul stufenlos von 0 % bis 100 % dieses Maximalwerts eingestellt werden).
Die Anzahl der Module, die in die Kern- und Ringfasern eingespeist werden, wird bei der Herstellung des Systems festgelegt. So kann ein 8-kW-ARM-Laser, der aus vier 2-kW-Modulen aufgebaut ist, mit drei verschiedenen maximalen Leistungsverhältnissen zwischen Kern und Ring konfiguriert werden. Diese sind 6 kW/2 kW, 4 kW/4 kW, oder 2 kW/6 kW. Diese Summen können nachträglich nicht mehr geändert werden, daher die angebliche „Unflexibilität“..”
Die Konfiguration, die für einen bestimmten Kundenlaser verwendet wird, basiert jedoch auf Prozessversuchen, die lange vor dem Kauf des Lasers durchgeführt werden. Diese legen die Leistungsniveaus und Leistungsverhältnisse fest, die für die erfolgreiche Durchführung des Zielprozesses in der Produktion erforderlich sind. Außerdem bieten sie ein ausreichend großes Prozessfenster, um alle Änderungen zu unterstützen, die aufgrund von Prozessschwankungen (z. B. Änderungen bei den Rohmaterialien von Charge zu Charge) erforderlich sind. Darüber hinaus lässt ein bestimmter Laser in der Regel einen sehr großen Spielraum für spätere Änderungen im Prozess selbst. Unterm Strich bedeutet dies, dass die Bestimmung der richtigen Leistung und des richtigen Leistungsverhältnisses zu Beginn des Prozesses spätere größere Änderungen der Laserleistung überflüssig macht.
Die Konkurrenz mag behaupten, dass das Coherent-Produkt kein „echter“ 8-kW-Faserlaser ist. Und Recht behalten – denn es ist ein 8 kW ARM-Faserlaser. Das bedeutet, dass er besser als alle anderen Geräte in der Lage ist, die Laserenergie genau so einzusetzen, dass die besten Ergebnisse für eine bestimmte Aufgabe erzielt werden. Und derselbe 8-kW-Faserlaser wird auch dann noch bessere Ergebnisse liefern, wenn sich Ihre Anforderungen ändern oder weiterentwickeln.
Entdecken Sie die Highlight FL ARM-Serie von Coherent
Verwandte Ressourcen