白皮书
MicroLED – 用于显示屏生产的激光加工
综述
高能量的紫外光激光束在显示屏制造中用于 UVtransfer 工艺,明确地说就是激光剥离技术 (LLO) 和激光诱导前向转移 (LIFT) 以及像素修复。 本文档介绍了最新动态,内容包括:随着芯片尺寸的不断缩小,UVtransfer 如何确保这些巨量转移和放置生产步骤仍将满足未来需求。 此外,该工艺还具有与各种修复方案兼容的优势,可满足预期的实际芯片成品率。
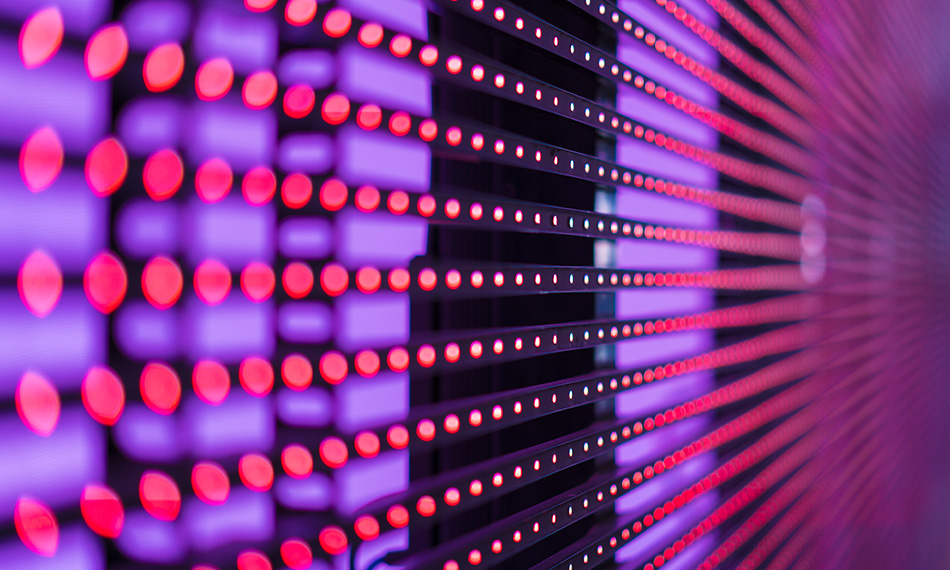
MicroLED – 潜力与挑战
MicroLED (μLED) 是一类新兴设备,具有打造未来显示屏的巨大潜力,十分值得期待。 这些设备通常基于氮化镓 (GaN),目前的尺寸在 20-50 μm 范围内,并有望缩小到 10 μm 或更小。 在蓝宝石晶元生长基板上使用现有 GaN 制造技术,能够以非常高的密度制造具有几微米切割道宽度的 μLED。
微米尺寸、高亮度和高制造密度的结合可以拓展显示屏市场,使其不局限于目前使用的 OLED 和 LCD 技术。 例如,μLED 可用于为 AR/VR 应用创建微型(例如,<1")高清显示屏。 与此同时,它们也可用于室内和室外的超大尺寸显示屏。
使用 µLED 能够经济实惠地制造这种大型显示屏,因为随着芯片尺寸的缩小,给定尺寸的晶圆上生长的芯片数量将大大增加。因此,对于像素间距比芯片尺寸大得多的大型显示屏,影响显示屏成本的主要因素将变为像素总数。 这与 OLED 和其他技术形成对比,这些技术的成本会随总显示面积增加。
但是,在广泛部署 μLED 之前,有几项技术挑战需要克服。 一个重大障碍是要开发一种从蓝宝石生长晶元上剥离芯片的工艺。 另一个障碍是以微米级的精度和可靠性将芯片转移到显示基板上的工艺。 并且,这些工艺必须与维修/更换方案兼容,以解决不可避免的瑕疵芯片问题。 同时,它们必须与自动化兼容并提供高吞吐量,因为 LED 行业的目标是将当前的总体成本降低 20 倍。 而且,该工艺顺应了微型化趋势,而预期会不断缩小的芯片尺寸正对此大有好处,这就不需要为未来尺寸减小而耗费大量资本来改进工具。
“......越来越小的模具将有利于适应这种小型化趋势的工艺。”
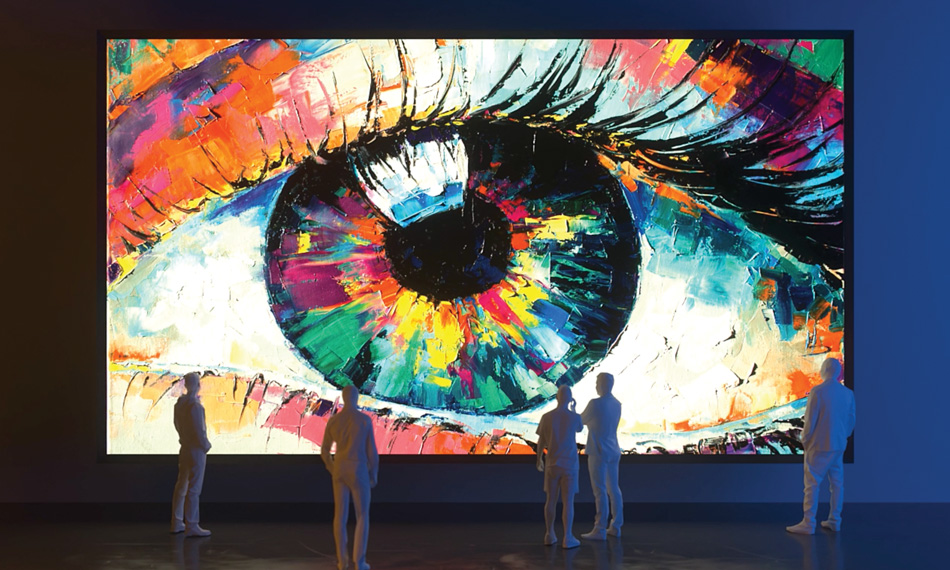
图 1: 大型直视 MicroLED 显示屏的图示
激光加工的背景
具有纳秒脉冲持续时间的高能紫外光激光脉冲用于激光加工,这种工艺有多项独特优势,可以应对这些挑战。 短波长紫外光可以直接烧蚀界面和表面的材料薄层,而不会深入到材料中。 结合较窄的脉冲宽度,这种冷光烧蚀工艺可避免引起热冲击和对底层材料的损坏。 大脉冲能量具有独特的多用途工艺优势,由于光束可用于投射光掩膜,因此每个脉冲可处理数百甚至数千个芯片。 因此,显示屏行业广泛使用这些类型的激光器作为批量生产工具来生产用于 OLED 和高性能 LCD 显示屏的 TFT 硅背板 – 毫无疑问,下一代 μLED 显示屏也会继续采用这一技术。
目前,激光工艺为 μLED 显示屏生产带来的优势包括:
- 激光剥离 (LLO) 将成品 μLED 与蓝宝石生长晶片分离
- 激光诱导前向转移 (LIFT) 将 μLED 从供体移动到基板
- μLED 的激光修复功能可解决产量问题并降低缺陷率
- 准分子激光退火 (ELA) 用于制造 LTPS-TFT 背板
- 按多种的聚合程度进行激光切割
以下是其中一些领域最近取得的重大发展成果。
激光剥离技术 (LLO) 动态
激光剥离技术 (LLO) 可以将成品 μLED 与蓝宝石生长晶元分离,前面的MicroLED 的激光工艺中已经介绍过这一点。 因此,在这里,我们只简要回顾一下 LLO 对蓝色和绿色芯片的主要优势,包括最新的自动对准功能,该功能现已成为开发工具的一部分。
通常将蓝宝石作为最佳生长基板来批量制造 GaN μLED。 但是,随后必须将薄 LED 与蓝宝石分开,以便为垂直结构 LED 创建第二个接触点。 此外,对于下游加工过程而言,蓝宝石体积过于庞大,其厚度是 μLED 芯片的 50 至 100 倍。 这就需要从蓝宝石基板上移走高密度 μLED 并将其转移到临时载体上。
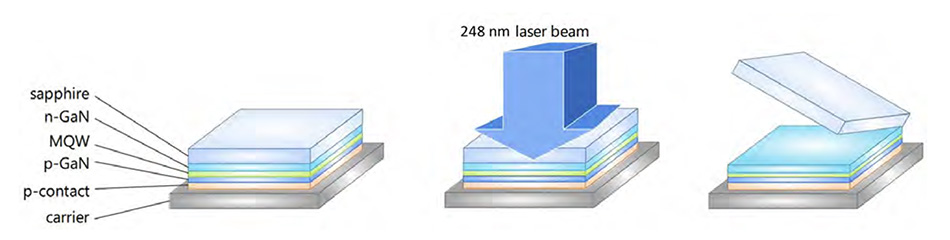
图 2: 用于从蓝宝石晶片上剥离 GaN 膜的 LLO 工艺示意图。
针对 μLED 的 LLO,相干公司开发了 UVtransfer 工艺。 LLO 工艺的工作方式是从后表面(通过透明蓝宝石)照射芯片。 这会烧蚀 GaN 的微小层,产生少量膨胀的氮气,从而释放芯片。 UVtransfer 工艺的 (248 nm) 波长使其还可用于生长于其他种类材料(包括 AlN)的 μLED。
在 UVtransfer 工艺中,将紫外光激光束通过光掩膜投射到蓝宝石晶元之前,会将其形状改变为具有“高顶礼帽”强度波形的矩形光束。 这种均匀的强度可确保在加工区域内的每个点上施加相同的力。 光学器件经过配置,使得每个高能脉冲都会剥离大面积芯片。 我们的 UVtransfer 工艺在 LLO 中应用高能量、紫外光准分子激光脉冲,因此具备这种独特的多用途优势,此优势对于降低批量生产成本将发挥重大作用。 (相干公司的另一个类似系统 UVblade 现在已广泛用于柔性 OLED 的 LLO 中。)
基于准分子的 LLO 系统已经在多个 μLED 试点产品线中运行。 最初,晶元相对于投射(掩盖)光束的运动仅由平移台上的编码器控制。 “芯片上加工”是最近的一项技术进步,也是 UVtransfer 工艺的核心,可以进一步提高对准精度,从而实现更小的芯片和更窄的切割道。
“芯片上加工”还消除了激光线边缘上的芯片被部分照亮的可能性。 在这种情况下,仍然通过平移台上的编码器监视粗略对准。 但是,精细对准是使用闭环的智能视觉系统实现的,该系统使用芯片的棋盘图案使晶元相对于光束对准。 这样可以确保激光场的边缘始终与切割道的中间重合,并且永远不会横穿芯片。
图 3: 在 UVtransfer 工艺中,“芯片上加工”功能可确保激光场的边缘始终与切割道的中间重合。
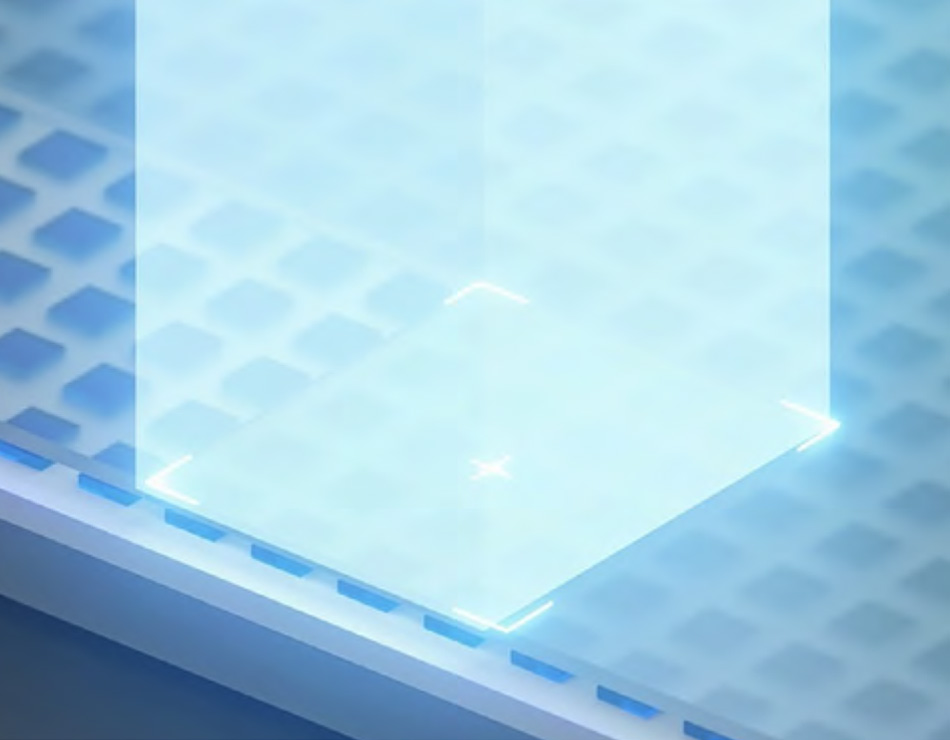
激光诱导前向转移 (LIFT)
UVtransfer 工艺利用激光诱导前向转移 (LIFT) 的原理,也非常适合巨量转移和放置所选芯片。 这个方面的一个关键挑战是巨大的间距差异。 芯片在晶元和转移载体上排列十分紧密,目前的间距约为 1000 dpi。 但根据尺寸和分辨率的不同,显示屏上的间距可能只有 50-100 dpi。 另外,芯片必须混合放置,每个像素位置都要放置红色、蓝色和绿色芯片各一片。
现有的非激光转移方法在所需的分辨率下无法提供必要的吞吐量。 例如,机械拾取和放置方法的速度和放置精度都很有限,因此无法跟上当前的技术趋势。 另一方面,倒装贴片机虽然能够进行高精度贴片(例如,±1.5 μm),但一次只能处理一个芯片。 相比之下,UVtransfer 既可以提供高精度 (±1.5 μm),又可以凭借多用途的特性提供大量吞吐量,一次激光照射可移动并放置数千个芯片。
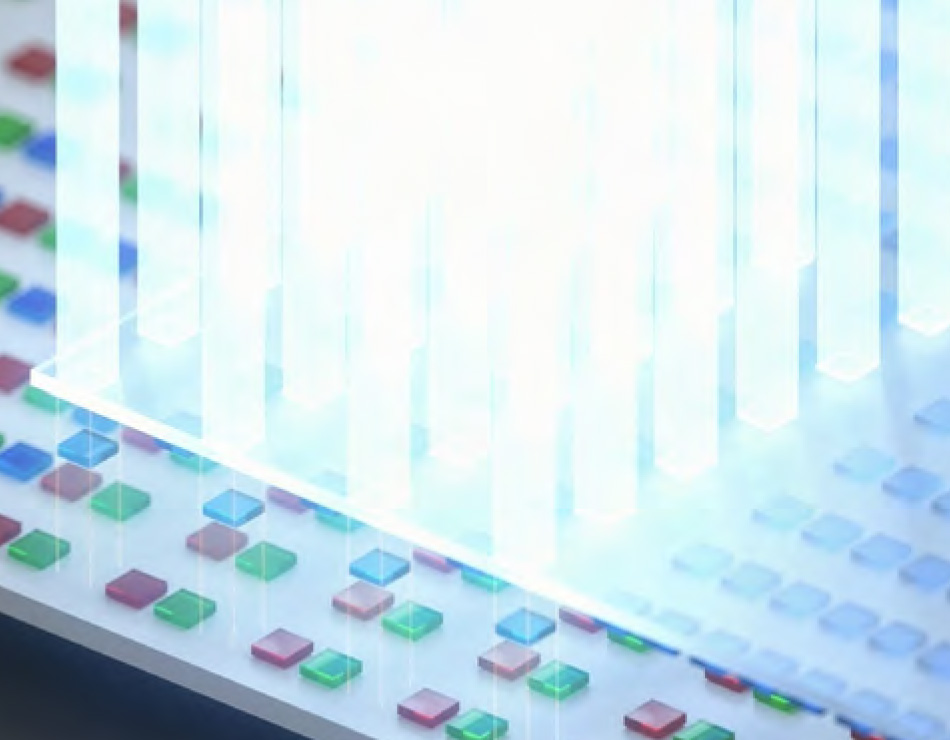
图 4 显示了该方法的工作过程。 LLO 通过动态释放层将芯片保留在临时载体上。 这是一种可大量吸收紫外光的温和粘合剂。 临时载体和芯片与最终载体几乎接触,最终载体通常是已经用 TFT 背板制图并覆盖有粘合层或焊盘的玻璃或柔性面板。 紫外光从载体的背面照射进来。 几乎所有激光能量都被动态释放层吸收,动态释放层因而被蒸发。 由于蒸气膨胀压力而产生的冲击力会将芯片从载体推到最终基板上,理想情况下芯片上不会有任何残留物。
图 4: UVtransfer 对掩膜使用步进扫描工艺,以在显示屏上创建正确的间距。
LLO 工艺同时处理整个区域内的所有相邻芯片,而转移工艺则与此不同,它会将芯片的间距从原始晶片的紧密间距更改为最终显示屏的像素间距。 这就要使用光掩膜,采用每隔 5 个芯片或每隔 10 个芯片才照射一次的模式。 然后,当显示屏的下一个区域平移到位等待芯片填充时,就会对掩膜进行分度,使其相对于临时载体移动一个单位的晶元间距,以便转移新的一列芯片。
LLO 和转移之间的另一个区别是后者涉及到粘合剂的烧蚀,所需激光通量比 III-V 半导体低 5-20 倍。 这种高效率意味着较小的激光功率即可实现高吞吐量。
我们 UVtransfer 工艺还有其他几个特性也对其运作十分关键。 例如,即使安装在载体上的芯片与 TFT 基板之间的间隙接近于零,也必须管理和控制冲力,以成功转移每个芯片,同时确保放置准确且无损坏。 具体而言,必须在整个显示屏上优化力的大小和方向,并保持一致,以便确保传输工艺质量。
要在加工区域高度均匀且一致地转移芯片,就需要高度均匀的激光照射,而这一优势正是相干公司的核心竞争力,正广泛造福于各种应用。 这将形成高度均匀的 2D 场,然后通过光学方式将其重塑为正方形或长宽比较大的矩形,以符合应用需要。 例如,对于 6" 晶元的转移,晶元上的可用区域大约为 100 mm x 100 mm。如图 4 所示,在局部(单个芯片)区域强度均匀,就意味着可以在整个区域内均匀地推动芯片。 因此,力始终是垂直的,不会因光束波形呈高斯分布或倾斜状而引起横向偏移。 在更大的(晶元宽度)范围内具有均匀的光束强度同样重要,因为这样可以确保以相同大小的力推动每个芯片。
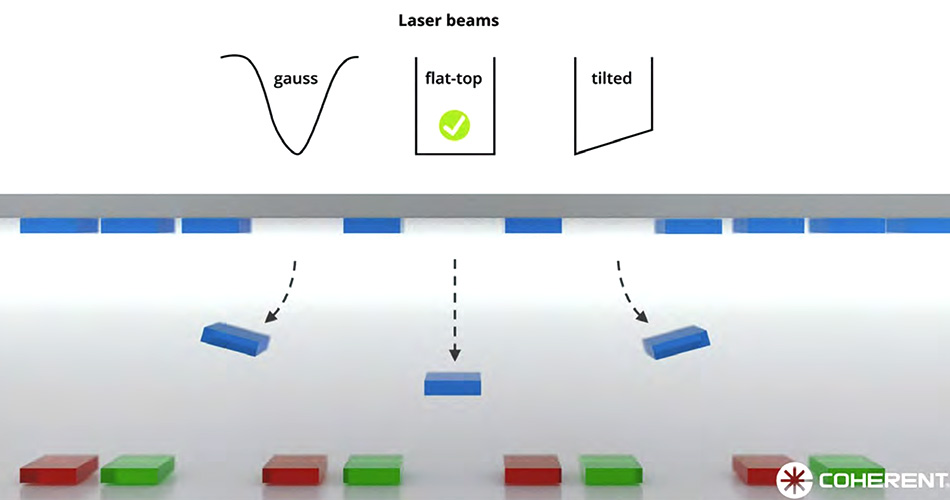
图 5: 高度均匀的“平顶”光束波形对于精确放置至关重要,但对处理规模却没有多大作用。
重要的是,UVtransfer 工艺可以轻松支持比目前试生产更小的芯片(<5 微米)和更狭窄的切割道。 实际上,由于紫外光波长较短,将来可以实现微米级分辨率。 较小的芯片所需的只是一个不同的投影掩膜。
异常芯片的维修/更换
μLED 显示屏要想在市场上获得成功,既需要大幅降低生产成本,又要不遗余力地朝着 100% 良率努力。 若非如此,生产出数亿像素的显示屏将无法实现。 但问题芯片是不可避免的,因此制造商只能采用与维修/更换方案兼容的生产技术平台。 相干公司适用于 LLO 和转移的 UVtransfer 与目前研究中的更换概念兼容。
该工艺的第一步是在晶元上找到并去除缺陷芯片。 但是,这样会在临时载体上留下空缺(原本由缺陷芯片所占据)。 因此,必须在最终基板上重新填充这些空缺。
将该工艺仅应用于选定区域,或仅应用于单个芯片,就可以在 LLO 之前从晶元上去除缺陷芯片。 然后,每个晶元上去除的芯片会形成一张地图,并进一步形成基板上缺失芯片的地图。 可以在巨量转移后通过类似的前向 UVtransfer 工艺分别插入缺失的芯片,只不过此时要使用指定的单束紫外光。 激光功率取决于激光烧蚀的是 III-V 材料还是可蒸发粘合剂。
总结
MicroLED 是一项激动人心的开发技术,可以拓展微型和大型显示屏的性能和应用范围。 毫无疑问,在实现高吞吐量生产之前,有许多障碍需要克服。 但是,使用紫外光激光束的两种多用途工艺已经在试点工厂证明了其强大的功能。 更重要的是,UVtransfer 是完全可扩展的,这使微型化发展趋势能够顺利推进,而无需进行成本高昂的再投资或工艺更换。 客户工艺一旦开发完毕,由于高能量紫外光激光器的可扩展性,这种经过实际考验的解决方案就能轻松地转移到生产线,并符合当今和未来的精度要求。