백서
MicroLED - 디스플레이 생산을 위한 레이저 공정
개요
고출력 자외선 레이저 빔은 디스플레이 제작, 특히 LLO(레이저 Lift-Off)와 LIFT(레이저 유도 순방향 전사) 및 픽셀 수리를 위한 UVtransfer 공정에 사용할 수 있습니다. 이 문서에는 다이 치수가 계속 축소되고 있는 상황에서 UVtransfer로 이러한 대량 전사 및 배치 생산 단계의 미래를 대비할 수 있는 방법을 포함하는 최신 정보가 담겨 있습니다. 그리고 이 공정은 다양한 수리 기법에 사용할 수 있어 예상하는 실제 다이 수율을 맞출 수 있다는 장점도 있습니다.
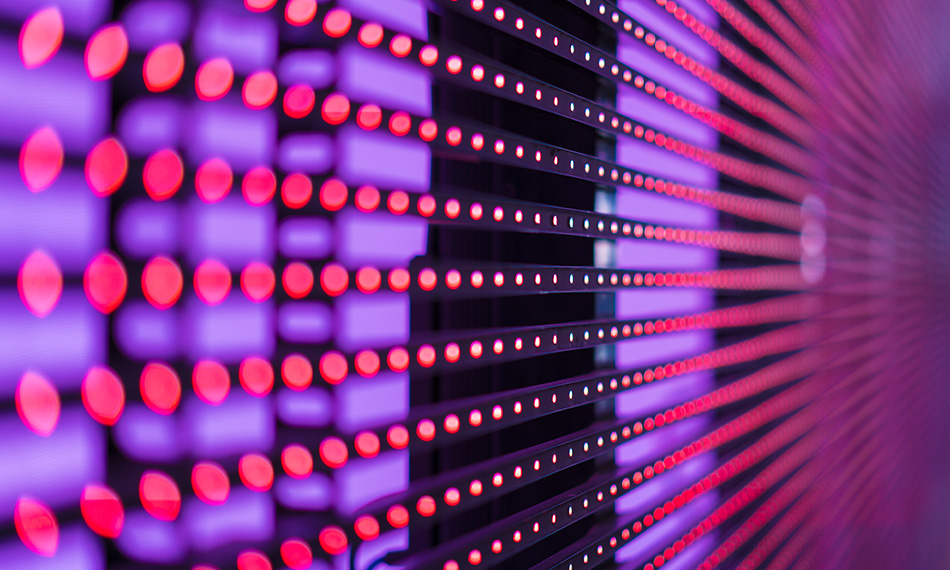
MicroLED - 잠재력과 과제
MicroLED(μLED)는 미래의 디스플레이에 엄청난 잠재력을 선사할 수 있는 새로운 유형의 놀라운 소자입니다. 일반적으로 질화 갈륨(GaN)을 기반으로 하는 이 소자는 현재 그 치수 범위가 20-50μm이나, 10μm 이하로 축소될 것으로 예상됩니다. 사파이어 웨이퍼 성장 기판에 기존 GaN 제조 기술을 사용하면, 스트리트 폭이 몇 미크론인 밀도가 매우 높은 μLED를 만들 수 있습니다.
미크론 치수, 고휘도, 높은 제조 밀도가 결합되면 현재 OLED와 LCD 기술로 구현되는 디스플레이 시장이 확대될 수 있습니다. 예를 들어, μLED는 AR/VR 용도에 필요한 소형(예: <1") 고선명 디스플레이 제작에 사용할 수 있습니다. 그리고 크기 스펙트럼의 반대쪽 끝에서는 실내와 실외에서 사용되는 초대형 디스플레이를 지원합니다.
이러한 대형 디스플레이를 µLED로 제작하면 경제성이 좋을 수 있는데 그 이유는 다이 크기가 작아져 주어진 크기의 웨이퍼에서 성장하는 다이의 수가 상당히 늘어나기 때문입니다. 따라서 픽셀 피치가 다이 치수보다 훨씬 더 큰 대형 디스플레이는 전체 픽셀 수가 디스플레이의 원가를 높이는 주요 요인이 됩니다. 이는 전체 디스플레이 면적에 따라 비용이 증가하는 OLED 및 기타 기술과는 대조를 이룹니다.
그러나 μLED가 널리 보급되려면 먼저 극복해야 할 몇 가지 기술적 과제가 있습니다. 넘어야 할 주요 장애 요소 하나는 사파이어 성장 웨이퍼에서 다이를 분리하는 공정을 개발하는 것입니다. 또 하나는 미크론 수준의 정밀도와 신뢰도로 디스플레이 기판에 다이를 전사하는 공정입니다. 그리고 이러한 공정은 불가피하게 발생하는 다이 결함 문제를 해결하는 수리/교체 기법과도 호환되어야 합니다. 동시에 LED 산업의 목표가 현재 전체 비용을 최대 20배까지 절감하는 것이기 때문에 자동화와 호환되고 대량 생산이 가능해야 합니다. 게다가 다이 크기가 계속 작아질 것으로 예상됨에 따라 이런 소형화 추세에 맞출 수 있어 크기가 축소될 때마다 자본을 많이 들여 설비를 교체할 필요가 없는 공정이 선호될 것입니다.
"...다이 크기가 계속 작아질 것으로 예상됨에 따라 이런 소형화 추세에 맞춰진 공정이 선호될 것입니다."
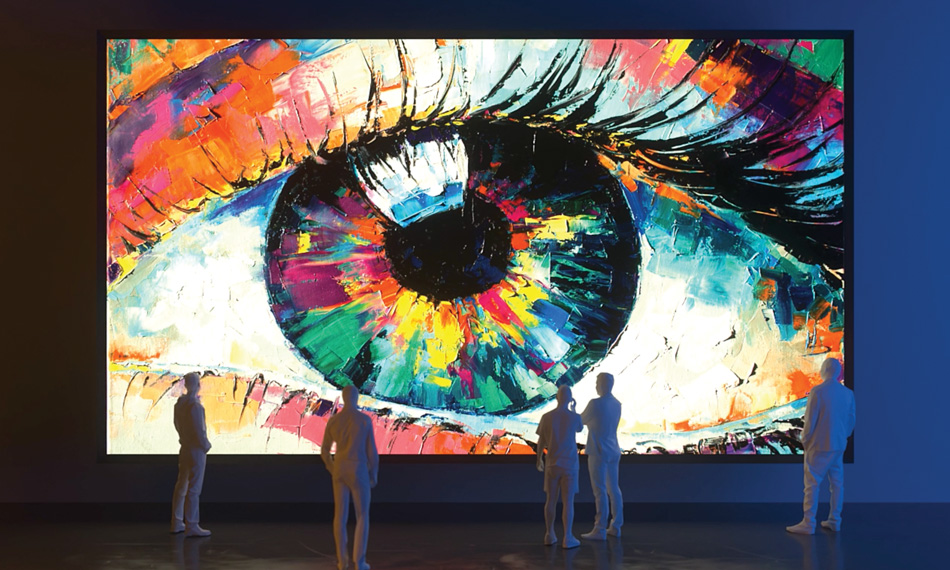
그림 1: 대형 직시형 MicroLED 디스플레이.
레이저 가공 상황
나노 초 펄스 지속 시간의 고출력 자외선 레이저 펄스를 기반으로 하는 레이저 가공은 이러한 문제를 해결할 수 있는 여러 장점을 지니고 있습니다. 단파장 UV 광선은 재료 깊숙이 침투하지 않고 경계면과 표면에서 재료의 얇은 층을 직접 제거할 수 있습니다. 펄스 폭이 짧은 이 저온 광융제 공정은 열 충격 유발에 의한 하부 재료의 손상을 방지합니다. 그리고 펄스 에너지가 크다는 것은 다중 공정에 유리한데, 그 이유는 빔을 이용해 포토마스크를 투영하여 각 펄스마다 수백, 수천 개의 다이를 가공할 수 있기 때문입니다. 따라서 이런 유형의 레이저가 디스플레이 산업에서 OLED와 고성능 LCD 디스플레이의 TFT 실리콘 백플레인을 만드는 대량 생산 도구로 널리 사용되는 이유가 여기에 있습니다. 당연히 이 기능은 차세대 μLED 디스플레이에도 계속 사용될 것입니다.
현재 레이저 가공은 μLED 디스플레이 생산에서 몇 가지 기회를 제공합니다.
- 완성된 μLED를 사파이어 성장 웨이퍼에서 분리하는 LLO(Laser Lift-Off: 레이저 Lift-Off)
- μLED를 도너에서 기판으로 옮기는 LIFT(Laser Induced Forward Transfer: 레이저 유도 순방향 전사)
- 수율 문제와 결함률을 해결하기 위한 μLED 레이저 수리
- LTPS-TFT 백플레인을 제작하는 ELA(Excimer Laser Annealing: 엑시머 레이저 어닐링)
- 다양한 응집 수준의 레이저 절단
이러한 일부 영역에서 최근의 주요 개발 사항은 다음과 같습니다.
LLO(레이저 Lift-Off) 업데이트
완성된 μLED를 사파이어 성장 웨이퍼에서 분리하는 LLO(레이저 Lift-Off)는 이전에 마이크로 LED의 레이저 가공에서 설명한 적이 있습니다. 따라서 여기에서는 현재 발달 중인 조형 기술에 속하는 최신 자동 정렬 기능을 포함해 청색 및 녹색 다이용 LLO의 주요 이점을 간략히 살펴봅니다.
벌크 GaN μLED는 일반적으로 최적의 성장 기판인 사파이어로 제작됩니다. 그러나 얇은 LED는 이후 수직 LED 작동을 위한 두 번째 접점을 생성할 수 있도록 사파이어에서 분리해야 합니다. 게다가 사파이어는 후속 처리 공정에서 μLED 다이 두께의 50-100배로 가공하기에는 부피가 너무 큽니다. 따라서 사파이어 기판의 고밀도 μLED를 이동하여 임시 캐리어로 옮겨야 합니다.
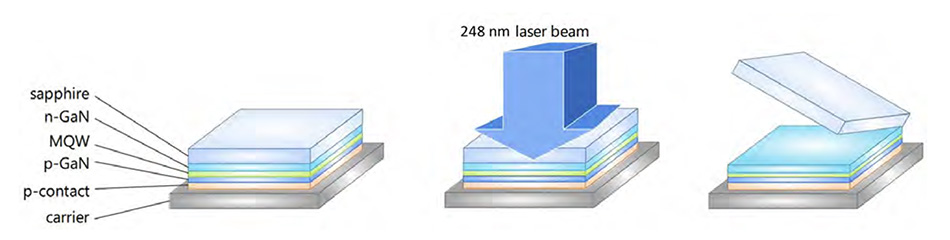
그림 2: 사파이어 웨이퍼에서 GaN 필름을 박리하는 LLO 공정 개략도.
Coherent는 μLED의 LLO를 위해 UV 전사 공정을 개발했습니다. LLO 공정은 후면에서 다이를 조사하는 방식으로(투명 사파이어를 통해) 작동합니다. 이 공정에서 미세한 GaN 층을 제거하는데 이때 소량의 팽창 질소 가스가 생겨 다이를 분리합니다. Coherent의 UV 전사 공정의 (248nm) 파장은 AIN을 포함하는 몇 가지 다른 재료와 같이 성장한 μLED에도 사용할 수 있습니다.
UVtransfer 공정에서는 UV 레이저 빔의 모양이 “탑햇(top hat)" 세기 프로파일을 갖는 직사각형 빔으로 바뀐 후에 포토마스크를 통해 사파이어 웨이퍼에 투영됩니다. 이 강도가 균일해 공정 필드 내의 모든 지점에 동일한 힘이 적용됩니다. 면적이 넓은 다이가 각각의 고출력 펄스로 들어 올려지도록 여러 광학장치가 구성되어 있습니다. 이러한 다중 이점은 고출력, UV 엑시머 레이저 펄스를 기반으로 하는 UVtransfer 공정을 사용하는 Coherent LLO에만 있으며, 대량 생산 시 비용 절감을 구현하는 중요한 요인이 될 것입니다. (이와 유사한 UVblade라고 하는 Coherent 시스템이 현재 플렉스 OLED용 LLO에 널리 사용되고 있습니다).
엑시머 레이저 기반 LLO 시스템은 이미 여러 μLED 파일럿 제품 라인에서 운영되고 있습니다. 처음에는 투영된(마스킹된) 빔에 따른 웨이퍼 동작은 변환단에서 인코더에 의해서만 제어되었습니다. "온다이 가공"은 최신 고급 기술로서, 현재 정렬 정밀도를 더 개선하여 다이 크기를 줄이고 스트리트 폭을 좁힐 수 있는 UVtransfer 공정의 핵심 기술입니다.
"온다이 가공"은 레이저 라인의 가장자리에 다이가 부분적으로 투영될 가능성도 없애줍니다. 이 경우에는 변환단에서 인코더가 개략적인 정렬 상태를 계속 모니터링합니다. 그러나 미세 정렬은 다이의 바둑판 패턴을 사용하여 빔에 맞춰 웨이퍼를 정렬하는 폐쇄 루프, 스마트 비전 시스템으로 구현됩니다. 따라서 레이저 필드의 가장자리가 항상 스트리트 중앙과 일치하고 다이를 넘어가는 일이 없습니다.
그림 3: UVtransfer 공정에서 온다이(on-die) 가공 기능은 레이저 필드의 가장자리를 항상 스트리트 중앙에 맞춰줍니다.
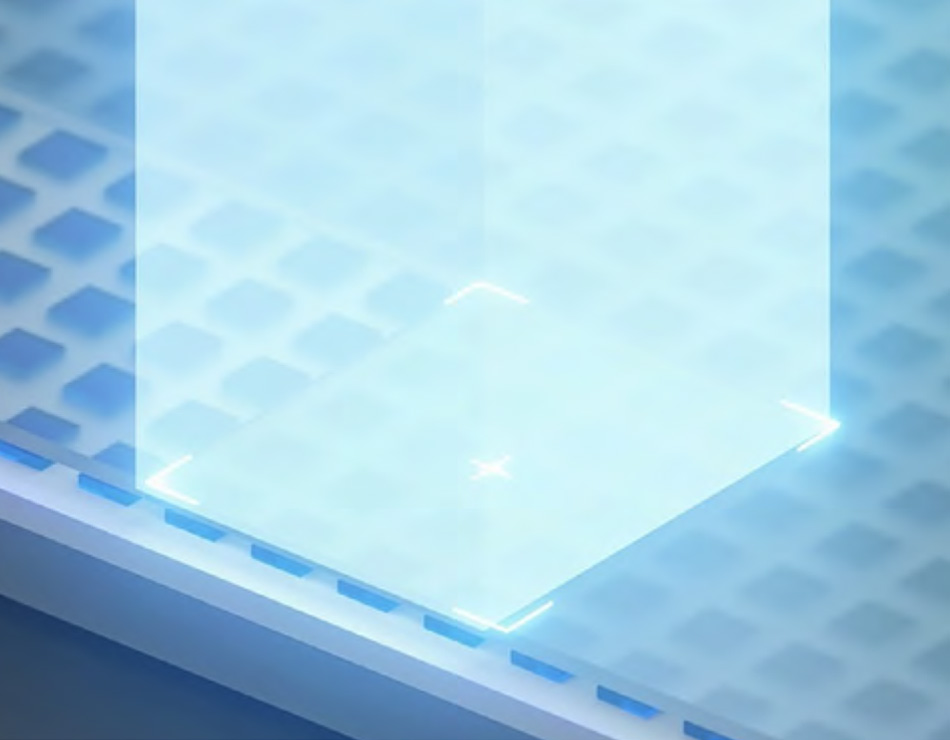
LIFT(레이저 유도 순방향 전사)
UVtransfer 공정은 LIFT(레이저 유도 순방향 전사) 원리를 사용하는 다이의 대량 전사와 배치에도 적합합니다. 여기에서 중요한 과제는 극적인 피치 차이입니다. 현재 웨이퍼와 전사 캐리어에는 다이가 약 1,000dpi의 피치로 밀집되어 있습니다. 그러나 크기와 해상도에 따라 디스플레이의 피치는 50-100dpi도 될 수 있습니다. 그리고 다이를 비월 방식으로 주사하여 각 픽셀 위치에 적색, 청색 및 녹색 다이가 배치되어야 합니다.
기존 비-레이저 전사 방식은 필요한 해상도로 필요한 처리량을 구현할 수 없습니다. 예를 들어, 기계식 픽 앤 플레이스(pick and place) 방식은 속도와 배치 정확도가 제한적이므로 현재 기술 궤적을 지원하지 못합니다. 한편 플립 칩 본더는 고정확도 배치(예: ± 1.5μm)가 가능하지만 한 번에 하나의 다이만 처리할 수 있습니다. 이와 달리 UVtransfer는 높은 정확도(± 1.5μm)와 대량의 다중 처리를 모두 구현할 수 있어, 한 번의 레이저 샷으로 수천 개의 다이를 움직이고 배치할 수 있습니다.
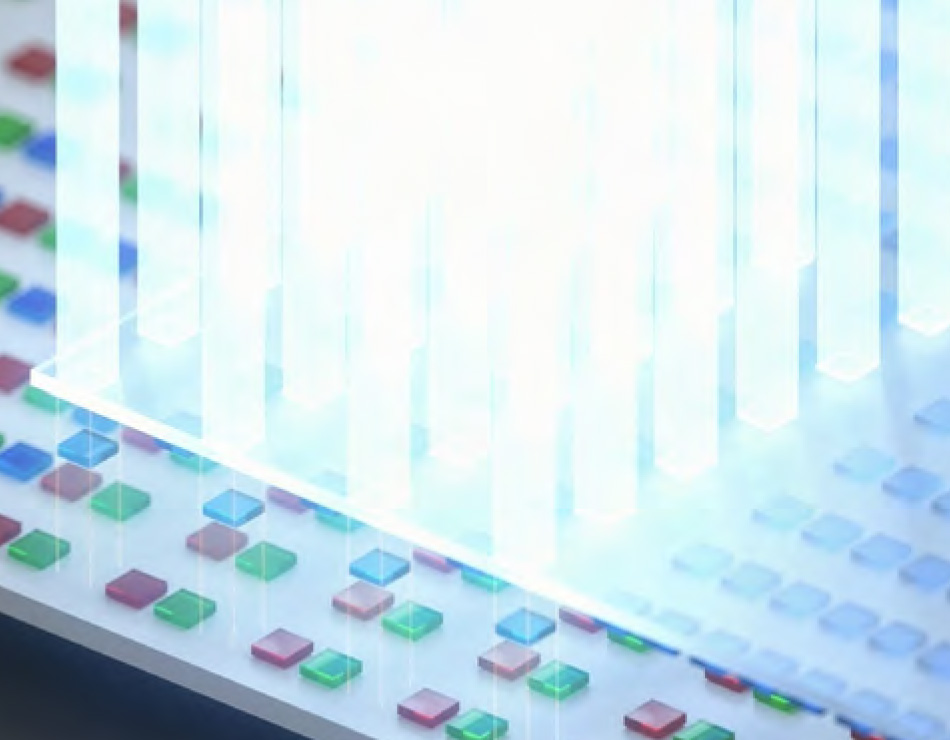
그림 4는 이 방식의 작동 방식을 개략적으로 보여줍니다. LLO는 동적 이형층을 통해 다이를 임시 캐리어에 부착한 상태로 둡니다. 이것은 자외선을 확실하게 흡수하는 접착제입니다. 임시 캐리어와 다이는 최종 캐리어에 근접촉 상태로 배치되는데, 일반적으로 최종 캐리어는 TFT 백플레인으로 이미 패턴화되어 있고 결합층 또는 패드로 덮여 있는 유리 또는 플렉스 패널입니다. 자외선은 캐리어 뒷면에서 비춰집니다. 거의 모든 레이저 에너지는 동적 이형층에 흡수되어 기화됩니다. 팽창하는 증기압으로 인한 충격력에 의해 다이가 캐리어에서 최종 기판으로 추진되어 다이에 잔류물이 남지 않습니다.
그림 4: UVtransfer는 디스플레이에 정확한 피치가 생성되도록 마스크 스텝 앤 스캔(step and scan) 공정을 사용합니다.
인접 다이의 전체 영역이 동시에 처리되는 LLO 공정과 달리 전사 공정은 다이의 피치가 원래 웨이퍼와 세밀하게 분리되어 있다가 최종 디스플레이의 픽셀 피치로 바뀌는 단계입니다. 예를 들어, 이 공정에서는 다섯 번째 다이 또는 열 번째 다이만 조사하는 패턴의 포토마스크를 사용합니다. 이후 디스플레이의 그 다음 영역이 다이 충진 위치로 바뀌면 마스크 인덱싱을 통해 임시 캐리어에 따라 웨이퍼 피치 한 단위를 이동시켜 새로운 다이 전체 어레이를 전사할 수 있게 됩니다.
LLO와 전사의 또 다른 차이점은 후자는 접착제를 제거하기 때문에 레이저 플루언스가 III-V 반도체보다 5-20배 낮아도 된다는 것입니다. 이렇게 에너지 효율이 좋기 때문에 레이저 출력이 크지 않아도 대량을 처리할 수 있습니다.
이를 위해서는 Coherent UVtransfer 공정의 다른 몇 가지 기능이 필요합니다. 예를 들어, 캐리어 장착 다이와 TFT 기판 사이의 간극이 거의 제로에 가까워도 각 다이가 손상 없이 정확한 위치에 성공적으로 전사되려면 충격력을 관리하고 제어해야 합니다. 특히, 충격력의 크기와 방향이 최적화되고 전체 디스플레이에서 일관되게 유지되어야만 전사를 위한 공정 범위가 손상되지 않습니다.
공정 필드에서 다이가 매우 균일하고 일정하게 전사되려면 레이저가 매우 균일하게 조사되어야 하는데 이는 다양한 용도에서 광범위하게 사용되는 Coherent의 핵심 능력입니다. 이후 매우 균일한 2D 필드가 광학장치에 의해 용도에 맞게 종횡비가 큰 정사각형 또는 직사각형으로 모양이 바뀝니다. 예를 들어, 6" 웨이퍼를 전사할 경우 웨이퍼에서 약 100mm x 100mm의 필드를 사용할 수 있습니다. 그림 4에 개략적으로 묘사된 바와 같이 국소 규모(단일 다이)의 세기가 균일해 전체 영역에서 균일하게 밀립니다. 따라서 충격력은 항상 수직으로 작용해 가우스 또는 경사형 세기 프로파일을 지닌 빔으로 유발되는 측면 이동이 없습니다. 더 큰 (웨이퍼 폭) 규모에서 빔 세기가 동일하다는 것도 중요합니다. 그래야만 각 다이가 동일한 힘으로 밀리기 때문입니다.
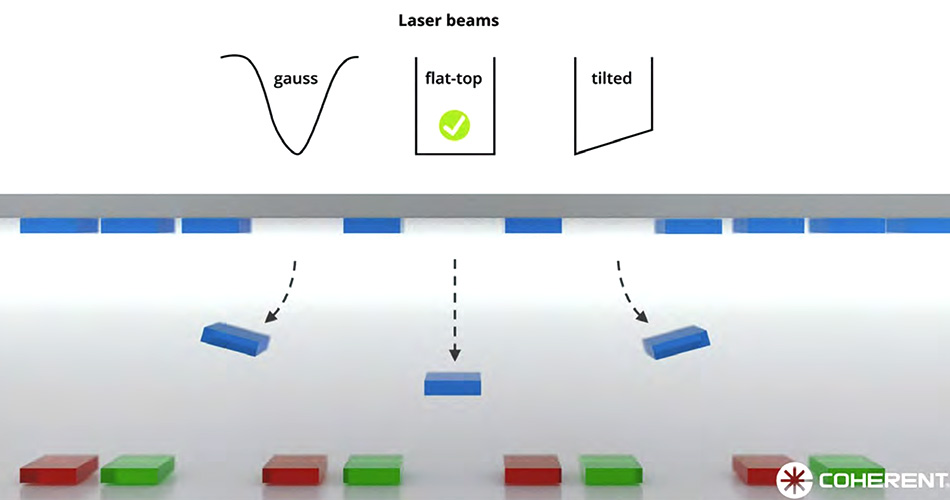
그림 5: 확장이 아닌 정확한 배치에는 매우 균일한 "플랫탑(flat top)" 빔 프로파일이 매우 중요합니다.
특히 UVtransfer 공정은 현재 시험 생산에서보다 훨씬 작은 다이(<5 미크론)와 좁은 스트리트를 쉽게 지원할 수 있습니다. 실제로, 짧은 UV 파장 때문에 미래의 미크론 단위 해상도를 달성할 수 있습니다. 더 작은 다이에는 다른 투영 마스크를 사용하면 됩니다.
불량 다이의 수리/교체
μLED 기반 디스플레이가 시장에서 성공하려면 생산비를 크게 절감하고 수율 100%를 달성해야 합니다. 안 그러면 수억 개의 픽셀이 들어가는 디스플레이가 불가능할 것입니다. 그러나 다이 결함은 불가피하기 발생하기 때문에 제조업체들은 수리/교체 방식과 호환되는 생산 기술 플랫폼만 채택할 수 있습니다. LLO와 전사에 모두 응용되는 Coherent의 UVtransfer는 이미 조사가 진행 중인 여러 교체 개념과 호환됩니다.
이 공정의 첫 단계는 웨이퍼에서 불량 다이를 찾아 제거하는 것입니다. 그러나 이로 인해 임시 캐리어에 미싱 스폿(제거된 다이가 있었던 자리)이 남게 됩니다. 따라서 최종 기판에서 이러한 빈 스폿을 다시 채워야 합니다.
선택한 영역(단일 다이)에만 이 공정을 적용하여 LLO 전에 결함 다이를 웨이퍼에서 제거할 수 있습니다. 이후 각 웨이퍼에서 제거된 다이의 맵이 순방향으로 전사되어 기판에서 빠진 다이의 맵으로 바뀝니다. 비슷한 순방향 UVtransfer 공정으로 대량 전사한 후에 개별적으로 삽입할 수 있지만 이제는 정의된 단일 초음파 빔을 사용합니다. 레이저로 III-V 재료를 제거할지 또는 희생 접착제를 제거할지 여부에 따라 레이저 출력이 맞춰집니다.
요약
MicroLED는 크기 스펙트럼의 양쪽 끝에 있는 디스플레이 모두 그 성능과 용도를 확대할 수 있는 놀라운 개발 기술입니다. 물론 대량 생산을 실현하기 전까지 넘어야 할 장애가 많이 있습니다. 그렇지만 UV 레이저 빔을 이용해 다양하게 활용할 수 있는 두 공정은 시험 설비 수준에서 그 능력을 입증해 보이고 있습니다. 특히 UVtransfer는 크기 확장이 가능해 비용이 많이 드는 재투자나 공정 교체 없이 소형화 추세에 원활하게 따라갈 수 있습니다. 고출력 UV 레이저의 확장 가능성 덕분에 고객 공정이 개발되면 우수성이 입증된 솔루션을 생산 라인으로 간편하게 옮길 수 있습니다. 물론 현재와 미래의 정밀도 요건은 그대로 유지됩니다.