WHITEPAPER
„Energie für die E-Mobilität“: Schweißen von Kupfer mit dem Adjustable Ring Mode-Faserlaser
Überblick
Faserlaser sind zwar die vorherrschende Laserquelle zum Schweißen, aber ihre Infrarotleistung wird von einigen Metallen, insbesondere Kupfer, stark reflektiert, was ihre Effektivität bei diesen Materialien einschränkt. Daher haben sich grüne Festkörperlaser mit hoher Leistung als mögliche Alternative für das Schweißen von Kupfer erwiesen, da diese Wellenlängen von diesem Metall stärker absorbiert werden. Aber diese grünen Laser haben einige praktische Einschränkungen, die letztlich zu höheren Betriebskosten führen. In diesem Dokument werden die Ergebnisse aktueller Kupferschweißtests vorgestellt, die erfolgreich mit einem neuartigen ARM-Faserlaser (Adjustable Ring Mode) mit hellem Zentralstrahl durchgeführt wurden. Hier lieferte der ARM-Laser mit seiner hohen Helligkeit eine ausgezeichnete Schweißqualität und einen besseren Einbrand bei verschiedenen Schweißgeschwindigkeiten als handelsübliche grüne Laser der kW-Klasse. Diese Ergebnisse zeigen, dass diese Technologie alle Kosten-, Zuverlässigkeits- und praktischen Vorteile von Faserlasern für die anspruchsvolle Aufgabe des Kupferschweißens bieten könnte.
Fertigung von E-Mobilität
Der Boom bei der Herstellung von Elektromobilität ist der Hauptfaktor, der zu einem deutlichen Anstieg der Nachfrage nach Kupferschweißlösungen führt. Kupfer besitzt im Vergleich zu anderen Metallen eine Reihe wünschenswerter elektrischer, thermischer, mechanischer und kostensparender Eigenschaften. Deshalb wird es in allen Elektrofahrzeugen verwendet – in den Statoren der Elektromotoren selbst, im Stromverteilungssystem (Sammelschienen usw.) und in den Batterien. Bei der Herstellung vieler dieser Komponenten und Systeme wird Kupfer geschweißt.
Die gleiche hohe elektrische und thermische Leitfähigkeit, die Kupfer ideal für diese Anwendungen macht, stellt jedoch gleichzeitig eine Herausforderung beim Schweißen mit herkömmlichen Faserlasern dar. Insbesondere seine elektronischen Eigenschaften sorgen dafür, dass es bei der nahen Infrarot-Wellenlänge von Faserlasern stark reflektiert. Und seine ausgezeichnete Wärmeleitfähigkeit erfordert den Einsatz einer großen Menge an Laserenergie, um das Material zu schmelzen und den Schweißprozess einzuleiten.
Daher ist bei der Verwendung eines herkömmlichen Faserlasers in der Regel eine sehr hohe Leistung erforderlich, um die für das anfängliche Schmelzen des Materials notwendige Leistungsdichte zu erreichen. Aber dieser Ansatz der „rohen Gewalt“ macht den Schweißprozess instabil und extrem empfindlich gegenüber kleinen Schwankungen der Arbeitsfläche. Insbesondere das Vorhandensein von lokalisierter Oberflächenoxidation oder Inhomogenitäten der Oberflächenstruktur im kleinen Maßstab kann zu Prozessinstabilitäten führen. Das Endergebnis können inkonsistente Schweißnähte, schlechte Oberflächenqualität und Porosität sein.
Grüne Festkörperlaser
Kupfer ist im grünen Bereich fast um eine Größenordnung absorbierender als im nahen Infrarot. So kann die Energie eines grünen Lasers effizienter in das Werkstück eingekoppelt werden, was zu einem stabileren und unempfindlicheren Prozess führt, als dies mit herkömmlichen Faserlasern möglich ist. Infolgedessen werden grüne Hochleistungs-Festkörperlaser von einigen wenigen Herstellern eingesetzt und von vielen anderen getestet.
Der Einsatz von grünen Hochleistungslasern bei der Herstellung von Elektromobilität birgt jedoch einige erhebliche praktische Probleme. Einige davon ergeben sich aus den inhärenten Eigenschaften und der Konstruktion dieser grünen Laser selbst.
Die Lasermaterialien, die für grüne Festkörper-Faser- oder Scheibenlaser verwendet werden, erzeugen Licht im nahen Infrarotbereich; die Frequenzverdopplung wird verwendet, um das Infrarot in grünes Licht umzuwandeln. Während dieses Verfahren im unteren Leistungsbereich (unter kW) mit großem Erfolg eingesetzt wird, stößt es bei der für die meisten industriellen Kupferschweißaufgaben erforderlichen Leistung von mehreren kW auf einige Schwierigkeiten. Insbesondere die Frequenzumwandlung selbst ist nur etwa 50 % effizient. Es wird also ein Single-Mode-IR-Laser mit 4 kW Leistung benötigt, um 2 kW grüne Ausgangsleistung zu erzeugen. Die nicht umgewandelte Energie wird zu Wärme, die über einen wassergekühlten Kühlkörper abgeführt werden muss. Dies macht diese Laser energieineffizient (was zu höheren Betriebskosten aufgrund des höheren Stromverbrauchs führt) und erfordert eine große Menge an Kühlwasser. Außerdem verschlechtern sich die Verdopplungskristalle im Laufe der Zeit aufgrund der hohen Leistung und können zu Problemen mit der Zuverlässigkeit und Ausfallzeiten führen, wenn sie nicht sorgfältig verwaltet werden. Einige Designs verwenden komplexe Strahlverschieber und Kristalltemperaturstabilisatoren, um dies zu kompensieren.
„... ein Single-Mode-IR-Laser mit 4 kW Leistung wird benötigt, um 2 kW grüne Ausgangsleistung zu erzeugen.“
Ein weiteres praktisches Problem bei grünen Lasern ist, dass die für die Strahlübertragung verwendeten standardmäßigen Lichtleitfasern durch grünes Licht schneller verdunkelt werden, was ihre Lebensdauer verringert. Spezielle Fasern für grünes Licht können dieses Problem lösen, sind aber teurer und weniger leicht verfügbar. Der Verdunkelungseffekt nimmt auch mit der Länge der Faser zu. Dadurch ist die Faserlänge derzeit auf 10 m begrenzt, was die Flexibilität bei der Platzierung des Lasers in der Produktionsumgebung einschränkt. Außerdem sind die im Handel erhältlichen grünen Hochleistungs-CW-Laser derzeit auf eine maximale Leistung von 2 kW begrenzt.
Die meisten Industrielaser arbeiten im nahen Infrarot, so dass die gesamte Infrastruktur für ihre Unterstützung auf dieser Wellenlänge basiert. z. B. ist die Auswahl an Prozessköpfen für grüne Laser begrenzt, und oft müssen sie angepasst werden. Ebenso sind Hilfslinsen, Schutzgläser und andere optische Komponenten meist für Infrarotlaser. So muss ein Hersteller, der bereits Infrarotlaser einsetzt, möglicherweise einen größeren Vorrat an Ersatzteilen und Verbrauchsmaterialien vorhalten, um den Einsatz von grünen Lasern in seinem Betrieb zu ermöglichen, ohne dass es zu Serviceverzögerungen und Ausfallzeiten kommt.
Der HighLight™ ARM-Faserlaser
Faserlaser sind elektrisch viel effizienter als grüne Festkörperlaser. Das bedeutet, dass sie für eine bestimmte Ausgangsleistung weniger Strom benötigen und weniger Abwärme produzieren. Dies reduziert die Betriebskosten und vereinfacht die Kühlung. Außerdem sind Faserlaser sehr zuverlässig. Und ihre Infrarotleistung wird über Glasfaser übertragen. Aber trotz dieser wünschenswerten Eigenschaften wurden sie aufgrund der zuvor genannten Probleme nicht häufig zum Schweißen von Kupfer verwendet.
Coherent hat vor einigen Jahren Faserlaser der HighLight-Serie mit einstellbarem Ringmodus (ARM) eingeführt, um die Kosten und praktischen Vorteile dieser Quellen für Anwendungen nutzbar zu machen, für die herkömmliche Technologien nicht ausreichen. Typischerweise handelt es sich dabei um Aufgaben, bei denen die räumliche Verteilung von Leistung und Leistungsdichte an der Arbeitsfläche sorgfältig kontrolliert werden muss, um eine gute Schweißqualität zu erzielen (geringe Spritzer, minimale Rissbildung und reduzierte Porosität). Typische Beispiele sind das spaltfreie Schweißen von verzinktem Stahl, das spritzerfreie Schweißen von Komponenten des Antriebsstrangs und das rissfreie Schweißen von Aluminium-Anbauteilen ohne Zusatzdraht.
Diese präzise Kontrolle über die räumliche Leistungsverteilung wird durch den einzigartigen Ausgangsstrahl des ARM-Lasers erreicht, der aus einem zentralen Punkt besteht, der von einem weiteren konzentrischen Ring aus Laserlicht umgeben ist. Die Leistung in der Mitte und im Ring kann unabhängig voneinander eingestellt und bei Bedarf moduliert werden, was eine sehr sorgfältige Kontrolle der Dynamik des Schmelzbades ermöglicht.
Coherent HighLight ARM-Laser sind mit verschiedenen Zentrum-zu-Ring-Verhältnissen und Leistungsstufen erhältlich, die auf spezifische Anwendungen zugeschnitten werden können. Der Durchmesser des Zentrums kann zwischen 22 µm und 100 µm liegen. Der Außendurchmesser des Rings kann zwischen 140 µm und 200 µm variieren.
Zum Schweißen von Kupfer wird ein hochintensiver, leistungsstarker Zentralstrahl benötigt. Dies liefert die nötige Energie, um das Material trotz seines relativ niedrigen Absorptionskoeffizienten zu schmelzen, während der Ringstrahl zur Stabilisierung des Schlüssellochs beiträgt. Das Ergebnis ist, dass der Schweißprozess unabhängig von Oberflächenvariationen des Werkstücks eingeleitet und konstant aufrechterhalten wird, wodurch die Einschränkungen, die bei herkömmlichen Faserlasern auftreten, überwunden werden.
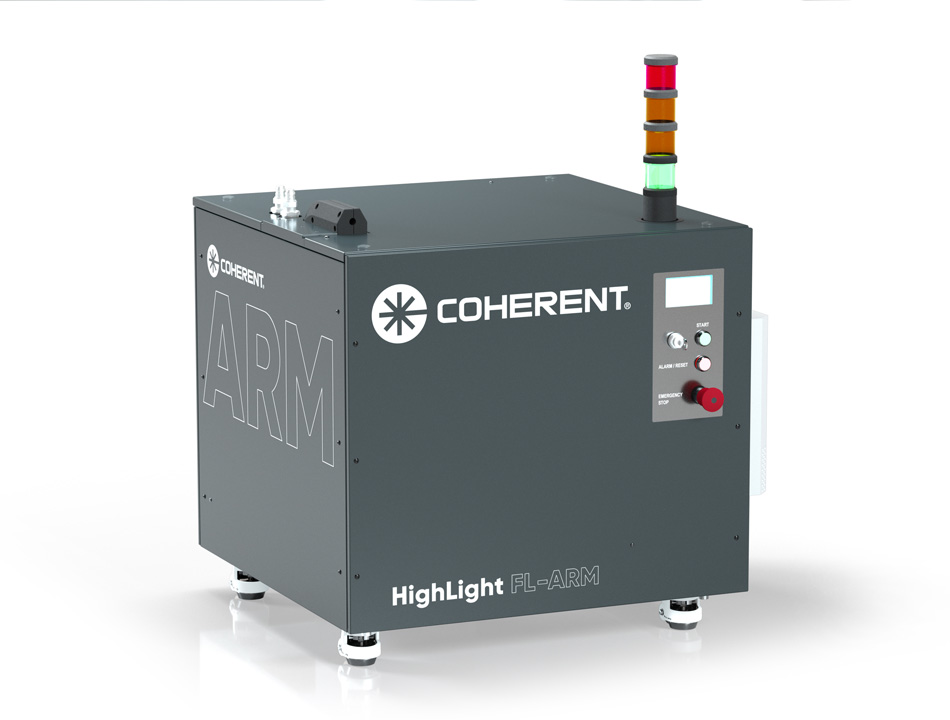
Abbildung 1: HighLight FL4000CSM-ARM Faserlaser.
„Zum Schweißen von Kupfer wird ein hochintensiver, leistungsstarker Zentralstrahl benötigt.“
Ergebnisse beim Schweißen von Kupfer
Die Anwendungstechniker von Coherent führten eine Reihe von Kupferschweißtests mit einem ARM-Laser durch, der einen sehr hellen Mittelstrahl mit einem Durchmesser von 22 µm und einen Ringstrahl mit einem Innen-/Außendurchmesser von 100 µm/170 µm hat. Der Laser wurde mit einem Remote-Bearbeitungskopf mit einer Vergrößerung von 1,4 fokussiert, mit Stickstoff als Schutzgas und Cross-Jet. Das geschweißte Material war reines Kupfer. Die Laserleistung betrug 4 kW, mit 1,5 kW in der Mitte und 2,5 kW im Ring für alle Tests. Das Foto (Abbildung 2) zeigt den Versuchsaufbau.
Die Fokusposition wurde variiert und es wurde festgestellt, dass die beste Schweißqualität bei einer Fokuseinstellung von 1,5 mm über der Materialoberfläche erzielt wurde. Genauer gesagt war diese Position der beste Kompromiss zwischen Schweißnahtausbuchtung und Schweißnahtqualität. Der ARM-Laser erzeugt eine tiefere Schweißnaht, wenn er direkt auf die Materialoberfläche fokussiert wird. Die daraus resultierende Qualität der Schweißnahtoberfläche und die Spritzer sind jedoch für typische E-Mobility-Anwendungen nicht ausreichend. Das Strahlprofil auf der Arbeitsfläche bei optimaler Strahlfokusposition (1,5 mm über der Oberfläche) ist in der Grafik dargestellt.
„Der Infrarot ARM-Laser liefert eine doppelt so große Schweißtiefe“
Das Diagramm zeigt die Schweißnaht auf 2 mm dickem Kupfer als Funktion der Geschwindigkeit unter den gerade beschriebenen Bedingungen. Zum Vergleich wurde auch ein grüner Laser mit 2 kW Leistung unter den gleichen Bedingungen getestet. Es wurde eine geringere grüne Leistung verwendet, da ein Infrarot-Faserlaser mit 4 kW Leistung nur 2 kW grüne Leistung erzeugt. Der Vergleich zeigt, dass der ARM-Infrarotlaser über einen weiten Bereich von Schweißgeschwindigkeiten eine doppelt so hohe Einschweißtiefe liefert.
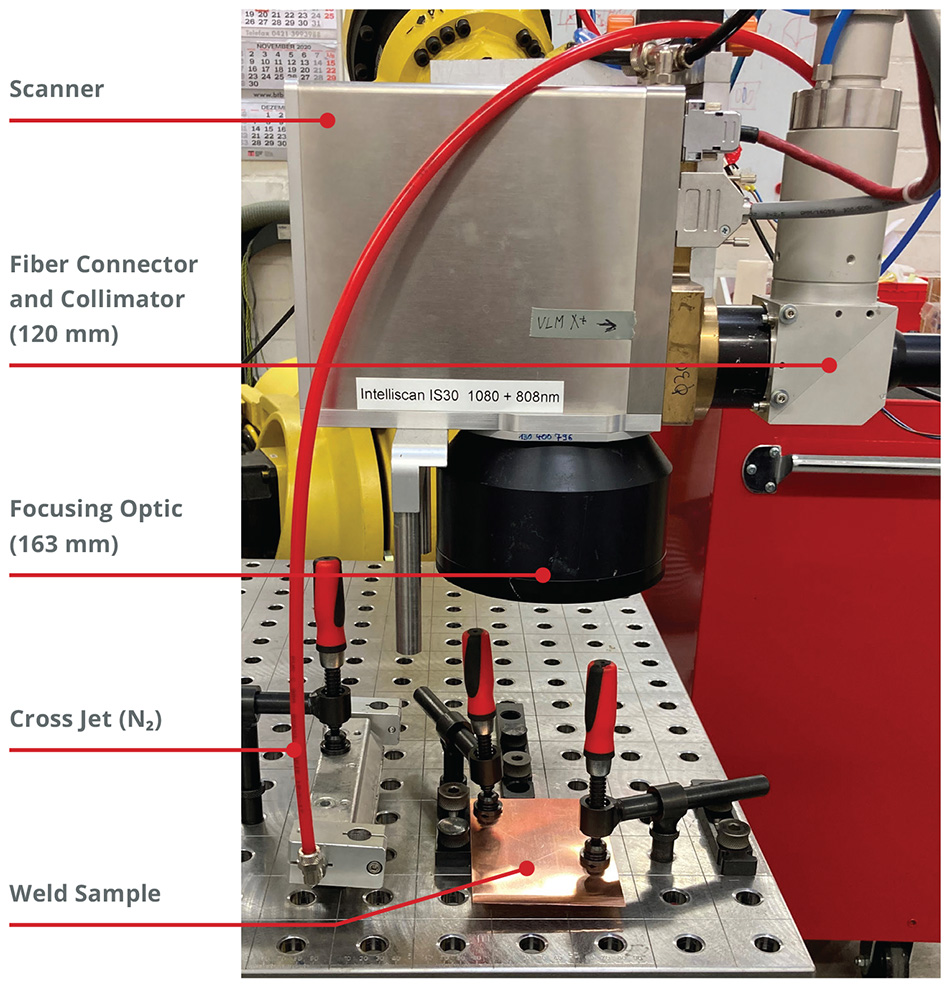
Abbildung 2: ARM-Faserlaser-Schweißstation mit hoher Helligkeit, Scanner und Abschirmdüse.
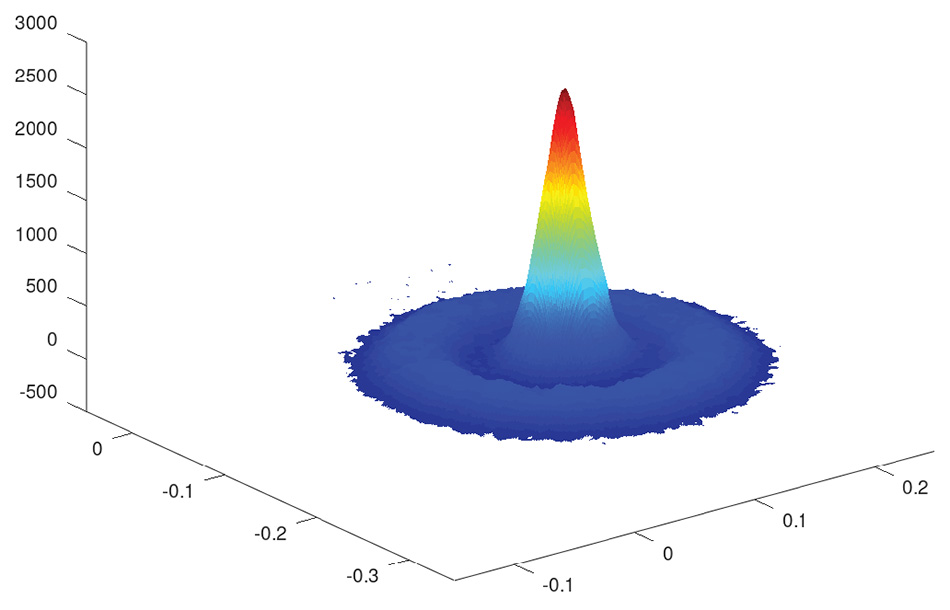
Abbildung 3: Strahlprofil des ARM auf der Arbeitsfläche (1,5 kW in der Mitte und 2,5 kW im Ring), wobei der Laser 1,5 mm über der Arbeitsfläche fokussiert ist.
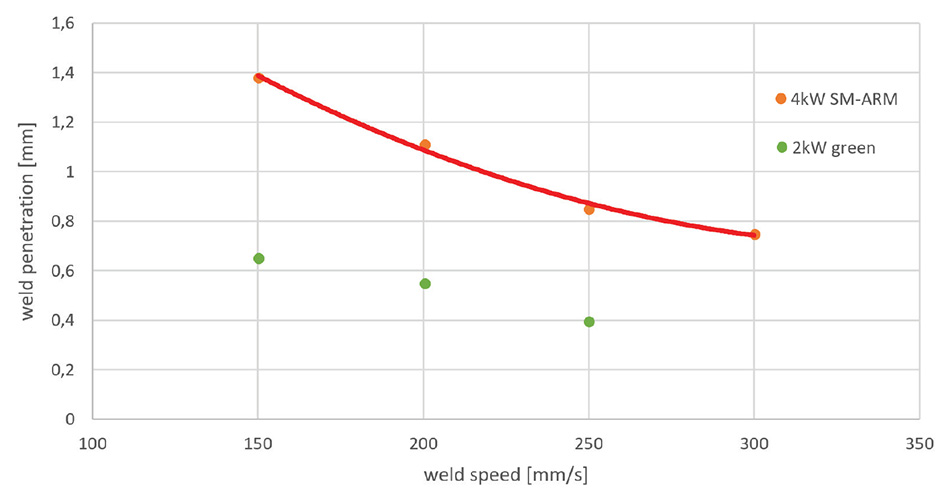
Abbildung 4: Schweißdurchdringung bei einem 4 kW ARM mit hoher Helligkeit im Vergleich zu einem grünen Faserlaser mit 2 kW Leistung.
Schweißeffizienz
Die Schweißeffizienz des ARM-Lasers wurde ebenfalls gemessen und mit zuvor veröffentlichten Schweißergebnissen für einen grünen Laser mit 2 kW Leistung verglichen. Für beide Schweißnähte wurde Stickstoff als Schutzgas verwendet. Die veröffentlichten Daten für den grünen Laser zeigten einen (konstanten) Schweißnahtquerschnitt von 0,5 mm² und eine Eindringtiefe von etwa 1 mm. Der ARM-Laser wurde so konfiguriert, dass er dieselben Ergebnisse liefert. Dies erforderte eine Ausgangsleistung von 3,5 kW und eine Schweißgeschwindigkeit von 300 mm/s, verglichen mit einer Schweißgeschwindigkeit von 200 mm/s pro Sekunde für den grünen Laser mit 2 kW Leistung. Die Normalisierung dieser Ergebnisse ergibt eine lineare Laserleistung von 10 J/mm für den ARM-Laser, verglichen mit 11,8 J/mm für den grünen Laser. Daher bietet der grüne Laser eine etwas höhere Schweißleistung. Die höhere Gesamtleistung des ARM-Lasers ermöglicht es jedoch, trotz dieses kleinen Unterschieds in der Effizienz, mit viel höheren Schweißgeschwindigkeiten zu arbeiten.
Oberflächenqualität
Ein weiterer wichtiger Aspekt ist die Qualität der Oberfläche. Herkömmliche Faserlaser können zwar Kupfer schweißen, sind aber sehr empfindlich gegenüber Veränderungen der Oberflächenqualität. Das Foto zeigt Schweißraupen für ein ARM-Laserschweißen mit hoher Helligkeit auf geschliffenem und poliertem Kupfer. Der Prozess bleibt auf beiden Oberflächen stabil, ohne dass sich die Schweißqualität verändert.
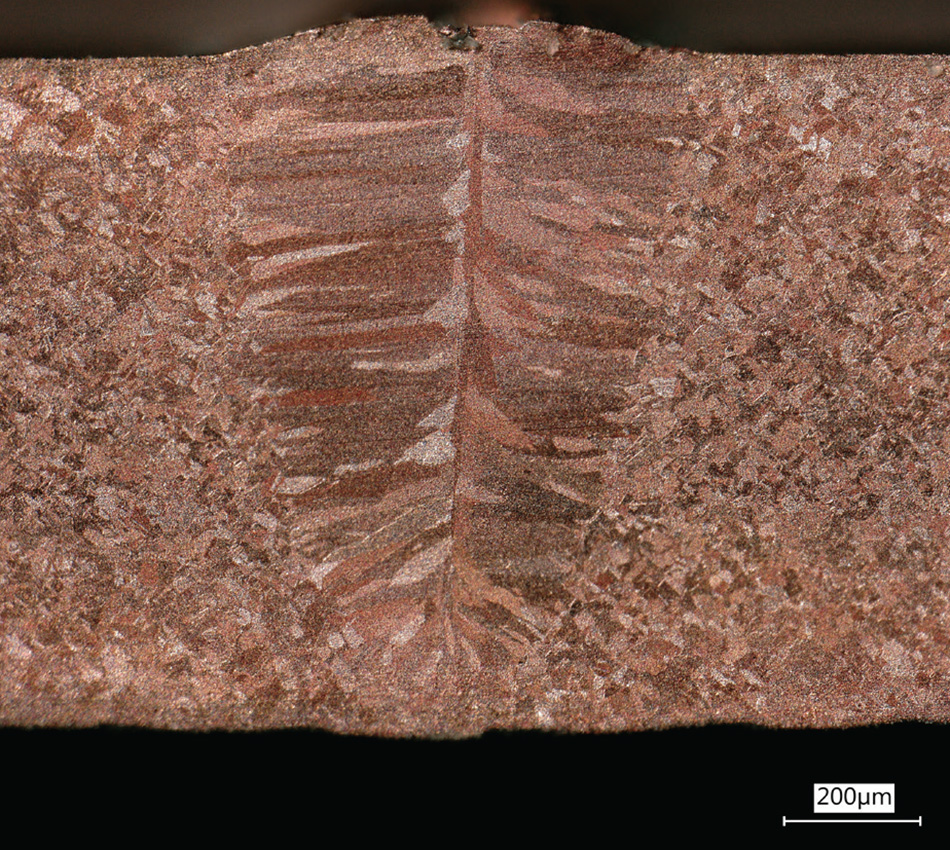
Abbildung 5: Querschnitt einer Kupferschweißnaht, die mit dem ARM-Laser mit hoher Helligkeit und einer Ausgangsleistung von 3,5 kW bei einer Schweißgeschwindigkeit von 300 mm/s erzeugt wurde.
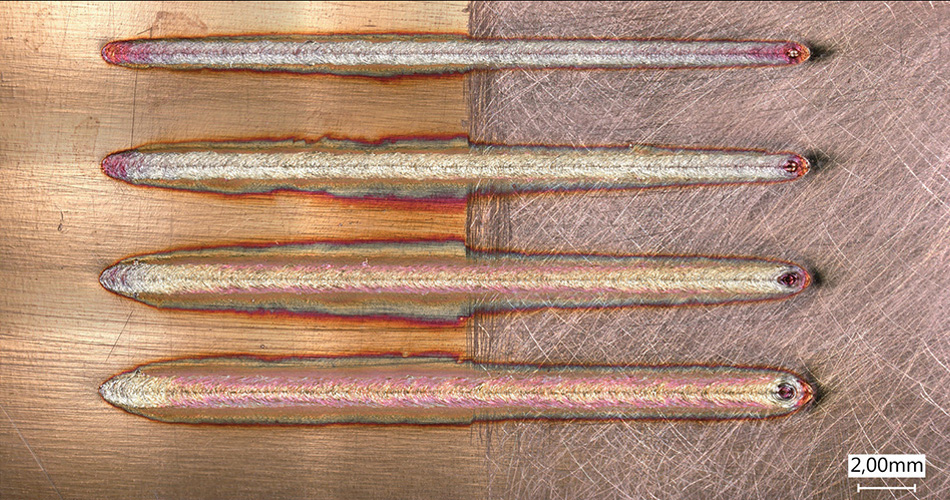
Abbildung 6: Abbildung 6: Gleichmäßige Schweißraupen auf glattem und geschliffenem Kupfer mit dem 4 kW ARM-Laser bei verschiedenen Geschwindigkeiten (300–150 mm/s von oben nach unten)
Schlussfolgerung
Diese Tests zeigen, dass der einzigartige, sehr helle ARM-Laser von Coherent eine praktische Lösung für anspruchsvolle Kupferschweißanwendungen in der Elektromobilität ist. Schweißtiefe und Prozessgeschwindigkeit entsprechen oder übertreffen die aktuellen Produktionsanforderungen. Außerdem vermeidet der ARM-Laser die Probleme mit der Oberflächenqualität und der Prozessinstabilität, die in der Vergangenheit den Einsatz von Faserlasern für Kupfer eingeschränkt haben. Damit liefert dieser neue ARM-Laser endlich alle Kosten-, Zuverlässigkeits- und praktischen Vorteile, die Faserlaser zur ersten Wahl für so viele andere industrielle Anwendungen gemacht haben, auch für die anspruchsvolle Aufgabe des Kupferschweißens.
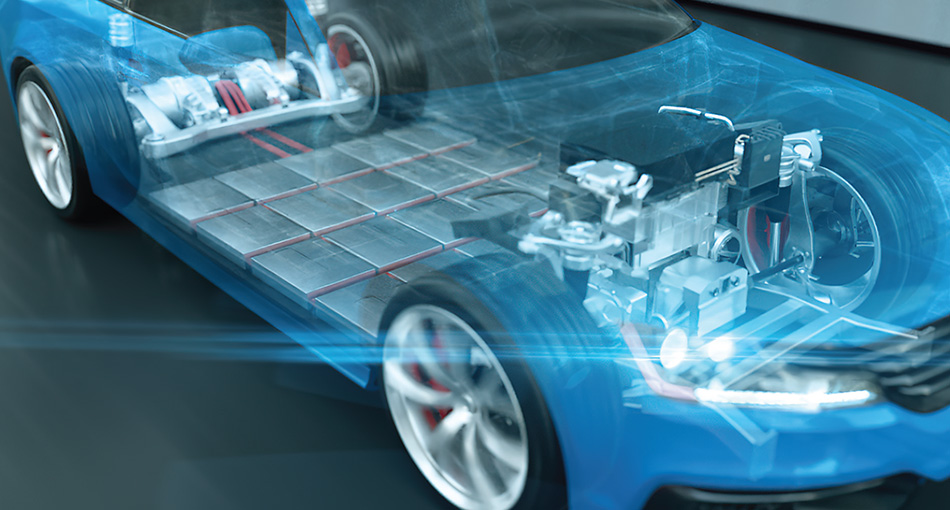