ERFOLGSGESCHICHTE EINES KUNDEN
Westaustralische Schwerindustrie profitiert von Direktdioden-Lasertechnologie
APEX ETG setzt 10 kW Direkt-Diodenlaser von Coherent zum effizienten Hochgeschwindigkeits-Auftragschweißen von Komponenten für Branchen wie Bergbau, Energie und Bauwesen ein.
Daniel Rhind arbeitet seit 20 Jahren mit Oberflächenbeschichtungen und ist sich der Vorteile des Laserauftragsschweißens gegenüber anderen Methoden zur Reparatur verschlissener Metallteile sehr bewusst. Er ist sogar so begeistert von dem Laserauftragsschweißen, dass er sein eigenes Unternehmen – APEX ETG – gegründet hat, um die Vorteile dieser Technologie der Industrie in Westaustralien zugänglich zu machen.
Aber als Geschäftsinhaber ist er genauso sehr auf Kosten und Produktivität wie auf die Qualität der Ergebnisse bedacht. Um erfolgreich zu sein, muss seine Ausrüstung für das Laserauftragsschweißen also verschiedene Anforderungen erfüllen.
Zunächst muss schnell beschichtet werden. Dadurch ist er in der Lage, die vielen Aufträge, die er für die Beschichtung sehr großer Teile in der Öl- und Gasindustrie, im Bergbau und im Baugewerbe erhält, in einem Zeitrahmen auszuführen, der seine Kunden zufrieden stellt.
Als Nächstes benötigt er operative Flexibilität. Er möchte, dass jedes Auftragsschweißsystem in seinem Geschäft ein möglichst breites Spektrum an Aufgaben erfüllt – so dass es die ganze Zeit über in Betrieb ist. Dies maximiert die Produktivität und die Investitionsrendite. Die Produktivität wird weiter gesteigert, wenn er eine Maschine mit einem Minimum an Ausfallzeiten und Schwierigkeiten zwischen verschiedenen Aufträgen wechseln kann.
Ein weiterer wichtiger Faktor für die Produktivität ist die Zuverlässigkeit und Betriebszeit der Geräte. Ein Laserauftragsschweißsystem, das nicht funktioniert, generiert keine Einnahmen und trägt sich nicht selbst.
Schließlich ist es fast selbstverständlich, dass er hochwertige Ergebnisse benötigt. Der Erfolg von APEX ETG hängt stark vom Wiederholungsgeschäft ab – zum Beispiel von laufenden Programmen zur Überholung von Hydraulikzylindern für Bergbauunternehmen. Er bindet diese Kunden nur, wenn er die richtige Mischung aus Qualitätsergebnissen, schneller Bearbeitungszeit und natürlich dem Preis bietet. „Der Erfolg unserer Kunden ist auch unser Erfolg“, erklärt Daniel.
Um all diese Anforderungen zu erfüllen, setzt APEX ETG auf Laserauftragsschweißsysteme, die auf Produkten der Coherent HighLight DD-Serie basieren. Es handelt sich um Diodenlaser mit einer Ausgangsleistung von bis zu 10 kW. Sie erzeugen einen Freiraumstrahl (statt eines fasergekoppelten Strahls), der leicht in eine rechteckige Form über einen weiten Bereich von Abmessungen gebracht werden kann. Durch eine einfache Änderung der Strahlführungsoptik können Strahlen mit einer Breite von 1 mm bis 12 mm und einer Länge von 6 mm bis 36 mm erzeugt werden. Sowohl Druck- als auch Schwerkraft-Pulverdüsen sind von Coherent erhältlich, um das Auftragsschweißen mit hoher Abscheidungsrate zu unterstützen.
DER VORTEIL DER DIREKTDIODEN
„Wenn Sie die meisten Leute in meiner Branche und vor allem die Anbieter dieser Geräte fragen würden, würden sie Ihnen sagen, dass ein fasergekoppelter Diodenlaser das beste Werkzeug für ein großflächiges Auftragsschweißgeschäft ist. Sie würden sagen, dass Sie einen fasergekoppelten Diodenlaser nehmen und ihn dann je nach Bedarf an verschiedene Bearbeitungsköpfe anschließen können, um verschiedene Aufgaben zu erledigen“, bemerkt Daniel. „Aber als jemand, der viel mit Laserauftragsschweißen gearbeitet hat, kann ich Ihnen sagen, dass das genau die falsche Antwort ist. Das Problem tritt bei Auftragswechseln auf. Wenn ich einen Auftrag mit einem 6 mm langen Linienbalken ausführe und der nächste Auftrag einen 18 mm langen Balken erfordert, dann muss ich auf einen anderen Auftragsschweißkopf umsteigen. Das erfordert eine Neuausrichtung und Anpassung – und das braucht Zeit.“
„Die gängige Meinung ist, dass man ein einziges fasergekoppeltes Diodenlasersystem und einen Haufen verschiedener Prozessköpfe kaufen kann und dann alles machen kann. Und vielleicht können sie es – aber sie können es nicht schnell und effizient tun. Und wenn die Geräte für Umrüstungen ausfallen, verdienen Sie kein Geld. Das schränkt Ihre Möglichkeiten ein, großflächige Auftragsschweißarbeiten mit hoher Geschwindigkeit durchzuführen“, fügt er hinzu.
„Im Gegensatz dazu muss ich bei der HighLight DD nur die Optik im Prozesskopf austauschen, um die Linienabmessungen zu ändern – und den Prozess erneut starten. Es dauert buchstäblich nur einen Moment. Und ich kann Laserlinien bekommen, die lang genug sind, um das Auftragsschweißen auch für wirklich große Flächen in einem Zeitrahmen, der wirtschaftlich sinnvoll ist, anzuwenden.“
„Natürlich sage ich nicht, dass es mit fasergekoppelten Systemen nicht geht. Ich habe selbst mehrere und benutze sie ausgiebig. Sie sind ein kosteneffizientes Werkzeug für das Auftragsschweißen kleinerer Flächen auf minderwertigen Teilen. Aber sie bieten nicht die Flexibilität, die oft versprochen wird. Und sie sind sicherlich nicht das Richtige für die großflächigen Auftragsschweißaufgaben, die bei APEX ETG zu einem großen Teil des Geschäfts geworden sind. Das würde wirtschaftlich keinen Sinn machen.“
AUFTRAGSSCHWEIßEN IN AKTION
Der 10 kW Direkt-Diodenlaser Coherent HighLight DD hat APEX ETG in die Lage versetzt, Auftragsschweißarbeiten durchzuführen, die in Westaustralien – und vielleicht auch sonst nirgendwo auf der Welt – jemals zuvor durchgeführt wurden. Ein Beispiel ist das „Hartauftragsschweißen“ einer Baggerschaufel. Dies ist die riesige Schaufel des Baggers, die die Erde aufnimmt. Die Schaufel, die APEX ETG zur Verfügung gestellt wurde, hatte ein Volumen von 42 m³ – buchstäblich so groß wie ein Schulbus.
Diese Schaufeln werden durch den Gebrauch abgenutzt und werden schließlich mit neuem Material überzogen, damit sie weiter benutzt werden können. In der Vergangenheit bedeutete dies, dicke Chromkarbid-/Wolfram-„Verschleißplatten“ auf die Schaufel zu schweißen. Jede Platte kann etwa 3 m x 1 m groß sein, so dass ziemlich viele benötigt werden, um die gesamte Oberfläche der Schaufel abzudecken.
Das Schweißen von Verschleißblechen hat jedoch einige erhebliche Nachteile. Erstens ist es ein zeitraubender und arbeitsintensiver Prozess. Als Nächstes kommt eine Tonne zusätzliches Gewicht auf die Schaufel – genauer gesagt 9 Tonnen für das Verschleißplattenpaket für diese spezielle Schaufel.
Das Anschweißen der flachen Verschleißplatten an die gewölbte Oberfläche der Schaufel verursacht einige zusätzliche Probleme. Die Platten stehen unter Spannung (weil sie gebogen werden), und manchmal springen sie während des Gebrauchs zurück. Das bedeutet, dass der Bagger stillsteht, während die Platte wieder angeschweißt wird. Außerdem gibt es ein großes Sicherheitsproblem. Eine Platte springt mit erheblicher Kraft ab. Dies birgt die Gefahr von Verletzungen der Arbeiter.
Für das Laserstrahl-Auftragsschweißen hat APEX ETG die Schaufel auf eine große Roboterplattform montiert. Dadurch konnte sich der Laserstrahl kontinuierlich bewegen und die gesamte Oberfläche mit dem Auftragsschweißen bedecken. Das hat viel weniger Zeit in Anspruch genommen als eine typische Reparatur durch Schweißen.
Die gesamte Menge des auf die Schaufel aufgebrachten Auftragsschweißmaterials wog 450 kg. Das bedeutet, dass der Bagger mit jeder einzelnen Schaufel 8,5 Tonnen mehr aufnehmen kann als mit einer Schaufel mit Verschleißblechen. Das macht die Geräte effizienter und senkt die Kraftstoffkosten erheblich.
Auch die mit dem Direktdiodensystem aufgebrachten Auftragsschweißarbeiten machen keine Kompromisse bei der Qualität. Tatsächlich ist es genau das Gegenteil. Die bei APEX ETG gepanzerte Schaufel hat bereits 5.000 Betriebsstunden auf dem Buckel, und die laserauftragsgeschweißte Oberfläche hat sich nicht verändert. Außerdem gibt es beim Laserauftragsschweißen keine Sicherheitsbedenken, da die neue Oberfläche nicht abspringt.
„Dieser Job ist ein extremes Beispiel“, bemerkt Rhind. „Es ist wahrscheinlich das größte Teil, das jemals beschichtet wurde. Und es wäre schlichtweg unmöglich, mit einer anderen Technologie die gleichen Ergebnisse zu erzielen. Dies unterstreicht die außergewöhnlichen Möglichkeiten eines Hochleistungs-Direkt-Diodenlasers, um die Vorteile des Auftragsschweißens von sehr großen Teilen zu nutzen, wie sie im Baugewerbe, in der Öl- und Gasindustrie, im Bergbau und in anderen Schwerindustriezweigen üblich sind.“
„Aber die Fähigkeiten von APEX ETG beim Laserauftragsschweißen eignen sich für Anwendungen aller Größen und Geometrien. Dadurch sind wir in der Lage, die Bedürfnisse einer Vielzahl von Branchen in Westaustralien zu erfüllen. Es ist unserer guten Beziehung zu Coherent zu verdanken, dass wir diese Technologie auf den Markt bringen können.“
„Das Laserauftragsschweißen ist fast immer der beste Weg, um ein verschlissenes Metallteil wieder zu beschichten, und es gibt nichts Besseres als den 10 kW Direkt-Diodenlaser von Coherent, wenn es um das wirtschaftliche und schnelle Auftragen großer Teile geht.“
– Daniel Rhind, Geschäftsführer, APEX ETG
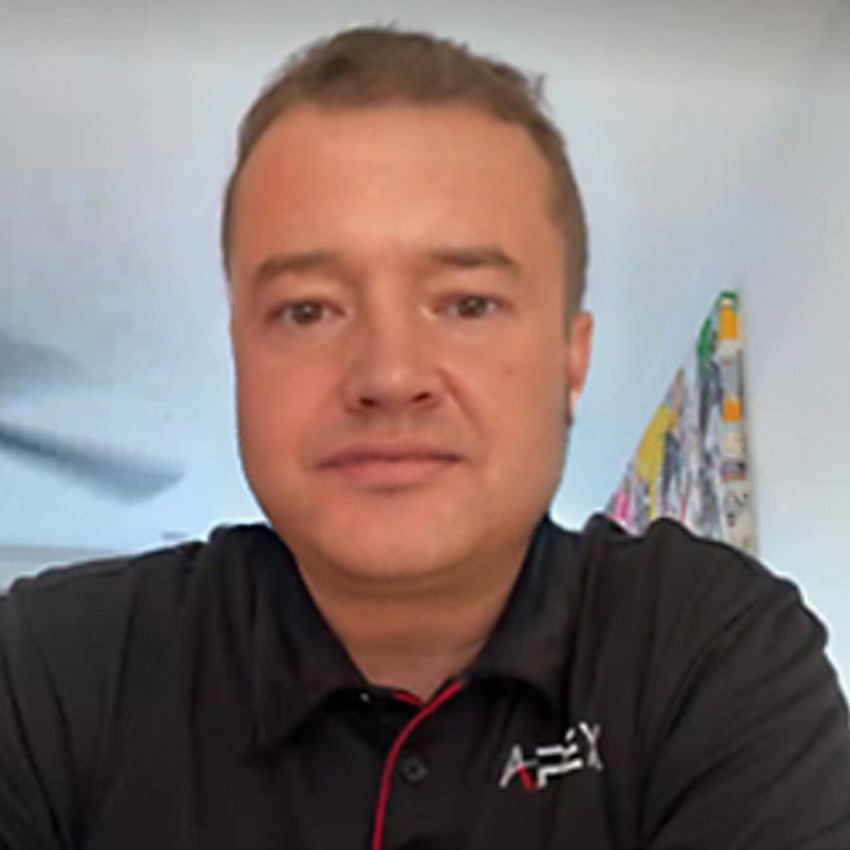
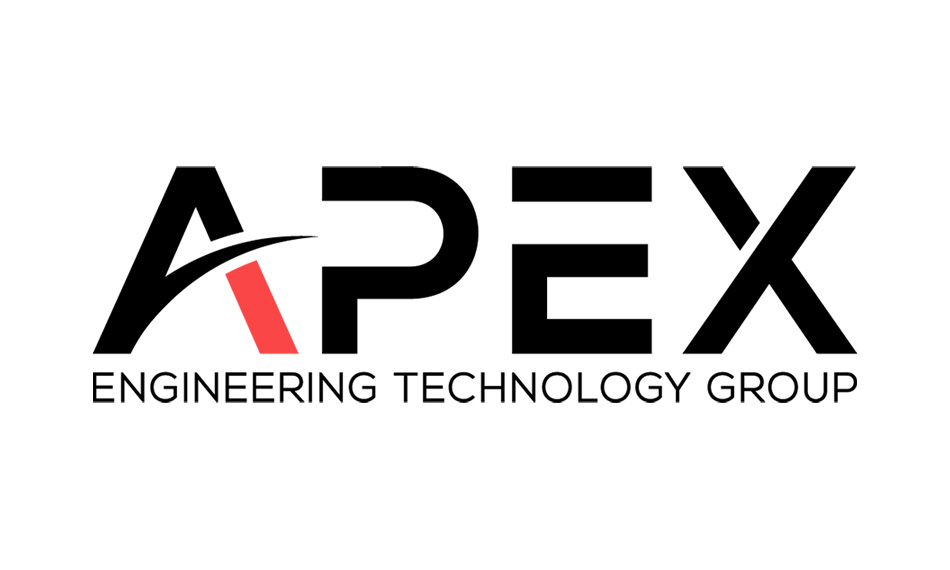
WAS IST LASERAUFTRAGSSCHWEIßEN
Auftragsschweißen ist ein additiver Fertigungsprozess, der in einer Vielzahl von Industrien zur Verbesserung der Oberflächeneigenschaften eines Teils oder zur Erneuerung einer durch Gebrauch abgenutzten Komponente eingesetzt wird. Beim Auftragsschweißen wird eine neue Oberflächenschicht auf einem Substrat erzeugt, die eine andere Zusammensetzung hat als das Basismaterial.
Es gibt eine Reihe verschiedener Techniken für das Auftragsschweißen, jede mit ihren eigenen spezifischen Eigenschaften in Bezug auf die verwendeten Materialien, die Qualität der auftragsgeschweißten Schicht und verschiedene praktische Fragen, einschließlich Durchsatzgeschwindigkeit, Prozesskompatibilität und Kosten.
Einige Methoden beinhalten eine Form des Lichtbogenschweißens, wie z. B. das Wolfram-Lichtbogenschweißen (GTAW), das Plasma-Lichtbogenschweißen (PAW), das Plasma-Transfer-Lichtbogenschweißen (PTA), das Metall-Gas-Lichtbogenschweißen (GMAW), das Unterpulver-Lichtbogenschweißen (SAW) und einige andere.
Bei all diesen Verfahren schmilzt ein Lichtbogen die Oberfläche des Grundmaterials. Das Auftragsschweißmaterial wird dann entweder in Draht- oder Pulverform eingeführt und ebenfalls durch den Lichtbogen geschmolzen. Es vermischt sich mit der Oberfläche des geschmolzenen Teils und erstarrt dann wieder, um die auftragsgeschweißte Schicht zu bilden.
Ein anderer Ansatz ist das thermische Spritzen. Hier wird das pulverförmige auftragsgeschweißte Material durch eine Flamme oder Elektrizität geschmolzen und dann auf das Werkstück aufgesprüht. Das Werkstück wird nur auf <200 °C erhitzt. Die vier gängigsten Arten des thermischen Spritzens sind Flammspritzen, Lichtbogenspritzen, Plasmaspritzen und Hochgeschwindigkeitsflammspritzen (HVOF).
Das Laserauftragsschweißen ähnelt den Lichtbogenschweißverfahren. Der Laser schmilzt sowohl die Substratoberfläche als auch das auftragsgeschweißte Material, das in Form von Draht, Streifen oder Pulver vorliegen kann.
Das Laserauftragsschweißen bietet jedoch erhebliche Vorteile gegenüber all diesen anderen Techniken. Wie beim Schweißen gehen die laserauftragsgeschweißten Schichten eine echte metallurgische Verbindung mit dem Substrat ein. Das bedeutet eine extrem haltbare Auftragsschweißschicht, die nicht abplatzt oder sich ablöst und die eine hervorragende Verschleiß- und Korrosionsbeständigkeit aufweist. Das ist beim thermischen Spritzen nicht der Fall.
Im Gegensatz zum Lichtbogenschweißen erhitzt der Laser den Großteil des Werkstücks jedoch nicht wesentlich. Dadurch wird eine thermisch bedingte Verformung der Teile und die Notwendigkeit von Nachbearbeitungsschritten zur Korrektur dieser Verformung vermieden. Die beim Lichtbogenschweißen auftretende Erhitzung kann auch dazu führen, dass flüchtige Legierungselemente verdampfen und bei einigen Materialien eine Einsatzhärtung verursachen.
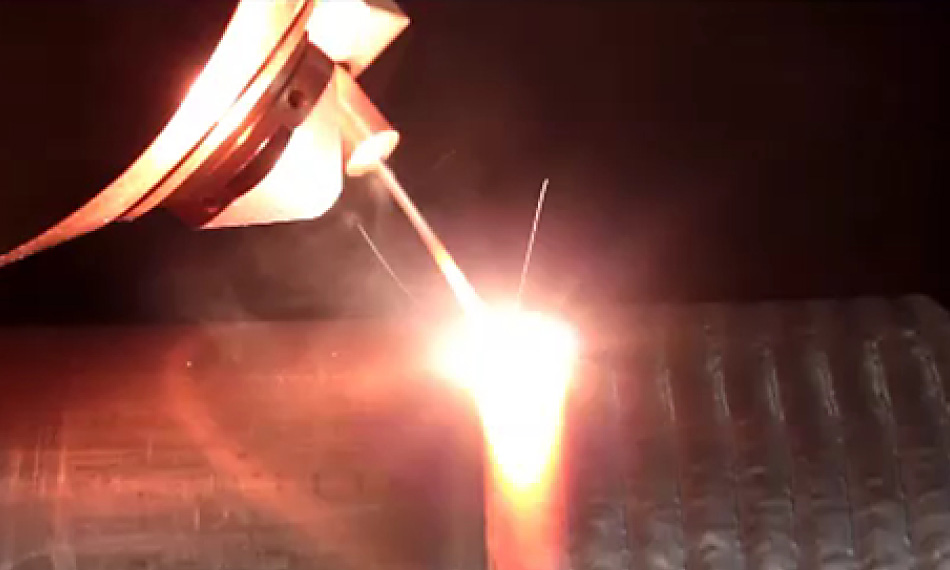
Abbildung 1. Laserauftragsschweißen ist eine hocheffektive Methode zur Reparatur verschlissener Metallteile.
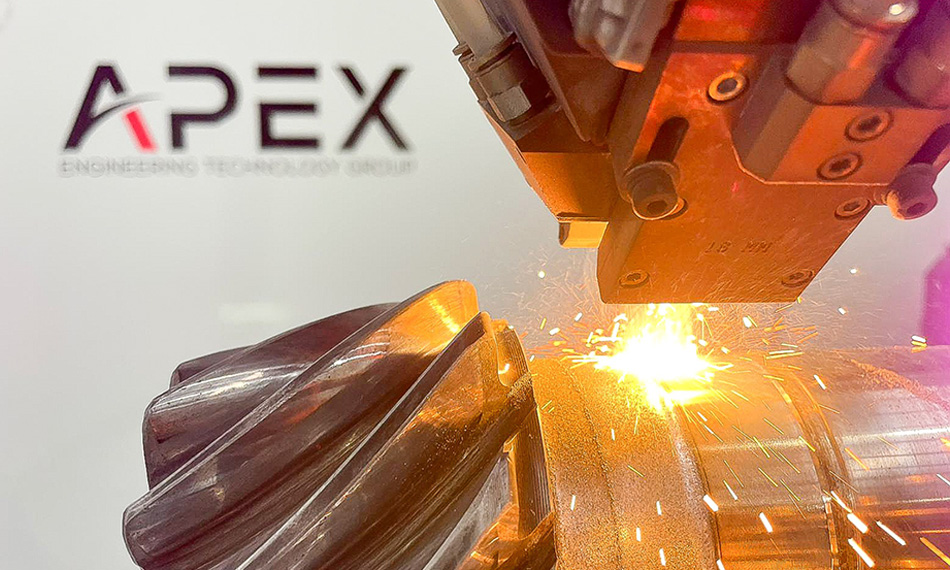
Abbildung 2. Das Auftragsschweißen mit einem Laser der Coherent HighLight DD-Serie, der einen Freiraumstrahl erzeugt, der sich leicht zu einer langen Linie formen lässt, ermöglicht die Abdeckung großer Flächen in einem wirtschaftlich sinnvollen Zeitrahmen.
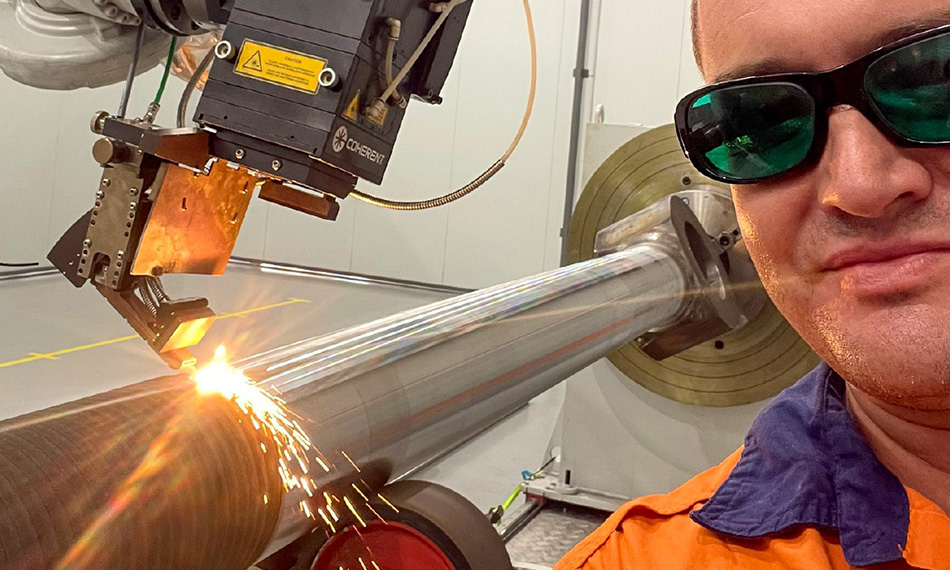
Abbildung 3. Die Überholung von Hydraulikzylindern für Bergbauunternehmen ist ein Teil des laufenden Geschäfts bei APEX.