SOLUTION BRIEF
Verbessertes Schweißen von Autositzen
mit ARM-Faserlasern
Einleitung
Die Strukturen der Vordersitze von Kraftfahrzeugen sind zunehmend komplexer geworden, da die Hersteller versuchen, das Gesamtgewicht (das sich auf die Kraftstoffeffizienz auswirkt) mit der Festigkeit und der Crashsicherheit in Einklang zu bringen. Um diese widersprüchlichen Anforderungen zu erfüllen, werden heute üblicherweise Sitzstrukturen aus drei bis fünf Lagen dickem Stahl verwendet. Hochfester Stahl (HSS) wird oft verwendet, um die Dicke der Baugruppe und damit das Gewicht zu reduzieren.
Aber das Schweißen dieser mehrschichtigen Strukturen ist eine Herausforderung. Eine davon ist die Aufrechterhaltung eines gleichmäßigen Einbrandes beim Schweißen eines komplex geformten Teils. Ein zweites Problem sind Spritzer, die nach dem Schweißen gereinigt werden müssen. Schließlich neigt insbesondere HSS zur Rissbildung, wenn es nach dem Schweißen von dicken Bauteilen mit der sehr hohen Laserleistung zu schnell abkühlt.
Prozess
Ein Coherent HighLight FL-ARM-Faserlaser mit einer Faser mit einem Durchmesser von 100 μm/290 μm (Center/Ring) wurde mit einem II-VI RLSK Remote-Laserbearbeitungskopf (450 mm Brennweite) bei 3-facher Vergrößerung auf die Arbeitsfläche fokussiert. Die Laserleistung betrug 1800 W/5000 W (Mittelstrahl/Ringstrahl). Die Schweißgeschwindigkeit wurde angepasst, um optimale Ergebnisse zu erzielen und variierte von 6,3 m/min für die dickste Baugruppe bis 8,8 m/min für die dünnste. Die Tests wurden in Zusammenarbeit mit dem II-VI HighYAG Anwendungslabor in Detroit durchgeführt.
Ergebnisse
Der Einbrand der Schweißnaht war sehr gleichmäßig, da der HighLight FL-ARM-Faserlaser über einen geschlossenen Regelkreis zur Leistungssteuerung verfügt und unempfindlich gegen Rückreflexion ist. Vor allem aber wurden rissfreie HSS-Schweißnähte mit einem speziellen Rezept für den Schweißabschluss erzielt. Konkret bedeutete dies, dass die Leistung am Ende der Schweißung unabhängig voneinander in den Mittel- und Ringbalken heruntergefahren wurde. Dadurch wird das Temperaturgefälle, das beim Abkühlen des Teils auftritt, erheblich reduziert – und genau diese unterschiedliche Abkühlung führt zu Spannungsrissen. Diese Fähigkeit des FL-ARM, die zugeführte Laserenergie über einen großen Bereich zu verteilen und den Temperaturgradienten zu minimieren, führt auch zu einem weniger turbulenten und stabileren Schmelzbad, wodurch Spritzer bei diesen Tests praktisch ausgeschlossen werden konnten.
Anwendungsfeld
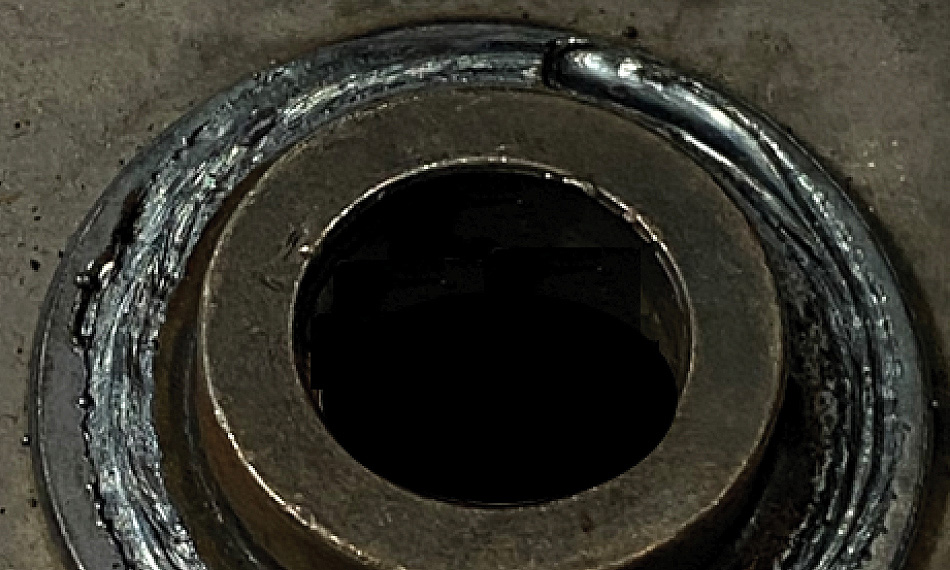
Abbildung 1. Sehr gleichmäßiger Einbrand der Schweißnaht
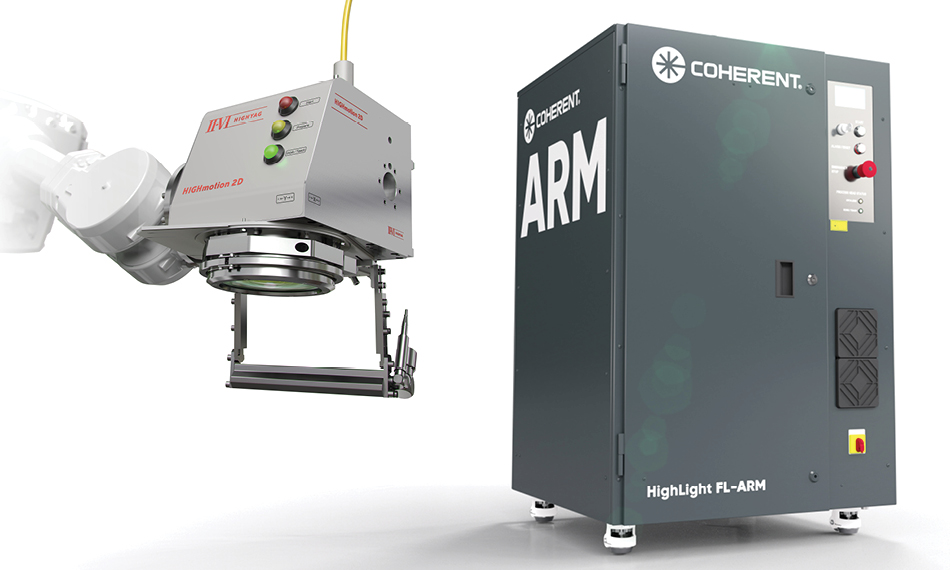
Abbildung 2: HighLight FL-ARM Laser mit II-VI HIGHmotion 2D-Scanner
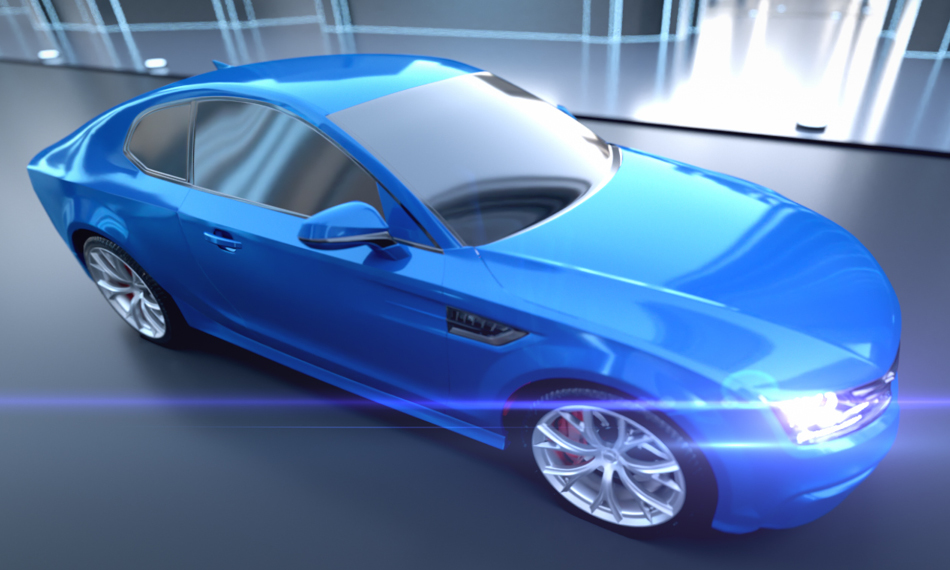