백서
의료장치 산업의 과제: 이종 금속의 가는 와이어 용접
개요
스텐레스 강철 또는 니티놀은 의료장치에서 널리 사용되는 재료입니다. Coherent의 응용 전문가들은 이러한 용접하기 까다로운 재료로 제작된 가는 와이어를 안전하게 용접하는 프로세스를 개발했습니다. 이 프로세스는 플라스틱 코팅을 파괴하지 않고도 수행할 수 있습니다.
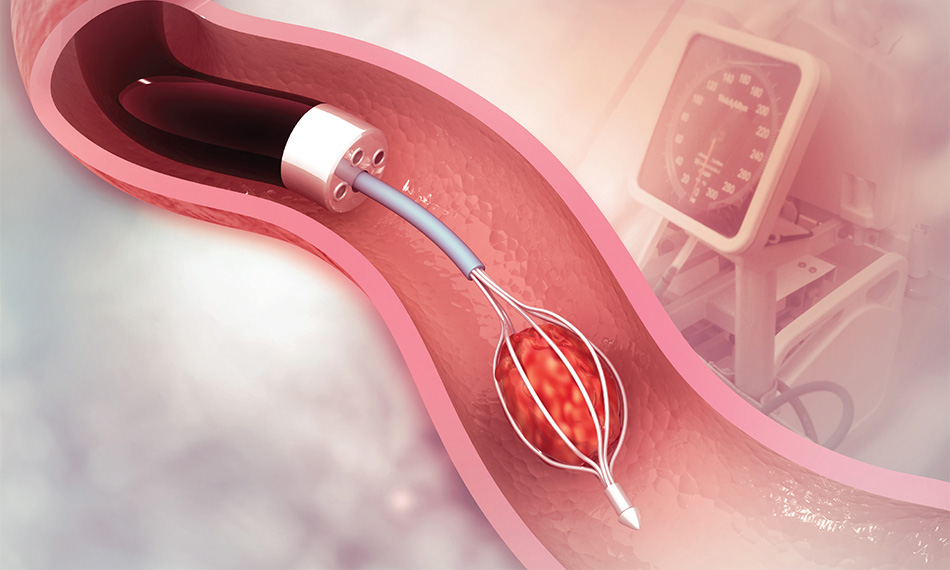
의료장치용 마이크로 용접
레이저 용접은 임플란트 또는 내시경 기기와 같은 의료장치 제조에 널리 사용되며 종종 섬세한 부품을 접합합니다. 이는 접합 파트너가 용접하기 어려운 재료로 제작된 매우 가는 와이어인 경우 까다로운 작업이 됩니다. 일반적인 재료는 생체에 적합하고, 부식에 강하며, 쉽게 살균되는 스텐레스 강철, 니티놀 또는 티타늄입니다. 이질적인 재료를 연결하려는 경우 문제는 훨씬 더 어려워집니다. 레이저는 이 작업에 선호되는(유일한 도구가 아닌 경우) 도구입니다. 이러한 재료를 용접할 때 니티놀의 기억 특성과 같은 바람직한 물리적 특성을 손상시키지 않아야 합니다.
가는 와이어를 연결할 때는 갭이 없어야 합니다. 필러가 사용되지 않고 작은 갭이라도 안정적으로 연결하기에는 너무 클 수 있으므로 와이어가 서로 정확하게 배치되어야 합니다. 따라서 레이저 빔도 정확하게 초점을 맞춰야 합니다. 전자의 문제는 고정 장치로 해결되지만 후자의 작업은 자동화된 비전 시스템을 통해 레이저 초점 위치를 정렬해야 합니다.
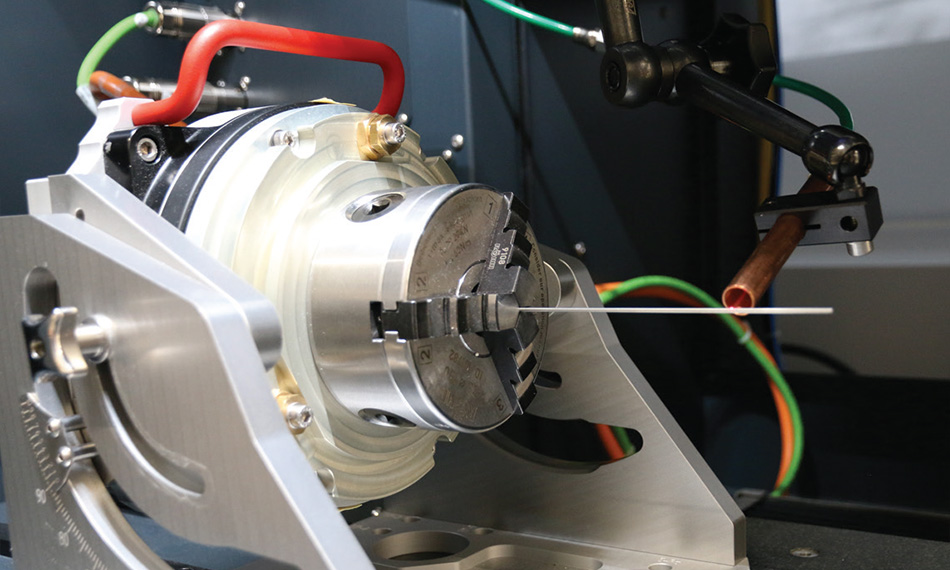
그림 1: 와이어 용접 설정: 용접 파트너는 튜브에 고정됩니다. 공정 가스는 8mm 황동 튜브를 통해 유입됩니다.
ExactWeld 430을 사용한 용접
직경이 25µm(0.001")만큼 작은 가는 와이어를 용접하려면 용접 지점에 에너지를 정밀하게 가해야 합니다. 작은 펄스 에너지는 제어되고 재현 가능한 방식으로 전달되어야 합니다. 이러한 레이저 펄스의 지속 시간과 시간적 형태는 중요한 역할을 합니다.
Coherent의 ExactWeld 430 기계는 이러한 모든 요구 사항을 충족하는 정밀 레이저 용접을 위한 턴키 솔루션입니다. 워크스테이션에는 통합 파이버 레이저 소스(Coherent StarFiber)가 포함되어 있습니다. ExactWeld의 일반적인 레이저 구성 범위는 100W에서 600W 사이입니다. 재현 가능한 펄스 변조 폭으로 밀리줄 에너지 레이저 펄스를 생성할 수 있습니다. 레이저 빔은 검류계 스캐너 또는 고정식 용접 광학 시스템에서 전달됩니다. 워크스테이션에는 공정 가스의 제어 및 공급을 위한 시스템도 포함되어 있습니다. 중요한 것은 클래스 1 레이저 하우징이 최신 인체 공학적 지침을 준수한다는 것입니다.
비전 시스템과 조명은 매우 작은 치수의 부품을 처리할 때 중요한 역할을 합니다. 비전 시스템은 올바르게 최적화되면 자동 가공을 지원합니다. 예를 들어 용접 갭이 너무 큰 경우 갭 제어가 용접 프로세스를 중지합니다.
와이어는 가공 전에 지정된 고정 장치에 배치됩니다. 이 고정 장치는 용접 프로세스에서 와이어를 제자리에 정확하게 고정하는 데 필수적입니다. 워크스테이션은 고정 장치의 로봇 부품 클램핑을 위한 여러 옵션과 함께 사용할 수 있습니다. 최대 4개의 자유도(x, y, z 및 회전)를 지원합니다. 사용하기 쉬운 소프트웨어는 작은 금속 부품 용접의 품질, 수율 및 처리량을 향상시키기 위해 공장 자동화 기능(Industry 4.0/사물 인터넷 지원)도 갖춘 시스템을 제어합니다. 추적성을 위해 가공된 모든 부품을 기록할 수 있습니다. 데이터에는 부품 번호, 타임 스탬프 및 특정 이미지가 포함될 수 있습니다.
"비전 시스템은 올바르게 최적화되면 자동 가공을 지원합니다. 예를 들어 용접 갭이 너무 큰 경우 갭 제어가 용접 프로세스를 중지합니다."
25µm 니티놀 및 스텐레스 강철 와이어의 레이저 용접
Coherent 응용 연구실에서 수행한 최근 연구에서는 ExactWeld 430을 사용하여 니티놀과 스텐레스 강철로 제작된 가는 와이어를 연결했습니다. 다음과 같은 몇 가지 재료 조합을 선택하였습니다.
1) 니티놀/니티놀
2) 스텐레스 강철 316L/스텐레스 강철 316L
3) 스텐레스 강철 316L/니티놀
이러한 두 가지 와이어는 PTFE 슬리브로 보호된 라이너에 코일로 고정되었습니다. 중요한 목표는 PTFE 슬리브를 손상시키지 않고 와이어를 연결하는 것이었습니다. 용접 파트너의 직경은 동일했습니다. 와이어는 25.4µm의 직경과 더 큰 직경으로 테스트했습니다. 작업은 모든 경우에 PTFE 슬리브를 절단하지 않고 성공적으로 수행되었습니다.
몇 가지 주요 공정 세부 정보는 다음과 같습니다. 레이저는 초점 거리가 100mm인 2x 빔 확장기를 사용했습니다. 작동 거리는 0.5mm이고 이론적 스팟 직경은 12.5μm입니다. 직경 25.4μm의 경우 용접용 레이저 출력은 재료 조합에 따라 30W에서 50W까지 다양했습니다. 펄스 지속 시간은 0.035~0.05ms로 조정되어 1mJ(용접 시)에서 2.5mJ(돌출된 와이어 절단 시) 사이의 펄스 에너지가 발생했습니다. 아르곤은 15L/분의 유량, 8mm 직경의 황동 튜브, 1.4mm 거리에 있는 BAK 4 노즐을 사용하여 모든 실험에서 공정 가스로 사용했습니다(그림 2 참조).
두꺼운 와이어 용접의 경우 펄스 지속 시간은 증가했지만 실제 레이저 출력은 가는 와이어 용접과 동일한 수준으로 유지되었습니다. 와이어를 용접한 후 방해되는 와이어 끝은 일련의 더 강한 펄스로 절단했습니다.
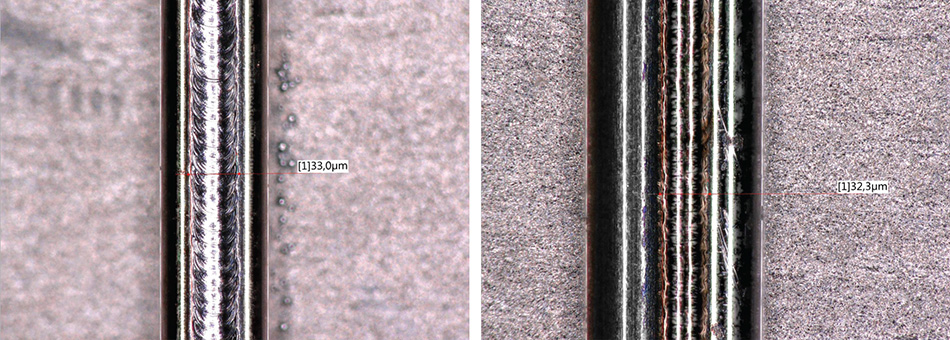
그림 2: 니티놀과 니티놀의 용접(왼쪽) 및 니티놀과 스텐레스 강철의 용접(오른쪽).
연구 결과
적용 시험 결과 100와트 StarFiber 레이저가 다양한 와이어 조합을 용접하기에 충분히 강력한 것으로 나타났습니다. 공정 윈도우는 모든 유형에 대해 상당히 좁습니다. 피크 출력이 10W 미만이고 펄스 지속 시간이 10μs 미만입니다. 더 높은 값은 와이어를 절단하고 더 낮은 값은 와이어를 연결하지 않습니다. 사용된 펄스 모양은 프로세스를 안정적으로 만드는 데 도움이 되었습니다. 와이어가 서로 닿아 간격을 메울 수 없도록 하는 것이 중요합니다. 와이어를 절단하면 와이어 끝이 다음 와이어에 용접될 위험이 있습니다. 따라서 위치 지정이 중요합니다.
피크 파워[W] | 펄스 지속시간[ms] | 반복률[Hz] | 속도[mm/min] | 비고 |
30 | 0.035 | 30 | 20 | 용접 |
40 | 0.05 | 30 | - | 절단 |
턴키 최적화 솔루션
ExactWeld 워크스테이션은 원하는 용도에 따라 Coherent의 응용 전문가가 공장에서 맞춤화합니다. 이 맞춤화에는 레이저, 공정 제어, 자동 처리 시스템뿐만 아니라 필요한 경우 특수 고정 장치도 포함됩니다. 따라서 고객은 응용 분야의 엔지니어의 종합적인 지식과 경험을 통해 엄청난 가치를 얻게 됩니다.
이러한 방식으로 ExactWeld는 다양한 용접 유형 및 형상에 최적화될 수 있습니다. 접촉 용접의 경우 직경이 10μm 이하인 최소 용접 지점을 구현할 수 있습니다. 심 용접의 경우 높은 용접 속도에서 작은 심 형상을 얻을 수 있습니다. 자유형 용접도 프로그래밍할 수 있습니다. 회전식 스테이지 덕분에 기공이 없고 이음매에 균열이 없는 밀봉 용접을 수행하여 누출 방지 용접이 가능합니다. 모든 시스템에 대해 전 세계의 현지 서비스 및 예비 부품 공급이 항상 쉽게 이용할 수 있습니다.
"따라서 고객은 응용 분야의 엔지니어의 종합적인 지식과 경험을 통해 엄청난 가치를 얻게 됩니다."
"최근 신뢰성, 성능 및 사용 용이성 측면에서 이루어진 실질적인 개선 사항을 통해 경제적인 매력도 높일 수 있습니다."
Coherent는 다양한 통합 수준에서 우수한 제품을 제공할 수 있는 능력 면에서 타의 추종을 불허하는 수직 통합 제조업체입니다. 예를 들어 새로운 ExactWeld 430은 이미 많은 응용 분야에서 입증된 업계 최고의 ExactSeries 워크스테이션 플랫폼과 최신 Coherent StarFiber 100~600 레이저 하위 시스템을 결합합니다. 추적성을 위해 모든 부품을 부품 및 공정 세부 정보와 함께 기록할 수 있습니다.
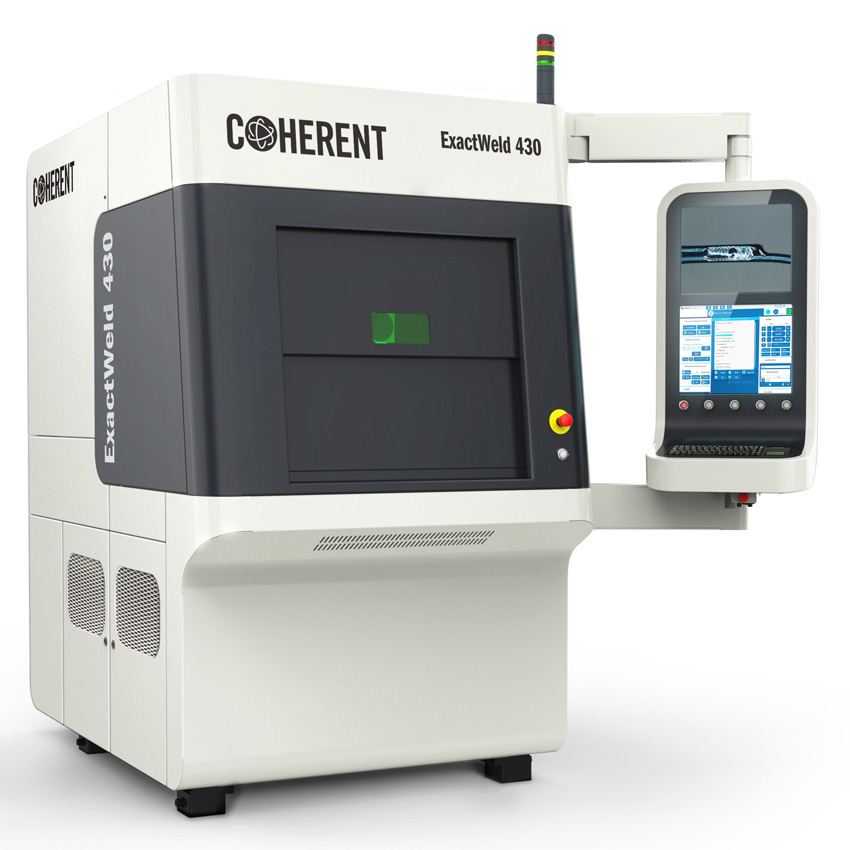
그림 3: Coherent의 ExactWeld 430은 자동화 용접 작업을 위한 클래스 1 레이저 장치입니다.
요약
결론적으로 의료장치 제조에서 가장 어려운 용접 작업 중 하나인 니티놀과 스텐레스 강철로 만든 얇은 25.4µm(0.001") 와이어의 용접 작업이 성공적으로 수행되었습니다. 니티놀과 같은 특수 재료에는 작은 공정 윈도우가 필요합니다. 펄스 전력, 지속 시간 및 시간적 형태는 안정적이고 반복적으로 생성되어야 합니다. 또한 작은 치수로 인해 공작물과 집중된 레이저의 정확한 위치 지정이 필요합니다. Coherent ExactWeld 430은 이미 의료장치 산업의 기타 다양한 까다로운 용접 분야에서 자리를 잡았습니다. 이 장비는 이제 이 어려운 와이어 용접 작업에 적합한 최상의 솔루션을 제공할 수 있는 것으로 입증되었습니다. 최근 신뢰성, 성능 및 사용 용이성 측면에서 이루어진 실질적인 개선 사항을 통해 경제적인 매력도 높일 수 있습니다.