솔루션 개요
이종 재료 용접: 알루미늄 포일 버스바와 구리 바
소개
배터리 시스템 제조업체는 얇은 알루미늄 및 구리 포일 작업을 위한 빠르고 비용 효율적이며 안정적인 용접 방법을 필요로 합니다. 비접촉 레이저 용접도 매력적인 방법이지만 과거에는 포일 두께가 200µm 미만인 경우에는 사용할 수 없었습니다. 이는 기존의 파이버 레이저 소스가 필수적인 공간 분포로는 출력을 전달할 수 없었기 때문입니다. 특히 고출력 파이버 레이저는 상단 포일 시트에 손상을 일으키고, 저출력 파이버 레이저로는 적절한 용입이 이루어지지 않습니다. 싱글 모드 센터 빔이 있는 가변 링 모드(ARM) 파이버 레이저는 이러한 한계를 극복합니다.
과정
배터리 모듈 생산의 일반적인 작업은 얇은 알루미늄 버스 바를 더 두꺼운 구리 바에 중첩 용접하여 여러 배터리를 전기적 직렬로 연결하는 것입니다. 0.2mm 두께의 알루미늄 시트(상단)를 1.5mm 두께의 구리 바(하단)에 용접하여 테스트를 수행했습니다. HighLight 시리즈 FL4000CSM-ARM 소스에는 25µm/170µm(센터 빔/링 빔) 프로세스 파이버와 함께 작업 표면에서 빔의 3배 배율을 생성하는 원격 용접 스캐너 광학이 사용되었습니다. 센터 빔 출력은 500~800W이고 링 출력은 1000~1200W입니다. 레이저 출력은 0.18~0.32초 동안 적용되었습니다. 센터 및 링 빔의 출력은 독립적으로 제어되었습니다.
결과
얇은 알루미늄 포일을 손상시키지 않고 고품질의 완전 침투 용접이 이루어졌습니다(그림 2 참조). 이 공정에서는 스패터가 발생하지 않았으며 필러 와이어를 사용할 필요가 없었습니다. 이러한 긍정적인 결과를 얻을 수 있는 이유는 ARM 레이저가 링 빔으로 키홀 용접 깊이를 안정화시키기 때문입니다. 높은 밝기(에너지 밀도는 높지만 총 에너지는 낮음)의 싱글 모드 센터 빔은 너무 많은 열을 유입하여 재료를 손상시키지 않고 실제 용접을 수행합니다. 마지막으로, 링 출력을 독립적으로 제어하여 줄임으로써 재료를 제어된 방식으로 냉각시켜 용접 풀 난류를 최소화하고 스패터를 제거합니다.
응용 분야
배터리 및 e-모빌리티 응용 분야에 사용되는 얇은 포일 및 열에 민감한 재료의 레이저 용접. 여기에는 배터리 산업의 구리 포일 스텐레스 강철 및 포일-탭 용접과 알루미늄 시트-구리 바 용접이 포함됩니다.
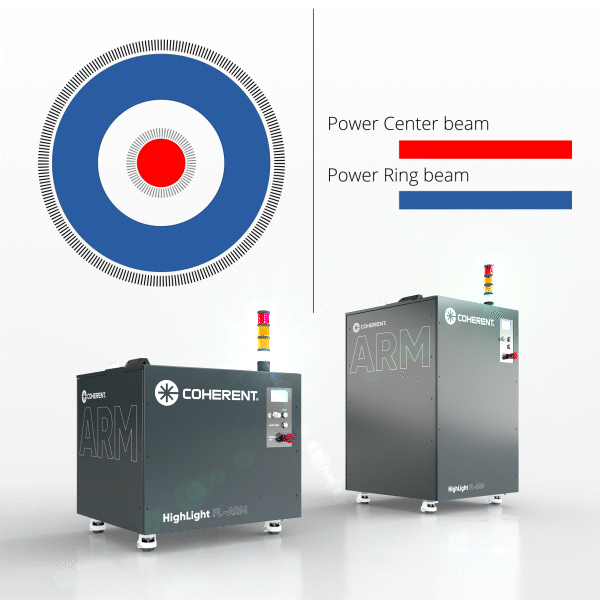
그림 1: 가변 링 모드(ARM) - 독립적으로 제어 가능한 링 및 센터 빔
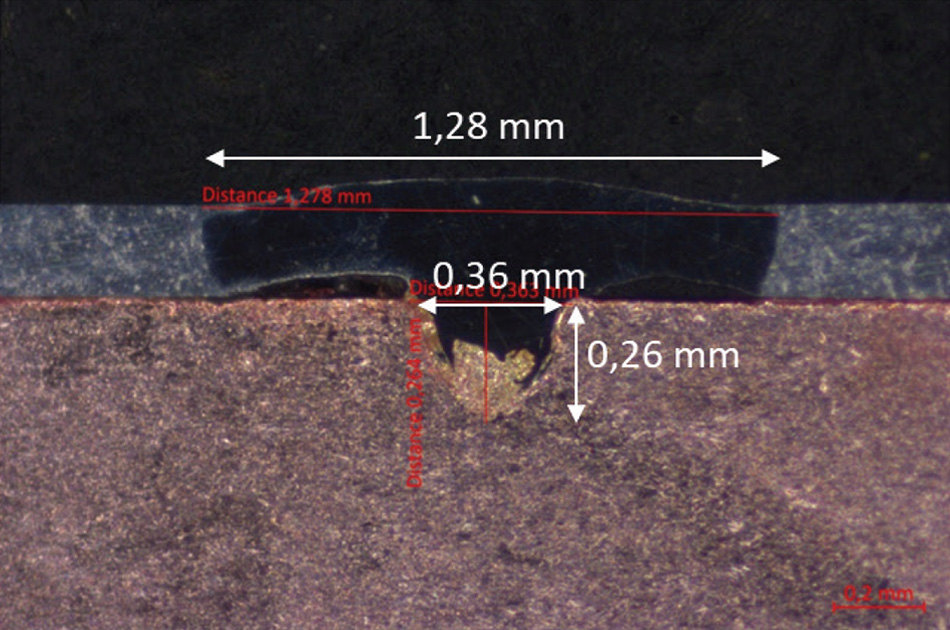
그림 2: 구리-알루미늄 용접의 단면.