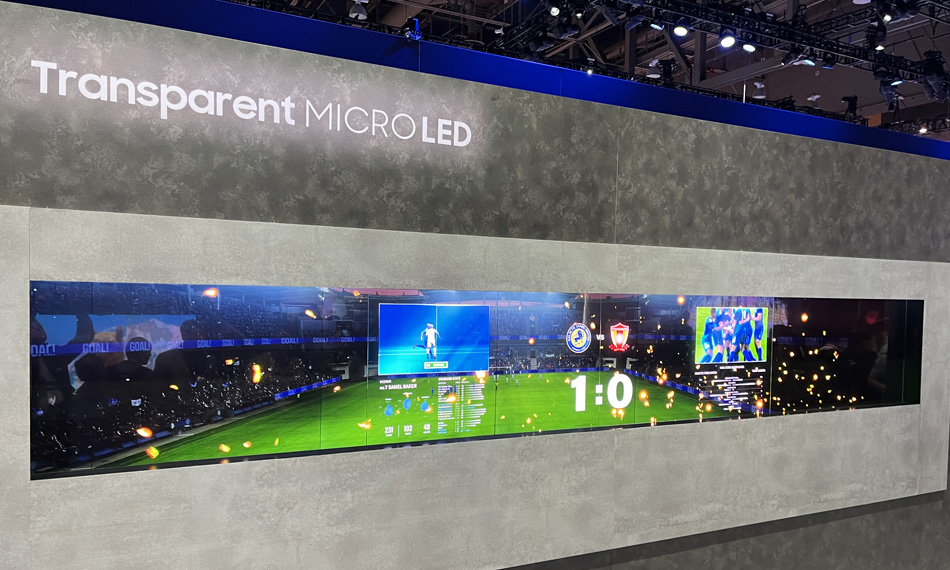
サムスンは、2024年1月のコンシューマー エレクトロニクス ショー (CES) で、巨大な透明なmicroLEDディスプレイで出席者を驚かせました。しかし、microLEDディスプレイはただ見た目が良いだけではありません。LEDやOLEDなどの他のディスプレイ技術に比べて、いくつかの利点があります。これらには、エネルギー効率の向上、長寿命、より高い輝度、より優れた色精度が含まれます。さらに、microLEDを利用することで、メーカーは大規模な再設備を必要とせずに、サイズ、形状、解像度を簡単に変更して新しいディスプレイデザインを作成できます。
これらの利点にもかかわらず、microLEDはまだ一般的になっていません。これは、一般に他のディスプレイに比べて作成が複雑であるためです。この技術の商業化を成功させるためには、克服しなければならない重要な課題がまだいくつかあります。
エキシマレーザがmicroLEDにLIFTを提供
これらの課題がどこで発生するかを理解するのに役立つように、図面はmicroLEDディスプレイ製造における重要なステップのいくつかを示しています。これらが完了したら、その他のさまざまなテスト手順と「エージング」プロセスが行われます。大きなディスプレイは複数の小さなパネルを組み合わせて作成されるため、この場合は追加の組み立てと梱包の手順が発生します。
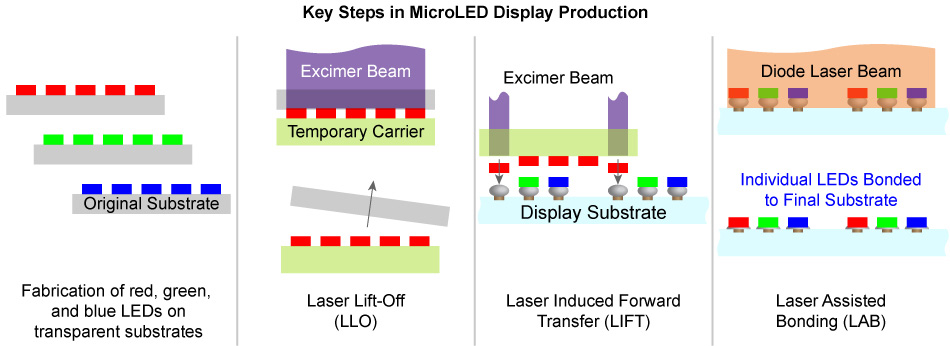
1) 赤、緑、青のLEDは透明基板上に個別に製造されます。2) LLO:LEDは、それらを保持するための接着剤を備えた一時的なキャリアに接続されます。エキシマ レーザは透明基板を通して焦点を合わせられ、透明基板からLEDを分離します。3) リフト:エキシマ レーザは一時的なキャリアを通して集束されることで、個々のLEDが分離され、最終基板上のはんだパッドに向かって推進力が与えられます。4) レーザアシストボンディング:ダイオード レーザは、多数のLEDとはんだバンプを一度に加熱して、それらを急速に溶かし、最終的な接合を形成します。
ほとんどの半導体デバイスと同様に、LEDはもともとウェーハ上でエピタキシャル成長させられます。通常、これはサファイア基板です。microLEDディスプレイの各ピクセルを作成するには、赤、緑、青の各原色を発光する個別のLEDが必要です。しかし、各ウェーハには単一色のデバイスしか含まれていません。したがって、LEDを個々のダイに分割し、最終的なディスプレイを作成するために必要なパターンにまとめて配置する必要があります。
エキシマ レーザは、この加工方法の最初の2つの主要なステップにおいて費用対効果の高いツールであることがすでに証明されています。具体的には、まず レーザ リフトオフ (LLO) を使用して、サファイア ウェーハから個々のLEDダイを分離し、一時的なキャリアに移します。
次に、レーザ誘導順転送 (LIFT)を使用して「大量転送」を実行します。これは、ダイを一時的なキャリアから最終的なディスプレイ基板に移動する加工方法です。最も重要なことは、大量転送ではLEDが目的のピクセル パターンに配置されることです。
microLED組み立ての課題
LEDを基板上の所定の位置に配置した後、それを基板に接着し、電気的に接続する必要があります。そうしないと、ディスプレイが点灯せず、移動したときにすべてのLEDが落ちてしまいます。
このプロセスを容易にするために、最初に、はんだ「バンプ」(はんだの小さなボール)が基板上の電気接続の予定されたすべての点に配置されます。次に、LIFTを使用してダイを配置した後、はんだが溶けるまで加熱します。この状態では、はんだが基板とダイの両方の電気接点の周囲に流れます。その後、それらが冷却されて再固化し、電気的および機械的接続の両方が形成されます。これはエレクトロニクス業界全体で標準的な組み立て技術です。
はんだを溶かすための最も一般的な方法は「マスリフロー」(MR) と呼ばれます。基本的には、はんだボールとダイを含む基板のアセンブリ全体をオーブンに入れるというプロセスです。温度は、はんだを溶かすために循環され、その後それが冷却されます。
しかし、マスリフローは、より高い位置精度でより密接に配置する必要がある小型LEDへの移行には役立ちません。問題は、加熱サイクルに数分かかることです。これにより、すべてのコンポーネントに大きな熱負荷がかかり、コンポーネントが歪んだり、熱機械的歪みが生じたり、基板上のダイの位置が物理的に移動したりする可能性があります。マスリフローオーブンでの処理時間が長いと、電気接続不良が発生するリスクも高まります。この処理自体もエネルギーを大量に消費します。
熱圧着 (TCB)は、MRによって引き起こされる反りのリスクを軽減する代替手段です。TCBは熱を加えると同時に力を加え、相互接続の高さと形状をより適切に制御します。ただし、特定のダイスとパッケージ本体のサイズに合わせてカスタマイズされた複雑なノズルが必要であり、基本的には一度に1つのダイスのみを接着します。このため、1つのディスプレイを作成するために文字通り何百万ものLEDダイを接合する必要があるmicroLEDアプリケーションにはあまり適していません。
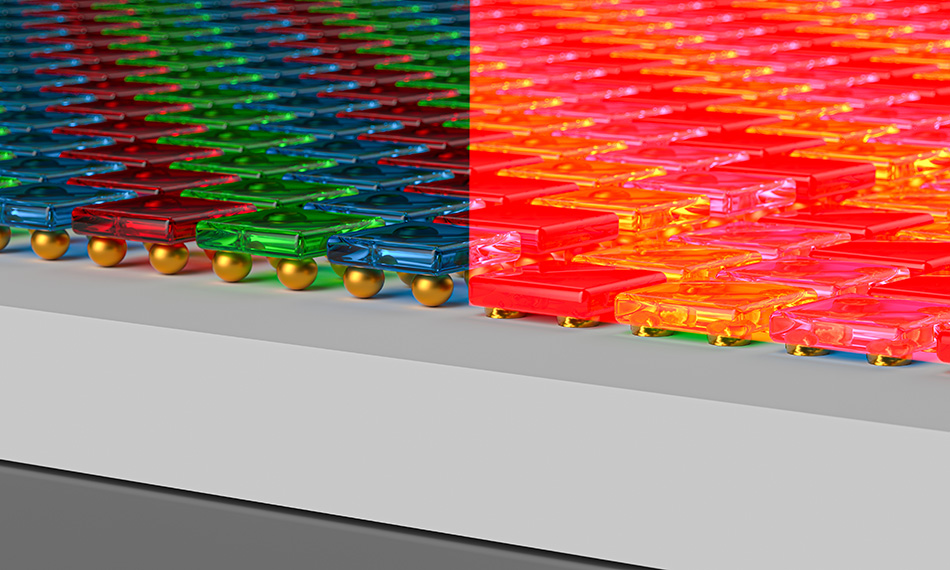
レーザアシスト接着
レーザ支援接合 (LAB) は、これらすべての問題に対処します。LABでは、高出力の赤外線ダイオードレーザビームの出力が長方形に成形されます。強度分布はビームの全領域にわたって高度に均一になるように均質化されます。長方形のビームの寸法は用途によって異なりますが、それでも基板上の数千または数百万のLEDを一度に照らすのに十分な大きさにすることは十分に可能です。
LABの間、レーザは非常に短時間 (1秒未満) オンになります。ただし、はんだを溶かすのに十分な熱をアセンブリに伝えるのに十分な時間です。ただし、ダイの反りやダイの位置変動につながる大量の加熱を引き起こすには短すぎます。レーザにより、必要に応じて冷却フェーズを含めた加熱サイクルの正確な制御が可能になります。その結果、はんだ付けの加工は迅速に実行され、重大な悪影響は発生しません。LABはサイクル時間が短いため、MRやTCBよりも大幅にエネルギー効率が高くなります。
LABを改善するためのより優れたレーザ
レーザに関して言えば、LABの重要な要件は、ビーム強度がその領域全体にわたって均一であることです。これは、はんだの一貫した均一な加熱と、それによる一貫した結果を実現するために必要です。目標は、特定の数のmicroLEDを含む必要な領域のみを選択的に加熱し、周囲の領域をまったく加熱しないことです。このため、エッジ付近で強度があまり低下しない長方形のビーム パターンを生成することが特に重要になります。そうしないと、この領域のLEDがまったく結合されない可能性があります。ただし、照射領域の外側ではビーム強度が非常に急速に低下する必要があります。
Coherent HighLight DLシリーズ のファイバー伝送ダイオードレーザは、 PH50 DL Zoom Optic と組み合わせて、この種の非常に均一な長方形ビームを生成することができます。通常、4kW HighLight DLレーザ (1 ~ 4 kW) がmicroLEDのLABに使用されます。
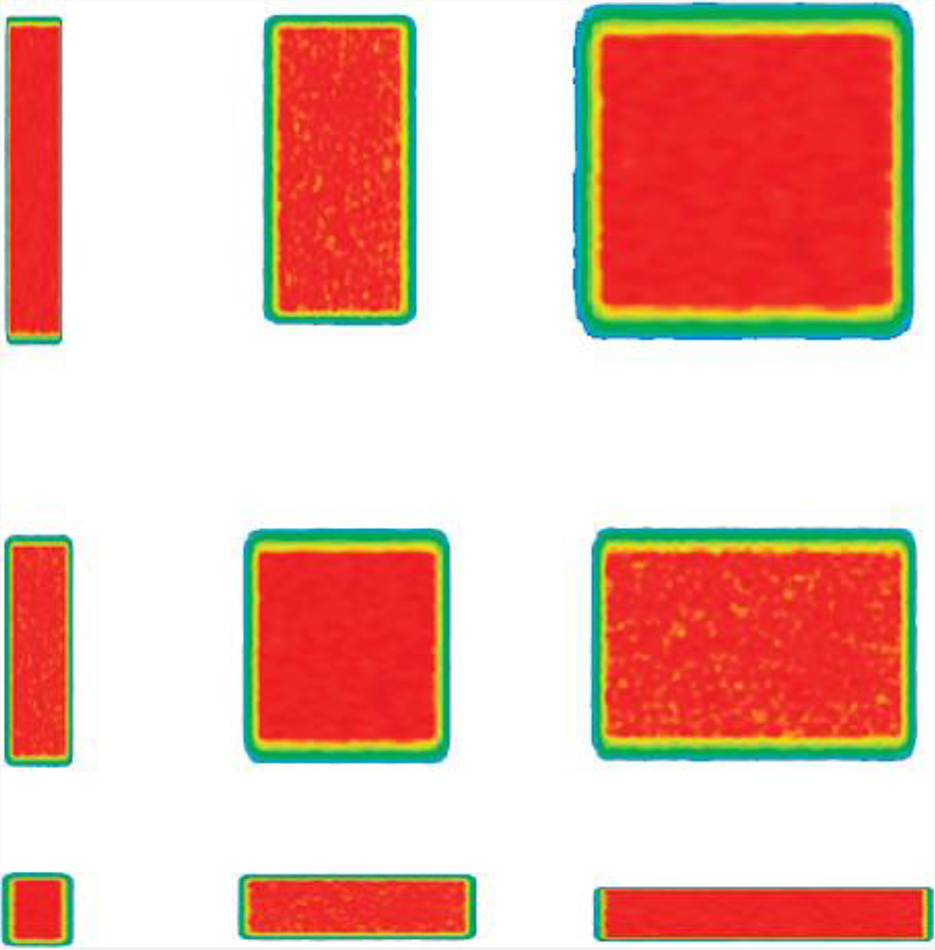
Coherent PH50 DL Zoom Opticは、ファイバーで伝送されるHighLight DDシリーズ ダイオードレーザのマルチモード出力を、非常に均一な長方形のビームに変換します。長方形の長さと幅は、個別に動的に調整できます。ここに示されているスポット サイズの範囲は12x12mmから110x110mmですが、他のズーム構成も利用できます。
この組み合わせは、当社独自の光学設計を使用することにより、競合製品の中で最も優れた強度均一性を実現します。具体的には、ビームの均質化は、入射レーザビームを多数の「ビームレット」に分離するマイクロレンズのアレイを使用して行われます。次に、これらを拡張して重ね合わせて、高度に均一な強度分布を生成します。
Coherent PH50 DL Zoom Opticのもう1つの大きな利点は、プロセス中であっても「オンザフライ」で調整できることです。長方形のビームの長さと幅は、必要に応じて広い範囲にわたって個別に調整できます。このズーム機能は、製造業者が加工方法を開発および評価する際に役立ちます。これにより、さまざまな構成を試して、何が最も効果的かつ最も効率的に機能するかを確認できるようになります。もちろん、Coherentは同じアプローチを利用して、特定の顧客要件を満たす固定(ズームではない)光学系を製造できます。このようなラインビームは、数ミリメートルから最大1000 mmまでの範囲になります。
LLOとLIFTは、microLED製造における2つの主要な実現技術としてすでに確立されています。現在、Coherentレーザをベースとした別の加工方法であるLABにより、高解像度のmicroLEDディスプレイの大量生産が容易になるようです。
LAB用コヒーレント レーザの詳細については、こちらをご覧ください。