MDM Laser Cutting Machines: To Buy or To Build?
Global support and service, single point of contact, and laser safety conformity are just some of the reasons why it makes economic sense to buy rather than build.
October 11, 2022 by Coherent
A key question for anyone using laser cutting for medical device manufacturing is whether to buy a complete machine or to build your own system from the various components, including laser, optics, motion stages, fumes/exhaust handling, process monitoring equipment, etc.
Historically, smaller contract manufacturers would favor buying a machine, while some larger corporations might task the engineering and software departments with building a machine.
Today, the question of whether to buy or build is clear: it makes sound economic sense to buy.
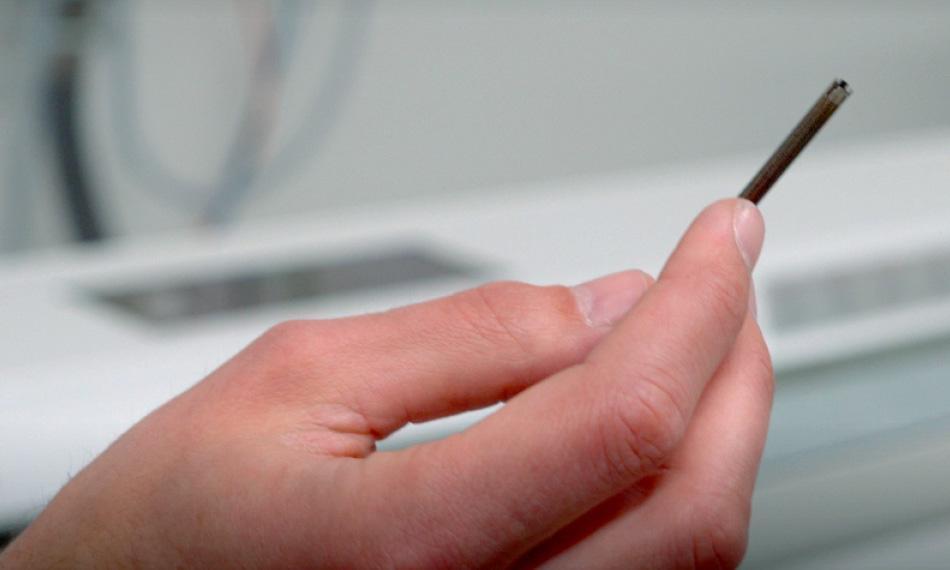
A lot of MDM cutting applications involve tubular parts. Get better results by buying a dedicated machine optimized for tube cutting.
In this blog, we’ll look at four buying factors – some obvious, some not so – that contribute to higher productivity and lower manufacturing costs.
The problem with building and the blame game
When you buy a machine, you’re buying its performance specifications. If the machine is not delivering results, you have a single point of contact with a single line of responsibility.
If you’ve built a machine on your own from lasers, optics, stages, and so forth, who is going to determine why a process is no longer working properly? Perhaps the edge-quality of the struts on stents you’re making is suddenly unacceptably rough. Is it the laser, the optics, or the stages that’s at fault? Just determining the source of the problem is going to take time and probably some finger-pointing. Eventually, the problem has to be identified, fixed, and the machine reassembled and re-aligned — and that can all translate into a whole lot of costly downtime.
On the other hand, when you buy a complete machine, it’s always the machine builder’s responsibility. So there’s no wasted time and energy assigning blame. And the downtime is even shorter if that builder has local service personnel.
Global manufacturing needs global support
In the past, slogans like “Made in the USA” had real marketing value. But today who makes the product is far more important than where it’s made, even for smart consumer products where the brand quality image is paramount.
It is particularly true for small medical devices and components like stents and hypotubes, where shipping costs are a tiny fraction of the overall costs. As a consequence, corporations are free to take their manufacturing global, locating factories wherever the local economic climate and labor costs make the most sense.
It is extremely advantageous to equip these factories with identical laser cutting machines and, this is critical, global service and support.
A large MDM corporation might have a pretty competent in-house engineering team in one location. But a leading laser machine builder usually has a large network of service and support facilities in strategic locations throughout the world. And a machine builder with laser application labs around the world also can provide local expert process development and applications support.
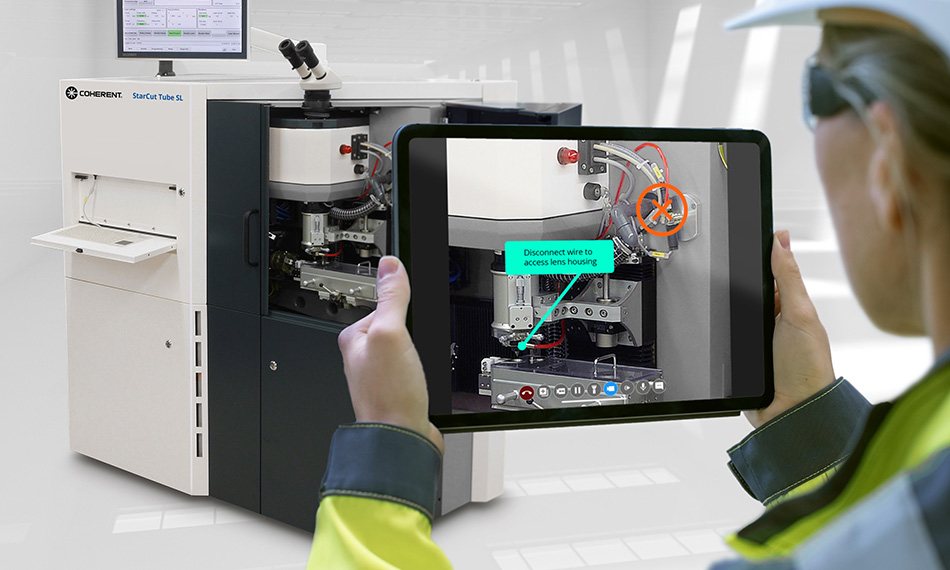
Fast local service is one of several advantages to buying a complete turnkey machine rather than assembling all the components in-house.
Service continuity is an equally important support consideration. What if your in-house engineering “guru” who built your machine is no longer with the company? That could turn into a real nightmare scenario. But a leading machine builder has multiple experts who understand every detail of the machines they’ve supplied and know the fastest fix for any operational problems.
Taking care of laser safety, harmful fumes, and more
With any industrial machine, operator safety is a paramount concern. With laser cutting machines for MDM, there are a couple of safety issues that have to be considered.
The first safety issue is the beam itself. The beam is powerful enough to cut metal, so it’s definitely powerful enough to damage someone’s skin or eyes. That’s why machines need to include failsafe interlocks and various other safety features that meet the appropriate government regulations. This is straightforward for an experienced machine builder. But it’s not trivial and certainly shouldn’t be based on guesswork and assumptions.
There’s also the issue of fumes. Depending on the material you’re using, laser cutting can create potentially harmful fumes. It may be safe to vent these through a factory extraction system. It may not. A turnkey machine will have safe exhaust capabilities built-in, with the appropriate filters and other safeguards, backed up by expert knowledge.
Innovation - Benefit from a future-proof investment
Medical devices and industrial lasers are both technologies characterized by, and benefiting from, continuous innovation. The evolution in stent materials and coatings to reduce the chance of restenosis is a good example. Similarly, the available power in femtosecond lasers has dramatically increased in recent years, offering much higher cutting throughput.
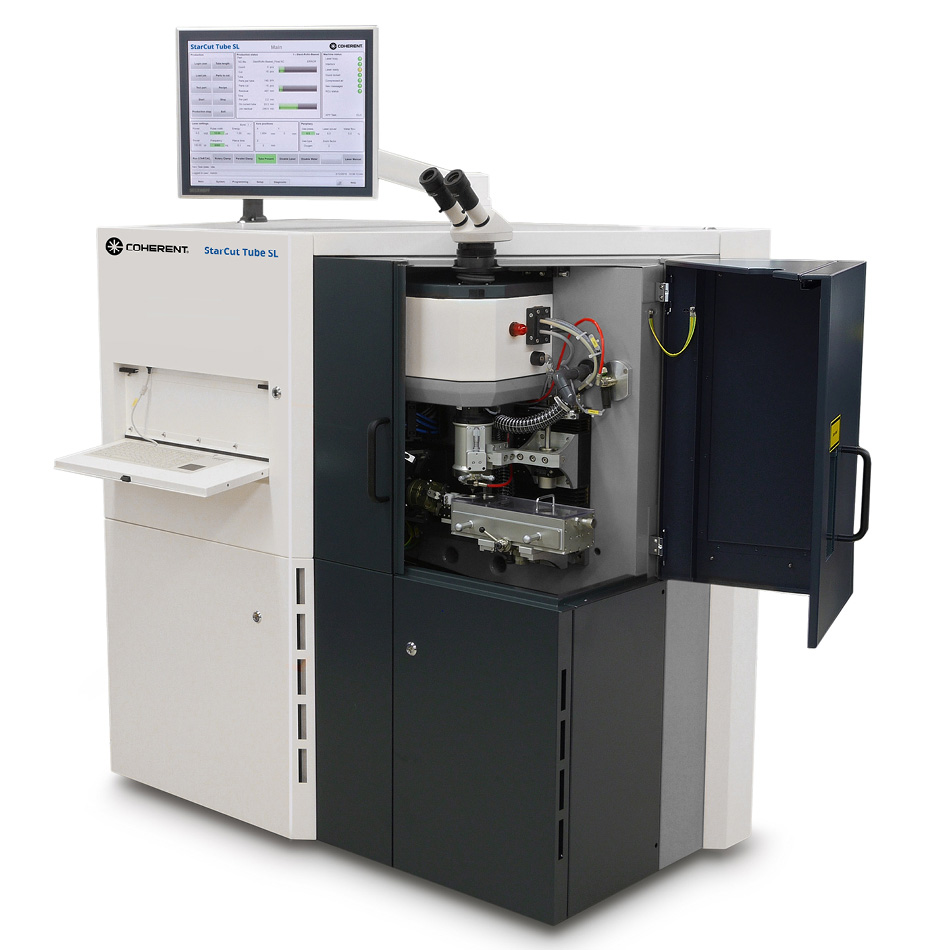
The StarCut Tube from Coherent is a widely used cutting machine in MDM.
When you partner with a laser machine supplier like Coherent — a recognized world leader in laser technology — you will have access to the very latest developments. You will have the opportunity to upgrade and improve your machine with the latest laser hardware and the latest machine software. We will make sure you’re always on the cutting edge.
Related Resources