Fortschrittliche Faserlaser bringen die Produktion von Autositzen voran
Adjustable Ring Mode (ARM) Faserlaser von Coherent ermöglichen das Schweißen von hochfestem Stahl und anderen Materialien in Leichtbau-Sitzstrukturen für Autos ermöglichen
Aktualisiert: 22. Sep. 2022 von Coherent
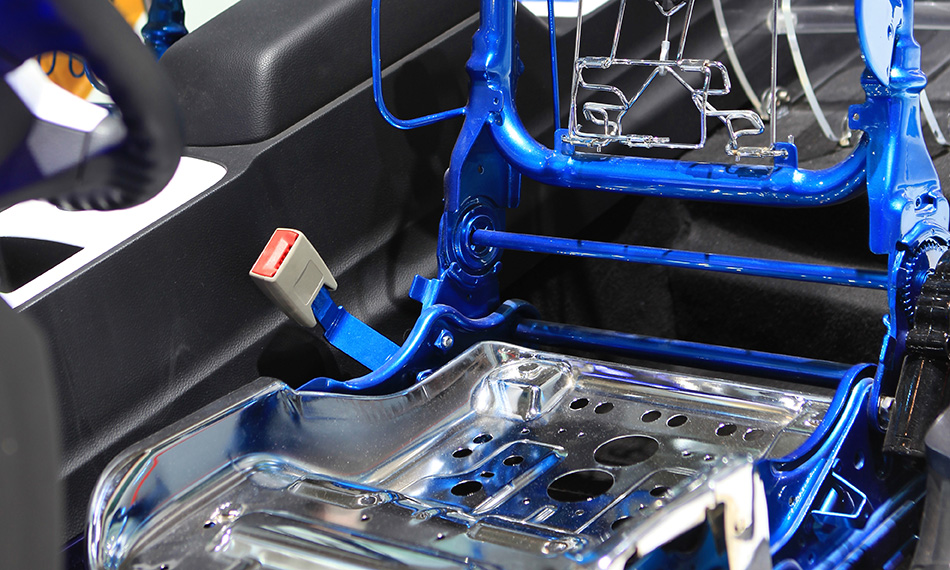
Wenn die meisten von uns über Autositze nachdenken, geht es in der Regel um Komfort und Farbauswahl oder vielleicht um Optionen wie eine eingebaute Heizung oder Massagefunktion. Aber für die Ingenieure, die Autositze entwerfen und bauen, gibt es noch eine ganze Menge mehr zu beachten.
An erster Stelle steht natürlich die Sicherheit. Der Fahrer und die Passagiere sind buchstäblich an ihren Sitzen festgeschnallt. Bei einem Unfall ist die mechanische Festigkeit der Sitzstruktur die erste Verteidigungslinie, um die Fahrzeuginsassen zu schützen und Verletzungen zu vermeiden.
Aber die Kehrseite der Medaille ist das Gewicht. Denn eine Struktur stärker zu machen, bedeutet in der Regel auch, sie schwerer zu machen. Und die Autohersteller stehen unter enormem Druck, das Gewicht ihrer Fahrzeuge zu reduzieren. Dies verbessert die Kraftstoffeffizienz und reduziert die Emissionen von Benzin- und Dieselautos und erhöht die Reichweite von Elektrofahrzeugen. Dies ist in der Automobilindustrie so wichtig, dass es dafür sogar einen eigenen Begriff gibt – „Lightweighting”.
Hochfester Stahl entlastet
Wie stellt man Autositze her, die gleichzeitig stabil und leicht sind? Der Schlüssel liegt in der Verwendung von Materialien, die von Natur aus stärker sind – wie Stahl, Titan und Magnesiumlegierungen – so dass die einzelnen Komponenten dünner und leichter sein können, ohne an mechanischer Festigkeit einzubüßen. Und die Verwendung von Plastik, Verbundwerkstoffen oder anderen wirklich leichten Materialien für Teile, die nicht wesentlich zur Festigkeit oder Steifigkeit des Sitzes beitragen.
Eine der neuesten Entwicklungen bei der Konstruktion von Autositzen ist die Verwendung von hochfestem, niedrig legiertem Stahl (HSLA) und hochfestem Stahl (AHSS). Diese Materialien haben ein noch besseres Verhältnis von Festigkeit zu Gewicht als andere Stähle, so dass sie sehr nützlich sind, um Leichtbauziele zu erreichen. Die Automobilhersteller verwenden sie bereits seit einiger Zeit für Fahrgestelle, und jetzt halten sie auch Einzug in Autositze.
Die Herausforderung beim Schweißen von hochfestem Stahl
Moderne Autositze bestehen aus einer ganzen Reihe von Einzelteilen, die zu ziemlich komplexen Strukturen zusammengesetzt sind. Manchmal werden sogar Metall und andere Werkstoffe in mehrschichtigen Verbundwerkstoffen kombiniert.
Das Remote-Laserschweißen (bei dem sich der Laserbearbeitungskopf in größerer Entfernung vom Werkstück befindet) hat sich aus mehreren Gründen als sehr nützliches Werkzeug für die Herstellung dieser Teile erwiesen. Erstens kann es die komplexen dreidimensionalen Formen von Sitzkomponenten problemlos verarbeiten. Vor allem, wenn ein Multi-kW-Faserlaser oder ein Festkörperlaser eingesetzt wird, liefert er gleichmäßige, konsistente Schweißnähte mit der erforderlichen Eindringtiefe, um mehrere dicke, sandwichartige Metallschichten zu verbinden. Es ist auch eine schnelle und flexible Methode.
Allerdings gibt es Probleme beim Schweißen von hochfestem Stahl mit herkömmlichen Faserlasern. Einer davon sind Spritzer. Spritzer führen zu einer Schweißnaht mit höherer Porosität und Defekten, was eine schlechte mechanische Festigkeit bedeutet. Die Spritzer werden mit zunehmender Schweißgeschwindigkeit schlimmer, was den Produktionsdurchsatz einschränkt.
Ein weiteres Problem ist die inkonsistente Eindringtiefe. Das Ergebnis ist eine Schweißnaht, die nicht auf der gesamten Linie die gleiche mechanische Festigkeit aufweist.
Materialrisse sind auch bei herkömmlichen Faserlasern ein Problem und verringern ebenfalls die mechanische Festigkeit. Risse entstehen, wenn das Material zu schnell abkühlt. Sie treten in der Regel am Ende der Schweißnaht auf, wo die Laserleistung plötzlich abgeschaltet wurde.
Ein weiteres Problem bei der schnellen Abkühlung von hochfestem Stahl ist, dass dabei manchmal eine kristalline Form namens Martensit entsteht. Martensit ist zwar stark, aber auch die sprödeste Form von Stahl. Das bedeutet, dass es reißen kann, wenn es im Gebrauch zu stark beansprucht wird.
ARM-Faserlaser halten dem Schweißen von hochfestem Stahl stand
Der Schlüssel zur Vermeidung all dieser Schwierigkeiten liegt darin, die Laserenergie über einen größeren Bereich zu verteilen und eine präzisere Kontrolle über die Verteilung der Laserenergie innerhalb dieses Bereichs zu haben. Auf diese Weise lassen sich sowohl der Temperaturgradient als auch die Abkühlungsrate im Material besser steuern. Wenn Sie es richtig machen, werden Spritzer, Risse und Martensitbildung vermieden.
Coherent hat die Adjustable Ring Mode (ARM) Faserlasertechnologie entwickelt, um genau diese Art von präziser Steuerung der Materialerwärmung und -abkühlung beim Schweißen zu ermöglichen. Der ARM-Laser verfügt über einen Doppelstrahl-Ausgang. Hierbei wir der Mittel-Strahl von einem zweiten, konzentrischen Ring aus Laserlicht umgeben. Die Leistung im Center und Ring kann unabhängig voneinander eingestellt und sogar moduliert werden, was die gewünschte Kontrolle ermöglicht. ARM-Laser werden bereits bei anderen anspruchsvollen Fügeanwendungen in der Automobilindustrie eingesetzt, z. B. beim Schweißen von Batterien und Kupfer, die dieselbe Art von Finesse erfordern.
Vor kurzem hat ein großer Hersteller von Autositzen Coherent Labs gebeten, eine Reihe von Schweißtests an hochfesten Stahlmaterialien durchzuführen. Konkret ging es um das Überlappschweißen von HSLA-Blechen verschiedener Dicken mit einem Coherent HighLight FL8000-ARM Faserlaser. Es wurde ein spezielles Konzept für die Beendigung der Schweißnaht verwendet, bei dem die Leistung im Center und im Ring unabhängig voneinander heruntergefahren wurde.
Diese Tests zeigten erfolgreich spritzer- und rissfreie Schweißungen bei Prozessgeschwindigkeiten von bis zu 8,8 m/min für die dünnste Materialkombination (2 mm Gesamtdicke) und 6,3 m/min für die dickste (5,7 mm Gesamtdicke). Diese Geschwindigkeiten sind wesentlich höher als die, die mit herkömmlichen Faserlasern erreicht werden können. In allen Fällen war die Einschweißtiefe dank der geschlossenen Leistungsregelung und der inhärenten Rückreflexionsunempfindlichkeit des Coherent FL-ARM Lasers sehr gleichmäßig.
Diese Testergebnisse zeigen, dass das Coherent HighLight FL-ARM qualitativ hochwertige, fehlerarme Schweißnähte in hochfestem Stahl liefern kann. Die hohen Durchsatzraten und die inhärente Zuverlässigkeit dieser Faserlasertechnologie machen sie zu einer kostengünstigen Lösung für die Produktion von Autositzen. Dadurch haben die Autohersteller die Möglichkeit, die fortschrittlichsten Designs zu implementieren, und die Verbraucher können sich mit einem Gefühl von Komfort und Sicherheit entspannen.
Möchten Sie mehr über diese Anwendung erfahren? Dann lesen Sie mehr über die Details in unserer Lösungskurzbeschreibung hier.
Verwandte Ressourcen